Accounting Exam Review PDF
Document Details
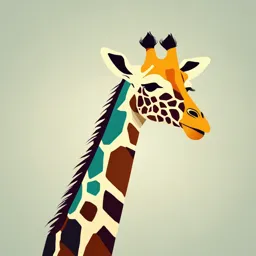
Uploaded by SpellbindingFermium2472
UTSA
Tags
Summary
This document reviews key concepts for an accounting exam, covering topics like costs, overhead application, and manufacturing processes. It includes example formulas and definitions relevant to accounting principles. Keywords: accounting, costs, overhead, manufacturing.
Full Transcript
**[Accounting 2 Exam 1 Review (Ch. 1, 2, & 4)]** **[CHAPTER 1]** A screenshot of a computer AI-generated content may be incorrect. [Margin] = Net Income / Revenue [Prime Costs] = Direct Materials + Direct Labor [(Total) Manufacturing Costs]\_= Direct Materials + Direct Labor + Manufacturing Ove...
**[Accounting 2 Exam 1 Review (Ch. 1, 2, & 4)]** **[CHAPTER 1]** A screenshot of a computer AI-generated content may be incorrect. [Margin] = Net Income / Revenue [Prime Costs] = Direct Materials + Direct Labor [(Total) Manufacturing Costs]\_= Direct Materials + Direct Labor + Manufacturing Overhead [Conversion Costs] = Direct Labor + Manufacturing Overhead - The cost of converting raw materials into a finished product. [Direct Materials:] All the materials used directly in the production of a product. We only account for the important and relevant materials in this category. Minor parts that are too hard to keep track of like screws count as [manufacturing overhead.] [Direct Labor:] All the labor that was directly put into the production of a product. The wages of factory workers, for example, count in this category. Salaries of the president and supervisors of the factory line and similar do not count into this category and go into [Nonmanufacturing costs (NA in the picture above) or manufacturing overhead] respectively. [Manufacturing Overhead:] All the costs other than direct materials and direct labor that are indirectly involved in the production of a product. - Example: Warehouses, factories, indirect labor, indirect materials, supervisors' salaries, property tax, indirect materials or materials that are too hard to account for, utilities, depreciation on machinery used in the production line, etc. [Non-manufacturing Costs/NA costs:] All the costs associated with the company but not the production of a product. - Example: Advertising, depreciation for salesperson vehicles, presidents' salary, commissions. [Variable Costs]: Costs that change in proportion to changes in activity level (Basically costs that fluctuate and are not constant throughout periods). - Example: Materials, utilities, wages, commissions, etc. [Fixed Costs]: Costs that remain constant and do not change regardless of activity level. - Example: Rent, depreciation, insurance, advertising, salary. [Period Costs:] Costs that are not directly involved in the production of a product. They are expenses immediately. - Example: Selling expenses, administrative expenses, interest expense, depreciation of sales vehicle, sales commission, etc. [Product Costs:] Costs that are directly related to the production of a product. - Example: Direct materials, direct labor, manufacturing overhead. **[CHAPTER 2]** [Overhead Applied ] - Step 1: Get the overhead rate. - [Overhead Rate] = Estimated overhead cost / Estimated labor hours - Step 2: Get the overhead applied - [Overhead Applied] = Direct labor hours \* Overhead Rate [Direct Materials (If not given)] = Total Manufacturing costs -- Direct Labor -- Manufacturing Overhead Applied [Cost of Goods Manufactured] = Manufacturing Costs + Beginning Work in Process Inventory -- Ending Work in Process Inventory. - [Beginning Work in Process Inventory] = Cost of Goods Manufactured -- Manufacturing Costs + Ending Work in Process Inventory - [Ending Work in Process Inventory] = Manufacturing Costs + Beginning Work in Process Inventory -- Cost of Goods Manufactured [Cost of Goods Sold] = Cost of Goods Manufactured + Beginning Finished Goods Inventory -- Ending Finished Goods Inventory. - [Beginning Finished Goods Inventory] = Cost of Goods Sold -- Cost of Goods Manufactured + Ending Finished Goods Inventory - [Ending Finished Goods Inventory] = Cost of Goods Manufactured + Beginning Finished Goods Inventory -- Cost of Goods Sold [Direct Labor] = Conversion Costs (Ans 1)/ Percentage given in the problem (EX: 150% = 1.5) - [Conversion Costs (Method 2, chapter 2 questions for direct labor)] = - Manufacturing Costs -- Direct Materials = Ans 1 [ESTIMATED Direct Labor Hours] = Direct Labor (usually a monetary value in these type of problems) / Estimated Rate (usually given by the problem). [Predetermined Overhead Rate] = Estimated Manufacturing Overhead / Estimated Direct Labor Hours [Applied Manufacturing Overhead] = Predetermined Overhead Rate \* Actual hours (Picture is to illustrate a little more on the formulas above, lacking a little context).  [Labor Costs] = Direct Labor + Indirect Labor [Salaries and Wages Payable] = Work in Process Inventory + Manufacturing Overhead + Selling, General, Administrative expenses + Salaries. [Indirect Labor:] Labor that was not directly involved in the production of a product. - Example: Supervisors' salaries If [Manufacturing Overhead has a Credit Balance], it is [Overapplied] Manufacturing\ Overhead, so you have to [Decrease (Credit) Cost of Goods Sold].\ If [Manufacturing Overhead has a debit balance], it is [Underapplied] Manufacturing\ Overhead, so you have to [Increase (Debit) Cost of Goods Sold]. [Direct] [Materials] and [Direct] [Labor] are [charged] to [WIP] [Inventory].\ However, [overhead] (indirect materials, indirect labor, utilities) is [not] [charged] to\ [WIP] [Inventory]. [Instead], [overhead] is [charged] to [Manufacturing] [Overhead].\ It is [not cost effective] to track [indirect materials] to [specific jobs and charge them to\ WIP]. Therefore, [we charge them to Manufacturing Overhead]. Then, [applied\ Manufacturing Overhead] (MOH rate \* the actual direct labor hours) is charged to\ WIP. [Raw Material Inventory:] Raw materials that have not been used in production yet. [Work in Process Inventory:] Raw materials that are currently being converted/used in the production process. Incomplete jobs. [Finished Goods Inventory:] Finished products that have not been sold yet. [Raw Material Inventory à Work in Process Inventory à Finished Goods Inventory. ] [Process Costing:] Type of costing used by companies that make standardized/homogenous products (same type of product across various companies) - Example: Thermos, toothbrushes, etc. [Job Order Costing:] Type of costing used by companies that offered customized or unique products or services. - Example: Consulting or legal services. EXAMPLE OF JORUNAL ENTRIES FOR RAW MATERIALS, WORK IN PROCESS INVENTORY AND FINISHED GOODS INVENTORY (From the notes): Bought Raw Materials for \$100 on account. Journal Entries:\ Debit: Raw Inventory 100\ Credit: A/P 100\ I transferred the Raw Materials to the factory floor:\ Debit: Work In Process (WIP) Inventory 100\ Credit: Raw Materials Inventory 100\ We completed our product:\ Debit: Finished Goods Inventory 100\ Credit: WIP Inventory 100 **[EXAMPLE 2]** Assume the house-flipping company has two projects in process ([Jobs 27 and 28]).\ The following information is available at the beginning of this period:\ ▪ The purchase price of the properties for the two projects [were \$250,000 and\ \$200,000 respectively, included in beginning Work in Process Inventory.]\ ▪ The company [started] the period with [\$10,000] of [Raw Materials Inventory].\ ▪ The company has [two completed] but [unsold projects] in [Finished Goods] [Inventory at a total cost of \$600,000.] Record the purchase and issue of materials: The company purchased \$25,000\ of materials for cash. Other minor materials of \$500 were issued and used on both\ jobs. [Purchase:]\ Debit: Raw Materials Inventory 25,000\ Credit: Cash/AP 25,000 [Raw Materials of 25,000 were issued to be used for each individual job:]\ Debit: WIP Inventory 25,000\ Credit: Raw Materials Inventory 25,000 [Other minor materials of \$500 were issued and used on both jobs]:\ Debit: Manufacturing Overhead 500\ Credit: Raw Materials Inventory 500 **[CHAPTER 4]** [Activity Rate] = Total Activity Cost / Total Cost Driver [Target Cost] = Market Price \* Target Profit = (Answer) -- Market Price [Cost Driver (Example on how to get it)] = Engineering hours + Product Assigned + Machine hours [Unit Cost] = Overhead Assigned / \# of units = (Answer) + Direct Materials + Direct Labor Traditional: Cost driver / total overhead cost of production = estimated unit cost Estimated Unit Cost \* hours = total production costs [Gross Profit Per Unit =] Add -- Average selling price Less -- Manufacturing Cost per unit Traditional is a faster more efficient way to find a units production cost but is not as accurate. [ABC]: Individual Total Cost / Total Hours using machine= exact unit production cost Exact unit production cost \* hours = exact machine production costs for standard or deluxe ABC is more time consuming than traditional, but you will receive a more accurate answer