B2-4B Electronic Fundamentals PDF
Document Details
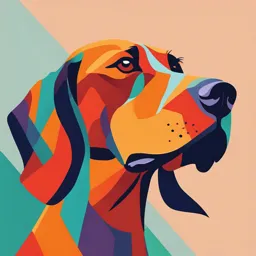
Uploaded by PreEminentBiography3382
2020
CASA
Tags
Related
- Electrical Fundamentals for Aircraft Maintenance Licence PDF
- B2-05A.11 Electronic Displays PDF
- Aircraft Electrical and Electronic Systems (Principles, Maintenance & Operation) PDF
- Electronic Fundamentals PDF - B2 Certification
- CASA B-03a Electrical Fundamentals I PDF
- Electronic Displays (PDF) - Aviation Australia Training
Summary
This document is part of a training module for aircraft maintenance licenses, specifically covering Electronic Fundamentals II. It details knowledge levels, table content, integrated circuits, operational amplifiers, printed circuit boards, and servomechanisms, providing information on the theory and application of electronic components and systems used in aircraft.
Full Transcript
MODULE 04 Category B2 Licence CASA B2-04b Electronic Fundamentals II Copyright © 2020 Aviation Australia All rights reserved. No part of this document may be reproduced, transferred, sold or otherwise disposed of...
MODULE 04 Category B2 Licence CASA B2-04b Electronic Fundamentals II Copyright © 2020 Aviation Australia All rights reserved. No part of this document may be reproduced, transferred, sold or otherwise disposed of, without the written permission of Aviation Australia. CONTROLLED DOCUMENT 2022-11-10 B2-04b Electronic Fundamentals Page 2 of 169 CASA Part 66 - Training Materials Only Knowledge Levels Category A, B1, B2 and C Aircraft Maintenance Licence Basic knowledge for categories A, B1 and B2 are indicated by the allocation of knowledge levels indicators (1, 2 or 3) against each applicable subject. Category C applicants must meet either the category B1 or the category B2 basic knowledge levels. The knowledge level indicators are defined as follows: LEVEL 1 Objectives: The applicant should be familiar with the basic elements of the subject. The applicant should be able to give a simple description of the whole subject, using common words and examples. The applicant should be able to use typical terms. LEVEL 2 A general knowledge of the theoretical and practical aspects of the subject. An ability to apply that knowledge. Objectives: The applicant should be able to understand the theoretical fundamentals of the subject. The applicant should be able to give a general description of the subject using, as appropriate, typical examples. The applicant should be able to use mathematical formulae in conjunction with physical laws describing the subject. The applicant should be able to read and understand sketches, drawings and schematics describing the subject. The applicant should be able to apply his knowledge in a practical manner using detailed procedures. LEVEL 3 A detailed knowledge of the theoretical and practical aspects of the subject. A capacity to combine and apply the separate elements of knowledge in a logical and comprehensive manner. Objectives: The applicant should know the theory of the subject and interrelationships with other subjects. The applicant should be able to give a detailed description of the subject using theoretical fundamentals and specific examples. The applicant should understand and be able to use mathematical formulae related to the subject. The applicant should be able to read, understand and prepare sketches, simple drawings and schematics describing the subject. The applicant should be able to apply his knowledge in a practical manner using manufacturer's instructions. The applicant should be able to interpret results from various sources and measurements and apply corrective action where appropriate. 2022-11-10 B2-04b Electronic Fundamentals Page 3 of 169 CASA Part 66 - Training Materials Only Table of Contents Integrated Circuits and Operational Amplifiers (4.1.3.2) 9 Learning Objectives 9 Summary 9 Digital Systems 10 Digital vs Analogue Systems 10 Advantages of Digital Techniques 10 Limitations of Digital Techniques 12 Integrated Circuits 15 Microelectronics 15 Integrated Circuits 16 Logic Integrated Circuits 18 Logic Gates and Logic Circuits 19 Linear Integrated Circuits 22 Operational Amplifiers 25 The Operational Amplifier 25 The Ideal Op-Amp 26 The Practical Op-Amp 27 Operational Amplifier Operation 27 Op-Amp Modes and Feedback 29 Single-Ended Input Mode 29 Differential Input Mode 29 Common-Mode Input Mode 29 Negative Feedback 30 Negative Feedback Application 31 Positive Feedback 31 Negative Feedback Usage 32 Non-Inverting Amplifier 32 Voltage-Follower 33 Inverting Amplifier 34 Differentiating Op-Amps 35 Integrating Op-Amps 37 Integrator with Capacitor 39 Comparator Op-Amps 40 Zero-Level Detection 41 2022-11-10 B2-04b Electronic Fundamentals Page 4 of 169 CASA Part 66 - Training Materials Only Over-Temperature Sensing Circuit 43 Amplifier Coupling 45 Resistive Capacitive (RC) Coupling 45 Inductive Capacitive (LC) Coupling 45 Transformer Coupling 45 Direct Coupled 46 Printed Circuit Boards (4.2) 47 Learning Objectives 47 Printed Circuit Boards 48 Introduction to PCBs 48 Basic PCB Construction 49 Through-Hole Technology 52 THT Component Mounting 53 Surface-Mounted Technology 54 PCB Terminology 55 PCB Additional Components 56 PCB Types 59 Single-Sided Boards 59 Double-Sided Boards 59 Multi-Layer Boards 60 Advanced PCB Construction 62 PCB Manufacture Process 62 PCB Substrate 64 Copper Foil 66 Pads 67 Vias and Through-Holes 68 Tracking 69 Clearances 70 Multi-Layer Design 71 Grounding 74 Bypassing 74 Flexible PCB 75 Servomechanisms (4.3.2) 78 Learning Objectives 78 Summary 78 Servomechanism Terminology 79 Servomechanisms 79 2022-11-10 B2-04b Electronic Fundamentals Page 5 of 169 CASA Part 66 - Training Materials Only Control Systems and Feedback 79 Open-Loop Control 81 Closed-Loop Control 82 Follow-Up 83 Analogue Transducers 85 Digital Transducers 89 Closed-Loop Control Operation 90 Hunting 91 Deadband 92 Null Condition 94 Damping 94 Overshooting 97 Synchros 98 Aircraft Error Detection Devices 99 Synchro Systems Components 101 Linear Variable Differential Transformer 101 Force Transducers 104 E and I Bar Transformer 105 E and I Bar Acceleration Sensor 106 C and Y Core Differential Transformer 107 Capacitance Transmitters 109 Inductance Transmitters 110 Pendulous Transmitters 112 Desynn 113 Synchro Principles 115 Synchro Symbols 117 Torque Transmitter 118 Differential Transmitter (TDX) 120 Torque Differential Receiver (TDR) 123 Torque Differential Transmitter (TDX) 123 Differential Subtraction 124 Differential Addition 126 Differential Synchro Wiring Interface 126 Differential Synchro Transmitter 127 Differential Transmitter (TDX) Symbols 128 Differential Synchro Example 129 Control Synchro Systems 129 2022-11-10 B2-04b Electronic Fundamentals Page 6 of 169 CASA Part 66 - Training Materials Only Synchro Control Transmitter (CX) 131 Synchro Control Transformer (CT) 131 Control Transformer Rotor 132 Synchro Control Transformer (CT) 132 Control Synchro System Operation 133 Control Transformer Symbols 135 Troubleshooting Servomechanisms 136 Troubleshooting 136 Synchro Connections 137 Resolver Synchro Systems 140 Resolvers 140 ADF Application of a Resolver 144 Resolver Synchro 144 Servo Motor Control Principles 146 DC Servo Motor Loop - Potentiometer 146 DC Servo Motor Loop - Amplifier 146 Two-Phase Servo Motor 147 Servo Motor Loop - Control Synchro Input 149 AC Servo Motor 150 Servo Motor Loop - Limited Rotation Synchro 151 Servo Motor Loop - Synchro Transmitter and Receiver 151 Servo Motor Loop - Differential Synchro 152 Position Control Servomechanism 153 Speed Control Servomechanism 154 Rate Generator and Servo 155 Servomechanism Performance 157 Response of Servomechanism 157 Ideal Servomechanism 158 Time Lag 158 Desired Servo Performance 159 Frictional Damping 159 Velocity Feedback Damping 160 Error-Rate Damping 163 Acceleration Feedback 164 Phase Advance Damping 165 Integral Control 166 Displacement and Rate Controls 167 2022-11-10 B2-04b Electronic Fundamentals Page 7 of 169 CASA Part 66 - Training Materials Only Summary of Servomechanisms 169 Advantages of Servomechanisms 169 Limitations of Servo Systems 169 2022-11-10 B2-04b Electronic Fundamentals Page 8 of 169 CASA Part 66 - Training Materials Only Printed Circuit Boards (4.2) Learning Objectives 4.2 Describe the function and use of printed circuit boards (Level 2). 2022-11-10 B2-04b Electronic Fundamentals Page 47 of 169 CASA Part 66 - Training Materials Only Printed Circuit Boards Introduction to PCBs A Printed Circuit Board or PCB for short, is a flat insulating surface upon which printed wiring and miniaturised components are connected in a predetermined design and attached to a common base. The image below shows a typical printed circuit board. Aviation Australia Double sided PCB - front (left) and back (right) Note that various components are connected to the board and the printed wiring is on the reverse side. With this technique, all interconnecting wiring in a piece of equipment, except for the highest power leads and cabling, is reduced to lines of conducting material (copper, silver, gold, etc.) deposited directly on the surface of an insulating circuit board. Since printed circuit boards are readily adapted as plug-in units, the elimination of terminal boards, fittings and tie points, not to mention wires, results in a substantial reduction in the overall size of electronic equipment. 2022-11-10 B2-04b Electronic Fundamentals Page 48 of 169 CASA Part 66 - Training Materials Only Schematic and PCB Layout Preceding Technology Before the advent of the PCB, circuits were constructed through a laborious process of point-to- point wiring. This led to frequent failures at wire junctions and short circuits when wire insulation began to age and crack. A PCB is found in almost every electronic device. If you have electronic components in a device, they are mounted on a PCB, big or small. Besides keeping the components in place, the purpose of a PCB is to provide electrical connections between the components mounted on it. As electronic devices have become more complex and require more components, the PCB has become more densely populated with wiring and components. 2022-11-10 B2-04b Electronic Fundamentals Page 49 of 169 CASA Part 66 - Training Materials Only Basic PCB Construction Printed circuit boards can be made from a variety of substances. They are usually a flat laminated composite made from non-conductive substrate materials with layers of copper circuitry buried internally or on the external surfaces. PCB The PCB can be as simple as one or two layers of copper, or in higher density applications they can have fifty layers or more. The flat composite surface is ideal for supporting the components that are soldered on or attached to the PCB, while the copper conductors connect the electronic components to one another. 2022-11-10 B2-04b Electronic Fundamentals Page 50 of 169 CASA Part 66 - Training Materials Only Base or Substrate Material The base material of a printed circuit board, referred to as the substrate or laminate, is made of phenolic paper, epoxy paper and epoxy glass. The metal foil, referred to as the cladding, is usually made of copper but other types of metal may be used. The substrate board is produced first and then the cladding is bonded to it. PCB cutaway (single, double and multi layer) Conductor Pattern The substrate of the board itself is an insulating and non-flexible material. The thin wires that are visible on the surface of the board are part of a copper foil that initially covered the whole board. In the manufacturing process this copper foil is partly etched away and the remaining copper forms a network of thin wires. These wires are referred to as the conductor pattern or the tracks and they provide the electrical connections between the components mounted on the PCB. A basic printed circuit board has the copper circuit pattern or foil on one side of the board. Holes are drilled through pads or terminals in the foil and board. The component leads are pushed through the holes from the other side of the board. The leads are then soldered to the copper foil to complete the circuit connections. PCB Conductor Pattern 2022-11-10 B2-04b Electronic Fundamentals Page 51 of 169 CASA Part 66 - Training Materials Only Solder Mask and Silk Screen What gives the PCB its green or brown colour is the solder mask. This is an insulating and protective coat that protects the thin copper wires from corroding and prevents solder from attaching outside the connection points for the components. Solder mask A silk screen is printed on top of this coloured mask. This consists of text and symbols (often white) printed on the board to label the locations for the different components that are to be mounted. The silk screen is also referred to as the legend. PCB silk screen used to label components 2022-11-10 B2-04b Electronic Fundamentals Page 52 of 169 CASA Part 66 - Training Materials Only Through-Hole Technology The components that are mounted on one side of the board while its legs are soldered on the opposite side are called through-hole PCBs often referred to as Through-Hole Technology (THT). Such components take up a large amount of space and require a hole to be drilled in the PCB for every leg. Through-hole components Hence, their legs occupy space on both sides of the board, and the connection points for them are also fairly large. On the other hand, THT components are fairly good mechanically connected to the PCB compared to surface-mounted devices, which will be discussed below. Connectors for cables and similar devices also have to withstand mechanical stress and are usually THT. Aviation Australia Through-hole technology 2022-11-10 B2-04b Electronic Fundamentals Page 53 of 169 CASA Part 66 - Training Materials Only THT Component Mounting To fasten the components to the PCB, their legs are soldered to the conductor pattern. On the most basic PCBs (single-sided boards) the components are located on one side of the board and the conductor pattern on the opposite side. This requires holes in the PCB for the component legs to penetrate the board. Component mounting Hence the legs are soldered to the PCB on the opposite side of where the components are mounted. The top and bottom side of a single sided PCB is therefore respectively referred to as the 'component side' and 'solder side'. PCB soldering (bottom side) 2022-11-10 B2-04b Electronic Fundamentals Page 54 of 169 CASA Part 66 - Training Materials Only Surface-Mounted Technology The legs of components that are made using Surface Mounted Technology (SMT) are soldered to the conductor pattern on the same side of the PCB on which the component is mounted. This technology therefore does not require a hole in the PCB for every leg of the component. Surface-mounted components could even be mounted on both sides of the PCB directly underneath each other. SMT components are also much smaller than THT components. This makes PCBs with SMT components much more dense compared to similar PCBs with THT components. Today, SMT components are also cheaper than THT components. It is therefore no surprise that most components on main boards nowadays are SMT. Since the connection points and component legs are so small it becomes very hard to solder on an SMT component manually. Considering that machines do almost all assembly, this issue only becomes important when repairs have to be done. Surface Mounted Technology 2022-11-10 B2-04b Electronic Fundamentals Page 55 of 169 CASA Part 66 - Training Materials Only PCB Terminology Often PCBs have distinct labelling. The foil pattern takes various shapes, depending on function of circuit. Heat sinks are used to dissipate heat from components and require large areas. Voltage and ground lines or planes are long and slender and follow a path so as to provide power to components on board. Terminals or pads are points drilled with holes to accommodate component leads. Conductors or runs are thin foil strips between components. Edge connectors are part of foil that connects circuit board to a special plug. Aviation Australia PCB with some components labelled 2022-11-10 B2-04b Electronic Fundamentals Page 56 of 169 CASA Part 66 - Training Materials Only PCB Additional Components Component Sockets If a component needs to be removable from the PCB after it is manufactured, it is mounted on the board with the use of a socket. The socket is soldered to the board while the component can be inserted and taken out of the socket without the use of solder. Component socket Components sockets 2022-11-10 B2-04b Electronic Fundamentals Page 57 of 169 CASA Part 66 - Training Materials Only Edge Connector To connect a PCB to another PCB, an edge connector is often used. The edge connector consists of small uncovered pads of copper located along one side of the PCB. These copper pads are actually part of the conductor pattern on the PCB. The edge connector on one PCB is inserted into a matching connector (often referred to as a slot) on the other PCB. In PC graphic cards, sound cards and other similar products are connected to the main board with the use of edge connectors. Edge connector (top) and slot (bottom) 2022-11-10 B2-04b Electronic Fundamentals Page 58 of 169 CASA Part 66 - Training Materials Only PCB Types Single-Sided Boards Most basic boards have the components mounted on one side of the board and the conductor pattern on the opposite side. Since there only is a conductor pattern on one side, this type of PCB is called single-sided. It has severe limitations when it comes to routing the wires in the conductor pattern (since there is only one side no wires can cross and they have to be routed around each other), so it is only used in very primitive circuits. Single sided PCB top view (top) and bottom view (bottom) 2022-11-10 B2-04b Electronic Fundamentals Page 59 of 169 CASA Part 66 - Training Materials Only Double-Sided Boards These types of boards have a conductor pattern on both sides of the board. Having two separate conductor patterns requires some kind of electrical connection between them. Such electrical connections are called vias. A via is simply a hole in the PCB that is filled or plated with metal and touches the conductor pattern on both sides. Since the surface available for the conductor pattern is twice as large compared to a single-sided board, and as wires can now cross (by routing them on opposite sides of the board), double-sided PCBs are much more suited for complex circuits than the single-sided ones. Double sided PCB top view (top) and bottom view (bottom) 2022-11-10 B2-04b Electronic Fundamentals Page 60 of 169 CASA Part 66 - Training Materials Only Multi-Layer Boards A typical multi-layer PCB (which covers most of the PCBs used to implement a complex circuit) consists of a sandwich of conducting and insulating layers. It is onto this format that the PCB design must be produced. The sandwich of layers, or stack of layers, alternates between some sort of non-conducting dielectric layer and copper foil which has been patterned to form the circuit connections. Multi-layer PCB design 2022-11-10 B2-04b Electronic Fundamentals Page 61 of 169 CASA Part 66 - Training Materials Only Advanced PCB Construction PCB Manufacture Process This is a general overview of the PCB manufacturing steps. Aviation Australia Circuit example - High Speed NiCd Charger Components for this circuit need to be mounted on a printed circuit board. Firstly, components are laid out on board for ease and economy of construction. Typically done on a breadboard as a prototype. Then a virtual circuit can be produced using PCB creation software. 2022-11-10 B2-04b Electronic Fundamentals Page 62 of 169 CASA Part 66 - Training Materials Only Aviation Australia Components laid out Circuit track is then designed from component layout. This is usually done with software. Aviation Australia PCB overlay and circuit track 2022-11-10 B2-04b Electronic Fundamentals Page 63 of 169 CASA Part 66 - Training Materials Only Once complete, the design is sent for manufacturing. Aviation Australia PCB produced Once the PCB has been created, the component can be soldered to the device. 2022-11-10 B2-04b Electronic Fundamentals Page 64 of 169 CASA Part 66 - Training Materials Only PCB Substrate As previously discussed, the base (or substrate) material of a printed circuit board is typically made of phenolic paper, epoxy paper or epoxy glass. The main criteria of the base layer of a PCB is that is does not conduct electricity. The quality of the material is also important and helps to avoid problems like open circuit, delamination caused by inflation and other malfunctions. The base should also be heat resistant. PCB materials can be classified according to their properties. The base material of a PCB is basically composite material made of a dielectric layer and conductor or high purity (copper foil). PCB substrate (also referred to as the base or laminate) 2022-11-10 B2-04b Electronic Fundamentals Page 65 of 169 CASA Part 66 - Training Materials Only Dielectric A dielectric material is a substance that is a poor conductor of electricity, and used as an insulating layer in the PCB build up. Porcelain, mica, glass, plastics and some metal oxides are good dielectrics. The lower the dielectric loss, (the proportion of energy lost as heat) the more effective the dielectric material. The dielectric can be one of a number of different materials (depending on the application). The most common is FR-4 and this is formed from an epoxy resin that is reinforced using glass fibres. This dielectric is manufactured in the form of a thicker layer (often called a laminate) or a thinner layer called a prepreg (pre-impregnated) that is normally manufactured from a resin-impregnated glass cloth. Laminates and prepregs are available in a variety of thicknesses and can be bonded together to form even thicker layers if the application demands it. A typical laminate may be between 0.1 mm and 0.25 mm thick whilst a typical prepreg may be between 0.05 mm and 0.2 mm. PCB Materials classification according to reinforced materials (most common): 1. Paper board - FR-1, FR-2 (Phenolic Cotton Paper), FR-3 (cotton paper and epoxy) 2. Epoxy Glass Cloth - FR-4 (Woven Glass and Epoxy), FR-5 (Woven Glass and Epoxy) 3. Composite board - CEM-1 (Cotton Paper and Epoxy), CEM-3 (Non-woven Glass and Epoxy) 4. HDI board (RCC - Resin Coated Copper) 5. Special board (metal board, ceramic board, etc.). FR means Flame Retardant and CEM means Composite Epoxy Materials. PCB substrate is the base (dielectric) layer 2022-11-10 B2-04b Electronic Fundamentals Page 66 of 169 CASA Part 66 - Training Materials Only Copper Foil The copper foil forming the interconnection is available in a number of weights, e.g., 0.5 oz, 1 oz or 2 oz. The weight refers to the weight of a standard area of the foil, and 0.5 oz is about 10 µm thick. The most common weight for general-purpose applications is 1 oz, but the higher weights allow more current to be carried for a particular track width. For example, a 0.5 oz track that is 20 mm long and 0.5 mm wide has a resistance of 38 mΩ, whereas the same track in 2 oz copper has a resistance of 9.5 mΩ. Copper foil Pads Pads provide the copper surface that the legs of the components will be soldered to, providing the necessary electrical connection. The area of these pads has an important part to play in the final manufacturing process Pad sizes, shapes and dimensions will depend not only upon the components used but also the manufacturing process used to assemble the board, among other things. The PCB package should come with a set of basic component libraries with some standard-sized pad values. Pads (in a through hole PCB) 2022-11-10 B2-04b Electronic Fundamentals Page 67 of 169 CASA Part 66 - Training Materials Only There is an important parameter known as the pad:hole ratio. This is the ratio of the pad size to the hole size. Each manufacturer will have its minimum specification for this. As a simple rule of thumb, the pad should be at least 1.8 times the diameter of the hole, or at least 0.5 mm larger. This is to allow for alignment tolerances on the drill and the artwork on top and bottom layers. This ratio gets more important the smaller the pad and hole become, and it is particularly relevant to vias. Vias and Through-Holes The multiple layers of copper foil are interconnected by through-holes and vias. Both of these structures are holes in the laminate with electroplated copper on the surface forming a bridge between two (or more) conducting layers. The distinction between a through-hole and a via lies in their specific purpose. A through-hole is sized to allow a pin of a component to pass through from one side of the PCB to the other (allowing it to be soldered to the PCB), while a via is merely to connect two points in the circuit that are on different layers. For this reason, vias are usually smaller in diameter than through-holes. PCB vias and pads Through-holes go from one side of the PCB to the other. This is not necessary for a via, as a via can bridge two layers inside the PCB and may not be visible at the surface of the PCB. Such a via is called a blind via. 2022-11-10 B2-04b Electronic Fundamentals Page 68 of 169 CASA Part 66 - Training Materials Only There must be an area of copper around a through-hole to allow the solder to form a proper meniscus and adhere properly to the PCB. This is not the case for a via, and a via may have very little copper around it – a landless via. Through-holes are only required where through-hole components are being used. In the case of a PCB using only surface-mount devices, there are no through-holes (except for the external connectors, possibly). The surface-mounted devices are soldered to small areas (or lands) of copper on the external surface of the PCB and vias are used to carry the connections to other layers. Holes in vias are usually a fair bit smaller than component pads, with 0.5 mm-0.7 mm being typical. Tracking There is no recommended standard for track sizes. The size of track used depends on the electrical requirements of the design, the routing space and clearance available and personal preference. As a general rule, though, the bigger the track width, the better. Bigger tracks have lower DC resistance, lower inductance, can be easier and cheaper for the manufacturer to etch and are easier to inspect and rework. PCB tracking dimensions 2022-11-10 B2-04b Electronic Fundamentals Page 69 of 169 CASA Part 66 - Training Materials Only The lower limit of track width will depend upon the track/space resolution that the PCB manufacturer is capable of. For example, a manufacturer may quote a 10/8 track/space figure. This means that tracks can be no less than 0.25 mm wide, and the spacing between tracks (or pads, or any part of the copper) can be no less than.020 mm. Real world typical figures are 0.25/0.25 and.020/.020 for basic boards. The lower the track/space figure, the greater care the manufacturer has to take when aligning and etching the board and, hence, the greater the cost of production. As a start, use, for example, 0.635 mm for signal tracks, 1.25 mm for power and ground tracks, and 0.25 mm, 0.38 mm for going between Integrated Circuit (IC) and component pads. Some designers like the look of smaller signal tracks like 0.25 mm or 0.38 mm, while others like all of their tracks to be big and chunky. Good design practice is to keep tracks as big as possible, and then to change to a thinner track only when required to meet clearance requirements. In practice, track width will be dictated by the current flowing through it and the maximum temperature rise of the track that can be tolerated. Remember that every track will have a certain amount of resistance, so the track will dissipate heat just like a resistor. The wider the track the lower the resistance will be. The thickness of the copper will also play a part, as will any solder coating finish. 2022-11-10 B2-04b Electronic Fundamentals Page 70 of 169 CASA Part 66 - Training Materials Only Clearances Electrical clearances are an important requirement for all boards. Too tight a clearance between tracks and pads may lead to hairline shorts and other etching problems during the manufacturing process. These can be very hard to fault find once the board is assembled. At least 0.38 mm is a good clearance limit for basic through-hole designs, with 0.25 mm or 0.20 mm being used for more dense surface mount layouts. The clearance will vary depending on whether the tracks are on an internal layer or the external surface. They also vary with the operational height of the board above sea level, due to the thinning of the atmosphere at high altitudes. Creepage is the shortest distance between conductor traces on a PCB along the surface of the insulation material while clearance is defined as the minimum distance through the air (line of sight) between two conductor traces. PCB clearance 2022-11-10 B2-04b Electronic Fundamentals Page 71 of 169 CASA Part 66 - Training Materials Only Multi-Layer Design A multi-layer PCB is much more expensive and difficult to manufacture than a single- or double-sided board, but it really does give you a lot of extra density to route power and signal tracks. By having the signals running on the inside of the board, more components can be placed more tightly on the board to give a more compact design. Multi-layer boards usually come in an even number of layers, with 4, 6 and 8 layers being the most common. A typical 6-layer board is illustrated in the diagram below. Multilayer PCB (6 layer) With a multi-layer board, typically dedicate one complete layer to a ground plane and another to power. If it is a digital-only board, then dedicate the entire power layer also. If there is room on the top or bottom layer, it is possible to route any additional power rail tracks on there. Once power has been taken care of on the inner layers, there will be much more room available for signal tracks. 2022-11-10 B2-04b Electronic Fundamentals Page 72 of 169 CASA Part 66 - Training Materials Only Multi-layer typically have a ground plane and power plane If power planes are vital and you have a lot of connections to route, then move from 4 to 6 layers, as this will give four full signal routing layers and two layers dedicated to power. Eight layers and above is basically more of the same. With multi-layer design come the options of using different types of vias to improve routing density. There are three types of vias: Through vias go through the whole board, and can connect any of the top, bottom or inner layers. These can be wasteful of space on layers which are not connected. Blind vias go from the outside surface to one of the inner layers only. The hole does not protrude through the other side of the board. The vias is in effect blind to the other side of the board. Buried vias only connect two or more inner layers, with no hole being visible on the outside of the board. The hole is completely buried inside the board. 2022-11-10 B2-04b Electronic Fundamentals Page 73 of 169 CASA Part 66 - Training Materials Only Aviation Australia Examples of different types of vias Blind and buried vias cost more to manufacture than standard vias. But they are very useful and practically mandatory for very high density designs like those involving Ball Grid Array (BGA) components. Note: The issues raised in the following sections will be raised in much more detail later in this module. Grounding Grounding is fundamental to the operation of many circuits. Good or bad grounding techniques can make or break the design. There are several grounding techniques which are always good practices to incorporate into any design. PCB Grounding 2022-11-10 B2-04b Electronic Fundamentals Page 74 of 169 CASA Part 66 - Training Materials Only Bypassing Active components and points in the circuit which draw significant switching current should always be bypassed. This serves to smooth out the power rail going to a particular device. Bypassing uses a capacitor across the power rails as physically and electrically close to the desired component or point in the circuit as possible. Bypassing capacitors 2022-11-10 B2-04b Electronic Fundamentals Page 75 of 169 CASA Part 66 - Training Materials Only Flexible PCB Also known as flex circuits, this is a technology for assembling electronic circuits by mounting electronic devices on flexible plastic substrates, such as polyimide, PEEK or transparent conductive polyester film. Additionally, flex circuits can be screen printed silver circuits on polyester. Flexible electronic assemblies may be manufactured using components identical to those used for rigid printed circuit boards, allowing the board to conform to a desired shape or to flex during its use. Flexible PCB 2022-11-10 B2-04b Electronic Fundamentals Page 76 of 169 CASA Part 66 - Training Materials Only These flexible printed circuits (FPC) are made with photolithographic technology. An alternative way of making flexible foil circuits or flexible flat cables (FFCs) is laminating very thin (0.07 mm) copper strips in between two layers of polyester (PET). These PET layers, typically 0.05 mm thick, are coated with an adhesive which is thermosetting and will be activated during the lamination process. FPCs and FFCs have several advantages in many applications: Tightly assembled electronic packages, where electrical connections are required in 3 axes, such as cameras (static application) Electrical connections, where the assembly is required to flex during its normal use, such as folding cell phones (dynamic application) Electrical connections between sub-assemblies to replace wire harnesses, which are heavier and bulkier, such as in cars, rockets and satellites Electrical connections where board thickness or space constraints are driving factors. Ease of manufacturing or assembly. Flex circuits are often used as connectors in various applications where flexibility, space savings or production constraints limit the serviceability of rigid circuit boards or hand wiring. A common application of flex circuits is in computer keyboards; most keyboards use flex circuits for the switch matrix. In liquid crystal display (LCD) fabrication, glass is used as a substrate. If thin flexible plastic or metal foil is used as the substrate instead, the entire system can be flexible, as the film deposited on top of the substrate is usually very thin, on the order of a few micrometres. Organic light-emitting diodes (OLEDs) are normally used instead of a back-light for flexible displays, making a flexible OLED display. Most flexible circuits are passive wiring structures that are used to interconnect electronic components such as integrated circuits, resistors, capacitors and the like, however some are used only for making interconnections between other electronic assemblies either directly or by means of connectors. Flexible circuits are found in industrial and medical devices where many interconnections are required in a compact package. Cellular telephones are another widespread example of flexible circuits. Flexible solar cells have been developed for powering satellites. These cells are lightweight, can be rolled up for launch and are easily deployable, making them a good match for the application. They can also be sewn into backpacks or outerwear. 2022-11-10 B2-04b Electronic Fundamentals Page 77 of 169 CASA Part 66 - Training Materials Only