Production Planning and Execution (PP) - PDF
Document Details
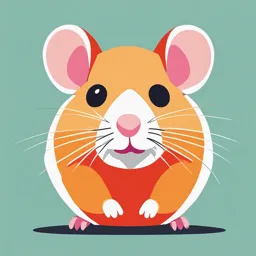
Uploaded by Joashin
2023
Tags
Related
- Production Planning 5.6 PDF
- Review of Enterprise Resource Planning (ERP) Systems PDF
- SAP S/4HANA Cloud Private Edition - Production Planning and Manufacturing Exam (C_TS422_2023) PDF
- C_TS422_2023 SAP Exam PDF Questions & Answers
- IS II Produktionsplanung (PP) PDF
- SAP PDF: Demand Management & Production Planning
Summary
This document covers the basics of Production Planning and Execution (PP). Key areas include PP organizational structure, master data, routing, and processes within an enterprise resource planning (ERP) context. The document also discusses demand management, material requirement planning (MRP), and manufacturing execution processes.
Full Transcript
IT2401 Production Planning and Execution (PP) Production Planning is the process of aligning demand with manufacturing capacity in creating production and procurement schedules for the finished products and component materials. As a SAP module, SAP PP tracks and recor...
IT2401 Production Planning and Execution (PP) Production Planning is the process of aligning demand with manufacturing capacity in creating production and procurement schedules for the finished products and component materials. As a SAP module, SAP PP tracks and records the manufacturing process flow such as the planned and actual costs and good movement from the conversion of raw material to semi-finished goods. SAP divided production into multiple processes: Production Planning, Manufacturing Execution including Discrete Manufacturing, Repetitive Manufacturing, and KANBAN, and Production – Process Industries designed primarily for chemical, pharmaceutical, food, and beverage industries and batch-oriented electronics. PP Organizational Structure (SAP SE, 2022) The PP organizational structure shares some organizational units with the previous modules. This includes: Client – an independent environment in the system. Company Code – the smallest organizational unit where a legal set of books can be maintained. Plant – the operating area or branch within the company, such as manufacturing, distribution, purchasing, or maintenance facility. Storage Location – allows differentiation between the various stocks of material in a plant. Work Center Locations – define where and when the operation is performed. These can be machines, people, production lines, or groups of tradespeople. The activities performed in this unit are evaluated by charge rates, which cost centers and activity types determine. PP Master Data (SAP SE, 2022) The PP Master Data has five (5) types: Material, Bill of Materials (BOM), Routing, Work Center, and Product Group. Material Master This master data contains all the information a company needs to manage a material. It includes the General Data of the material, Material Requirement Procedure (MRP), Lot Size Data, and MRP Areas. Bill of Materials (BOM) This master data lists the components that make up a product or assembly. For example, here are the components of a finished bike in Global Bike: Finished Bike o Wheel Assembly (Tire, Tube, Wheel, Hex Nut, Lock o Pedal Assembly Washer, Socket Head Bolt) o Chain o Frame o Brake Kit o Derailleur Gear Assembly o Warranty Document o Seat Kit o Packaging o Handler Bar Table 1. Component list. There are three (3) different kinds of BOM: Single-level lists the main components. Multi-level lists the main components and their sub-components. Variant Bill of Materials displays several products with many identical parts. 05 Handout 1 *Property of STI  [email protected] Page 1 of 6 IT2401 Item Category It is an object that defines the items in a BOM according to criteria, such as the object type of the component, for example, material master record or document information record. The Item Categories include the following: o Stock Item o Document Item o Non-stock Item o Text Item o Variable Material The item categories contain the screen sequence, field selection, default values, material entry, inventory management, and subitems. Routing It is the series of sequential steps or operations that must be carried out to produce a given product. It enables the planning of the production of materials (products.) It is also used as a template for production orders and run schedules and as a basis for product costing. Routing contains each step's what, where, when, and how. Figure 1 shows the series of sequential steps (operations) that must be carried out to produce a given product. Figure 1. Routing. Retrieved from SAP SE/SAP UCC. What – Operation 20, Where – ASSY100 (Assembly Work Center), When – 1 min, How – Attach the seat to frame. Figure 2. Routing for finished bike. Retrieved from SAP SE/SAP UCC. Figure 2 shows the routing involved for Finished Bikes. The Operation, Work Center, Plant, Description, and Time and Unit of Measurement are shown. Additionally, the Control Key and Activity Type are displayed. Control Key specifies how an operation or a sub- operation is processed in functions such as orders, costing, or capacity planning. Activity Type is a unit in a controlling area that classifies the activities performed in a cost center. 05 Handout 1 *Property of STI  [email protected] Page 2 of 6 IT2401 Work Center It is the location within a plant where Value-added work (operations or activities) is performed. It can represent people or groups of people, machines or groups of machines, and assembly lines. It defines capacities such as labor, machine, output, and emissions used in Capacity Requirements Planning (CRP), detailed scheduling, and costing. Work Centers capture and use the following Resource-related data: o Basic Data: Person Responsible, Location of Work Center o Scheduling Information: Queues and Move Times (interoperation), Formula Keys o Costing Data: Cost Center, Activity Types o Personnel Data: People, Positions, Qualifications o Capacity Planning: Available Capacity, Formulas, Operating Time o Default Data: Control Key, Standard Text Key Product Group It is aggregate planning that groups materials or other product groups (Product Families). It can be a multi- level or single-level, wherein the lowest level must always consist of materials. PP Processes (SAP SE, 2022) The Production Planning & Execution includes the following processes: Forecasting Master Production Scheduling (MPS) Sales and Operations Planning (SOP) Material Requirement Planning (MRP) Demand Management These processes are divided into three (3) layers: Strategic Planning (Forecasting and SOP), which involves the CEO, COO, CIO, CFO, Controller, and Marketing Director. The Detailed Planning (MPS and MRP) involves the Line Managers, Production Scheduler, MRP Controller, and Capacity Planners. The Manufacturing Execution involves Line Workers and Shop Floor Supervisors. Forecasting It is the foundation of a reliable Sales and Operations Planning (SOP). Accurate forecasts are essential in the manufacturing sector, which could help oversee the stock since overstocked and understocked warehouses both result in a profit loss. Though forecasting is vital, it should always be considered wrong. Forecasting Models include the following, which can be selected automatically or manually: o Trend – uses market research and consumer data to predict future trends. o Seasonal – used for predicting short-term customer demand at different times of the year. o Constant – uses the actual value of each period to predict the next. o Trend and Seasonal Sales and Operations Planning (SOP) Sales, Marketing, Manufacturing, Accounting, Human Resources, and Purchasing information came from this planning utilizing Intra-firm Collaboration (Institutional Common Sense). SOP consists of three (3) layers: Sales Plan, Production Plan, and Rough Cut Capacity Plan. Each layer must be planned at an aggregate level in a time bucket. 05 Handout 1 *Property of STI  [email protected] Page 3 of 6 IT2401 Demand Management It serves as the link between the Strategic Planning and Detailed Planning layers in Production Planning and Execution. It is the planning of requirement quantities and requirement dates for finished products and important assemblies. It also defines the strategy for planning, producing, or procuring a finished product. Demand Management can also be done manually or based on previous planning results such as sales planning, forecast, and SOP. The result of this process is called the Demand Program, which is generated from Independent Requirements, Planned Independent Requirements (PIR), and Customer Independent Requirements (CIR). Master Production Scheduling (MPS) It allows a company to distinguish planning methods between materials that strongly influence profit or use critical resources and those that do not. Material Requirement Planning (MRP) In MRP, the system calculates the net requirements while considering available warehouse stock and scheduled receipts from purchasing and production. During MRP, all levels of the bill of material are planned. MRP ensures the availability of materials based on the need generated by MPS or the Demand Program. It has five (5) logical steps: o Net Requirements Calculations o Lot Size Calculations: Static – based on fixed values in the Material Master. Periodic – groups net requirements together from multiple periods. Optimized – calculates the optimum lot size for several periods of net requirements. o Procurement Type: External Procurement (Purchase Requisition, Purchase Order, Schedule Line) and Internal Procurement (Planned Order, Production Order, Process Order). o Scheduling o BOM Explosion The output of MRP is a detailed production and/or purchasing plan. o Planned Order: A request created in the planning run for material in the future (converts to either a production or purchase order). o Production Order: A request or instruction internally to produce a specific product at a specific time o Purchase Order: A request or instruction to a vendor for a material or service at a specific time. Production Order It is another PP Process used to control production operations and associated costs and defines the material produced, quantity, location, timelines, work involved, resources used, and cost settlement. Manufacturing Execution Process (SAP SE, 2022) The Manufacturing Execution Process includes the following operations: Production Proposal Goods Issue Capacity Planning Completion Confirmation Schedule and Release Goods Receipt Shop Floor Documents Order Settlement 05 Handout 1 *Property of STI  [email protected] Page 4 of 6 IT2401 Schedule and Release Scheduling calculates the production dates and capacity requirements for all operations within an order. It determines a routing concerning the operation-specific timelines and Material Consumption Points. The release operation has two (2) processes: Header Level: Entire order and all operations are released for processing, order is given a REL status Operational Level: Individual operations within an order are released. A REL status is given to the order if the last operation is released. Until then, the order is given a PREL status. The time between scheduling and releasing an order is used for company checks and any preparation needed to process the order. Once an order has been released, it is ready for execution, wherein shop floor documents are printed, goods movements are executed, and confirmations against the order are accepted. Shop Floor Documents These are printed upon release of the Production Order. Examples include the following: o Operation-based Lists: Time Tickets, Confirmation Slips o Component-based Lists: Material Withdrawal Slips, Pull List (consumption list) o Production Resource Tool (PRT) Lists: Overview of PRTs used with their respective operations o Multi-Purpose Lists: Operation Control Ticket, Object Overview Goods Issue (Material Withdrawal) When a production order is created, it references a BOM to determine the necessary components to produce the material. It then places a reservation on each of the components. Upon release of the order (or operation), the reserved materials can be withdrawn from inventory. It is when the reservation and inventory are updated, and costs are assigned to the order as actual costs. Confirmations These are used to monitor and track the progression of an order through its production cycle. Exact confirmation shortly after the completion of an operation is essential for realistic production planning and control. Data that need confirmation include quantities, activity data, dates, personnel data, work center, goods movements, variance reasons, and PRT usage. Goods Receipt It is the acceptance of the confirmed quantity of output from the production order into stock. The Material, Accounting, and Controlling documents will be created here. A goods receipt will also do the following: o Updating the stock quantity o Updating the production order o Updating the stock value o Changing the price stored for future valuation Order Settlement It consists of settling the actual costs incurred in the order to one or more receiver cost objects. The parameters for Order Settlement include: o Settlement Profile: Specifies the receivers and distributions rule and method. o Settlement Structure: Determines how the debit cost elements are assigned to the settlement cost elements. 05 Handout 1 *Property of STI  [email protected] Page 5 of 6 IT2401 References: Quesnot, M. (2023). Introduction to SAP PP (Production Planning) in SAP cloud public edition. [Web Article]. Retrieved on February 20, 2024, from https://community.sap.com/t5/enterprise-resource-planning-blogs-by- members/introduction-to-sap-pp-production-planning-in-sap-cloud-public-edition/ba-p/13573624 Partner (2022 SAP SE/SAP UCC Magdeburg from Academic Competency Centre) 05 Handout 1 *Property of STI  [email protected] Page 6 of 6