APU.docx
Document Details
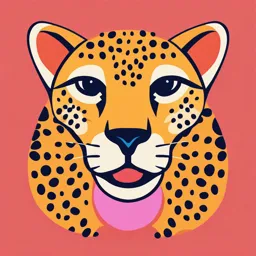
Uploaded by PhenomenalNumber
Full Transcript
APU 2A-49-10: Auxiliary Power Unit (APU) General The purpose of the Gulfstream 650 Auxiliary Power Unit (APU) system is to supply anauxiliary source of pneumatic power (bleed air) andelectrical power during flight or ground operations. The RE220 APU is a turbine engine composed of one compressor...
APU 2A-49-10: Auxiliary Power Unit (APU) General The purpose of the Gulfstream 650 Auxiliary Power Unit (APU) system is to supply anauxiliary source of pneumatic power (bleed air) andelectrical power during flight or ground operations. The RE220 APU is a turbine engine composed of one compressor stage and two turbine stages with accessory mountings for a 40 KVA generator and a Load Control Valve that provides compressor pressurized air for the aircraft pneumatic system bleed air supply manifold.The APU allows the aircraft to operate independently without requiring a ground air cart and external AC I DC power to start the aircraft engines. The APU also provides the ability to operate the air conditioning packs to cool or heat the aircraft interior without the necessity of starting the engines while preparing for departure. During flight, the APU can be used as a backup eledrical power supply if a malfunction renders one or both aircraft engine generators inoperative. If necessary, APU air may also be used to assist in air-starting an engine if the aircraft altitude is 30,000 ft and below. TheAPU operating envelope extends upto 45,000 ft ifthe APU is started at a lower altitude.The APU is guaranteed to start at or below 30,000 feet. The APU is housed withina fireproof titanium container in the aft equipment bay. The air intake for the APU is on the top of the aircraft fuselage to the left of the dorsal fin forward of the vertical stabilizer.The APU exhaust is below the right engine pylon. The APU is mounted on two rails within the housing container and a hatch on the left side of the aircraft fuselage can be opened and the APU removed from the aircraftfor maintenance byslidingthe unit out horizontally onthe mounting rails. However, if necessary, three removable panelsontheAPU housingcontainer provide maintenance and servicing access with the unit in place. The APU system is divided into the following subsystems: 2A-49-20: APU Mechanical Assembly 2A-49-30: APU Control and Operation 2A-49-20: APU Mechanical Assembly General: The Auxiliary Power Unit (APU) assembly comprises the following subsystems: Powerplant Electronic Control Unit (ECU) Starter and lgniters Fuel Control Lubrication System Fire Detedion and Warning System Alternating Current (AC) Generator Bleed Air Description of Subsystems, Units and Components: (See Figure 1.APU Compartment General Arrangement thru Figure 3. APU Air System Simplified Block Diagram.) Powerplant System: The APU is a single shaft, constant speed gas turbine engine that drives an accessory gearbox connected to a 40 kVA generator and provides bleed air to the supply manifold of the pneumatic system. The APU mechanical assembly indudes the following components: Air Intake: An air inlet door mounted on the top left side of the fuselage (infront of the vertical stabilizeQ provides an intake to the APU turbine. The door is connected to a duct made of composite material that routes external air intothe APU and surrounding endosure. The dud is split downstream of the inlet door with one section of the duct providing flow into the APU inlet plenum, and the other sedion flow for the oil cooler and circulatingair cooling for the APU exterior. The cooling air stream is routed to merge with the APU exhaust where it is vented overboard. The inlet door is controlled by the APU ECU and operated by an electrical aduator. A Rotary Variable Displacement Transducer (RVDT) attached to the actuator body provides position feedback to the ECU. The ECU opens the inlet when the APU MASTER switch, located on the APU panel on the Cockpit Overhead Panel (COP), is selected ON (ground only). \l\lhen the air inlet door has opened, a READY light illuminates on the APU panel, indicating that the APU is configured for starting. (APU inlet door position is shown graphically on the Doors synoptic 213 window and the APU I Bleed system 116 window - see Section 28-09-00.)Theinlet door is fully open when the APU is started on the ground, but if the aircraft is airborne, the amount of inlet opening is regulated by the ECU to match the air requirements for combustion and cooling. The inlet door maximum openingis 45% upto an altitude of 25,000 ft. The maximum opening is 100%, if necessary, above that altitude. The inlet door remains open for a period when the APU is shut down in order to provide airflow for the APU cooldown cyde. The door is fully closed only after APU rpm degrades below 40%. Two sensors are installed in the air inlet duct. A T2 temperature sensor provides ambient air data to the ECUfor fuel control metering. Temperatureinformation from the sensor is also used by the ECU to determine if reverse airflow is entering the inlet duct from a malfunction in the bleed air Load Control Valve (LCV). A separate P2 pressure sensor provides information to the ECU for fuel control management, air inlet door position commands and Surge Control Valve (SCV) operation. Compressor and Turbine: The APU has a single-stage compressor section coupled on a common shaft to a two-stage turbine. The APU is mounted horizontally so that air drawn into the inlet duct impinges directly onto the blades of the compressor section.The compressor inaeases the pressure of the ambient air and routes some of the air around the turbine stage for cooling and injects the rest into the annular-shaped combustor surrounding the two turbine stages. In the combustor, the air is mixed with fuel sprayed through atomizers and the fuel I air mixture ignited by electrically-powered igniters. The resulting pressure drives the turbine stages. The hot gases from the turbine section are mixed with cooling air flowing around the section and from the exhaust side of the oil cooler split intake duct. The resulting mixture is significantly cooler and acoustically quieter when exhausted overboard on the right rear of the fuselage below the engine pylon. Accessory Gearbox: An accessory gearbox mounted atthe compressor end of the APU is turned by the axial drive shaft. The gearbox converts the high rpm of the drive shaft to a lower rpmwith higher torque suitable for powering the APU accessories. The gearbox drives the AC generator and APU oil pump and provides the mounting interface for the APU starter. A speed sensor, mated to the gear teeth on the compressor bearing, provides data to the ECU for on-speed control and overspeed protection during APU operation. The sensor uses a permanent magnet surrounded by dual coils to generate a voltage output to the ECU proportional to APU rpm. Surge Control Valve (SCV): A SCV is installed on the APU to promote uninterrupted smooth air flow through the compressor and turbine stages. The ECU opens the SCV when the APU is started above 16,500 ft. VVhen the valve is open, some air is bled from the compressor section is ducted to discharge into the APU exhaust shroud through a separate port. Exhaust: Spent exhaust gases from the APU turbine section are directed through a tailpipe exhaust assembly overboard, venting beneath the right engine nacelle. The tailpipe shroud has a larger diameter than the APU turbine exhaust exit opening. As exhaust gases pass through the shroud, ambient air in the APU compartment is drawn into the tailpipe assembly by the ejector pump action of the gas flOIN. Ambient air flow decreases the temperature of the APU exhaust and aeates alower pressure withinthe compartment, causing additional airflow that cools the APU components and accessories. Mixing ambient air with the exhaust also acts to reduce the noise and temperature levels of the exhaust. Two Exhaust Gas Temperature (EGT) sensors are mounted to protrude into the stream of gases exiting the turbine section. The sensors sample the gases prior to mixing with cooling airflow to provide an accurate indication of APU combustion. Each of the sensors has two probes (one short and one long) to furnish accurate data for the whole exhaust stream to the ECU. The ECU uses the temperature information to manage fuel flow to maintain the APU within operating limits. The EGT sensors provide continuous temperature sampling from 400°F- 1300°F (204°C- 704°C) and can detect transient temperature rises up to 1900°F (1038°C). Because the APU exhaust is located beneath the right engine pylon, starting the APU on the ground is inhibited with the lower cowling open since the APU exhaust high temperature gases would seriously damage the cowling.An amber warning indicator on the APU control panel (located on the COP) illuminates whenever the lower cowling on the right engineis open for servicingor maintenance and indicates to the flight crew that the APU cannot be started untilthe cowling is dosed. APU starting is prevented by using an input from the two fan cowl position sensing switches on the nacelle. Both switches must indicate that the cowl is open in order to prevent the START pushbutton electric signal from reaching the ECU. The start prevention circuit is routed through the combined Weight-On-Wheels CNQW) sensor to ensure that the cowl position switch inputs are only used during APU starts on the ground. The APU start signal cannot be interrupted by the switches while in the air. Electronic Control Unit (ECU): The ECU is a microprocessor with embedded software that provides independent control and operational monitoring of the APU through direct wire connections to the mechanical components of the APU and ARINC 429 bus connections to Modular Avionics Units (MAUs) #1 and #2 for aircraft sensor data monitoring ambient atmospheric conditions.The ECU is physically located in the Aft Electronics Equipment Rack (AEER) in the baggage compartment. The ECU is powered through the APU MASTER switch by the Left Essential DC bus throughthe APU CONT #1 circuit breaker or by the right battery bus through the APU CONT #2 circuit breaker (the ECU selects one of the two power sources if both are available).The ECU controls the APU start sequence induding opening the air inlet door, providingvoltage to the APU starter, initiating fuel flow to the combustion chamber when rpm is sufficient and powering the igniters. Once the APU has been started, the APU monitors performance and adjusts operating temperature and rpm by commands to the fuel control, controls and monitors the loading of the AC generator and provides bleed air to the pneumatic system, if selected, by varying the position of the LCV. The ECU also records the cumulative operating time of the APU whenever rpm reaches the normal range though an hourmeter function. The electronically-stored record of APU operationis usedto schedule periodic maintenance and inspection of the APU. The ECU provides operational protection for the APU by shutting down the unit if operating parameters are exceeded or if a fire is detected within the APU housing. The APU ECU uses two sets of operating limits: one for ground operation, termed the non-essential mode and another for inflight operation, termed the essential mode. Shutdown parameters for both modes are detailed in Section See Section 2A-49-30: APU Control and Operation. Starter and lgniters: APU Starter: The APU starter is electrically driven by the power source selected by the ECU. The starter is physically mounted on the accessory gearbox and spins up the APU through the gear interface. As the APU drive shaft rotates, the blades in the compressor section draw in ambient air through the open air inlet and furnish pressurized air flow to the combustion chamber. Fuel and ignition are introduced in the chamber and the APU accelerates through the forces generated in the turbine section. The starter is disengaged when the APU reaches 46% rpm if the aircraft is on the ground or 60% if the aircraft is airborne. lgniters: Two igniters in the combustion chamber supply an intermittent, high voltage spark to ignite fuel during the start sequence. Operation of the igniters is fully automatic and controlled by the ECU. During ground starting, ignition is terminated at 50% rpm. During an airstart, ignition is terminated at 98% rpm. The ignition unit will also automatically energize through the auto-relight function of the ECU if the APU flames out during operation. Fuel Control System: Fuel is supplied to the APU from the left wing tank using the left mainfuel pump (the right main tank and pump may be used if the crossflow valve is opened). Pressurized fuel is routed through the APU fuel shutoff valve on the left wing rear beam structure that is controlled by the APU MASTER switch and the ECU. A fuel line transits aft from the shutoffvalve to supply the APU fuel control. The fuel control is a dosed-loop system that receives control inputs from the ECU. The unit combines a fuel pump, filter, pressure regulator and metering valve into a single Line Replaceable Unit (LRU). The ECU calculates the appropriate output from the metering valve using data inputs for atmospheric conditions from the MAUs and APU-mounted speed and temperature sensors. The correct amount of fuel is delivered to the combustion section, where it is atomized and mixed with compressor section air for combustion. The ECU also provides protective shutdowns of the APU by interrupting fuel flow at the fuel control unit. Note Pressure from a fuel tank boost pump is required to start the APU. Lubrication System: The APU lubrication system uses a lube (oil) pump to circulate pressurized oil to cool and lubricate the gearbox, bearings and shafts in the powerplant. Oil is containedin an integral 5.25 quart oil reservoir with an oil level sensor and a temperature probe. External air drawn through the oil cooler section of the APU air inlet ducts cools the oilas it passes through a oil cooler heat exchanger. Checking the oil level and I or oil servicing can be accomplished by two different methods. Itcan be done manually by removingthe gravity fill cap on the oil tank and visually inspecting the oil level. Oil can be added directly into the tank if servicing is required. The APU oil level is also electronically displayed on the oil replenisher, located on the left side of the tailcompartment, adjacent to the tailcompartment door. An oillevel reading is also indicated on the Ground Service synoptic page 213window or SMC, Utility, Engine Oil menu. Automatic servicing is accomplished using the oil replenisher. The oil replenisher is powered by the Ground Service bus. For more information about oil servicing and oilreplenisher operation, see Section 04-02-30: Auxiliary Power Unit (APU) Oil Servicing. Fire Detection and warning System: Fire detection and warning for the APU is provided by an assembly consisting of a hermetically sealed stainless steel loop filled with helium and a stabilizing chemical.Embedded withinthe loop isa pressure sensor element. VVhen heat is applied to the detector loop,the pressure of the helium within rises, which triggers the sensor element. The sensor communicates the existence of fire in the APU compartment to MAUs #1, '#2 and '113.The MAUssignalthe Monitor and Warning System (MWS)that intum generates Crew Alerting System (CAS) messages for display in the cockpit. Hard-wired connections from the detector switches initiate illumination of the FIRE legend on the APU control panel on the COP and the red MASTER WARN light on the cockpit glareshield. If the aircraft is on the ground, the warning hom in the nose wheel well will also sound. The ECU automatically initiates animmediate protective shutdown ifa fire exists, bypassing the normal APU cool down period. (Automatic APU shutdown is inhibited during FIRE TEST checks.) For a complete description of the APU fire detection and protection features, see Section 2A-26-20: Engine and Auxiliary Power Unit (APU) Fire and Overheat Detection and warning System and Section 2A-26-30: Engine and APU Fire Extinguishers. Alternating Current (AC) Generator: A generator mounted on the APU gearbox provides a source of Alternating Current (AC) power for use on the ground or in flight if an engine-driven generator is not available. The APU generator produces three-phase 400 Hz 115 I 120 volt power and can deliver up to 40 kVA. The generator can provide a full 40 kVA output up to the limit of the APU operating envelope of 45,000 ft. VVhen the APU has reached an operating rpm of 99% for at least two seconds, the APU is capable of driving the generator.The APU generator has a Generator Control Unit (GCU) that monitors the voltage output and phase sequencing of the generator.If the output of the generator is within acceptable parameters and the APU is at operating rpm, the ECU determines that the APU generator is ready to assume aircraft electrical loads. The APU generator can be selected ON or OFF using the APU GEN pushbutton on the ELECTRICAL POVVE.R CONTROL panel on the COP. The amber ON legend within the pushbutton will illuminate when the APU generator is in use. The APU generator GCU will drop the generator off line if the quality of power produced by the generator falls outside of normal parameters. For a description of the APU generator and the AC power system, see Section 2A-24-20: AC Electrical Power System. APU Air: The APU air system provides pressurized air for engine starting and operation of the air conditioning packs on the ground. APU air may, under certain circumstances, also be used to provide additional pressurized air to aid in starting an engine in flight. APU air is available immediately after the APU has reached an operating speed of 99% rpm for at least two (2) seconds. If the APU was started under cold conditions, APU air loading will be delayed for 60 seconds, unless the bleed air is being used in attempting to start a main engine in flight. The ECU operates the APU load control valve to provide bleed air to the manifold supply duct when the pushbutton switch labelled APU on the BLEED AIR control panel on the COP is selected to ON. VVhen the load control valve is open, the blue ON legend within the switch will illuminate. The ECU adjusts fuel flow at the fuel control to maintainthe APU rpm at 100% when providing bleed air loads. APU air is drawn off of the compressor section of the powerplant and ducted through a check valve that prevents engine bleed air pressure from disrupting airflow withinthe APU. Additional information regarding APU air is contained in Section 04-02-50: Pneumatic Servicing. Controls and Indications: See Section 2A-49-30: APU Control and Operation. Limitations: See Section 2A-49-30: APU Control and Operation. Figure 1.APU Compartment General Arrangement INLET DUCT APU AIR INLET OIL COOLER DUCT APU GENERATOR APU EXHAUST DUCT LOAD CONTROL VALVE FUEL CONTROL UNIT & LUBE MODULE MANUAL OIL FILL CAP SURGE CONTROL VALVE STARTER IGNITION UNIT TIL-002624 OEM Provided Data APU Revision 4 2017-30 2A-49-00: B of 26 Figure 2. APU System Simplified Block Diagram STARTER CONTROL STARTER ______\ LEFT ENGINE \ \ I I I I \ I I I I I I I IENGINE I BLEED / SELEClOR 1 \ I I I I I RIGHT I ENGINE I I I I I .... _ _ _ _ _J GENERATOR ON . OFF GENERATOR OVTPUT TO BUS DISlRIBVTION TIL-002627A 0Iii! """ N )> "II 0 -=::: -I G) ... CLOSING "C 0 ::::J'" CD CO RATE 0!:. QC..DI. CD C::D!! ::::J c TORQUE ORIACE, SOLENOID Cl ADDCal ·- - -.. _...,""' 0Cit ::::J 0 ::::J'" Ill • • 0 , ,., -"T1· !if 0 ::::J Q CD ,.. RATE a:::I ;!S: CJ! " OPENING CONTROL C CD :iii: ::::t. C: CHAMBER ORIFICE ii )> 0 C') a.OSING OPENING C.S . "' :::! a m c 0 CD 0 0 CHAMEER CHAMBER )> (j) m' i,'g a -< Q 'tJ TO C lJl t/J - AIRCRAFT I )> Q < & I) \llSUAL POSITION :::;· m 'tJ Q:1: 3- ... OPENcw INDICATOR (JJ ::0 CD 0 0 "< i! :C;Du >"ll - CD CD 0 Q. \llSUAL CLOSED CLOSED t/J ..., A> ::::J Q POSITION S° Q C Q. 1::s INDICATOR fi 3 "U .'At>J -· CD - m;lJ ;A· c l> i g. ; n 3 )> o' 'tJ - TO APU ::j C 0 0 0 COMPAlmlENT Z ':-" o ::::i 8. Gl !;;! .:!! st [JJ N {Q_ "::::'. CD 0 )> -..J -· 'tJ S (i! C !;;! 1,, g_ !i o c2l r Q 0111 A> iii en ::::J -I :::!. COMPRESSOR NE 3 S. Q. ;;c APU -- --- T\JRBINEASSEMBLY J,. )> 3S" -..I 'P -a·')t>l !:l c:J = DENOTESAPU Bl..EEDAIRFLOW z - DENOTES COMPARTMENT AIRFLOW CD m a N Cl temperature and rpm are provided above the pushbuttons.A separate pushbutton switch on the BLEED AIR Control Panel on the COP is used to select the APU as a source of bleed air for the pneumatic system. The APU CONTROL panel indudes an APU fire warning light and a FIRE EXT pushbutton that can be used to inject the contents of the left fire extinguisher bottle into the APU container. After the APU has been started, operation of the APU is controlled by the Electronic Control Unit (ECU). The ECU functions autonomously to maintain APU temperature and rpm within limits during all load conditions. The ECU also controls the operation of the air inlet and maintains oversight of the po.ver quality of the AC generator by monitoring the Generator Control Unit (GCU). The ECU provides protective shutdowns of the APU if operational parameters are exceeded to prevent damage to the unit. Malfunctions are reported by the ECU to Modular Avionics Units (MAUs) #1 and #2 for communication to the Monitor and Warning System (MWS) for the generation of Crew Alerting System (CAS) messages and for storage in the Central Maintenance Computer (CMC) for post-flight analysis and troubleshooting. APU Control and Operation employs the following components: Electronic Control Unit (ECU) APU Control Panel APU I Bleed system 1/6 windo.v display Description of Subsystems, Units and Components: (See Figure 4. APU Controls and Indications Component Locations and Figure 5. APU Electronic Control Unit (ECU) Block Diagram.) Electronic Control Unit (ECU): General Description: The ECU is installed in the Aft Electronics Equipment Rack (AEER) in the baggage compartment. The ECU is powered from either the Right Essential DC bus or the Left Battery bus, depending upon availability. If both are available the ECU is powered by the bus with the highest voltage reading. The dual power sources allow for starting the APU with only battery power and provide redundancy in the event of an electrical malfunction when APU operation might be advantageous. The ECU is initially powered from one of the sources when the APU MASTER switch is selected ON and remains powered until five minutes after the APU rpm drops below 5% during shutdown providingtemperature and rpm data to the digital displays and APU I Bleed system window display through ARING 429 bus connections to the MAUS. The ECU control authority for the APU has two operating regimes: non-essential and essential.The non-essential regime is for normal ground operations when the APU is suppling electrical and I or pneumatic bleed air to aircraft systems. While operating in this regime the ECU will provide a full range of protective shutdowns to prevent damage to the APU. The protective logic is based on the assumption that for ground operations other sources can be used to supplant the APU to meet airaaft requirements, such as an external AC electrical supply or a pneumatic air cart. The essential control mode is confined to APU operation while the aircraft is airborne. The essential regime is initiated by the aircraft combined Weight-On-VVheels CNQW) sensors, transitioning to the "airbome" state. In the essential control mode, the ECU blocks some of the protective shutdowns of the APU since the control logic assumes that starting the APU while airborne would only be necessary during a malfunction or failure. Abnormal circumstances might require that the APU electrical power or bleed air be essential to recovering from the condition, therefore the safe condition of the aircraft takes precedence over any possible damage to the APU. The following table illustrates the control regime matrix: Protective Shutdown Non-Es.entia I Mode (Ground) Essential Mode (Fllght) Description Exhaust Gas Temperature (EGT) Overheat YES NO EGT above 732•c OilTemperature Hot YES NO Oiltemp above 148.9°C for 10 seconds with APU rpm >95% or during cooldown <70% Low OilPressure YES NO Oilpress <30 psiwith APU rpm >95% - shutdown in 15 seconds Low OilPressure Switch Failure YES NO ECU detects pressure switch failure Loss of both EGT Sensors YES NO If thermocouples fail,APU defaults to 2eo•c to maintain operation No Lightoff YES YES APU rpm increases above 10% with no EGT increase Starter Failure YES YES Start contactor energized with no increase inAPU rpm Slow Start YES YES APU rpm does not accelerate on schedule No Start Acceleration YES YES Starter energized with no rpm increase Fire YES YES Fire detector senses fire in APU ECU Failure YES YES ECU internal failure Overspeed YES YES Over 106% rpm Protective Shutdown Non-Essentia I Mode {Ground) Essential Mode (Flight) Description Loss of Speed Sensors YES YES ECU unable to determine rpm Loss of Overspeed Protection YES NO ECU overspeed circuit fails Reverse Airflow YES NO APU air inlet temp over 176°C for 5 seconds Underspeed YES NO Low rpm during any phase of operation Loss of DC Power YES YES DC power absent for 50 milliseconds or more Right Engine Cowl Open YES NO If airborne, assumes faulty indication Air Inlet Door Failed Closed YES YES Door not open in 30 seconds or with rpm>95% or door closes to only 5% open during cooldown (rpm <70%) - APU shuts down in 2 seconds VVhen the ECU initiates a protective shutdown of the APU during either the non-essential or essential operating regime, the nonmal APU cooldown period is bypassed in order to immediately eliminate the malfunction. Note The ECU exchanges data with the MAUs over the ARING 429 data bus system. If the data bus does not function property, the APU canstill bestarted and electrically loaded, however; without ambient atmospheric data from the MAUs, the APU cannot provide pneumatic bleed air. Loss of data bus communication would also prevent the MWS from generating CAS messages regarding the perfonmance of the APU. Non-Essential (Ground) Mode APU Operation: Ground APU start using only aircraft battery power: Prior to starting the APU, the flight crew ascertains that the aircraft battery is fully charged, that the APU fire detector is operational and that the left fire extinguisher bottle is full. These checks are accomplished by turning on the main batteries and ensuring a minimum of 22 volts, depressing the APU TEST pushbutton on the FIRE TEST panel on the COP and observing the correct indications and selectingthe display systems on with the CAS window adive to ensure that the following messages are not displayed: APU Fire Detector Fail (caution) L-R Fire Bottle Discharg (caution) The CAS message display should not contain any other messages indicating an APU malfunction. The display system should be turned off after checking for CAS messages to preserve battery power. The flight crew should verify that the amber R COWL OPEN warning indicator on the APU control panel (located on the COP) is not illuminated prior to attempting an APU start - an electrical interlock will prevent the APU from starting if the right engine cowling is open. The left mainfuel boost pump is normally used to provide fuel for APU starting. The pump is turned on by depressing the pushbutton labelled L MAIN on the FUEL SYSTEM panel and observing that the OFF legend within the pushbutton is not illuminated. If necessary, the right main boost pump can provide fuel pressure if the crossflow valve is opened - both the left and right main boost pumps are powered and controlled by the essential DC bus that is supported by the batteries. The APU start proceeds in the following order: The APU MASTER switch is depressed to ON and the blue ON legend withinthe switch illuminates The APU ECU performs a prestart Built-In Test (BID,opens the airinlet door and opens the fuel shutoff valve atthe left tank rear wing spar Within 10 -16 seconds when the BIT test is complete and the air inlet door and fuel shutoff valve configurations are correct, the ECU illuminates the READY light below the START switch Note lfthe Outside Air Temperature (OAD is 20°F (-6.6°C) or below, the APU will start, but requires alonger interval to reach normal speed. If the ECU senses oiltemperature below -23.3°C (-10°F), the starter motor may remain engaged for up to 50 seconds. When the READY light is illuminated, depressingthe START pushbutton closes the APU Start Contactor connecting the APU starter on the accessory gearbox to the battery tie bus, initiating rotation of the APU. The blue ON legend withinthe START switch will illuminate as long as the starter is engaged At 5% rpm, the fuel control shutoff valve opens and the igniters are energized At 12% rpm, the READY light extinguishes (if previously on) At 25% rpm, the fuel divider opens porting additional fuel to the fuel atomizers in the combustion chamber At 46% rpm, the ECU disengages the starter since the APU has sufficient rpm to accelerate using turbine stage energy and the blue ON legend withinthe START switch extinguishes At 50% rpm, the ignitors are de-energized and combustion is self-sustaining At 95% rpm, the hourmeter starts recording cumulative operating time of the APU After reaching at least 99% rpm for two seconds, the APU can support operation of the generator and after 60 seconds bleed air is available Stabilized on speed rpm of 100% equals 45,586 rpm (b) Normal Ground Operation: After the APU rpm has stabilized, the APU generator may be selected on by depressing the APU GEN switch on the ELECTRICAL POV\IE.R CONTROL panel on the COP. The amber ON legend within the switch will illuminate when the generator is providing power to aircraft systems. The APU Load Control Valve (LCV) may be opened by depressing the APU switch on the BLEED AIR Control Panel on the COP. The blue ON legend within the switch will illuminate when the LCV is open. Selecting the LCV open with the engine bleed switches off will automatically open the isolation valve. The APU will provide a bleed air source for air conditioning if the L PACK and I or R PACK switches are selected ON. A slight rise in APU EGT will be seen when the APU generator is selected on and I or the air conditioning packs are selected on (since the ECUwill increase fuel flow through the fuel control to accommodate the increased demands on the APU). If the normal operating temperature limit of732°C / 1350°F isreached, the ECUwill begindosing the LCV to reduce demand on the APU in order to remain within the temperature limit. Essential (Ai" Mode APU Operation: lnflight APU start using normal aircraft electrical power: The inflight start sequence of the APU is the same as that of the non-essential (ground) mode sequence with some modifications. The start may be monitored by selecting the APU I Bleed system display 1/6 window. The APU start proceeds in the foll011Ving order: The APU MASTER switch is depressed to ON and the blue ON legend within the switch illuminates The APU ECU performs a prestart BIT, detennines APU oil temperature, opens the air inlet door and opens the fuel shutoff valve at the left tank rear wing spar Within 10 - 16 seconds when the BIT test is complete and the air inlet door and fuel shutoff valve configurations are correct, the ECU illuminates the READY light below START switch When the READY light is illuminated, depressing the START pushbutton closes the APU Start Contactor connecting the APU starter on the accessory gearbox to the battery tie bus, initiating rotation of the APU. The blue ON legend within the START switch will illuminate as long as the starter is engaged At 5% rpm, the fuel control shutoff valve opens and the igniters are energized At 12% rpm, the READY light extinguishes (if previously on) At 25% rpm, the fuel divider opens, porting additional fuel to the fuel atomizers in the combustion chamber At 60% rpm, the ECU disengages the starter since the APU has sufficient rpm to accelerate using turbine stage energy and the blue ON legend within the START switch extinguishes At 95% rpm, the hounneter starts recording cumulative operating time of the APU At 98% rpm, the ignitors are de-energized After reaching 99% rpm for two seconds, the APU willsupport the generator or provide bleed air to assist engine starting if the aircraft is below 30,000 ft Stabilized on speed rpm of 100% equals 45,586 rpm (4) Commanded (Normal) Shutdown: The APU is shut down by selecting the APU STOP switch to OFF, which triggers the following sequence of events: The APU is shutdown by momentarily depressing the APU STOP switch. The ECU commands an APU cool down period. If the APU is in a loaded condition at the time of the commanded shutdown, the loads are shed and the APU enters a 60-second cool down period in which the RPM decreases Y.z% per second untilthe APU reaches 70% speed. If AIC is above 20,000 ft, all loads are shed and the APU cool down period is 100% APU for 60 seconds. If the APU Start switch is selected before the 60-second timer has expired, the APU is commanded back to 100% speed Note If the APU MASTER switch is selected OFF with the APU running, the 60-second cool down is bypassed and an immediate shutdown is commanded.The 60-second cool down bypass mode is not recommended by Gulfstream due to redudion in APU life. After the 60-second cool down period, the ECU enters the SHUTDOVVN mode. During each nonnal shutdown, the primary overspeed system is tested. The ECU software intentionally issues an invalid command to the primary overspeed circuit and verifies that the primary overspeed circuit de-energizes the output to the APU FCU mounted shutoff valve. The ECU then checks for a reduction in APU speed as confinnation that the valve has dosed. After completion of the test, the ECU commands the FCUtorque metering valve to dose (0 mA torque motor command). This action verifies the operation of the hardware overspeed circuit once each run VVhen the APU speed decreases below 63%, the ECU closes the air inlet door to only 10% open. When the door opening decreases, the ECU samples APU rpm until the speed drops below 40% and closes the door The ECU then initiates a five minute monitor period, continuing to supply power for EGT and rpm indications to ensure a complete shutdown. The ECU prompts an APU Master On (advisory) CAS message until the APU MASTER switch is selected off. If the APU MASTER switch is selected off before the five minute period expires, the message is not displayed Note If the APU START switch is depressed during the cool down period, the APU will accelerate back to nonnal rpm. Note The starter is capable of an immediate restart during spool down if the APU is at or below 7% rpm. Additional procedures for starting and operating the APU in various scenarios are detailed in the Airplane Flight Manual. b. APU Control Panel: (See Figure 6. APU Control Panel (1 of 2).) The APU control panel is located on the COP and contains the pushbutton switches and digital indicators necessary for APU operation. Installed on the panel are: A digital EGT indicator calibrated in degrees Centigrade (C0 with white numerals A digital rpm indicator with white numerals A MASTER pushbutton with a blue ON internal legend that illuminates when in use A START pushbutton with a blue ON internal legend that illuminates when in use A STOP switch with a blue ON internal legend that illuminates when in use A READY light with a blue internal legend that illuminates when the APU is ready to start A FIRE EXT guarded pushbutton A red FIRE annunciator light that illuminates when a fire is detected withinthe APU enclosure An amber R COWL OPEN indicator that illuminates ifthe rightengine cowling is open The ELECTRICAL POWER CONTROL panel on the COP contains the APU GEN pushbutton switch that connects the APU generator to the aircraft AC buses. The amber ON legend within the switch will illuminate when the APU generator is in service. The BLEED AIR Control Panel on the COP contains the bleed air pushbutton switch labelled APU that controls the APU LCV. V\/hen the APU is supplying bleed air to the supply manifold, the blue ON legend within the switch will illuminate. If the engine bleed air switches are selected off, opening the LCV with the switch will also open the supply manifold isolation valve. c. APU I Bleed System 116 Window Display: The APU I Bleed system 116 window display contains a graphic presentation of APU operating temperature and rpm in the format of simulated analog gages, a depiction of the air inlet door and digital readouts of bleed air manifold pressure. The top left gage figure is a readout of APU EGT. The display includes a pointer that rotates clockwise within a circular band and a digital readout of temperature with a resolutionof 1°C.The pointerand the digital readout are displayed in white ifthe APU EGT is within normal parameters. If EGT exceeds temperature limits and the pointer reaches the red portion of the circular band, both the pointer and the digital readout will tum red. To the right of the EGT gage is a rpm gage shown in the same format. If the rpm limit is exceeded and the pointer reaches the red band of the gage, both the pointer and digital readout of rpm are shown in red. Below the analog gage displays is a depiction of the aircraft fuselage shown from the rear. The APU air inlet door is indicated on the top left of the fuselage when the door is open - if the APU is not operating, the door is not shown. To the left and right of the fuselage depiction are digital readouts of pressure within the respective sides of the bleed air supply manifold. The readouts have a range from 0 - 256) with a resolution one psi. For a complete description of the APU I Bleed system page display, see Section 28-07-00. OEM Provided Data APU Revision 4 2017-30 2A-49-00: 1B of 26 Controls and Indications: Circuit Breakers (CBs): The following CBs protect the APU system: Circuit Breaker Name CB Panel Location Power Source APU PWR 1 POP E-7 L BATT Bus B APU PWR 2 CPOP E-7 R ESS DC Bus APU CTRL 1 POP E-6 L ESS DC Bus APU CTRL 2 CPOP E-6 R BAT BUS B APU DOOR POP E-6 L ESS DC Bus Crew Alerting System (CAS) Messages: The following CAS messages are associated with the APU system: Area Monitored CAS Message APU Fire Detector tJ ij11$(warning) APU Air Inlet Door position incorrect tf1ijii1).t.p (caution) ECU detects a fault that would shut down the APU if in non-essential mode tf1ijil£f i§u®1 (caution) ECU APU Exceedanc (caution) ECU detects uncommanded shutdown tf1ijiljjl ! (caution) APU Fire Detector APU GCU APU Fire Detector Fai (caution) APU Generator Overloa (caution) ECU APU Oil Pressure Low (caution) APU GCU tf1ijilij0fo§ijjl l (caution) APU GCU APU Power Faul (caution) ECU APU Shutoff Valve Fail (caution) APU starter remains engaged above 60% rpm APU Starter Engag (caution) APU door failed closed fjjijil1).!.], (advisory) APU GCU Miji@ijiltDI (advisory) APU GCU APU Generator Fail(advisory) APU GCU APU Generator Maint Reqd (advisory) ECU APU Maintenance Require (advisory) APU MASTER switch remains on five minutes after shutdown tf1iji1M£1t#•Jj! (advisory) Area Monitored CAS Message ECU detects fault that prevents starting APU Unavailabl {advisory) lnflight engine start requiresAPU air Assisted Airsta (advisory) Other Indications: (See Figure 5. APU Electronic Control Unit (ECU) Block Diagram and Figure 6. APU Control Panel (1 of 2).) Limitations: APU Indications: APU EXHAUST GAS TEMPERATURE (EGT): No limitations markings. APU RPM: 106% and above: Red Digits 104% to 105%: Amber Digits O to 103%: White Digits APU Operation: General: The APU can be operated on the ground, during takeoff, in flight and during landing. Inflight, it is an optional source of electrical power via the APU GEN instead of one or both engine-driven generators. The APU may be used for starter-assisted main engine starts below 30,000 ft if required. The APU operating envelope is 45,000 ft and below. Maximum Permissible EGT: Start: 1050°C Running: 732°C Maximum Rotor Speed: All conditions: 106%. APU Starting Limits: Continuous operation of the APU starter, when powered by airplane batteries, islimited to a maximum of three consecutive start attempts. A one-hour cool down period must be observed before the next full starter cycle is commenced. Note Successful consecutive starts are limited to six (6) at ten (10) minute intervals per start. - - C-a-ut-io-n - - USE OF AN EXTERNAL DC POWER SOURCE TO START THE APU IS PROHIBITED. c. APU Generator Electrical Load: The APU generator can deliver 100% (40 kVA) electrical power on the ground or in flight from sea level to 45,000 ft. APU Airstart Envelope: For APU airstart limitations, see Figure 7. APU Airstart Envelope: APU Airstart Envelope. The APU is guaranteed to start at or below 30,000 ft. Other Limitations: There is no provision to manually open the inlet door if the door actuator fails or if electrical power is not available. If the inlet door is in transit and electrical power is lost, the inlet door will no longer move. Figure 4. APU Controls and Indications Component Locations TIL-002631A Figure 5. APU Electronic Control Unit (ECU) Block Diagram ECUlntorr.co TIL-002630 Figure 6. APU Control Panel (1of 2) RPM Displays APU speed as a percentage, where 100% is designed operating speed. Display is active when APU MASTER switch is selected ON, until 5 minutes after APU MASTER switch is selected off. EGI Displays Exhaust Gas Temperature in degrees Centigrade. Displayis active when APU MASTER switch is selected ON, until 5 minutes after APU MASTER switch is selected off. APU CONTROL PANEL EG'T , APU 0 1 ® I I FIREEXT I I N'IJ CONTROL I START STOP I I I FIRE EXT DISCHD I FIRE See Section 2A-26-00: Fire Protection. READY (Blue) Indicates APU is ready to start. Illuminates when: APU MASTER switch is selected ON. ECU initialization and prestart BIT are complete. APU air inlet door is open. Extinguishes when: APU speed reaches 12% RPM during start. APU MASTER switch is selected off. TIL-002632 Figure 6. APU Control Panel (2 of 2) APU CONTROL PANEL START ON: Switch legend illuminates (Blue). APU startis initiated. Switch legend extinguishes at starter cutout. •If APU is in cool-down mode (prior to shut down), depressing START switch returns APU to on-speed condition (100% RPM). MASTER ON: Switch legend illuminates (Blue). ECU initializes and performs prestart BIT. Oil temperature is sensed and reported. APU air inlet door opens. APU fuel shu1off valve opens. OFF: Switch legend extinguishes. APU fuel shutoff valve closes. If APU is running,it immediately shuts down. STOP OFF: Switch legend illuminates (Blue). If APU is in a starting sequence, the start is aborted. If APU is running (on-speed), APU are shed and APU entens cool-down mode. After cool-down is complete, APU shuts down by performing an ovenspeed test. APU air inlet door closes. TIL-002633 APU Figure 7.APU Airstart Envelope 55000 50000 45000 40000 [35000 OPERATION LIMIT POSSIBLE Im - - - START ENVELOPE ' ::> !::: 30000 25000 \ \ ECS LIMIT \ GUARANTEED START ENVELOPE 20000 i ;15000 A. 10000 5000 0 -5000 I\ 'I\. \ \ ' '\ NOTE: APU AIR FOR '\ ENGINE START /' ABOVE 30,000 FT I I I -100 ·80 -60 -40 ·20 0 20 40 60 STATIC TEMPERATURE (°C) TIL-025519A