A Textbook of Production Technology PDF
Document Details
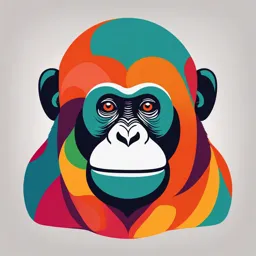
Uploaded by ImaginativePeachTree
STC/JHS
Tags
Summary
This textbook provides a comprehensive overview of production technology, focusing on various machining processes such as broaching and sawing. The text details different types of broaching machines, their operation, and materials used. It also describes surface broaching machines and continuous chain type surface broaching machines, including their advantages and limitations.
Full Transcript
554 A Textbook of Production Technology The “rear pilot” supports the broach after the last tooth leaves the hole. Follow-Rest Grip Root...
554 A Textbook of Production Technology The “rear pilot” supports the broach after the last tooth leaves the hole. Follow-Rest Grip Root Rear Pilot diameter Finish Pull Front Roughing ing end Teeth Pilot teeth Semifinishing teeth Shank length Cutting length Overall length Fig. 8.93. A typical Internal Broach. (a) Tooth Elements. The tooth shape of a typical broach is shown in Fig. 8.94. The front rake angle (face angle or hook angle) refers to rake angle of a single point cutting tool and the back -off angle (relief angle) is provided to prevent rubbing of tool with workpiece. Hook angle: 15° to 20° for steel 6° to 8° for C.I. Back-off angle: 1° to 3° Front rake Land Straight (or Hook angle) land (b) Material. High speed steel Relief Pitch (H.S.S.) is by far the most widely used Angle material for the broaches. Brazed carbides or disposable inserts are sometimes used for the cutting edges Depth when machining cast iron parts which Radius require close tolerances and production rates. Carbide tools are also used to an Fig. 8.94. Tooth Shape of a Broach. advantage on steel casting to offset the damaging effect of local hard spots. (c) Construction. A broach may be either solid or assembled or built up from shells, replaceable sections or inserted teeth. Replaceable sections, teeth or shells make a broach easier to repair. 8.8.2. Types of Broaching Machines. A broaching machine consists of a work-holding device (fixture), a broaching tool, a drive mechanism and a suitable frame. The broach is usually secured in the main slide of the broaching machine and travels with the slide. A broaching machine may be a horizontal or a vertical one depending upon whether the slide travels in the horizontal plane or in the vertical plane. A horizontal machine has the following characteristics : (i) Any part of it, especially, the work station can be reached readily from the floor. (ii) A long slide can be supported at many points and levelled to keep it straight. A vertical machine has the following characteristics : (a) It occupies less floor area. (b) For a machine with a long stroke, a pit should be sunk or there should be a platform for the operator to reach the workstation. 1. Internal Broaching Machines. We have pull broaching machines and push broaching machines and these machines may be horizontal or vertical. In pull broaching machines, the force is applied to the shank and the body of the broach is in tension, (Fig. 8.95 (a,b)). If the force is Machine Tools 555 applied to the rear end of the broach, it is a “push broach” and is in compression, (Fig. 8.95 (c)). To avoid buckling, a push broach should be shorter than a pull broach and its length usually does not increase 15 diameters. A vertical push broaching machine is mostly used for internal broaching such as hole sizing, and key way cutting. In horizontal pull broaching machine, Fig. 8.95 (a), the work is held tightly against the platen in the broaching operation by the cutting force. Vertical pull broaching machines may be : vertical pull-down machines or vertical pull up broaching machines. (a) Vertical Pull Down Broaching Machines. In these machines, the broach, instead of being pushed, is pulled through the job (Fig. 8.95 b). The pulling mechanism is in the base of the machine. The broach is suspended above the work-table by an upper carriage. To start the broaching process, the broach is lowered through the workpiece held in a fixture on the worktable. The broach is automatically engaged by the pulling mechanism and is pulled down through the job. After the operation is completed, the broach returns to its starting position. Work Work Pull Horizontal (a) Horizontal Pull Broaching Vertical Push Pull (b) Vertical Pull Down Broaching Work (c) Push Broaching Fig. 8.95. Internal Broaching. (b) Vertical Pull Up Broaching Machine. Here, the pulling mechanism is above the worktable and the broach is in the base of the machine. The broach enters the job held against the underside of the table and is pulled upward. At the end of the operation, the work is free and falls down into a container. 2. Surface Broaching Machines. External surface broaches are classified in respect to the surface they machine into : flat (slab), peripheral and contour broaches. The common surface broaching machines are discussed below : 556 A Textbook of Production Technology (a) Vertical Broaching Machine. A vertical broaching machine, (Fig. 8.96) has a box shape column 5 which houses electric drive 6 with the units of 3 4 hydraulic drive. Broaching tools 4 are mounted on slide 3 which is hydraulically driven and accurately guided 2 on the column ways. Slide with the broaches travels at 5 1 various speeds controlled by the hydraulic drive. Its stroke is adjusted to suit the broaching operation to be 6 per-formed. The slide has a rapid return stroke. The worktable 1 is mounted on the base in front of the column. It can be retracted to unload and load the broaching fixture and advanced to a preset Fig. 8.96. Vertical Surface Broaching broaching position. Workpiece 2 is held in a broaching Machine. fixture mounted on the table. After advancing the table to the broaching position, it is clamped and the slide with the broach travels downwards, machining the workpiece. The table then recedes to load a new workpiece and the slide returns to its upper position. The cycle is then repeated in the same order. Such a machine is called as “Single slide machine”. In vertical “double slide” surface broaching machine, there are two slides which operate opposite each other. The work is held on shuttle worktables which move out during the unloading and loading operations while the slide returns to its starting position. While this is going on, the other slide is at work. (b) Horizontal Surface Broaching Machine. Here, the broach is pulled over the top surface of the workpiece held in the fixture on the worktable. The cutting speed range from 3 to 12 mpm with a return speed upto 30 mpm. (c) Continuous Surface Broaching 4 5 6 7 Machine. A continuous chain type surface 3 broaching machine is shown in Fig. 8.97. A A 2 continuous chain 4 travels in a horizontal plane over sprockets mounted in box-shaped B 1 base 2. Fixtures 1 for locating and holding workpieces 3 are mounted at intervals on the 8 chain. Broach 5 is fixed horizontally above the chain, under bracket 7 mounted on the base. A Rigid guiding member 6 is arranged Fig. 8.97. Continuous Surface Broaching Machine. under the chain in the zone where the workpieces pass under the broach and provides for horizontal motion of the chain so that a definite amount of stock is removed from the workpieces. The workpieces are loaded into the fixtures at station A where they are clamped either manually or automatically. The workpieces, located and clamped on the travailing chain, passes between the broach and the guiding plate and then are automatically unclamped and ejected at station B where they drop into hopper 8 of the machine. Continuous surface broaching machine increases the productivity. 8.8.3. Broaching Drives. The drives used to reciprocate the broaching tools are : Hydraulic and Electro-mechanical. Hydraulic drives cost less, give smoother action and are more popular. An electro- mechanical drive employs a screw engaged with a recirculating ball nut. This type of drive is preferred for longer strokes and high speed machines. Most H.S.S. broaches cut at less than 0.15 m/s and the carbide broaches around 0.50 to 1.50 m/s. Machine Tools 557 8.8.4. Size of Broaching Machines. The size of a broaching machine is given by two numbers : a × b where a = Force the machine can apply in tonnes b = stroke of the slide, mm. 8.8.5. Advantages of Broaching 1. Rapid operation since the whole machining allowance is removed in a single stroke of the broach. 2. Very high production capacity. 3. High degree of surface quality. 4. The process can be used both for internal as well as external machining. Limitations 1. Cost of tool is very high. 2. A separate broach has to be made for each shape and size, therefore, broaching is primarily a method for mass production. 3. The workpiece must be rigidly held and the broach firmly guided. 4. Large amounts of metals can not be removed. PROBLEMS 1. Define a broaching operation. 2. Sketch and discuss a typical Internal Broach. 3. Sketch a typical tooth shape of a Broach. 4. Write briefly about the materials of broaching tools. 5. Write briefly about the construction of broaching tools. 6. With the help of neat sketches, explain the horizontal pull broaching operation and the vertical push broaching operation. 7. With the help of a neat sketch, discuss the working of a surface broaching machine. 8. With the help of a neat sketch, discuss the working of a continuous surface broaching machine. 9. Write the advantages and limitations of broaching process. 8.9. SAWING MACHINES The various construction materials (stock) available in shop stores are of standard forms and sizes. The stock is cut to correct length to make a product. The operation of cutting stock to correct length is called “sawing”. The process can be accomplished either by hand (hand hacksaw) or by power operated machines. Sawing by hand is very slow and laborious. These troubles are overcome by using power operated sawing machines. All the sawing machines use saw blades to cut the stock. Although different in overall form, they all contain a series of cutting teeth that operate in the same basic way. When the teeth are laid out into a straight line, one obtains a hacksaw, or, if the sawblade is flexible and made into an endless loop, a band saw. All these tools are form tools and the cut progresses by positive infeed or by the pressure exerted on the tool. 8.9.1. Saw Blade. The important features of a saw blade are : Material, Tooth form, Tooth set, Tooth spacing and Size. 1. Material. Blades are made of carbon steel, Tungsten alloy steel, High Speed tungsten steel, Molybdenum steel, High speed molybdenum steel and Cemented carbide. Most saws are 558 A Textbook of Production Technology solid, some have teeth of a hard material backed by flexible steel, and many have tipped or inserted teeth. 2. Tooth Form. Two commonly used tooth forms for saw blades are shown in Fig. 8.98. The straight tooth form, (Fig. 8.98 (a)) is suitable for finer pitches whereas the tooth form shown in (Fig. 8.98 (b)) is used with coarser pitches. This tooth form is theoretically better because the cutting edges are backed up by more metal. However, it is more difficult to obtain this tooth form on smaller teeth. 3. Tooth Set. Tooth set refers to how the teeth are bent or offset to one side or the other, and the amount of the offset. The set makes the cut or “kerf” (width of cut) wider than the blade thickness so that the blade will not stick or bind. This makes cutting much easier. We have three types of tooth sets, Fig. 8.99, which are used as per tooth spacing or pitch. 56° Saw width 10° +ve Rake angle (a) Clearance 15° angle Saw width (b) Fig. 8.98. Tooth Forms. (a) Straight Set. When the teeth are offset alternately to the right and left, (Fig. 8.99 (a)), it is called straight set or alternate set. This set is most suitable for non-ferrous metals and non-metals, and hacksaw blades with p = 1.6 mm (b) Wavy Set. When several teeth are offset (mainly, every two consecutive teeth) in one direction, and then several are offset in the opposite direction, it is called a wavy set, (Fig. 8.99 (c)). This set is employed with small teeth for sawing thin sheets and sections. (c) Raker Set. One tooth is offset to the left, the next tooth is offset to the right and the third tooth is unbent. This form is repeated and we get a raker set, Fig. 8.99(b). This set is used for cutting ferrous metals unless the metal thickness is too thin. 4. Tooth Spacing. Tooth spacing or pitch has an important influence upon saw performance. Selection of pitch for a sawing job will depend upon the length of saw in contact with the job and the work material. Longer saw cuts require coarser pitched teeth because these cuts will produce longer chips needing more space for chips between the teeth. Softer materials will also produce longer chips and so will need coarser pitched saws. Finer pitched teeth are used for sawing harder materials. For cutting thin workpiece or thin sections, at least 2 or 3 teeth should always be in contact with the workpiece to avoid snagging of the teeth. Machine Tools 559 Width of the saw cut (a) Straight set Width of the saw cut (b) Raker set Width of the saw cut (c) Wavy set Fig. 8.99. Tooth Sets. The commonly used hand hacksaw blades are furnished with 14, 18, 24 and 32 teeth per inch. Power hacksaw blades are coarser (from 4 to 14 teeth per inch). Band saws are also with coarser pitches and may have as few as 2 teeth per inch. The pitch may run from 0.20 inch on small circular saws to 2 inches on large diameter saws for soft materials. 5. Size. The size of hand hacksaw blades is : thickness = 0.64 mm, width = 12.7 mm Length = 254 and 304.8 mm. The size of power hacksaw blades is thickness = 1.27 to 2.54 mm, width = 25.4 to 50.8 mm Length = 304.8 to 609.6 mm. The heavier the cut, the longer should be the blade. Most band saws are welded in continuous 1 loops and commonly are from 0.020 to 0.060 inch thick and to 1 inch (a few upto 2 inch) wide. 16 The narrower blades are required to cut around small radii. Circular cold saws are tooth disks from 1/32 to 1/12 inch thick and 8 to 80 inch in diameter. 6. Cutting Speed. Cutting speed for tungsten H.S.S. blades : Mild steel = 0.75 m/s Cast iron = 0.50 m/s Brass and = 1.5 m/s Aluminium Bronze = 1.25 m/s Thin sections, = 1.5 m/s. pipes and tubes 8.9.2. Types of Sawing Machines. The common sawing machines are discussed below : 1. Power Hacksaw (Reciprocating Sawing Machine). The power hack saw is a power driven tool for cutting off stock, (Fig. 8.100). The machine consists of a base with a worktable and vise on it. The vise is adjustable for cutting at right angles and at several other angles. A saw frame holds the blade. In operation, the stock is held in a vise. The sawing takes place only on the forward, or draw, stroke. The frame lifts up slightly on the return stroke. There are switches to turn on the 560 A Textbook of Production Technology power and a clutch handle to start the sawing operation. A sufficient supply of cutting fluid should be flooded over all metals except Cast iron, at the cut. At the completion of a cut, an automatic switch may stop the sawing motion of the machine. The size of the saw is determined by the largest diameter (or square) that can be cut. A common size is 3 inch by 3 inch. Saw frame Speed change Vise lever Table Cut off Gauge Base Motor Fig. 8.100. Power Hacksaw. 2. Circular Sawing (Cold Sawing Machine). A saw for cold sawing of a metal is a profile sharpened cutter for milling a narrow slit. Saws of small diameter may be made in the form of a solid disk with teeth located on the periphery. At present, circular saws upto 250 mm in diameter are usually made solid with integral teeth. Circular saws over 250 mm in diameter are of either segmental or inserted-blade construction. The working of a circular sawing machine is illustrated in Fig. 8.101. Saw Clamp Work-piece Feed Fig. 8.101. Circular Sawing Machine. Machine Tools 561 3. Band Saws. Band saws with an endless saw blade are being used to a greater and greater extent for cut off and straight sawing operations for metals since they enable the width of the kerf to be substantially reduced. They are used in special power bandsawing machines. A continuous saw blade runs over the rims of two wheels on the machine. (a) Horizontal Band Saw. The horizontal band saw is a small metal cutting band saw that can be used with the blade in a horizontal position, (Fig. 8.102). The saw consists of a base with a worktable and vise. The saw frame is hinged at one end. On the frame are two wheels over which the continuous blade operates. Most of the blade is covered. Machine size is determined by the wheel diameter. The saw carried on a frame is fed downward through the workpiece held in the vise. Except for the continuous cutting action of the endless band saw blade, horizontal band saws incorporate most of the features of the power hacksaw. Saw frame Roller Guide Brackets Blade Tension Step pulleys for speed change Vise Hand Wheel Switch (Guarded) Leg Base Fig. 8.102. Horizontal band Saw. (b) Vertical Band Saw. In this machine, (Fig. 8.103), the endless band saw blade runs over two wheels in a vertical position. Saw guides help support the sides of the saw band near the sawing. Cutting speeds may range from 0.25 m/s to 7.5 m/s depending upon the metal to be cut. The blade tooth form, (Fig. 8.98 (a)), is commonly used for band saws. However, for sawing softer metals such as aluminium and lead alloys, the tooth form shown in Fig. 8.104 (buttress or skip- tooth form) is employed. This provides more space for chips and, therefore, the saw will not become overloaded. In the Fig. 8.103, the power is given to the power wheel from a variable speed motor. 562 A Textbook of Production Technology Upper wheel (idler) Saw band Upper saw guide Throat depth Work-piece Table Lower saw guide Lower wheel Floor Fig. 8.103. Vertical Band Saw Machine. 56° Saw width Direction of movement for cutting Fig. 8.104. Skin-Tooth Form. 8.9.3. Field of Application of Sawing Machines. Hacksaw machines are relatively slow and find usage in low-output production and toolroom and maintenance work. Cold Saw. Where production is in the medium or high ranges, cutoff and similar sawing operations are normally done on the cold saw. Manually operated cold saws are used for low production work and automatic-cycle and special units are used in the higher production ranges. Much larger sizes and cuts are possible than with hack saws. Standard machines commonly available employ blades with diameters ranging from 1016 to 1143 mm. Some machines use blades as much as 3.05 m in diameter. A typical machine with a 1143 mm blade will cut a full 406.4 mm square or a rectangle 330 × 644 mm. Band Saw. Capable of cuts other than straight, the band saw is useful for production operations other than cut off. With conventional plain contour band sawing, it is practicable to produce blank Machine Tools 563 parts in quantities upto about 500 pieces, eliminated the usual die costs for such parts. Sheet material is compressed and welded together to simplify the sawing, and intricate or three-dimensional shapes are practical. PROBLEMS 1. Define “sawing operation”. 2. Discuss the materials for saw blades. 3. Sketch and discuss the various tooth-forms used for saw blades. 4. What is “tooth-set” ? Sketch and discuss the various tooth-sets used for saw blades. 5. How the pitch for a saw blade is selected ? 6. Sketch and explain the working of a Power Hacksaw. 7. Sketch and explain the working of a Circular Sawing Machine. 8. Sketch and explain the working of a Horizontal Band Saw. 9. Sketch and explain the working of a Vertical Band Saw. 10. Discuss the field of applications of the Various Sawing Machines. 11. Explain why broaching is a commonly used process ? Give some typical applications. 12. Explain why hacksaws are not as productive as horizontal band saws ? 13. What is the function of burnishing teeth on broaches ? 14. Write briefly on Broaching drives. 15. How is the size of a broaching machine specified ? 16. Write briefly on Abrasive sticks. 17. What are grinding points ? Sketch the various grinding points. 18. Write briefly on Grinding segments. 19. What is skip-tooth form ? For which materials it is preferred ? 20. Explain why hacksaws are not as productive as band saws ? 21. Why do some saw blades have staggered teeth ? 22. Why are some saw blades equipped with H.S.S. or carbide teeth ? 23. Why is it very difficult to saw thin sections ? 24. What is friction sawing ? 25. How is the size of an abrasive grain related to its number ? 26. Differentiate between coated and bonded abrasives ? 27. Is the grinding ratio important in determining the economics of a grinding operations ? Explain. 28. Differentiate between finishing by form grinding and by generating. 29. Why are speeds so much higher in grinding than in cutting ? 30. What are the advantages and disadvantages of puss and push broaches ? 31. Under what conditions broaching would be the preferred method of machining ? 32. Explain why the cutting tool many easily chip or break during climb milling ? 33. Differentiate between form milling and straddle milling. 34. How are T-solts machined ? 35. What is the difference between a feed rod and the lead screw in the case of a lathe ? 36. How is the boring mill different from a lathe. 37. Explain the functions of Saddle on a lathe. 564 A Textbook of Production Technology 38. What are the ways in a lathe ? 39. Differentiate between a blind hole and a through hole. 40. What are the advantages of having a hollow spindle in the headstock of a lathe ? 41. Give the Main Specifications of Grinding Machines. Grinding Machine Main Specifications External Cylindrical Grinder Swing , Centre Distance Internal Cylindrical Grinder Max. Grinding Bore Centreless Grinder, External Job Centreless Grinder, Internal Bore Surface Grinder, Reciprocating Table Table Size (Length × Width) Surface Grinder Rotary Table Table 42. Give the Main Specifications of Sawing Machines. Machine Main Specifications Power Hacksaw Machines Job Circular Sawing Machine Blade Band Saw (Hor., Vert) Job (Throat Depth) Friction Sawing Machines Job Size Abrasive wheel cut-off Machines Wheel Pipe and Tube Cutting Machines Job Jig sawing and Filing Machines Table (Reciprocating) 43. What is Trepanning ? It is an operation used for drilling deep holes of 50 mm in and above, without twist drill, Fig. 8.51 (c). The tool comprises an annular body with single point cutters arranged uniformly on its periphery, which can number 6 to 12 for tools with 30 to 150 mm . Also, See Art 8.3.8. 44. What are Flat Drills ? Flat drills or spade drills (the point of these drills being in the shape of a spade, Fig. 8.105), are used to drill holes upto 25 mm in non-critical applications, mainly hard forgings and castings. The point angle is 118° to 120° and the clearance angle is 10° to 20°. These drills come in two designs : Two ways, Fig. 105(a) and one way, Fig. 105(b). The cutting angle for one way drill is 75° to 90° for steel and 45° to 60° for non-ferrous materials. For two way drill, this angle is 120° to 135°. These drills (made of alloy steel and H.S.S.) do not stand high cutting speed (drilling is affected by Ratchet drills and plain hand drills) and can not be used to drill deep holes as chips do not come out of the hole, but keep rotating with the tool and spoil the hole surface. Also, they wear out rapidly and loose cutting ability and tend to wander. Shank (a) Two-way Point Shank (b) A one-way Fig. 8.105. Flat drills Chapter 9 Unconventional Manufacturing Methods 9.1. GENERAL Unconventional manufacturing methods fall under two categories : Unconventional machining methods and Unconventional forming methods. (a) Unconventional Machining Methods. The unconventional machining methods are also called ‘‘Non-traditional Machining Methods, (NTMM)’’, also known as ‘‘New Technology’’. The basic principle of metal removal in the conventional methods of machining involves the use of some sort of tool which is harder than the workpiece and is subject to wear. The metal removal is by mechanical energy through the use of physical force (the tool and the workpiece being in direct contact with each other), which shears the chips. That is, the conventional machining methods involve removal of metal by compression shear chip formation. The conventional machining methods have the following inherent drawbacks : (i) Metal removal by chip formation is an expensive and difficult process. (ii) Chips produced during the process are an unwanted by-product. (iii) Removal of these chips and their disposal and recycling is a very cumbersome procedure, involving energy and money. (iv) Proper holding of the workpiece and to avoid its distortion are very important, due to the very large cutting forces involved. (v) Due to the large cutting forces and large amount of heat gene- rated at the tool-workpiece interface, undesirable deformation and residual stresses are set up in the workpiece. These undesirable effects have to be removed afterwards. (vi) Delicate components, for example, semi-conductor ‘chip’ can not be produced by conventional machining methods. On the other hand, the NTMM are generally non-mechanical, don't produce chips or a lay pattern on the work surface and often involve new energy modes. There is no direct physical contact between the tool and the workpiece and so, the tool need not be harder than the job. The impetus for developing most of these new methods was the search for better ways of machining complex shapes (dies, moulds etc.) in hard, high strength temperature resistant alloys, such as nimonics, carbides, titanium alloys, hastalloy, nitralloy, waspalloy, stainless steels and heat resisting steels etc. The use of these difficult to machine materials has lead to rapid developments in the aerospace and nuclear engineering industries. Many of these materials also find applications in other industries, owing to their high strength-to-weight ratio, hardness and heat-resisting qualities. 565 566 A Textbook of Production Technology The conventional machining processes, inspite of recent technical advancements, are inadequate to machine these materials economically. Besides, machining of these materials into complex shapes is difficult, time consuming and sometimes impossible. The NTMM have been developed to overcome all these difficulties. They also meet better dimensional and accuracy requirements. Classification of NTMM. The Non-traditional Machining Methods are classified according to the major energy sources employed in machining. 1. Thermal Energy Methods. In these methods, the thermal energy is employed to melt and vaporize tiny particles of work-material by concentrating the heat energy on a small area of the workpiece. The required shape is obtained by the continued repetition of this process. These methods include : Electrical discharge machining (EDM), Laser beam Machining (LBM), Plasma Arc Machining (PAM), Electron Beam Machining (EBM), and Ion Beam Machining (IBM). 2. Electro - Chemical Energy Methods. These methods involve electrolytic (anodic) dissolution of the workpiece material in contact with a chemical solution. These methods include: Electro-Chemical Machining (ECM), Electrochemical grinding (ECG), Electro-Chemical Honing (ECH) and Electro-chemical Deburring (ECD). 3. Chemical Energy Methods. These methods involve controlled etching of the workpiece material in contact with a chemical solution, for example, Chemical Machining Method (CHM). 4. Mechanical Energy Methods. In these methods, the material is principally removed by mechanical erosion of the workpiece material. These methods include : Ultra Sonic Machining (USM), Abrasive Jet Machining (AJM), and Water Jet Machining (WJM). Process Selection. The following aspects must be considered for the correct selection of the non-traditional machining method : 1. Physical parameters of the process. 2. Shapes to be machined. 3. Process capability. 4. Economics 1. Physical Parameters of Unconventional Methods. The physical parameters of dif- ferent unconventional machining methods are given in Table 9.1. Table 9.1. Physical Parameters of NTMM Parameters NTMM USM AJM CHM ECM EDM EBM LBM PAM Potential, V 220 220 - 10 - 30 100 - 300 150 × 103 4.5 × 103 100 Current, A 12 1.0 - 10,000 50 0.001 2 500 Power, kW 2.4 0.22 - 100 2.70 0.15 - 50 Gap, mm 0.25 0.75 - 0.20 0.025 100 150 7.5 Medium Abrasive Abrasive Liquid Electrolyte Di- Vacuum Air Argon in water, in Gas Chemicals electric or Paraffin fluid Hydrogen 2. Shapes Cutting Capability. The various NTMM have some special shape cutting capability as given below : (a) Micro-machining and Drilling : LBM and EBM (b) Cavity sinking and standard Hole Drilling : EDM and USM (c) Fine hole drilling and Contour Machining : ECM (d) Clean, rapid Cuts and Profiles : PAM (e) Shallow Pocketing : AJM Unconventional Manufacturing Methods 567 3. Process Capability. Table 9.2. gives the typical values of the various process capabilities. Table. 9.2. Process Capability of NTMM Process Capability Process Metal Removal Surface Finish Accuracy (μm) Specific power Penetration Rate, (mm3/s) (μm, CLA) (kW/cm3/min) rate, (mm/min) ECM 2700 0.1 - 2.5 50 7.5 12.0 EDM 14 0.4 - 12.5 10 1.8 12.0 EBM 0.15 0.4 - 6.0 25 450 160.0 LBM 0.10 0.4 - 6.0 25 2700 100.0 PAM 2700 Rough 250 0.90 250 USM 14 0.2 - 0.5 7.5 9.0 0.50 AJM 0.014 0.5 - 1.2 50 312.5 - CHM 0.8 0.4 - 2.5 50 - 0.02 By going through the Table 9.2, it can be observed that : EDM has the lowest specific power requirement and can achieve sufficient accuracy. ECM has the highest metal removal rate, MRR. USM and AJM have low MRR and combined with high tool wear, are used for non-metal cutting. LBM and EBM have high penetration rates with low MRR and, therefore, are commonly used for microdrilling, sheet cutting, and welding. CHM is used for manufacturing PCB and other shallow components. PAM can be used for clean, rapid cuts and profiles in almost all plates upto 20 cm thick with 5° to 10° taper. 4. Process Economy. The process economy of NTMM is given in Table 9.3. Table 9.3. Process Economy Process Capital Cost Tooling and Power require- Efficiency Total consu- fixtures ment mption USM Low Low Low High Medium AJM V. Low Low Low High Low ECM V. High Medium Medium Low V. Low CHM Medium Low High Medium V. Low EDM Medium High Low High High EBM Medium High Low High High EBM High Low Low V. High V. Low LBM Medium Low V. Low V. High V. Low PAM V. Low Low V. Low V. Low V. Low Conventional Low Low Low V. Low Low mechining Limitations of NTMM. These methods are generally more expensive to set up, have a slower rate of metal removal and require considerable technical know how. Out of the above machining methods, the electrical machining methods have the following advantages : 1. The tool material does not have to be harder than the work material. 2. Tool forces do not increase as the work material gets harder. 3. Economic metal removal rate does not decrease as the work material gets harder. 568 A Textbook of Production Technology However, the limitation of electrical machining methods is that the work material must be an electrical conductor. Also, consumption of electrical energy is very large. The NTMM which have not been proved commercially economical are : USM, AJM, CHM, EBM and PAM. (b) Unconventional Forming Methods. In these methods, the metals are formed through the release and application of large amounts of energy in a very short time interval. This makes it possible to form large parts and difficult to form metals with less expensive equipment and tooling than would otherwise be required. Unconventional forming methods can be broadly grouped under two categories : High Energy Rate Forming methods (HERF) and High Velocity Forming methods (HVF). In HERF, the released energy is used directly to form the metals, whereas, in HVF it is converted into mechanical energy which imparts high velocities to ram/die. The important processes under the first category are explosive forming, electro-hydraulic forming, electromagnetic forming etc. The important processes in the second category are : pneumatic mechanical forming, petro-forge hammer, high velocity forming machines from dynapack, clearing hammer, trans-energy and linear induction motors. HERF methods have one more plus point. The “Spring back” is minimal. This is due to the following fact : High energy pressure waves generated due to the release of energy produce high compressive stresses in the metal when it is forced against the die surface. Due to this, some elastic deformation of the die occurs, which results in over forming of the workpiece. Due to all this, the spring back will be almost nil or minimal when the forming is completed and the forming load is taken off. In this chapter, we shall discuss some of the above mentioned non-conventional manufacturing methods. 9.2. ELECTRICAL DISCHARGE MACHINING (EDM) It has long been recognized that a powerful spark, such as at the terminals of an automobile battery, will cause pitting or erosion of the metal at both the anode and cathode. This principle is utilized in Electric Discharge Machining (EDM), also called spark erosion. If anode and cathode are of the same material, it has been found that greater erosion takes place at anode (positive electrode). Therefore, in EDM process, work is made the anode and the tool is the cathode (negative electrode). 9.2.1. Description of Process. The mechanical set up and the electrical set up are shown in Fig. 9.1. Power for generating the spark is fed from an A.C. source to a rectifier. The D.C. output is then fed to the spark generating circuit. The tool and work and also the tool slide servo-mechanism, are connected into the circuit. The tool and work are submerged in a fluid having poor electrical conductivity (dielectric fluid). The function of the servo-mechanism is to maintain a very small gap (approximately 0.025 to 0.075 mm) between the tool and the work. The spark is a transient electric discharge across the gap between work and tool. When the potential difference (voltage) across the gap becomes sufficiently large, the dielectric fluid becomes ionized and breaks down to produce an electrically conductive spark channel and the condensers discharge current across the channel in the form of a spark. When the voltage drops to about 12 volts, the spark discharge extinguishes and the di-electric fluid once again becomes deionized. The condensers start to recharge and the process repeats itself. The spark occurs in an interval of from 10 to 30 microseconds and with a current density of approximately 15 - 500 A per mm2. Thus, thousands of spark-discharge occur per second across the gap between tool and work, which result in a local temperature of approximately 12000°C. At each discharge, heat transfer from high temperature spark (plasma) to both tool and work, melts, partially vaporizes and partially ionizes the metal in a thin surface layer. The resulting work surface is composed of extremely small craters. The time interval between the sparks is so short that the heat is unable to conduct into the tool and work. Unconventional Manufacturing Methods 569 Servo Gear motor Tool Feed box Servo Insulation control R Dielectric – fluid D.C. SUPPLY Tool C V0 Work + Fixture Base Fig. 9.1. Schematic Arrangement of EDM Method. Power Supplies. Many types of electric circuits are available to provide pulsating D.C., across the workpiece-tool gap. The earliest models of ED Machines were fitted with Resistance- Capacitance (R-C) relaxation circuit (Fig. 9.1). In this system, a current flowing through a resistor R charges a capacitor C to a voltage (50 to 200 V), at which spark-breakdown occurs. The value of C, which may be as high as 400 μ f (on heavy machines) is generally kept variable on most EDM machines, so that the machining conditions (rough, medium and finish) can be varied, to get the desired accuracy and surface finish. This value of R is kept sufficiently high, to prevent continuous arcing after the spark. The ratio of the discharge or breakdown voltage and the applied D.C. source voltage lies between 0.7 and 0.9. In this circuit, tool becomes alternately positive and negative terminal. At each reversal of polarity, there is more wear on tool than on work. So, tool wear is greater in this arrangement. Another disadvantage is that the metal removal rate is not high. Rotary Impulse Generator. In this system, the capacitor is charged through a diode, during the first half cycle. During the second half of the cycle, the sum of the voltage generated by the generator (which is rotated by a motor) and the charged capacitor, is applied to the workpiece-tool gap. The metal removal rate is higher, but the surface finish is not good. Transistorized Pulse Generator Circuit. In the above two systems, there is no provision to stop the current flow in the event of a short circuit. To overcome this problem, a transistor is used as the switching device for an automatic control in Transistorized pulse generator circuit. Circuits are also available in which reverse pulse can be eliminated, resulting in lesser tool wear. Potential volts = 100 to 380, current amperes = 50. Dielectric Fluid. A dielectric fluid is a medium that does not conduct electricity. In EDM process, the functions of dielectric fluid are : 1. It acts as an insulating medium. 2. It cools the spark region and helps in keeping the tool and workpiece cool 3. It maintains a constant resistance across the gap. 4. It carries away the eroded metal particles. The dielectric fluid is circulated through the tool at a pressure of 0.35 N/mm2 or less. To free it from eroded metal particles, it is circulated through a filter. Dielectric fluids must not be hazardous to operators or corrosive to equipment. The various mediums which are used as dielectric fluids are : petroleum based hydrocarbon fluids, paraffin, white spirit, transformer oil, kerosene, mineral oil or mixture of these. Occasionally, ethylene glycol and water miscible compounds are also used as dielectric fluids. 570 A Textbook of Production Technology Tool Materials. The prime requirements of any tool material are : 1. It should be electrically conductive. 2. It should have good machinability. 3. It should have low erosion rate or good work to tool wear ratio. 4. It should have low electrical resistance. 5. It should have high melting point. 6. It should have high electron emission. The usual choices for tool (electrode) materials are : Copper, brass, alloys of zinc and tin, hardened plain carbon steel, copper tungsten, silver tungsten, tungsten carbide, copper graphite, and graphite. The various factors affecting the choice of electrode material are: machining applications, material being machined, availability, cost and the practical limitations inherent in processing the electrodes to the desired shape. One major drawback of EDM is the wear that occurs on the electrode at each spark. Tool wear is given in terms of wear ratio which is defined as, Volume of metal removed work Wear ratio Volume of metal removed tool Wear ratio for brass electrode is 1 : 1. For most other metallic electrodes, it is about 3 : 1 or 4 : 1. With graphite (with the highest melting point, 3500°C), the wear ratio may range from 5 : 1 upto 50 : 1. Servo-Mechanism. As already mentioned, the gap between the tool and work has a critical importance. As the workpiece is machined, this gap tends to increase. For optimum machining efficiency, this gap should be maintained constant. This is done by servo- mechanism which controls the movement of the electrode. The servo-mechanisms can either be electro-mechanical (Fig. 9.1) or hydraulic. In the electro-mechanical system, the electrode is moved by a rack and pinion arrangement which is driven through reduction gearing from a D.C. servo motor. As the gap between the tool and workpiece increases because of their wear, the voltage across the gap drops. This voltage drop is automatically measured and a feedback is given to the servo control which sends a signal to the servo-motor, which operates the electrode downward until the gap reaches its critical value again. Metal Removal Rate and Surface Finish. Metal removal rate (volume of metal removed from the work per unit time) depends upon current density and it increases with current. But high removal rates produce poor finish. Therefore, the usual practice in EDM is (as in conventional methods) : a roughing cut with a heavy current followed by a finishing cut with less current. Metal removal rates are usually low, approximately 80 mm3/s, but this can be increased on machines having more efficient pulse generators. Tolerances of the order of 0.05 to 0.13 mm are commonly obtainable and with extra care, tolerances of 0.003 to 0.013 mm are possible. Surface finish of the order of 0.2 μm Ra is possible. In addition to current density or the electric eneregy expended per spark, the MRR per spark also depends upon the period over which it is expended. To minimize the structure-damaging heat transfer into the bulk of the workpiece, a spark duration of 10 to 20 micro-seconds appears to be optimum. The MRR : (i) increases with discharge time until an optimum value, after which it suddenly drops. (ii) increases with forced circulation of dielectric fluid. Unconventional Manufacturing Methods 571 (iii) is maximum when the pressure is below atmospheric, that is, cavitation helps in increasing MRR. (iv) increases with capacitance. (v) increases upto optimum work-tool gap, after which it drops suddenly. Advantages 1. EDM can be used for machining any material that is electrically conductive, thus including metals, alloys and most carbides. 2. The melting point, hardness, toughness or brittleness of the material poses no problems. Due to this EDM can be used for machining materials that are too hard or brittle to be machined by conventional methods. 3. The method does not leave any chips or burrs on the work piece. 4. Cutting forces are virtually zero, so very delicate and fine work can be done. 5. The process dimension repeatability and surface finish obtained in finishing are extremely good. 6. The characteristic surface obtained, which is made up of craters, helps in better oil retention. This improves die life. 7. The process once set up does not need constant operator’s attention. Disadvantages 1. Only electrically conductive materials can be machined by EDM. Thus non - metallics, such as plastics, ceramics or glass, cannot be machined by EDM. 2. Electrode wear and overcut are serious problems. 3. A rehardened, highly stressed zone is produced on the work surface by the heat generated during machining. This brittle layer can cause serious problems when the part is put into service. 4. Perfectly square corners cannot be made by EDM. Product Applications. EDM is widely used for machining burr free intricate shapes, narrow slots and blind cavities etc., for example, sinking of dies for moulding, die casting, plastic moulding, wire drawing, compacting, cold heading, forging, extrusion and press tools. Almost any geometry (negative of tool geometry) can be generated on a workpiece if a suitable tool can be fabricated (the use of punch as a tool to machine its own mating die is commonly employed in EDM method). The method is also employed for blanking parts from sheets, cutting off rods of materials, flat or form grinding and sharpening of tools, cutters and broaches. In EDM method, small holes, about 0.13 mm, in diameter and as deep as 20 diameters can be drilled with virtually no bending or drifting of hole. Due to this, EDM is particularly useful for machining of small holes, orifices or slots in diesel-fuel injection nozzles, or in aircraft engines, air brake valves and so on. 9.2.2. Wire Cut Electro-Discharge Machining Wire (WCEDM, Fig.9.2). The basic mechanism of metal Coolant Electrode removal in WCEDM (also known as Travelling wire EDM) is identical to that in die-sinking type EDM. However, there Work are some important differences :- Piece 1. Instead of a moving electrode (as in EDM), the electrode in this process is a moving wire of Cu or brass. X A vertically oriented wire is fed into the workpiece continuously travelling from a supply spool to a take up spool, so that it is continuously renewed, since it will get worn out during the process. For this purpose, a hole is Y predrilled in the work- piece, through which the wire electrode will pass. Fig. 9.2. Schematic of WCEDM. 572 A Textbook of Production Technology 2. The whole workpiece is not submerged in dielectric medium (as in EDM). Instead, the working zone alone is supplied with a co-axial jet of dielectric medium, which in this process is deionized water instead of hydrocarbon oils in EDM. This system removes the eroded particles efficiently and keep the working zone cool. 3. One of the most important aspects in WCEDM is its ability to cut complex two dimensional profiles. For this, the machine table on which the workpiece is held, has movements along X-axis and y- axis. The drive unit for the machine table (close loop DC motor drive system or a DC stepper motor drive) are controlled by the numerical control units based on CNC system. This system is easily programmable for linear and circular path interpolation and they provide high resolution data for accurate control of the slides of the worktable. This makes this method capable of machining any complicated through hole dies of electrically conductive materials. Advantages In addition to the above advantages, the process has got the following advantages also : 1. Saving of stages in sequential tools, due to absence of split lines in the die, hence permitting more punch opening per stage. 2. Moulded parts will not have flashes, as the moulds with draught can be made without vertical divisions. 3. Tool manufacturing and storage is not required. 4. Heat treatment distortions are totally avoided, as the workpieces are hardened before cutting. 5. Cycle time for die manufacture is shorter, as the whole work is done on one machine. 6. Inspection time is reduced, due to single piece construction of dies with high positioning accuracy. 7. The time utilization of WCEDM is high, as it can cut right through the day (24 hours a day). 8. Economical, even for small batch production, including prototypes, as most of the programming can be easily done. 9. High surface finish, with low thermal affected zone depths are obtained. This reduces the manual finishing operation time. 10. Avoids rejections, due to initial planning and checking the programme. 11. Improvement in design technique allows for easier layout in the compound dies. The method is best suited for parts having extra-ordinary workpiece configurations, close tolerances, the need of high repeatability and of hard to work materials. Common examples of jobs are : gears, tools, dies, rotors, turbine blades and cams, for small to medium size batch production. 1 Time of production may vary from hour to 20 hours. 2 9.2.3. Electric Discharge Grinding (EDG). EDG (Fig. 9.3) is similar to EDM except that the electrode is a rotating wheel (usually graphite). Positively charged workpieces are immersed in or flooded by a dielectric fluid and fed past the negatively charged wheel by servo-controlled machine table. Metal is removed by intermittent high frequency electrical discharges passing through the gap between wheel and workpiece. Each spark discharge melts or vaporizes a small amount of metal from the workpiece surface, producing a small crate at the discharge sit, as in EDM. The negative of the form on the wheel face is transferred to the workpiece surface. The metal chips are flushed away by the dielectric fluid carried through the cutting area by the wheel rotation. The spark gap is normally held at 0.013 to 0.076 mm by a servomechanism that controls the motion of Unconventional Manufacturing Methods 573 the worktable. The graphite wheel is rotated at 0.5 to 3 m/s. Slipring and brush assembly Graphite grinding Work leads Wheel Work pan Dielectric Job Fluid Machine Table Power supply Direction Automatic of table travel servo controlled under servo control table drive Fig. 9.3. Schematic of EDG. The power supply and the dielectric fluid are similar to those used in EDM, but lower amperage is used in most EDG applications, because the cutting area is usually small and the method is used primarily to achieve accuracy and smooth finish. The method can be used for : external cylindrical grinding, internal grinding and surface grinding. EDG is generally used for operations such as, 1. Grinding carbide and steel at the same time without wheel loading. 2. Grinding thin sections where abrasive wheel pressures might cause distortion. 3. Grinding brittle materials or fragile parts where abrasive materials might cause fracturing. 4. Grinding through forms, where diamond wheel costs would be excessive. 5. Grinding circular forms, in direct competition with abrasive wheel methods. 9.3. ELECTRO-CHEMICAL MACHINING (ECM) In ECM, the principle of electrolysis is used to remove metal from the workpiece. The principle of electrolysis is based on Faraday's laws of electrolysis which may be stated as : ‘‘The weight of substance produced during electrolysis is directly proportional to the current which passes, the length of time of the electrolysis process and the equivalent weight of the material, which is deposited’’. ECM is just the reverse of electroplating (which also uses the principle of electrolysis). In electroplating, two dissimilar metals are in contact with an electrolyte (an electrically conductive fluid) and anode loses metal to the cathode. In ECM, work is made the anode and the tool is the cathode. Therefore, work loses metal, but before it can be plated on to the tool, the dissolved metal is carried away in the flowing electrolyte. Description of Process. Schematic view of ECM method is shown in Fig. 9.4. In the D.C. supply circuit, the workpiece is made the anode and the tool is made the cathode. The tool is of hollow tabular type, to provide passages for circulating electrolyte between the tool face and the work. As the power supply is switched on and the current starts flowing through the circuit, electrons are removed from the surface atoms of the workpiece. These ions tend to migrate to the hollow cutting tool. But before these can get deposited on the cutting tool face, these are swept away by rapidly flowing electrolyte, out of the gap between the tool and the workpiece. The tool is fed towards the workpiece automatically at constant velocity to control the gap between the electrodes. Tool face has the reverse shape of the desired workpiece. The sides of the tool are insulated to concentrate the metal removal action at the bottom face of the tool. 574 A Textbook of Production Technology Constant-velocity down feed Electron flow Hollow insulated Electrolyte flow tool (cathode) Filter – D.C. Supply + Work (Anode) Insulation Fixture Base Pump Fig. 9.4. Schematic Arrangement of ECM. Advantages Like EDM, the ECM method has also been developed for machining new hard, and tough materials (for rocket and aircraft industry) and also hard refractory materials. ECM has the following outstanding advantages : 1. ECM is simple, fast and versatile method. 2. The metal removal is entirely by metallic ion exchange and so there are no cutting forces and the workpiece is left in an undisturbed, stress free state. It is never subjected to high temperatures or stresses. Also, due to the absence of cutting forces, very thin sections can be machined. Again, there will be no residual stresses in the workpiece as a result of the operation. 3. If proper electrolytes are used, there is no tool wear at all. 4. The process character does not depend at all upon the physical properties of the metal (hardness, toughness etc.). 5. Surface finish can be extremely good. 6. No burrs are produced. 7. Fairly good tolerances can be obtained. 8. The process can be easily automated. Limitations of ECM 1. Large power consumption, and the related problems. 2. Sharp internal corners cannot be achieved. 3. Post machining cleaning is a must, to reduce the corrosion of the workpieces. 4. Tool design is complicated and needs cut and try method to achieve the final shape. 5. Maintenance of higher tolerances requires complicated controls. Power Supply. The electrical supply circuit in ECM is simpler as compared to EDM. ECM power supplies are currently available in sizes upto 10,000 amperes (a few machines are rated upto 40,000 amperes). The range of voltage on most machines is from 5 to 30 volts d.c. In ECM method, a constant voltage has to be maintained. For this, voltage regulation circuits are available. Cut-off circuits are also available in the power-supply units to stop the supply of power to the machining gap. In ECM, the current density is usually high. At low current densities, the metal removal rate is low. In order to have a metal removal of the anode, a sufficient amount of current has to be given. Unconventional Manufacturing Methods 575 It has been found that at low current densities (5A / cm2), O2 is evolved at anode and all the energy is used for this purpose. In order to have a high current efficiency, higher current densities, of the order of 200 A/cm2, are used. Electrolyte. The electrolyte in ECM method serves two purposes. (1) It is essential for electrolytic process to work, and (2) It cools the cutting zone which becomes hot due to the flow of high current. The electrolytes vary from strong salt to strong acid solution, depending on the work material. Neutral salts are used as electrolytes in preference to highly corrosive acids and alkalies. The sodium and the potassium salts are probably the most common. A 20% common salt (NaCl) solution is appropriate for many materials. Some electrolytes are naturally corrosive and so ECM equipment is made of stainless steel and plastics. The electrolyte solution is pumped between the tool/workpiece gap at about 2.5 N/mm2 and 30 m/s. The electrolyte should never be allowed to boil. For this, the temperature of the electrolyte in the tank is thermostatically controlled (35° to 65°C), by electric heaters together with a heat exchanger or evaporative condenser. Unlike EDM, it is not necessary for the work to be submerged in liquid solution. Tool. As mentioned above, there is virtually no tool wear, so, any material that is good conductor of electricity can be used as tool material. Other requirements of good tool material are: 1. It should have good thermal conductivity. 2. It should be strong enough to withstand the high hydrostatic pressures caused by electrolyte flow. 3. It should be easily machined. 4. As the surface finish of the workpiece mainly depends upon the condition of the bottom face of the tool, this portion of the tool should be polished. The tool may be made from titanium, copper, brass, or stainless steel. The outer surface of tool is insulated by Vinyl, Teflon, epoxy, enamels or high temperature varnish. A constant gap of about 0.01 mm is maintained between the tool face and work. For this, the tool is fed towards the work at constant velocity with feed rate of about 0.5 mm to 25 mm per minute. The movement of the tool slide is controlled by a hydraulic cylinder. Machined Surface. The machining rate and surface finish are directly proportional to current density. Surface finish values as low as 0.1 μm Ra are possible with a tolerance of the order of 0.005 mm. The metal removal rates are high, upto 550 mm3/s. Metal Removal Rate. Even though, the metal removal rate depends on the current density, there is a limit upto which it can be done. Forcing more and more current per unit area through the electrolyte-surface combination, will saturate the system due to one of a number of effects given below : 1. Too much heating of the electrolyte (due to 12.R effect) may cause its boiling. This will appreciably reduce the electrolytic action. 2. The metallic ions react with an electrolyte component, to form a reaction product, which will greatly impede the action, unless it is removed from the surface. 3. Polarized ionic layers may build up at either electrode, causing large voltage drops near the surfaces. 4. Gas evolution (H2) at the cathode surface may reduce the current flow. The limiting effect of the above factors can be reduced by increasing the flow of clean electrolyte in the anode-cathode gap. Because this gap is small (0.025 to 0.125 mm) the high rate of electrolyte flow will require high fluid pressures. This will result in large hydrostatic separating forces between the tool and the work. For most operations, the maximum flow rate is determined by the practical considerations imposed by the phenomenon of cavitation. During cavitation, vapour bubbles are hydro-dynamically formed in the fluid and produce uneven metal removal. 576 A Textbook of Production Technology Product Application. ECM methods Feed find wide application in rocket, aircraft and gas turbine industries. ECM is a standard method for machining gas turbine blades. ECM is increasingly being used in airframe Shaped Tool component fabrication, die sinking and the – manufacture of general machine parts. The Work D.C. different operations like turning, drilling, Electrolyte Flow milling, shaping and planing etc. can be + combined and done quickly by ECM method. Product applications of ECM include Shaped Tool producing simple to complex cavities (die sinking), embossed surfaces, blind holes, through holes, irregular holes and complex Feed external shapes; cutting test blocks and sawing ingots to various desired lengths in Fig. 9.5. steel mills; rough machining of massive forgings; honey-combing aircraft panels ; jet engine blade airfoils (Fig. 9.5) and cooling holes ; operations on rock boring bits, transformer cores, pump impellers, gears ; operations on rock boring bits, transformer cores, pump impellers, gears ; extremely rapid deburring operations and salvage operations on worn machine parts or on dies. One very important advantage of ECM is that by merely changing electrolyte and current density, we can shift from roughing to polishing. At very high current densities and high electrolyte velocities, a very high polish can be obtained. 9.4. ELECTROLYTIC GRINDING OR ELECTRO-CHEMICAL GRINDING (ECG) In ECG method, the work is machined by the combined action of electro-chemical effect and conventional grinding operation. The majority of the metal removal results from the electrolytic action. A schematic view of electrolytic grinding is shown in Fig. 9.6. Here, the tool electrode is a rotating, metal bonded diamond or aluminium oxide wheel and it acts as cathode. The work acts as anode and hence current flows between the work and wheel. A constant gap of about 0.25 mm is maintained between work and wheel and through this gap, an essentially neutral electrolyte is circulated. The electrolyte is carried past the work surface at high speed by the rotary action of the grinding wheel. The grinding wheel runs at speeds of 900 to 1800 m/min. The important functions of abrasive particles are : (1) they act as insulators to maintain a small gap between the wheel and the workpiece (2) they remove electrolysis products from the working area (3) to cut chips if the wheel should contact the workpiece Abrasive Particles particularly in the event of power failure. Electrical When the process is started, about 90% of Wheel Connections Filter metal is removed by electrolytic action and only about 10% by abrasive grinding. The Work Piece abrasive particles rub against the workpiece, Feed Insulation scrubbing off the electrolysis products, thus – D.C. Work Table allowing good dimensional control. For best Supply dimensional control and efficiency, the non- Pump cutting areas of the tool (wheel and its Electrolyte spindle) should be insulated from the rest of the machine. Surface finish, precision and metal removal rate are influenced by the composition of the electrolyte. The metal Fig. 9.6. Schematic set up of Electrolytic Grinding. Unconventional Manufacturing Methods 577 removal rate also depends upon the pressure between the wheel and workpiece and is directly proportional to it. The following values can be commonly obtained : accuracy of 0.01 mm, surface finish of 0.1 μm Ra and metal removal rate 15 m m3/s. The commonly used electrolytes are : Aqueous solutions of sodium silicate, borax, sodium nitrate and sodium nitrite. The power supply is : D.C. voltage of 5 to 20 V, current density of 100 to 200 A/cm2. The ECG method is used for workpieces sensitive to the heat of the usual grinding methods. It is used almost exclusively for shaping and sharpening carbide cutting tools. It has been also successfully applied to refractory metals, high-strength steels, nickel and cobalt base alloys. The method has the following advantages over conventional grinding : 1. Tool wear is negligible which greatly increases the life of the grinding wheel. This factor is particularly valuable in the grinding of hard metals such as tungsten carbide where, costly diamond wheels are ordinarily used. In ordinary grinding there are high wear rates on these expensive diamond wheels. 2. It produces a smoother surface and does not produce surface stresses and distortion as in conventional grinding. 3. ECG is much more rapid than ordinary grinding. Like EDM and ECM, power consumption is high in ECG. 4. Requires very light grinding pressures and eliminates thermal problems. 5. Delicate parts can be machined without distortion. 6. Can machine burr-free parts. 7. Improved surface finish upto 0.μ m Ra, with no grinding marks. 8. In ECG, the ECM action is particularly efficient because, (a) the grinding grits remove all reaction products and polarized layers, presenting very clean metal to the electrolyte. (b) the grinding wheel continuously pumps fresh electrolyte into the active zone. Disadvantages of ECG : 1. Higher cost of grinding wheel. 2. Higher cost of maintenance. 3. Tolerances achieved are rather low, (of the order of 0.025 mm). Due to this, the workpieces need final abrasive machining. 4. Difficult optimization, due to the complexity of the process. Stainless steel tool Approx. 6.5 mm wall (Cathode, – ) Electrolyte Inlet Sleeve Gap Spacing 0.076 to 0.127 mm at start Workpiece (Anode, +) Exit Holes For Electrolyte Expandable Honing Stone in Slot. Fig. 9.7. Schematic of ECH. 578 A Textbook of Production Technology 9.4.1.Electro-Chemical Honing (ECH), (Fig. 9.7). Electro-chemical honing is similar to ECG in that it combines the anodic dissolution of material with abrasive cutting action. ECH, however, uses rotating and reciprocating, non-conducting bonded honing stones instead of a conducting grinding wheel. ECH is a modification of conventional honing and it combines the metal removal capabilities of ECM with the accuracy capabilities of honing. Electrolyte is introduced into the gap between the cathodic honing tool and the anodic workpiece, while D.C. is passed across the gap and the rotating tool is reciprocated through the work bore. The gap between the tool and the workpiece is usually about 0.075 to 0.125 mm at the start of the cycle and increases by the amount of stock removal per cycle. The gap can increase upto 0.50 mm or more. Most of the metal removal is by electro-chemical action. Because the honing stones keep the workpiece surface clean, the electrolyte does not have to be as corrosive as is necessary for ECM. On many metals, sodium nitrate can be used instead of more corrosive sodium chloride or acidic electrolytes. Several rows of small holes in the tool body enable electrolyte to be introduced directly between the tool and the work surface. Supply of the electrolyte can be upto 112.5 lit/min under a pressure of upto 1.05 N / mm2. depending upon the workpiece size. Bonded - abrasive honing stones are inserted in slots in the tool (which is normally of stainless steel). These stones are forced out radially by the wedging action of the cone in the tool. The expansion is controlled by an adjusting heat in the spindle of the machine. The stones, which must be non-conducting, assist in the metal removal action and generate a round, straight cylinder. They are fed out with equal pressure in all directions so that their cutting faces are in constant contact with the cylinder's surface. They abrade the residue left by the electro-chemical action so that a clean surface is always presented for continuing electrolysis. If the cylinder is tapered, out of round or wavy, the stones cut most aggressively on the high or tight areas and remove the geometric error. Automatic gauging devices designed into the system initiates a signal when the cylinder is of the desired diameter size and the cycle is automatically terminated. If the surface finish must be held to a special roughness, the stones are allowed to cut for a few seconds after electricity has been cut off. The direct current power source is a 3000 A, 24 V rectifier. Current density is of the order of 15 to 40 A/cm2 as compared to 100 to 240 A/cm2 for ECG. Commercial ECH equipment is available only for internal cylindrical grinding, with a size tolerance of 0.013 mm on diameter and 0.005 mm on roundness and straightness. The size of the cylinder that can be processed with ECH is limited only by the current and the electrolyte that can be supplied and properly distributed in the circuit. Hard materials can be finished more quickly than soft materials. Advantage 1. Faster and higher metal removal rate with reduced hone wear. It is about 10 times of that for conventional honing and about 4 times of that for internal grinding. 2. It removes sharp or burred edges. 3. Increased life of bonded abrasive. 4. The finished surfaces are virtually free from stress or heat damage. 5. Less pressure is required between stones and work. 6. Reduced noise and distortion, when honing thin walled tubes. 7. Cooling action of the electrolyte leads to increased accuracy with less material damage, so the process is particularly suitable for parts susceptible to heat and distortion. Unconventional Manufacturing Methods 579 9.4.2. Electro-Chemical Deburring (ECD). The process of ECM deburring (ECD) Electrolyte is identical to that of ECM countersinking except that there is no relative movement of the tool with respect to the workpiece. The tool and the Gap W workpiece are placed in a fixed relative position Burr O with a gap of 0.1 to 1.0 mm, (Fig. 9.8). The tool Tool R which is positioned near the base of the burr, is (–) K designed so that only that portion of the P I workpiece containing burrs is exposed to tool E material. The remaining portion of the tool is C insulated. E (+) The current levels in ECD are of the order of 6A/cm of linear edge length at 7 to 25 V DC Insulation supply. The electrolyte which is generally sodium nitrate is circulated at a pressure of 0.1 to 0.4 N/ Fig. 9.9. Schematic of ECD. mm2 to give flow rate of 5 to 20 lit/min for a 100 A electrolyzing current. Advantages 1. Both external and internal burrs, which may be inaccessible, can be removed. 2. The equipment is simple to operate and easy to maintain. 3. The system is very fast (5 to 40 times faster than hand deburring) and the operating costs are low. 4. Burrs may be removed even after heat treatment. 5. No stresses or embrittlement caused by ECD. 6. No tool wear, and tool designs are fairly simple. 7. Electrolytic system is small and simple to maintain. 8. A simple power supply system, without an extensive rapid shut off system, can be used. 9. ECD can be included in transfer lines. Applications. Automobile connecting rods, gear teeth, blanking dies, valve ports, nozzle interesting holes etc. 9.5. CHEMICAL MILLING In chemical milling, also known as chemical machining (CHM), photochemical machining, photo fabrication or photo Metal Removed etching, material is removed from selected areas of a workpiece by controlled chemical dissolution with chemical reagents, which may be either acidic or basic, depending on the material of the workpiece. The areas of the workpiece which are not to be machined are masked, (Fig. 9.9). The workpiece is then either Masking immersed in or exposed to a spray of chemical reagent. The time of immersion or exposure depends upon the amount of material to be removed by chemical action. The component to be machined is first cleaned in trichloroethylene vapour or in a solution of alkali at 80 to 85°C. This remove dust and oil. This ensures a good adhesion of the coating or mask which is applied to protect the portions which are not to be machined. The Fig. 9.9. Chemical Milling. component is then dried. 580 A Textbook of Production Technology The simplest method of masking is with masking tape. The usual methods are : scribed-and- peeled maskants and by photoresists. In the first method, a maskant (paint like material) is applied to the entire surface of the workpiece by dip, spray, brush or stencil. After the maskant hardens, it is removed from those areas where metal removal is desired, by scribing through the maskant with a knife and peeling away the desired portions. This method is used when the workpiece is not flat, or it is very large and the number of pieces to be produced are small. Where economical, templates may be used to assist in scribing. Photoresists are an excellent method of masking, especially for complex work. The various steps in this method are : 1. A large scale drawing of the part (know as ‘artwork’) is pre- pared. The scale of drawing may be upto 20,100 or as much as 200 to 1. 2. The master drawing is photographed and reduced to final size on a process camera, to get the master negative. 3. The metal workpiece is thoroughly cleaned and is then coated with an emulsion of photosensitive resist. The coating may be applied by dipping, spraying, brushing, roller coating or flow coating. 4. The coating is then dried and hardened by baking in an oven upto about 120°C. 5. The master photographic negative is placed over the dried photoresist coating and exposed to ultraviolet radiation from a mercury lamp. The clear areas of the master allow radiation to harden the resist. The black areas of the master protect the resist from the radiation and keep it unhardened in these areas. Each side of the workpiece can be printed individually or the two sides can be exposed simultaneously by using special mirror image master equipment. 6. The workpiece is then de- veloped by immersing it into a tank containing an organic solvent bath solution. The unexposed areas on the work- piece are dissolved away in the developer, while the exposed remain on the workpiece. 7. The final step is to spray the workpiece with or immerse it in the chemical reagent. The material is etched away from the surface of the workpiece except that portion on which the protected image is printed. Maskants and Etchants used in CHM : Maskant materials are : Plastics and Elastomers Plastics commonly used are : PVC, polystyrence, polyethylene The commonly used elastomers are : acrylonitrile rubber and butryl rubber The etchants used are :- Material Etchant 1. Al, M.S., Cu, Lead, Ni and Stainless steel Ferric chloride 2. Al alloys NaOH at 50°C 3. Zinc, Magnesium HNO3 4. Titanium, Silicon Hydrogen fluoride The use of chemical milling in the making of a disk with tapered sides is shown in Fig. 9.10. The disk is rotated in the chemical reagent while moving the axis of rotation gradually upward. By varying the vertical speed, different curvatures can be obtained. There are two variations of chemical milling : (i) Chemical blanking and (ii) contour machining. The difference between the two is that while Fig. 9.10. Chemical Milling. in chemical blanking, the material is etched entirely through a work piece, Unconventional Manufacturing Methods 581 in contour machining the material is selectively etched from certain areas on the workpiece. Chemical blanking is a method of cutting or stamping out parts from flat thin metal or foil sheets. In practice, the following results are achieved by chemical milling : (i) Metal thickness of blanked parts : About 1.50 mm. (ii) Depth of etch in contour machining : Approximately from 3.8 mm to 12.7 mm. Of course, heavy cuts have been made successfully (upto about 50 mm). However, lighter cuts are more characteristic of this process. (iii) Tolerance : About 0.05 mm per 2.54 mm of depth. (iv) Surface finish : Depending upon the material, characteristics of the chemical and the depth of cut, surface finishes can vary form 0.25 to 6.25 μmRa values. (v) Metal removal : Approximately 0.015 to 0.030 cm3 per minute. Advantages 1. The process is comparatively simple and there is no need of highly skilled labour, excepting for artwork and photography. 2. The process does not induce any stresses in the metal. 3. The process can be applied to any metal. 4. Parts of any shape and minimum thickness can be machined. 5. Parts of large sizes can be machined. Limitations 1. The metal removal rate is slow. 2. The material has to be fine grained, sound and homogeneous for best results. Any imperfections on the surface in the form of tool marks, scratches etc. must be removed before chemical milling, because the chemical reagent has the tendency to etch surface imperfections at a faster rate. Also, the parts should be heat treated and stress relieved before chemical milling. If there are any residual stresses in the part, these will get relieved during chemical milling resulting in warping of the part. 3. Weldments are usually not suitable for chemical milling because of non-uniform grain structure near welds. Product Applications. The chemically milled parts find main application in aerospace, aviation, automotive, electronic and instrument making industry. chemically blanked parts are used in the following products : tape recorders, computers, cameras, television sets, electric motors, timers, telephone systems, electric shavers and medical instruments etc. In aviation industry, chemical milling (contour machining) is used to produce special surface configurations on aircraft wing and fuselage sections. In aerospace industry, contour machining is used to produce contoured pockets on surfaces of bulkheads, skin panels etc. Chemical contour machining is also used to produce special geometries on the surfaces of parabolic radar reflectors, gyrohousings and heat exchangers etc. Other uses of contour machining are : to produce decorative surfaces on various flat or contoured parts, for example, elevator doors, ashtrays, plaques, signs, panels, instrument dials, metal tags or nameplates. The process is used for hard to reach spots, narrow recesses, form and helical grooves etc. 9.6. ULTRASONIC MACHINING (USM) ; (FIG. 9.11) Ultrasonic machining is a kind of grinding method. An abrasive slurry is pumped between tool and work, and the tool is given a high frequency, low amplitude oscillation, which, in turn, trans- mits a high velocity to fine abrasive particles which are driven against the workpiece. At each stroke, minute chips of material are removed by fracture or erosion. The general arrangement 582 A Textbook of Production Technology of ultrasonic machining is shown in Fig. 9.11. The equip-ment consists of a transducer, a tool holder and the tool. The linear oscillatory motion of the tool is obtained by magnetostrictive trans- ducer which converts electric energy into mechanical energy. The transducer consists of a stack of nickel laminations that are wound with a coil. When a high frequency current is passed through the coil, changes in the electromagnetic field produce longitudinal strains in the laminations. These longitudinal strains are transmitted to the tool through a tool holder. The tool oscillates linearly with an amplitude of about 0.05 mm at ultrasonic frequencies of from 15 to 25 kHz. Power supply is : Potential volts = 220, current = 12A. The tool, whose shape is essentially re-produced in the workpiece is also subjected to the impact-fracture action and should be made of a soft ductile material that is easily machined, for example, unhardened steel, copper or brass. The tool is ordinarily 0.075 to 0.10 mm smaller than the cavity it produces. The tool is brazed, soldered or fastened mechanically to the transducer through a tool holder. For selecting tool holder material, factors to be considered are : Conductivity, how well the material can be brazed and fatigue properties. The material for tool holder can be : titanium alloys, Monel, Aluminium, stainless steel etc. Important factor in tool fastening is that no relative motion and hence energy loss occurs. So, soldering and brazing have proved more satisfactory than mechanical clamping. The tool feed rate is about 0.1 mm/s, maximum. The abrasive used in USM can be aluminium oxide, boron carbide or silicon carbide grains in a slurry which also carries away debris. The slurry Nickel can be made in water which also acts as a coolant. Laminations The usual combinations are : boron carbide in water and silicon carbide in paraffin. Grain size of Power Supply Transducer abrasive particles ranges from 200 to 1000. The other commonly used abrasives are :- diamond dust and Boron Silicon Carbide and the Tool liquid carriers are :- kerosene, benzene, glycerol Reciprocating Holder or thin oil. Ratio of abrasive and liquid carrier Motion Abrasive Tool Slurry ranges from 1 : 4 to 1 : 1 by weight. Slurry can be fed externally or internally. In external feeding, the slurry is pump fed by several jets covering the Work circumference of the tool or by a single jet. In Machine Table internal feeding, hollow tools carry the slurry centrally to the workpiece. The slurry is to be fed continuously to avoid any drying up at the tool face. Fig. 9.11. Ultrasonic Machining. This method involves brittle fracture and obviously works only on relatively brittle materials. So, USM has been applied very successfully to hard, refractory, difficult to machine materials which are quite brittle, for example, ceramics, borides, ferrites, carbides, glass, precious stones, hardened steel, cermets and some super alloys etc. It is used chiefly for drilling holes, engraving, cavity sinking (carbide wire drawing dies), slicing and broaching etc. Hole diameter as small as 0.01 mm can be produced. Tolerance and surface finish depend upon grit size. More practical values for tolerance are 0.001 mm/mm. Of course, tolerance of 0.0005 mm/mm can be obtained. Usual values for surface finish are 0.25 to 0.50 μmRa. Metal removal is about 3 mm3/s. The ratio of workpiece wear to tool wear ranges from 1 : 1 to 100 : 1. The difference between conventional grinding and ultrasonic machining also known as grinding is that whereas in the former, the motion of the grinding grit is tangential to the surface of workpiece, Unconventional Manufacturing Methods 583 in USM (USG), the motion of grinding grits is normal to the work surface. Advantages of the process are : no thermal stresses, low tooling costs and the use of semiskilled workers for precision work. The limitations of the process are :- Its sonotrode vibration uniformity may limit the process to objects less than 100 mm in diameter and it has a low MRR. 9.7. USE OF HIGH ENERGY DENSITIES FOR MACHINING If a sufficiently high energy density can be produced and concentrated on a small zone of the workpiece, small-scale material removal can be accomplished. The material will get removed either mechanically or thermally. These processes include : Electron beam machining, Laser beam machining and Plasma arc machining, which will be discussed below : 9.7.1. Electron Beam Machining. In electron beam machining (EBM), electrons emitted by a hot surface and accelerated by a voltage of 10 to 50 kV are focused to a very small areas on the workpiece. This stream of high energy electrons posses a very high energy density (of the order of 104 kW / mm2)and when this narrow stream strikes the workpiece (by impact), the kinetic energy of the electrons is converted to powerful heat energy which is quite sufficient to melt and vapourize any material. Even though, the elect