Drive Shaft Operating Instructions (PDF)
Document Details
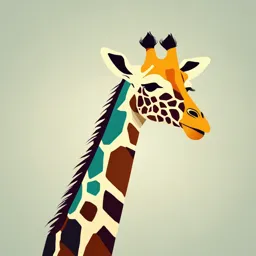
Uploaded by BestSellingBeige
null
Tags
Summary
This document provides operating instructions for a drive shaft. It details safety procedures, function descriptions, and scope of delivery. Includes diagrams and tables relevant to using and maintaining the equipment.
Full Transcript
Drive Shaft Operating Instructions 042/09 EN © All rights reserved by Maschinenfabrik Reinhausen Dissemination and reproduction of this document and use and disclosure of its content are strictly prohibited unless expressly permitted. Infringements will result in liability for compensation. All ri...
Drive Shaft Operating Instructions 042/09 EN © All rights reserved by Maschinenfabrik Reinhausen Dissemination and reproduction of this document and use and disclosure of its content are strictly prohibited unless expressly permitted. Infringements will result in liability for compensation. All rights reserved in the event of the granting of patents, utility models or designs. The product may have been altered since this document was published. We reserve the right to change the technical data, design and scope of supply. Generally the information provided and agreements made when processing the individual quotations and orders are binding. The original operating instructions were written in German. Table of contents Table of contents 1 Introduction......................................................................................................................... 5 1.1 Validity................................................................................................................................................. 5 1.2 Manufacturer....................................................................................................................................... 5 1.3 Subject to change without notice......................................................................................................... 5 1.4 Completeness...................................................................................................................................... 5 1.5 Safekeeping......................................................................................................................................... 6 1.6 Notation conventions........................................................................................................................... 6 1.6.1 Symbols................................................................................................................................................................. 6 1.6.2 Hazard communication system............................................................................................................................. 7 1.6.3 Information system................................................................................................................................................ 9 2 Safety................................................................................................................................. 10 2.1 General safety information................................................................................................................ 10 2.2 Appropriate use................................................................................................................................. 10 2.3 Inappropriate use............................................................................................................................... 10 2.4 Personnel qualification...................................................................................................................... 11 2.5 Operator's duty of care...................................................................................................................... 11 2.6 Personal protective equipment.......................................................................................................... 11 2.7 Drying transformer............................................................................................................................. 13 2.7.1 Drying transformer in autoclave.......................................................................................................................... 13 2.7.2 Drying transformer in the transformer tank.......................................................................................................... 13 3 Product description.......................................................................................................... 14 3.1 Function description.......................................................................................................................... 14 3.2 Scope of delivery............................................................................................................................... 14 3.3 Design/versions................................................................................................................................. 15 3.3.1 Drive shaft without cardan joint and without insulator......................................................................................... 16 3.3.2 Drive shaft without cardan joint and with insulator.............................................................................................. 17 3.3.3 Drive shaft with cardan joint and without insulator.............................................................................................. 18 3.3.4 Drive shaft with cardan joint and with insulator................................................................................................... 18 3.4 Identification plate.............................................................................................................................. 19 4 Packaging, transport and storage................................................................................... 20 4.1 Packaging.......................................................................................................................................... 20 4.1.1 Suitability............................................................................................................................................................. 20 Maschinenfabrik Reinhausen GmbH 2016 042/09 EN Drive Shaft 3 Table of contents 4.1.2 Markings.............................................................................................................................................................. 20 4.2 Transportation, receipt and handling of shipments............................................................................ 21 4.3 Storage of shipments......................................................................................................................... 22 4.4 Unpacking shipments and checking for transportation damages...................................................... 22 5 Mounting............................................................................................................................ 23 5.1 Fitting drive shaft............................................................................................................................... 23 5.1.1 Fitting a vertical drive shaft without cardan joint.................................................................................................. 25 5.1.2 Fitting a horizontal drive shaft without cardan joint............................................................................................. 35 5.2 Fitting drive shaft with cardan joints.................................................................................................. 48 5.3 Fitting drive shaft with insulator......................................................................................................... 66 5.3.1 Fitting vertical drive shaft with insulator............................................................................................................... 67 5.4 Fitting drive shaft with insulator and cardan joint............................................................................... 77 5.5 Centering on-load tap-changer and motor-drive unit......................................................................... 78 6 Appendix............................................................................................................................ 79 6.1 Bevel gear CD 6400, dimensional drawing (892916)........................................................................ 79 4 Drive Shaft 042/09 EN Maschinenfabrik Reinhausen GmbH 2016 1 Introduction 1 Introduction This technical file contains detailed descriptions on the safe and proper in- stallation, connection, commissioning and monitoring of the product. It also includes safety instructions and general information about the prod- uct. This technical file is intended solely for specially trained and authorized per- sonnel. 1.1 Validity This technical file applies to the following types of drive shaft: ▪ Drive shaft ▪ Drive shaft with insulator ▪ Drive shaft with cardan joints 1.2 Manufacturer The product is manufactured by: Maschinenfabrik Reinhausen GmbH Falkensteinstraße 8 93059 Regensburg, Germany Tel.: (+49) 9 41/40 90-0 Fax: (+49) 9 41/40 90-7001 E-mail: [email protected] Further information on the product and copies of this technical file are avail- able from this address if required. 1.3 Subject to change without notice The information contained in this technical file comprises the technical speci- fications approved at the time of printing. Significant modifications will be in- cluded in a new edition of the technical file. The document number and version number of this technical file are shown in the footer. 1.4 Completeness This technical file is incomplete without the supporting documentation. The following documents apply: ▪ Supplement (included in the scope of delivery) ▪ Dimensional drawings (included in the scope of delivery) Maschinenfabrik Reinhausen GmbH 2016 042/09 EN Drive Shaft 5 1 Introduction Also observe generally valid legislation, standards, and guidelines as well as specifications on accident prevention and environmental protection in the re- spective country of use. 1.5 Safekeeping Keep this technical file and all supporting documents ready at hand and ac- cessible for future use at all times. 1.6 Notation conventions This section contains an overview of the symbols and textual emphasis used. 1.6.1 Symbols Symbol Meaning Wrench size Tightening torque Number and type of fastening material used Fill with oil Cut open, cut through Clean Visual inspection Use your hand Adapter ring Apply a coat of paint Use a file 6 Drive Shaft 042/09 EN Maschinenfabrik Reinhausen GmbH 2016 1 Introduction Symbol Meaning Grease Coupling bolt Use a ruler Use a saw Hose clip Wire eyelet, safety wire Use a screwdriver Apply adhesive Lock tab Table 1: Symbols 1.6.2 Hazard communication system Warnings in this technical file are displayed as follows. 1.6.2.1 Warning relating to section Warnings relating to sections refer to entire chapters or sections, sub-sec- tions or several paragraphs within this technical file. Warnings relating to sections use the following format: WARNING Type and source of danger Consequences ► Action ► Action Maschinenfabrik Reinhausen GmbH 2016 042/09 EN Drive Shaft 7 1 Introduction 1.6.2.2 Embedded warning information Embedded warnings refer to a particular part within a section. These warn- ings apply to smaller units of information than the warnings relating to sec- tions. Embedded warnings use the following format: DANGER! Instruction for avoiding a dangerous situation. 1.6.2.3 Signal words and pictograms The following signal words are used: Signal Meaning word DANGER Indicates a hazardous situation which, if not avoided, will result in death or serious injury. WARNING Indicates a hazardous situation which, if not avoided, could result in death or serious injury. CAUTION Indicates a hazardous situation which, if not avoided, could result in injury. NOTICE Indicates measures to be taken to prevent damage to property. Table 2: Signal words in warning notices Pictograms warn of dangers: Pictogram Meaning Warning of a danger point Warning of dangerous electrical voltage Warning of combustible substances Warning of danger of tipping Table 3: Pictograms used in warning notices 8 Drive Shaft 042/09 EN Maschinenfabrik Reinhausen GmbH 2016 1 Introduction 1.6.3 Information system Information is designed to simplify and improve understanding of particular procedures. In this technical file it is laid out as follows: Important information. Maschinenfabrik Reinhausen GmbH 2016 042/09 EN Drive Shaft 9 2 Safety 2 Safety 2.1 General safety information The technical file contains detailed descriptions on the safe and proper in- stallation, connection, commissioning and monitoring of the product. ▪ Read this technical file through carefully to familiarize yourself with the product. ▪ Particular attention should be paid to the information given in this chap- ter. 2.2 Appropriate use If used as intended and in compliance with the requirements and conditions specified in this technical file as well as the warning notices in this technical file and attached to the product, then the product does not present any haz- ards to people, property or the environment. This applies throughout the product's entire life, from delivery through installation and operation to disas- sembly and disposal. The operational quality assurance system ensures a consistently high quality standard, particularly in regard to the observance of health and safety re- quirements. The following is considered appropriate use: ▪ Only operate the product in accordance with this technical file and the agreed delivery conditions and technical data ▪ Use the equipment and special tools supplied solely for the intended purpose and in accordance with the specifications of this technical file ▪ Use the product only with the transformer specified in the order ▪ You will find the standard valid for the product and the year of issue on the nameplate ▪ The serial numbers of on-load tap-changers and on-load tap-changer accessories (drive, drive shaft, bevel gear, protective relay etc.) must match if the on-load tap-changers and on-load tap-changer accessories are supplied as a set for one order 2.3 Inappropriate use Use is considered to be inappropriate if the product is used other than as de- scribed in the Appropriate use section. Please also note the following: ▪ Risk of explosion and fire from highly flammable or explosive gases, va- pors, or dusts. Do not operate product in areas at risk of explosion. ▪ Unauthorized or inappropriate changes to the product may lead to per- sonal injury, material damage, and operational faults. Only modify prod- uct following discussion with Maschinenfabrik Reinhausen GmbH. 10 Drive Shaft 042/09 EN Maschinenfabrik Reinhausen GmbH 2016 2 Safety 2.4 Personnel qualification The product is designed solely for use in electrical energy systems and facili- ties operated by appropriately trained staff. This staff comprises people who are familiar with the installation, assembly, commissioning and operation of such products. 2.5 Operator's duty of care To prevent accidents, disruptions and damage as well as unacceptable ad- verse effects on the environment, those responsible for transport, installa- tion, operation, maintenance and disposal of the product or parts of the prod- uct must ensure the following: ▪ All warning and hazard notices are complied with. ▪ Personnel are instructed regularly in all relevant aspects of operational safety, the operating instructions and particularly the safety instructions contained therein. ▪ Regulations and operating instructions for safe working as well as the relevant instructions for staff procedures in the case of accidents and fires are kept on hand at all times and are displayed in the workplace where applicable. ▪ The product is only used when in a sound operational condition and safety equipment in particular is checked regularly for operational relia- bility. ▪ Only replacement parts, lubricants and auxiliary materials which are au- thorized by the manufacturer are used. ▪ The specified operating conditions and requirements of the installation location are complied with. ▪ All necessary devices and personal protective equipment for the specific activity are made available. ▪ The prescribed maintenance intervals and the relevant regulations are complied with. ▪ Installation, electrical connection and commissioning of the product may only be carried out by qualified and trained personnel in accordance with this technical file. ▪ The operator must ensure appropriate use of the product. 2.6 Personal protective equipment Personal protective equipment must be worn during work to minimize risks to health. ▪ Always wear the personal protective equipment required for the job at hand. ▪ Follow information about personal protective equipment provided in the work area. Maschinenfabrik Reinhausen GmbH 2016 042/09 EN Drive Shaft 11 2 Safety Always wear Protective clothing Close-fitting work clothing with a low breaking strength, with tight sleeves and with no protruding parts. It mainly serves to protect the wearer against being caught by moving machine parts. Safety shoes To protect against falling heavy objects and slipping on slippery surfaces. Table 4: Personal protective equipment to be worn at all times Wear the following in spe- Special personal protective equipment cial environments is needed in special environments. The choice of equipment depends on the circumstances. Safety glasses To protect the eyes from flying parts and splashing liquids. Hard hat To protect from falling and flying parts and materials. Hearing protection To protect from hearing damage. Protective gloves For protection from mechanical, thermal, and electrical hazards. Table 5: Personal protective equipment to be worn in special environments 12 Drive Shaft 042/09 EN Maschinenfabrik Reinhausen GmbH 2016 2 Safety 2.7 Drying transformer 2.7.1 Drying transformer in autoclave Observe the following information when drying the transformer in an auto- clave. NOTICE Damage to drive shaft, on-load tap-changer and transformer! If the drive shaft is dried in a furnace, this may cause damage to the drive shaft and restrict its correct function. ► Do not dry drive shaft in an autoclave. 2.7.2 Drying transformer in the transformer tank If you dry the active part in the transformer tank, the drive shaft may remain fitted to the transformer. Maschinenfabrik Reinhausen GmbH 2016 042/09 EN Drive Shaft 13 3 Product description 3 Product description This chapter contains an overview of the design and function of the product. 3.1 Function description The drive shaft is the mechanical connection between motor-drive and on- load tap-changer head / de-energized tap-changer head. The bevel gear changes the direction from vertical to horizontal (see drawing 892916). Accordingly, the vertical drive shaft has to be mounted between drive and bevel gear and the horizontal drive shaft between bevel gear and on-load tap-changer or de-energized tap-changer. 3.2 Scope of delivery The product is packaged with protection against moisture and is delivered as follows: ▪ Drive shaft ▪ Bevel gear ▪ Operating instructions ▪ Supplements ▪ Dimensional drawing Please note the following: ▪ Check the shipment for completeness on the basis of the shipping docu- ments. ▪ Store the parts in a dry place until installation ▪ The product must remain in its airtight, protective wrapping and may on- ly be removed immediately before installation 14 Drive Shaft 042/09 EN Maschinenfabrik Reinhausen GmbH 2016 3 Product description 3.3 Design/versions The drive shaft consists of a square tube and is coupled at each end by two coupling brackets and one coupling bolt to the drive / driven shaft end of the device to be connected. Figure 1: Components of the drive shaft 1 Bevel gear 2 Hose clip 3 Telescopic protective tube 4 Coupling bracket 5 Square tube 6 Coupling bolt 7 Adapter ring 8 Protective cover 9 Hose clip Maschinenfabrik Reinhausen GmbH 2016 042/09 EN Drive Shaft 15 3 Product description 3.3.1 Drive shaft without cardan joint and without insulator Figure 2: Drive shaft without cardan joint and without insulator (= normal model) Configuration V 1 min Intermediate bearing Middle of hand crank – middle 536 mm When the maximum of bevel gear (maximum per- value of 2472 mm is missible axial offset 2°) exceeded, it is neces- sary to use an inter- mediate bearing. V 1 ≤ 2472 mm (with- out intermediate bear- ing) V 1 > 2472 mm (with intermediate bearing) 16 Drive Shaft 042/09 EN Maschinenfabrik Reinhausen GmbH 2016 3 Product description 3.3.2 Drive shaft without cardan joint and with insulator Figure 3: Drive shaft without cardan joint and with insulator (= special model) Configuration V 1 min Intermediate bearing Middle of hand crank – middle 706 mm When the maximum of bevel gear (maximum per- value of 2472 mm is missible axial offset 2°) exceeded, it is neces- sary to use an inter- mediate bearing. V 1 ≤ 2472 mm (with- out intermediate bear- ing) V 1 > 2472 mm (with intermediate bearing) Maschinenfabrik Reinhausen GmbH 2016 042/09 EN Drive Shaft 17 3 Product description 3.3.3 Drive shaft with cardan joint and without insulator Figure 4: Drive shaft with cardan joint and without insulator (= special model) Configuration V 1 min Intermediate bearing [mm] for [mm] Middle of hand crank – middle 798 V 1 > 2564 of bevel gear (maximum per- missible axial offset alpha = 20°) 3.3.4 Drive shaft with cardan joint and with insulator Figure 5: Drive shaft with cardan joint and with insulator (= special model) Configuration V 1 min Intermediate bearing [mm] for [mm] Middle of hand crank – middle 978 V 1 > 2772 of bevel gear (maximum per- missible axial offset alpha = 20°) 18 Drive Shaft 042/09 EN Maschinenfabrik Reinhausen GmbH 2016 3 Product description 3.4 Identification plate The identification plate is on the telescopic protective tube. Figure 6: Position of the identification plate Maschinenfabrik Reinhausen GmbH 2016 042/09 EN Drive Shaft 19 4 Packaging, transport and storage 4 Packaging, transport and storage 4.1 Packaging The products are sometimes supplied with a sealed packaging and some- times also dried depending on what is required. A sealed packaging surrounds the packaged goods on all sides with plastic foil. Products that have also been dried are identified by a yellow label on the sealed packaging. The information in the following sections should be applied as appropriate. 4.1.1 Suitability NOTICE Property damage due to incorrectly stacked crates! Stacking the crates incorrectly can lead to damage to the packaged goods! ► Only stack up to 2 equally sized crates on top of one another. ► Do not stack crates above a height of 1.5 m. The packaging is suitable for undamaged and fully functional means of transportation in compliance with local transportation laws and regulations. The packaged goods are packed in a stable crate. This crate ensures that when in the intended transportation position the packaged goods are stabi- lized to prevent impermissible changes in position, and that none of the parts touch the loading surface of the means of transport or touch the ground after unloading. 4.1.2 Markings The packaging bears a signature with instructions for safe transport and cor- rect storage. The following symbols apply to the shipment of non-hazardous goods. Adherence to these symbols is mandatory. Protect Top Fragile Attach lifting Center of against gear here mass moisture Table 6: Shipping pictograms 20 Drive Shaft 042/09 EN Maschinenfabrik Reinhausen GmbH 2016 4 Packaging, transport and storage 4.2 Transportation, receipt and handling of shipments WARNING Risk of severe injury or death! Danger due to tipping or falling load! ► Only trained and appointed persons may select the sling gear and se- cure the load. ► Do not walk under the hanging load. ► Use means of transport and lifting gear with a carrying capacity of > 500 kg. NOTICE Damage to packaged goods! Damage due to tipping or falling load! ► Only trained and appointed persons may select the sling gear and se- cure the load. ► Use means of transport and lifting gear with a carrying capacity of > 500 kg. In addition to oscillation stress and shock stress, jolts must also be expected during transportation. In order to prevent possible damage, avoid dropping, tipping, knocking over and colliding with the product. If a crate tips over, falls from a certain height (e.g. when slings tear) or expe- riences an unbroken fall, damage must be expected regardless of the weight. Every delivered shipment must be checked for the following by the recipient before acceptance (acknowledgment of receipt): ▪ Completeness based on the delivery slip ▪ External damage of any type. The checks must take place after unloading when the crate or transport con- tainer can be accessed from all sides. Visible damage If external transport damage is detected on receipt of the shipment, proceed as follows: ▪ Immediately record the transport damage found in the shipping docu- ments and have this countersigned by the carrier. ▪ In the event of severe damage, total loss or high damage costs, immedi- ately notify the sales department at Maschinenfabrik Reinhausen GmbH and the relevant insurance company. ▪ After identifying damage, do not modify the condition of the shipment further and retain the packaging material until an inspection decision has been made by the transport company or the insurance company. ▪ Record the details of the damage immediately onsite together with the carrier involved. This is essential for any claim for damages! Maschinenfabrik Reinhausen GmbH 2016 042/09 EN Drive Shaft 21 4 Packaging, transport and storage ▪ If possible, photograph damage to packaging and packaged goods. This also applies to signs of corrosion on the packaged goods due to mois- ture inside the packaging (rain, snow, condensation). ▪ Name the damaged parts. Hidden damage When damages are not determined until unpacking after receipt of the ship- ment (hidden damage), proceed as follows: ▪ Make the party responsible for the damage liable as soon as possible by telephone and in writing, and prepare a damage report. ▪ Observe the time periods applicable to such actions in the respective country. Inquire about these in good time. With hidden damage, it is very hard to make the transportation company (or other responsible party) liable. Any insurance claims for such damages can only be successful if relevant provisions are expressly included in the insur- ance terms and conditions. 4.3 Storage of shipments Packaged goods can be stored outdoors when the following conditions are complied with. When selecting and setting up the storage location, ensure the following: ▪ Protect stored goods against moisture (flooding, water from melting snow and ice), dirt, pests such as rats, mice, termites and so on, and against unauthorized access. ▪ Store the crates on timber beams and planks as a protection against ris- ing damp and for better ventilation. ▪ Ensure sufficient carrying capacity of the ground. ▪ Keep entrance paths free. ▪ Check stored goods at regular intervals. Also take appropriate action af- ter storms, heavy rain or snow and so on. 4.4 Unpacking shipments and checking for transportation damages ▪ Wherever possible keep the crate packaged for transport to the place where installation will take place. ▪ When unpacking, check the condition of the packaged goods. ▪ Check completeness based on the delivery slip. 22 Drive Shaft 042/09 EN Maschinenfabrik Reinhausen GmbH 2016 5 Mounting 5 Mounting This chapter describes how to fit and connect the drive shaft. 5.1 Fitting drive shaft Observe the following during mounting: NOTICE Damage to drive and on-load tap-changer or de-energized tap- changer! Trouble-free operation of the drive and the on-load tap-changer or de-ener- gized tap-changer cannot be guaranteed. ► The shaft ends to be connected must be exactly aligned. Permitted axial displacement for the drive shaft without cardan joint Minor axial displacement of the vertical and horizontal drive shafts is permit- ted as long as it does not exceed 35 mm per 1000 mm square tube length (that corresponds to 2°). Figure 7: Permitted maximum axial displacement of vertical drive shaft Maschinenfabrik Reinhausen GmbH 2016 042/09 EN Drive Shaft 23 5 Mounting Figure 8: Permitted maximum axial displacement of horizontal drive shaft Resistance to corrosion of components The square tubes, coupling brackets, coupling bolts, screws, and locking washers are corrosion-resistant. We therefore recommend not applying the same external coating to these parts as to the transformer tank. Cutting square tubes, telescopic protective tubes, and protective cover The square tubes, the telescopic protective tube and the protective cover are supplied in overlengths (graded standard lengths). You must cut these parts to the required size before mounting on the transformer. In rare cases, you also have to cut the inner tube of the telescopic protective tube to the de- sired length. The maximum permitted total drive shaft length of the drive - last column = 15 m. Standard lengths Motor-drive unit Manual drive 400 600 900 1300 1700 2000 24 Drive Shaft 042/09 EN Maschinenfabrik Reinhausen GmbH 2016 5 Mounting Standard lengths Motor-drive unit Manual drive 2500 Not permitted 1) Table 7: Graded standard lengths of square tubes 1) I>2000 only possible for vertical installation without shaft protection! Tele- scopic protective tubes for manual drives with vertical dimensions V1> 2462 should be delivered vertically, similar to the motor-drive unit with intermedi- ate bearing. 5.1.1 Fitting a vertical drive shaft without cardan joint To fit the vertical drive shaft to the drive, proceed as follows: 1. CAUTION! Switch off motor protective switch Q1 in the motor-drive unit (position O). If this is not done, the motor-drive unit may be started by accident and thereby cause injuries. 2. Fasten the bevel gear to the transformer. Figure 9: Bevel gear Maschinenfabrik Reinhausen GmbH 2016 042/09 EN Drive Shaft 25 5 Mounting 3. Determine dimension A between shaft end of drive and shaft end of bevel gear. Shorten square tube to length of A – 9 mm. Figure 10: Shortening square tube 26 Drive Shaft 042/09 EN Maschinenfabrik Reinhausen GmbH 2016 5 Mounting 4. Deburr cut surfaces of square tube. Figure 11: Deburring cut surfaces Maschinenfabrik Reinhausen GmbH 2016 042/09 EN Drive Shaft 27 5 Mounting 5. Slide the loosely screwed together coupling part onto square tube until stop is reached. Figure 12: Slide coupling part onto square tube 28 Drive Shaft 042/09 EN Maschinenfabrik Reinhausen GmbH 2016 5 Mounting 6. Insert coupling bolt into shaft end of drive. Grease coupling part, cou- pling bolt and shaft end (e.g. ISOFLEX TOPAS L32). Slide square tube with coupling part onto shaft end. Figure 13: Slide square tube with coupling part onto shaft end 7. Secure square tube onto drive. Figure 14: Secure square tube onto drive Maschinenfabrik Reinhausen GmbH 2016 042/09 EN Drive Shaft 29 5 Mounting 8. Pivoting square tube. Figure 15: Pivoting square tube 9. When installing inner tube of telescopic protective tube, if necessary shorten on side without slits. The minimum dimension for overlapping the two protective tubes is 100 mm. Inner tube must not be deformed and must be deburred in order to slide easily in the outer tube. 30 Drive Shaft 042/09 EN Maschinenfabrik Reinhausen GmbH 2016 5 Mounting Figure 16: Deburring inner tube Dimension A (= distance be- Inner tube Outer tube tween shaft end of drive and shaft end of bevel gear) 170 mm...190 mm Shorten to 200 mm = 200 mm 191 mm...1130 mm Dimension A + 20 = 200 mm mm 1131 mm...1598 mm = 700 mm = 1150 mm 1599 mm...2009 mm = 1150 mm = 1150 mm Maschinenfabrik Reinhausen GmbH 2016 042/09 EN Drive Shaft 31 5 Mounting 10. Slide outer tube over inner tube. When doing so, make sure that the un- slotted side of the inner tube is facing upwards. Slide telescopic protec- tive tube onto square tube Then slide hose clips over telescopic protec- tive tube. Figure 17: Sliding on telescopic protective tube 32 Drive Shaft 042/09 EN Maschinenfabrik Reinhausen GmbH 2016 5 Mounting 11. Place adapter ring over bearing collar of bevel gear and slide upwards. Insert coupling bolt into shaft end of bevel gear. Swing square tube in. Figure 18: Fitting adapter ring and coupling bolt Maschinenfabrik Reinhausen GmbH 2016 042/09 EN Drive Shaft 33 5 Mounting 12. Grease coupling brackets, coupling bolt and shaft end (e.g. ISOFLEX TOPAS L32) and secure square tube with coupling brackets on the bev- el gear. Set a unilateral axial clearance of 3 mm between coupling bolt and upper coupling piece. Figure 19: Mounting coupling brackets 34 Drive Shaft 042/09 EN Maschinenfabrik Reinhausen GmbH 2016 5 Mounting 13. Attach bottom protective tube (inner tube) with a hose clip to bearing collar of drive. Then slide upper protective tube (outer tube) over adapter ring on bevel gear. Secure upper protective tube to bottom protective tube with hose clip both at top end and at the connection point. Figure 20: Mounting protective tube 5.1.2 Fitting a horizontal drive shaft without cardan joint Aligning upper gear unit on the on-load tap-changer head In order to correctly install the horizontal drive shaft, under certain circum- stances you may have to first align the upper gear unit such that the horizon- tal drive shaft is flush with the shaft end of the upper gear unit. Maschinenfabrik Reinhausen GmbH 2016 042/09 EN Drive Shaft 35 5 Mounting Proceed as follows: 1. NOTICE! Make sure the oil compartment is filled completely with oil. Aligning the gear unit after drying without filling the oil compartment completely with oil will damage the on-load tap-changer. 2. Loosen screws and turn pressure ring segments to one side. Figure 21: Pressure ring segments 3. NOTICE! Align gear unit such that the horizontal drive shaft is flush with the drive shaft of the gear unit. While aligning the gear unit, turn the unit's drive shaft such that its output shaft retains its original position. Failure to do so may result in damage to the de-energized tap-changer and transformer when starting up. Figure 22: Aligning gear unit 36 Drive Shaft 042/09 EN Maschinenfabrik Reinhausen GmbH 2016 5 Mounting 4. Swivel pressure ring segments back towards gear unit and tighten screws. Ensure that the spring washer is between the screw head and pressure ring segment and that the pressure ring segments are firmly in contact with the gear unit housing. Figure 23: Securing pressure ring segments Aligning upper gear unit on the de-energized tap-changer head In order to correctly install the horizontal drive shaft, under certain circum- stances you may have to first align the upper gear unit such that the horizon- tal drive shaft is flush with the shaft end of the upper gear unit. Proceed as follows: 1. Loosen screws and turn pressure ring segments to one side. Figure 24: Pressure ring segments Maschinenfabrik Reinhausen GmbH 2016 042/09 EN Drive Shaft 37 5 Mounting 2. NOTICE! Align gear unit such that the horizontal drive shaft is flush with the drive shaft of the gear unit. While aligning the gear unit, turn the unit's drive shaft such that its output shaft retains its original position. Failure to do so may result in damage to the de-energized tap-changer and transformer when starting up. Figure 25: Aligning gear unit 3. Swivel pressure ring segments back towards gear unit and tighten screws. Ensure that the spring washer is between the screw head and pressure ring segment and that the pressure ring segments are firmly in contact with the gear unit housing. Figure 26: Securing pressure ring segments 38 Drive Shaft 042/09 EN Maschinenfabrik Reinhausen GmbH 2016 5 Mounting Aligning upper gear unit on the COMTAP® ARS head In order to correctly install the horizontal drive shaft, under certain circum- stances you may have to first align the upper gear unit such that the horizon- tal drive shaft is flush with the shaft end of the upper gear unit. Proceed as follows: 1. Loosen screws and turn pressure ring segments to one side. Figure 27: Pressure ring segments 2. Pull the gear unit upwards approx. 10-12 mm out of the locking range of the retention pins. Figure 28: Retention pin 3. NOTICE! Align gear unit such that the horizontal drive shaft is flush with the drive shaft of the gear unit. While aligning the gear unit, turn the unit's drive shaft such that its output shaft retains its original position. Failure to do so may result in damage to the de-energized tap-changer Maschinenfabrik Reinhausen GmbH 2016 042/09 EN Drive Shaft 39 5 Mounting and transformer when starting up. Due to the retention pins and the grooves in the housing of the gear unit fastening is possible only in 15° steps. Figure 29: Aligning gear unit 4. Press gear unit down until it again makes contact with the COMTAP® ARS head. Ensure that the retention pin engages in one of the grooves in the housing of the gear unit. Figure 30: Pressing down gear unit 40 Drive Shaft 042/09 EN Maschinenfabrik Reinhausen GmbH 2016 5 Mounting 5. Swivel pressure ring segments back towards gear unit and tighten screws. Ensure that the spring washer is between the screw head and pressure ring segment and that the pressure ring segments are firmly in contact with the gear unit housing. Figure 31: Securing pressure ring segments Fitting horizontal drive shaft To fit the horizontal drive shaft, proceed as follows. 1. Calculate dimension A between shaft end of upper gear unit and shaft end of bevel gear and shorten square tube to length A–9 mm. Figure 32: Shortening square tube Maschinenfabrik Reinhausen GmbH 2016 042/09 EN Drive Shaft 41 5 Mounting 2. Calculate inside width B between housings of upper gear unit and bevel gear. Cut down the protective cover to B-2 mm and deburr the cuts. Pro- tect protective cover against corrosion with a coat of paint. Figure 33: Shorten, deburr, and coat protective cover 42 Drive Shaft 042/09 EN Maschinenfabrik Reinhausen GmbH 2016 5 Mounting 3. Slide loosely screwed together coupling part onto square tube until stop is reached. Figure 34: Slide coupling part onto square tube Maschinenfabrik Reinhausen GmbH 2016 042/09 EN Drive Shaft 43 5 Mounting 4. Grease coupling bolt, coupling part and shaft end of the bevel gear (e.g. ISOFLEX TOPAS L32) and insert coupling bolt into shaft end. Thread hose clip onto square tube and slide square tube with coupling part onto shaft end. Figure 35: Slide square tube with coupling part onto shaft end 5. Secure square tube on bevel gear. Figure 36: Secure square tube on bevel gear 44 Drive Shaft 042/09 EN Maschinenfabrik Reinhausen GmbH 2016 5 Mounting 6. Grease coupling bolt, coupling brackets and shaft end of the upper gear unit (e.g. ISOFLEX TOPAS L32) and insert coupling bolt into shaft end. Secure square tube with coupling brackets on upper gear unit. Figure 37: Secure square tube on upper gear unit. Maschinenfabrik Reinhausen GmbH 2016 042/09 EN Drive Shaft 45 5 Mounting 7. Attach shortened protective cover to housing lugs on the on-load tap- changer head and bevel gear. Secure each end of protective cover with a hose clip. Figure 38: Fitting protective cover 46 Drive Shaft 042/09 EN Maschinenfabrik Reinhausen GmbH 2016 5 Mounting 8. If using a bearing block or angle gear, attach caps to the protective cov- er. Figure 39: Bearing block caps Figure 40: Angle gear caps Maschinenfabrik Reinhausen GmbH 2016 042/09 EN Drive Shaft 47 5 Mounting 5.2 Fitting drive shaft with cardan joints Installation of the drive shaft with cardan joints is mainly designed as a verti- cal drive shaft between motor-drive unit and bevel gear. Technically, a horizontal design is also possible. However, if using a horizon- tal design please note that the protective cover supplied must be adapted accordingly and a cardan joint with an inner hub diameter of 25 mm must be used if you want to use the cardan joint on the upper gear unit. Permitted axial displacement An axial displacement of 20° is permitted for the vertical and horizontal drive shaft with cardan joints. Figure 41: Permitted maximum axial displacement of vertical drive shaft with cardan joints 48 Drive Shaft 042/09 EN Maschinenfabrik Reinhausen GmbH 2016 5 Mounting Figure 42: Permitted maximum axial displacement of horizontal drive shaft with car- dan joints NOTICE Damage to property! Improper mounting of the cardan joint may result in damage or malfunc- tions! ► Ensure that the folding cardan joint does not damage the expansion bellows during mounting. ► Ensure that the angle of deflection α is no greater than 20°. ► Ensure that the angle of deflection α is the same on both cardan joints. Maschinenfabrik Reinhausen GmbH 2016 042/09 EN Drive Shaft 49 5 Mounting Figure 43: Angle of deflection α 50 Drive Shaft 042/09 EN Maschinenfabrik Reinhausen GmbH 2016 5 Mounting To fit the drive shaft with cardan joints, proceed as follows: 1. Grease coupling bolts, coupling brackets, and shaft ends, e.g. ISOFLEX TOPAS L 32. Figure 44: Greasing coupling bolts, coupling brackets, and shaft ends Maschinenfabrik Reinhausen GmbH 2016 042/09 EN Drive Shaft 51 5 Mounting 2. Insert adapter rings into the collar of the rotating protective tube. Place both parts of pivotable protective tube inside one another and turn towards one another to set the corresponding angle. Figure 45: Inserting adapter in pivotable protective tubes 3. When supplied, the cardan joints are fitted with coupling bolts. To mount on the shaft end, the following steps must be taken: Remove hose clip. Slide up expansion bellows. Remove coupling bolt. 52 Drive Shaft 042/09 EN Maschinenfabrik Reinhausen GmbH 2016 5 Mounting Slide cardan joint over device's output shaft. Push in coupling bolt. Slide expansion bellows over this. Secure expansion bellows with hose clip. Figure 46: Mounting cardan joints 4. Connect shorter cardan joint supplied to shaft end of motor-drive unit with coupling bolt. Figure 47: Attach cardan joint on shaft end of motor-drive unit Maschinenfabrik Reinhausen GmbH 2016 042/09 EN Drive Shaft 53 5 Mounting 5. NOTICE! Attach second, longer cardan joint to the bevel gear such that the position of both cardan joint lugs matches on the bevel gear and mo- tor-drive unit. If this is not done, damage or malfunction may result. Figure 48: Fit second cardan joint on bevel gear 6. Secure expansion bellows with hose clip. Figure 49: Secure expansion bellows with hose clip 54 Drive Shaft 042/09 EN Maschinenfabrik Reinhausen GmbH 2016 5 Mounting 7. Provisionally connect loose shaft ends of the joints to an angle bar and align so that they are flush. Figure 50: Connect shaft ends with angle bar Maschinenfabrik Reinhausen GmbH 2016 042/09 EN Drive Shaft 55 5 Mounting 8. Determine dimension A between the shaft ends. Cut square tube to LR = A + 106 mm (LR = length of square tube). Deburr cut surfaces of square tube. Figure 51: Shortening square tube 56 Drive Shaft 042/09 EN Maschinenfabrik Reinhausen GmbH 2016 5 Mounting 9. Before mounting, shorten both telescopic tubes to dimension A/ 2 + 120 mm (A = dimension between both cardan joint ends) and de- burr. Figure 52: Shortening telescopic tubes Maschinenfabrik Reinhausen GmbH 2016 042/09 EN Drive Shaft 57 5 Mounting 10. Fit one adapter ring to bearing collar of motor-drive unit and fit other adapter ring to bearing collar of bevel gear. Figure 53: Fitting adapters 11. Slide previously shortened and deburred square tube over upper cardan joint end until stop is reached. Figure 54: Sliding square tube over upper cardan joint end 58 Drive Shaft 042/09 EN Maschinenfabrik Reinhausen GmbH 2016 5 Mounting 12. Thread upper flexible protective tube with long outlet up onto square tube from below. Figure 55: Sliding flexible protective tube over square tube Maschinenfabrik Reinhausen GmbH 2016 042/09 EN Drive Shaft 59 5 Mounting 13. Slide inner tube into outer tube such that the slotted sides of the outer and inner tube are both facing down. Thread the hose clips. Figure 56: Sliding on telescopic tubes 60 Drive Shaft 042/09 EN Maschinenfabrik Reinhausen GmbH 2016 5 Mounting 14. Slide everything up and secure with a screw clamp. Figure 57: Secure everything with a screw clamp Maschinenfabrik Reinhausen GmbH 2016 042/09 EN Drive Shaft 61 5 Mounting 15. Slide bottom flexible protective tube (also with long outlet up) on to the square tube and secure with screw clamp. Figure 58: Sliding bottom flexible protective tube onto square tube 62 Drive Shaft 042/09 EN Maschinenfabrik Reinhausen GmbH 2016 5 Mounting 16. Swing in square tube and slide all the way down. Figure 59: Swinging square tube in Maschinenfabrik Reinhausen GmbH 2016 042/09 EN Drive Shaft 63 5 Mounting 17. Tighten bottom coupling brackets. Shaft end and coupling part must be securely connected such that no axial clearance remains between the coupling bolt and coupling bracket. Figure 60: Tightening lower coupling brackets 64 Drive Shaft 042/09 EN Maschinenfabrik Reinhausen GmbH 2016 5 Mounting 18. Fit upper coupling brackets with 3 mm axial clearance. Figure 61: Fitting upper coupling brackets 19. Working from top to bottom, mount the individual parts of the shaft pro- tection. Set angle position between both parts of pivotable protective tube and fix with available hose clip. Secure both upper and lower pro- tective tubes with a hose clip at both ends. Secure the two telescopic protective tubes to one another using a hose clip. The plastic adapters must be at the respective end of the pivotable protec- tive tube. Only slide telescopic protective tube into upper and lower pivota- ble protective tubes by the width of the adapter before tightening the hose clips. Maschinenfabrik Reinhausen GmbH 2016 042/09 EN Drive Shaft 65 5 Mounting Figure 62: Secure telescopic protective tube and flexible protective tubes with hose clips 5.3 Fitting drive shaft with insulator A model with insulator in the vertical drive shaft is available for insulating in- stallation of the drive shaft. 66 Drive Shaft 042/09 EN Maschinenfabrik Reinhausen GmbH 2016 5 Mounting Permitted axial displacement Minor axial displacement of the vertical drive shaft with insulator is permitted as long as it does not exceed 35 mm per 1000 mm square tube length (that corresponds to 2°). Figure 63: Permitted maximum axial displacement of vertical drive shaft with insulator 5.3.1 Fitting vertical drive shaft with insulator To fit the vertical drive shaft, proceed as follows. 1. CAUTION! Switch off motor protective switch Q1 in the motor-drive unit (position O). If this is not done, the motor-drive unit may be started by accident and thereby cause injuries. Maschinenfabrik Reinhausen GmbH 2016 042/09 EN Drive Shaft 67 5 Mounting 2. Screw down the bevel gear for fastening on the transformer on both sides with the contact washers provided to ensure permanent ground- ing. Screws are not included in the scope of supply. Figure 64: Bevel gear 68 Drive Shaft 042/09 EN Maschinenfabrik Reinhausen GmbH 2016 5 Mounting 3. Determine dimension A between shaft end of drive and shaft end of bevel gear. Shorten square tube to length of A–179 mm taking the insu- lator into account. Figure 65: Shortening square tube Maschinenfabrik Reinhausen GmbH 2016 042/09 EN Drive Shaft 69 5 Mounting 4. Deburr cut surfaces of square tube. Figure 66: Deburring cut surfaces 5. Screw down double coupling part with insulator supplied and square tube. Mount insulator on the side facing the drive. Figure 67: Screwing down square tube and insulator with double coupling part 70 Drive Shaft 042/09 EN Maschinenfabrik Reinhausen GmbH 2016 5 Mounting 6. Slide loosely screwed together coupling part onto insulator until stop is reached. Figure 68: Slide coupling part onto insulator 7. Place the supplied insulator ring on the bearing collar of the motor-drive unit. Figure 69: Insulating ring 8. Insert coupling bolt into shaft end of drive. Grease coupling part, cou- pling bolt and shaft end (e.g. ISOFLEX TOPAS L32). Slide square tube with coupling part onto shaft end. Figure 70: Slide square tube with coupling part onto shaft end Maschinenfabrik Reinhausen GmbH 2016 042/09 EN Drive Shaft 71 5 Mounting 9. Secure square tube onto drive. Figure 71: Secure square tube onto drive 10. Pivoting square tube. Figure 72: Pivoting square tube 11. When installing inner tube of telescopic protective tube, if necessary shorten on side without slits. The minimum dimension for overlapping the two protective tubes is 100 mm. Inner tube must not be deformed and must be deburred in order to slide easily in the outer tube. 72 Drive Shaft 042/09 EN Maschinenfabrik Reinhausen GmbH 2016 5 Mounting Figure 73: Deburring inner tube Dimension A (= distance be- Inner tube Outer tube tween shaft end of drive and shaft end of bevel gear) 170 mm...190 mm Shorten to 200 mm = 200 mm 191 mm...1130 mm Dimension A + 20 = 200 mm mm 1131 mm...1598 mm = 700 mm = 1150 mm 1599 mm...2009 mm = 1150 mm = 1150 mm Maschinenfabrik Reinhausen GmbH 2016 042/09 EN Drive Shaft 73 5 Mounting 12. Slide outer tube over inner tube. When doing so, make sure that the un- slotted side of the inner tube is facing up. Slide telescopic protective tube onto square tube Then slide hose clips over telescopic protective tube. Figure 74: Sliding on telescopic protective tube 74 Drive Shaft 042/09 EN Maschinenfabrik Reinhausen GmbH 2016 5 Mounting 13. Place adapter ring over bearing collar of bevel gear and slide upwards. Insert coupling bolt into shaft end of bevel gear. Swing square tube in. Figure 75: Fitting adapter ring and coupling bolt Maschinenfabrik Reinhausen GmbH 2016 042/09 EN Drive Shaft 75 5 Mounting 14. Grease coupling brackets, coupling bolt and shaft end (e.g. ISOFLEX TOPAS L32) and secure square tube with coupling brackets on the bev- el gear. Set a unilateral axial clearance of 3 mm between coupling bolt and upper coupling piece. Figure 76: Mounting coupling brackets 76 Drive Shaft 042/09 EN Maschinenfabrik Reinhausen GmbH 2016 5 Mounting 15. Attach bottom protective tube (inner tube) with a hose clip to bearing collar of drive. Then slide upper protective tube (outer tube) over adapter on bevel gear. Secure upper protective tube to bottom pro- tective tube with hose clip both at top end and at the connection point. Figure 77: Mounting protective tube 5.4 Fitting drive shaft with insulator and cardan joint A model with insulator and cardan joint in the vertical drive shaft is also available for insulating installation of the drive shaft. Maschinenfabrik Reinhausen GmbH 2016 042/09 EN Drive Shaft 77 5 Mounting Permitted axial displacement An axial displacement of 20° is permitted for a drive shaft with insulator and cardan joint. Figure 78: Permitted maximum axial displacement of vertical drive shaft with insulator and cardan joint 5.5 Centering on-load tap-changer and motor-drive unit Center on-load tap-changer and motor-drive unit as described in relevant MR operating instructions for motor-drive unit. 78 Drive Shaft 042/09 EN Maschinenfabrik Reinhausen GmbH 2016 6 Appendix 6 Appendix 6.1 Bevel gear CD 6400, dimensional drawing (892916) Maschinenfabrik Reinhausen GmbH 2016 042/09 EN Drive Shaft 79 MR worldwide Australia Malaysia Reinhausen Australia Pty. Ltd. Reinhausen Asia-Pacific Sdn. Bhd 17/20-22 St Albans Road Level 11 Chulan Tower Kingsgrove NSW 2208 No. 3 Jalan Conlay Phone: +61 2 9502 2202 50450 Kuala Lumpur Fax: +61 2 9502 2224 Phone: +60 3 2142 6481 E-Mail: [email protected] Fax: +60 3 2142 6422 E-Mail: [email protected] Brazil MR do Brasil Indústria Mecánica Ltda. P.R.C. (China) Av. Elias Yazbek, 465 MR China Ltd. (MRT) CEP: 06803-000 开德贸易(上海)有限公司 Embu - São Paulo 中国上海浦东新区浦东南路 360 号 Phone: +55 11 4785 2150 新上海国际大厦 4 楼 E 座 Fax: +55 11 4785 2185 邮编: 200120 E-Mail: [email protected] 电话:+ 86 21 61634588 传真:+ 86 21 61634582 Canada 邮箱:[email protected] Reinhausen Canada Inc. [email protected] 3755, rue Java, Suite 180 Brossard, Québec J4Y 0E4 Russian Federation Phone: +1 514 370 5377 OOO MR Fax: +1 450 659 3092 Naberezhnaya Akademika Tupoleva E-Mail: [email protected] 15, Bld. 2 ("Tupolev Plaza") 105005 Moscow India Phone: +7 495 980 89 67 Easun-MR Tap Changers Ltd. (Joint Venture) Fax: +7 495 980 89 67 612, CTH Road E-Mail: [email protected] Tiruninravur, Chennai 602 024 Phone: +91 44 26300883 South Africa Fax: +91 44 26390881 Reinhausen South Africa (Pty) Ltd. E-Mail: [email protected] No. 15, Third Street, Booysens Reserve Johannesburg Indonesia Phone: +27 11 8352077 Pt. Reinhausen Indonesia Fax: +27 11 8353806 German Center, Suite 6310, E-Mail: [email protected] Jl. Kapt. Subijanto Dj. BSD City, Tangerang South Korea Phone: +62 21 5315-3183 Reinhausen Korea Ltd. Fax: +62 21 5315-3184 21st floor, Standard Chartered Bank Bldg., E-Mail: [email protected] 47, Chongro, Chongro-gu, Seoul 110-702 Iran Phone: +82 2 767 4909 Iran Transfo After Sales Services Co. Fax: +82 2 736 0049 (Joint Venture) E-Mail: [email protected] Zanjan, Industrial Township No. 1 (Aliabad) Corner of Morad Str. U.S.A. Postal Code 4533144551 Reinhausen Manufacturing Inc. E-Mail: [email protected] 2549 North 9th Avenue Humboldt, TN 38343 Italy Phone: +1 731 784 7681 Reinhausen Italia S.r.l. Fax: +1 731 784 7682 Via Alserio, 16 E-Mail: [email protected] 20159 Milano Phone: +39 02 6943471 United Arab Emirates Fax: +39 02 69434766 Reinhausen Middle East FZE E-Mail: [email protected] Dubai Airport Freezone, Building Phase 6 3rd floor, Office No. 6EB, 341 Dubai Japan Phone: +971 4 2368 451 MR Japan Corporation Fax: +971 4 2368 225 German Industry Park Email: [email protected] 1-18-2 Hakusan, Midori-ku Yokohama 226-0006 Phone: +81 45 929 5728 Fax: +81 45 929 5741 Luxembourg Reinhausen Luxembourg S.A. 72, Rue de Prés L-7333 Steinsel Phone: +352 27 3347 1 Fax: +352 27 3347 99 E-Mail: [email protected] Maschinenfabrik Reinhausen GmbH +49 (0)941 4090-0 www.reinhausen.com Falkensteinstrasse 8 +49(0)941 4090-7001 93059 Regensburg [email protected] 042/09 EN ▪ 08/16 ▪ F0007709