ACTM-793-797 PDF - Technological Advancements in Indian Railways
Document Details
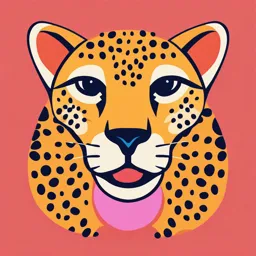
Uploaded by SolicitousOklahomaCity
Tags
Summary
This document details technological advancements in Indian Railways, discussing innovations in locomotive technology from foreign countries, including equipment conversions, control systems, and drive systems. It covers considerations regarding power ratings and indigenous developments for the Indian railway network.
Full Transcript
CHAPTER XI TECHNOLOGICAL ADVANCEMENTS 31101 Introduction Some of the recent technological innovations introduced by Foreign Railways are discussed below. Advantages offered by these innovations in respect of operating performance and maintainability hav...
CHAPTER XI TECHNOLOGICAL ADVANCEMENTS 31101 Introduction Some of the recent technological innovations introduced by Foreign Railways are discussed below. Advantages offered by these innovations in respect of operating performance and maintainability have also be indicated. With a view to use developed technology of 3- phase drives system on Indian Railways, import of 3- phase drive system locomotives with technology transfer for subsequent indigenous manufacturer is on hand. 31102 Conversion Equipment 1. With the availability of thyristor of higher power handling capability use of tap changer is being eleminated making the equipment entirely static. This will not only reduced attention required but also enhance reliability. Other very important benefit achieved by the thyristors is the capability they offer to control individually the supply to each motor permitting full utilization of the adhesion existing between the wheels and the rails. 2. Indian Railways have imported 12 locomotives from Japan and 6 from Sweeden with this technology (WAG6 series). Earlier a few experimental thyristors units were also fitted in existing locomotives, some of them with indigenous know – how. Indian Railways have also imported 25 sets of thyristor control traction equipment for fitment on 25kV ac MG EMUs from UK. These are being fitted on 25kV ac MG EMU coaches at ICF, Madras. Seven such thyristor controlled EMU rakes are presently in operation on MG Section of Southern Railway. 31103 Controls With the advent of solid state devices in general, and microprocessors in particular, more and more sophistication has become possible. Other things remaining the same, with stepless control and consequent non-pulsating torque offered by such controls, higher average tractive effort can be achieved. The solid state control is fast acting and methods are now available to detect incipient slip and take corrective action before the slippage becomes uncontrollable and curative action is called for by reducing the tractive effort applied. Thus the locomotives can be made to develop tractive efforts to very high levels of adhesion co-efficient. 31104 Drive 1. One of the severe restrictions imposed on the capability of electric locomotive is the dc series motors. These motors have limitations on their use because of windings on the rotor and assembly of commutators, making it vulnerable against centrifugal forces and requirements of satisfactory commutation. The 3-phase asynchronous motor with a bar rotor does not have the surface speed limitations. The useful portion of its speed torque characteristics is only near its synchronous speed.This useful portion can be spread over a wide range by varying the synchronous speed through frequency control. 2. With the advent of Gate Turn Off (GTO) thyristor problems associated with conversion of dc into multiphase ac system have been eliminated and use of 3-phase synchronous/ asynchronous motor has become feasible. “Variable Voltage and Variable Frequency” (VVVF) control has been developed and use of induction motors as traction drives has been tried successfully on the different railway systems. With induction machines a maximum surface speed of 100 m/s is achievable and an rpm level of 4500 has been accepted in the railways systems in Europe. This considerably increases the output power of the traction motor for the same size. This state of art technology has yet to arrive in our country. INDIAN RAILWAYS - AC TRACTION MANUAL - VOLUME III 3. Typical power circuit along with brief details of locomotive fitted with asynchronous motors is shown in Fig. 11. 0 1. 31105 Power Rating 1. Necessity for increasing the throughput resulted in the design of BOX "N" wagons. With these wagons, a trailing load of 4700 t has been optimized. Further improvements are under consideration which may result in a maximum trailing load of 5100 t on the existing loop lengths. Also efforts are on hand to increase the maximum speed of these stock to 100 km/h. For trailing loads of 4700t, a 6000 HP locomotive with 45 t starting effort was taken as an optimum. Once the trailing load is increased to 5100 t and the speed potential to 100 km/h, the horsepower requirements further go up to 8000 with a starting tractive effort of 50 t. Indian Railways will require a 8000 HP loco to meet the increasing throughputs of freight traffic. 31106 Other Developments on Hand 1. Indigenous development of multiplexing and locotrol for use on long passenger and heavy-hauled goods trains. 2. Indigenous development of on board power factor correction equipment for improving power factor of locomotive. 3. Indigenous development of fault diagnostics for locomotive INDIAN RAILWAYS - AC TRACTION MANUAL VOLUME, III ANNEXURE 11.01 ELECTRIC LOCOMOTIVES WITH 3-PHASE DRIVES 1. Introduction Till electronics came into the field of traction recently, the best suited drive for traction application was the dc series motor because of its inherent characteristics to give high torque at low speeds and vice-versa. The dc series motor was the best solution found for meeting the actual service as well as control requirements. On a fixed frequency, the asynchronous motor has a characteristic which is not well suited for traction application. However, this motor is of rugged construction when compared to a dc motor and requires much lower inputs for maintenance. Therefore its choice as a traction motor will always be preferred if control of the motor to suit the service requirements is possible. With the development of GTO thyristors, power electronics and micro processor control, controlling of any drive to suit specific requirements has become quite easy. In the circumstances, adoption of 3- phase induction motor for traction application has been tried for the past 10 years and has now become commercially viable proposition. The control is being achieved through variable voltage and variable frequency briefly referred to as VVVF. Originally thyristors were used with commutation requirements for cut off. With the advent of GTO, the control has been made much simpler and more efficient thus use of 3-phase asynchronous motors for traction could also become financially viable. A locomotive With 3-phase asynchronous motor drive has the following advantages - higher power capability due to high power/weight ratio, - regeneration capability over a wide speed range, - lesser maintenance, - unity power factor at pantograph, - higher adhesion. 2. Principle of control of 3-phase drives. The speed/torque characteristic of an induction motor supplied from a 3-phase voltage source of fixed frequency ‘f ’ is of the form shown in Fig. 11. 02. It may be seen that at low speed, the torque is small and the stator current is high. The zone normally usable lies at the extreme from the point of maximum torque, in the vicinity of synchronous speed. For traction applications a high TE is necessary for starting and accelerating the train. Therefore, when constant torque is required, it is necessary to obtain whole series of characteristics curves such as shown in Fig. 11.03. This calls for change in synchronous speeds and therefore variable frequency. 3. Control scheme for induction motors : The control of the ac induction motor drive in traction application is achieved in 3 stages. 1) Constant torque mode : The torque developed by a motor is proportional to the product of the magnetic flux in the air gap and the rotor current. The applied voltage is proportional to the synchronous frequency and the magnetic flux in the air gap. To keep the magnetic flux constant, therefore, the applied voltage to the traction motor is, to be made proportional to the synchronous speed. The rotor current depends upon the slip frequency of the rotor. By keeping this constant, the rotor current is also kept constant. This is possible till the voltage is increased to the rated terminal voltage of the traction motor. Thus in this mode the control is achieved by increasing the voltage and frequency uniformly with respect to the actual speed of the rotation of the rotor and the required slip frequency. INDIAN RAILWAYS - AC TRACTION MANUAL VOLUME III ii) Constant power mode : In this mode the voltage is already reached to the rated voltage. By increasing the frequency, the magnetic flux in the air gap is reduced proportionately. By keeping the slip frequency constant, the motor current is kept constant. Thus the motor is made to give constant power output till the maximum service speed is reached. iii) Balancing speed stage: Once the maximum pre-determined speed is achieved, the same power output from the traction motor may not be required and the output is to be matched to meet the resistance of the train for running at the balancing speed. This is achieved by suitably reducing the terminal voltage of the traction motor. These functions are performed through micro processor control giving various inputs of parameters like voltage, current and speed. iv) Convertor/Invertor System : In order to achieve the above control requirements, the convertor/ invertor system with a dc link is adopted. The convertor rectifies the ac voltage to dc and feeds it to the dc link. The dc link supplies power to the invertor. The convertor output power is controlled by controlling the output current keeping the dc link voltage constant. The invertor output power is controlled by varying the terminal voltage initially till the full voltage is achieved. However the motor output current is kept constant. The control of output current of the convertor and output voltage of the invertor is achieved by pulse width modulation control. The Power circuit diagram of a typical 3-phase locomotive fitted with asynchronous motors is shown in Fig. 11. 01. INDIAN RAILWAYS - AC TRACTION MANUAL - VOLUME III