Reliability Management PDF
Document Details
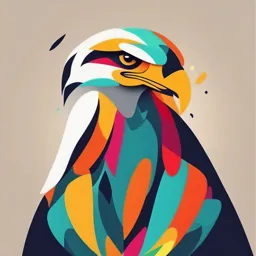
Uploaded by ValiantFantasy192
Kerala Public School Kadma
Hemant Urdhwareshe
Tags
Summary
This document is a CRE Reference Book about reliability management and leadership foundations. It covers various aspects of reliability engineering, including topics such as leadership foundations, reliability fundamentals, and supplier reliability assessments.
Full Transcript
CRE Reference Book Section I Reliability Management Presentation Developed by...
CRE Reference Book Section I Reliability Management Presentation Developed by Hemant Urdhwareshe ASQ Fellow, CMMBB, CRE, CSSBB, CMQ/OE, CQE Version February 2024 Version July 2024 1 Section 1 : Reliability Fundamentals A : Leadership Foundations B : Reliability Foundations 1. Benefits of reliability engineering 1. Basic Reliability Terminology 2. Interrelationship of safety, quality, and 2. Drivers of reliability requirements and targets reliability 3. Reliability Engineer Leadership 3. Corrective and Preventive Action Responsibilities 4. Reliability engineer role and 4. Root Cause Analysis responsibilities in product life cycle 5. Function of reliability in engineering 5. Product Life-cycle engineering stages 6. Ethics in reliability engineering 6. Economics of product maintainability and availability 7. Supplier reliability assessments 7. Cost of Poor Reliability 8. Performance Monitoring 8. Quality Triangle 9. Six Sigma Methodologies 10. Systems Engineering and Integration Copyright Institute of Quality and Reliability July-2024 CRE Reference Material 2 2 ©Institute of Quality and Reliability July-2024 1 CRE Reference Book Section 1 : Reliability Fundamentals Sub Section A : Leadership Foundations Topic 1A1 : Benefits of reliability engineering Describe the value that reliability has on achieving company goals and objectives, and how reliability engineering techniques and methods improve programs, processes, products, systems, and services. Understand Remember Evaluate Analyze Create Apply Maximum Cognitive Level : Copyright Institute of Quality and Reliability July-2024 CRE Reference Material 3 3 Benefits of reliability engineering Repeat Business. A concentrated effort towards improved reliability shows existing customers that a manufacturer is serious about their product, and committed to customer satisfaction. Customer Requirements. Many customers in today's market demand that their suppliers have an effective reliability programme. These customers have learned the benefits of reliability analysis from experience. Competitive Advantage. Many companies will publish their predicted reliability numbers to help gain an advantage over their competitors who either do not publish their numbers or have lower numbers. Copyright Institute of Quality and Reliability July-2024 CRE Reference Material 4 4 ©Institute of Quality and Reliability July-2024 2 CRE Reference Book Benefits of reliability engineering Reputation. A company's reputation is very closely related to the reliability of their products. Customer Satisfaction. While a reliable product may not dramatically affect customer satisfaction in a positive manner, an unreliable product will negatively affect customer satisfaction severely. Warranty Costs. If a product fails to perform its function within the warranty period, the replacement and repair costs will negatively affect profits, as well as gain unwanted negative attention. Introducing reliability analysis is an important step in taking corrective action, ultimately leading to a product that is more reliable. Copyright Institute of Quality and Reliability July-2024 CRE Reference Material 5 5 Few Case Histories Hewlett-Packard in one electronic measuring instrument through application of reliability engineering reduced service costs by 70% while reducing cost by 25% at the same time. Atlas Guidance System case: Following comparative data is self explanatory! “High” Reliability “Nominal” Program Reliability (Source Reliability Engineering Program Handbook by Dimitry Kececioglu) Development 59.3 50 Production 10.2 9.4 Maintenance 30.5 99 Total 100 158.4 Any inputs from the participants? Copyright Institute of Quality and Reliability July-2024 CRE Reference Material 6 6 ©Institute of Quality and Reliability July-2024 3 CRE Reference Book Section 1 : Reliability Fundamentals Sub Section A : Leadership Foundations Topic 1A2 : Interrelationship of safety, quality, and reliability Describe the relationship of and distinguish between reliability and quality, and describe the importance of safety in reliability engineering and how reliability impacts safety. Understand Remember Evaluate Analyze Create Apply Maximum Cognitive Level : Copyright Institute of Quality and Reliability July-2024 CRE Reference Material 7 7 Quality and Reliability Quality Reliability The totality of characteristics of a product (1) The duration or probability of failure or service that bear on its ability to satisfy free performance under stated stated or implied needs. conditions Other definitions of quality include: (2) The probability that an item can Fitness for use (Juran) perform its intended function for a Conformance to requirements (Crosby) specified interval under stated Loss to the society after a product is conditions shipped (Taguchi) Measures of quality include defect Reliability is measured as probability of levels such as parts per million (ppm) failure free performance. Sometimes, time when product is delivered to the is measured as Bx life by which x% parts customer will fail. For example, B10 life means that 10% parts will fail or 90% parts will survive. Examples of quality defects: Examples of reliability failures: Paint scratches, missing parts, a new part A computer hard disc failed after four not working, a new computer does not start months of purchase, compressor of a or hangs, a new mobile phone has a crack refrigerator failed after 15 months, a car had gear slippage problem after six months Copyright Institute of Quality and Reliability July-2024 CRE Reference Material 8 8 ©Institute of Quality and Reliability July-2024 4 CRE Reference Book Quality, Reliability and Safety Reliability can be considered as “Quality over time”. Customers frequently use the terms “quality” and “reliability”. We need to understand what they expect. Measurement of reliability is related to failure rates, number of failures, warranty cost etc.. Thus, reliability is experienced by the customers when they use the product. Quality Level is measured in terms of defect levels (such as ppm) when the product is received as new. Quality and reliability both can have significant impact on safety Copyright Institute of Quality and Reliability July-2024 CRE Reference Material 9 9 Quality, Reliability and Safety Quality defects and failures both can adversely affect safety of user, bystanders and equipment Some quality defects can lead to unreliable and/or unsafe product. Some examples of how unreliability can affect safety: – Failure of automobile steering system, brake system, axles etc. can result in serious accidents – Short circuit in electrical equipment can result in shock – Failure of safety valve in a pressure cooker, leakage of regulator of an LPG cylinder can result in an explosion – Poor reliability of a bridge can result in an accident and disaster However, all failures are not safety issues and all safety issues are not due to failures. Copyright Institute of Quality and Reliability July-2024 CRE Reference Material 10 10 ©Institute of Quality and Reliability July-2024 5 CRE Reference Book Section 1 : Reliability Fundamentals Sub Section A : Leadership Foundations Topic 1A3 : Reliability engineer leadership responsibilities Describe how to be a reliability champion by influencing program decisions and facilitating cross-functional communication. Understand Remember Evaluate Analyze Create Apply Maximum Cognitive Level : Copyright Institute of Quality and Reliability July-2024 CRE Reference Material 11 11 Reliability Engineer Leadership Responsibilities Reliability engineer (RE) plays important roles in product safety and liability Interestingly, he/she has to safeguard interests of the company and interests of the society and create a win-win situation The RE ensures compliance to the test and validation requirements so that the product is safe and functioning properly. The RE uses, trains others and emphasizes use of reliability tools such as FMEA, FMECA, HACCP, MIL standards etc. RE should ensure establishing and implementing an effective and closed loop Failure Reporting and Corrective Action System (FRACAS) so that there are no critical open issues when product is launched RE should be involved in establishing and assuring Design control mechanism so that activities such as design reviews, DFMEA, validation tests are carried out in accordance with the laid down procedures, standards Any gaps or anomalies must be brought to the notice of appropriate level of management so that the issues are resolved Copyright Institute of Quality and Reliability July-2024 CRE Reference Material 12 12 ©Institute of Quality and Reliability July-2024 6 CRE Reference Book Section 1 : Reliability Fundamentals Sub Section A : Leadership Foundations Topic 1A4 : Reliability engineer role and responsibilities in the product life cycle Describe how the reliability engineer influences the product life cycle, and describe a reliability engineer’s role in the design review process in order to anticipate how reliability can impact risk and costs, and ensure performance over time. Understand Remember Evaluate Analyze Create Apply Maximum Cognitive Level : Copyright Institute of Quality and Reliability July-2024 CRE Reference Material 13 13 Reliability functions in Design and Development Design and development process should integrate reliability aspect by using Design Evaluation methods including DFMEA, design reviews, reliability validation and demonstration tests, design optimization using Design of Experiments, Tolerance Analysis, Computer Aided Design (CAD) Using discovery testing such as Highly Accelerated Life Tests (HALT) is useful in identifying failure modes during design phase. These can be fixed to improve reliability and durability of products Strategy of test to failure is recommended by many experts as failure provides vital information for continuous improvement In most electronic products, it has been generally proven that in spite of good design and process controls, products tend to have early life failures. Thus screening methods such as burn-in, Environmental Stress Screening and Highly Accelerated Stress Screening (HASS) are deployed to minimize early life failures due to manufacturing defects and uncertainties Copyright Institute of Quality and Reliability July-2024 CRE Reference Material 14 14 ©Institute of Quality and Reliability July-2024 7 CRE Reference Book Design and Development Based on system reliability goals, reliability targets can be allocated for subsystems These can be used for subsystem evaluation and validation These targets are also useful to specify reliability and durability (end-of-life) targets to suppliers. The subsystem with higher failure rates can be prioritized for improvements. – Analysis of past field and in-house test data can be useful for this Use of Analytical Models and Reliability Predictions: For example, CAD, Finite Element Analysis, Physics of Failure (POF) Models, Part Count and Part Stress Analysis Models, Simulation studies can be useful. If predicted reliability does not match with goals, improvement actions will be required Copyright Institute of Quality and Reliability July-2024 CRE Reference Material 15 15 Role after the product is launched.. After the product is launched, the reliability engineer needs to monitor that the reliability goals are continually achieved. Analysis of field data should be performed using Weibull Analysis or appropriate statistical tool to estimate failure rates and warranty costs Any field failures must be quickly analyzed to identify root cause and correction/preventive action. For this, process of structured problem solving should be deployed. It is also necessary to monitor whether maintainability and availability goals are achieved. This should be done by calculating and monitoring mean time to restore (MTTR). Any unforeseen failures reported in field must be considered as early warning issues. Copyright Institute of Quality and Reliability July-2024 CRE Reference Material 16 16 ©Institute of Quality and Reliability July-2024 8 CRE Reference Book Roles throughout the Product Life Cycle An important aspect of reliability engineer’s role in product life cycle is to assess risks due to safety and liability The risks should be assessed during design reviews and DFMEA considering the following: Are there any product failure modes which could result in safety/liability implications? This could be done with functions responsible for safety. Are there any aspects or product which could cause safety/liability issues even if product has not failed? For example, accidently getting injured due to rotating machinery, hot pipes etc. Are there any possibilities of misusing the product which can result in safety/liability issues? For example, children or senior citizens using without knowledge etc. Is there any possibility of unsafe condition due to disposition of the product or materials? For example, disposition of batteries, oil; radiation etc. What is the impact of government regulation? This aspect is becoming more and more important. Copyright Institute of Quality and Reliability July-2024 CRE Reference Material 17 17 Section 1 : Reliability Fundamentals Sub Section A : Leadership Foundations Topic 1A5 : Function of reliability in Engineering Describe how reliability techniques can be used to apply best practices in engineering (e.g., measuring reliability early), how industry standards can impact reliability, and how reliability can inform the decision analysis process. Understand Remember Evaluate Analyze Create Apply Maximum Cognitive Level : Copyright Institute of Quality and Reliability July-2024 CRE Reference Material 18 18 ©Institute of Quality and Reliability July-2024 9 CRE Reference Book Role of the reliability function in Engineering Reliability experts say that about 60 to 70 percent of reliability depends on the design! Design and Engineering functions must therefore work with marketing, manufacturing, suppliers, service, Quality and all related functions to ensure that the product is reliable and meets all regulatory requirements Many of the tools and techniques used by designers are discussed in later sections. These include: – Design Failure Modes and Effects Analysis (FMEA); Robust Design, Design of experiments, Stress Strength Analysis, Tolerance analysis, Reliability Validation and testing, Simulation, Design for X, Reliability apportionment etc. Copyright Institute of Quality and Reliability July-2024 CRE Reference Material 19 19 Role of the reliability function in engineering Reliability engineering function is expected to determine product life and recommend improvements in reliability Reliability analysis can be used to improve product design – Derating, for example can be used to reduce stress on components and improve useful life – Redundancy can be used to improve reliability when individual components are unable to meet reliability targets Reliability data analysis is also useful in estimating warranty failures and costs more realistically. Reliability engineer is expected to predict or estimate useful life of the product and components before repairs or replacement. This can lead to gain in market share It is important to identify and mitigate risks due to liability issues Copyright Institute of Quality and Reliability July-2024 CRE Reference Material 20 20 ©Institute of Quality and Reliability July-2024 10 CRE Reference Book Section 1 : Reliability Fundamentals Sub Section A : Leadership Foundations Topic 1A6 : Ethics in reliability engineering Identify appropriate ethical behaviours for a reliability engineer in various situations. Understand Remember Evaluate Analyze Create Apply Maximum Cognitive Level : Copyright Institute of Quality and Reliability July-2024 CRE Reference Material 21 21 ASQ Code of Ethics Fundamental Principles ASQ requires its members and certification holders to conduct themselves ethically by: Being honest and impartial in serving the public, their employers, customers, and clients. Striving to increase the competence and prestige of the quality profession, and Using their knowledge and skill for the enhancement of human welfare. Copyright Institute of Quality and Reliability July-2024 CRE Reference Material 22 22 ©Institute of Quality and Reliability July-2024 11 CRE Reference Book ASQ Code of Ethics Members and certification holders are required to observe the tenets set forth below: Relations With the Public Article 1 – Hold paramount the safety, health, and welfare of the public in the performance of their professional duties. Relations With Employers, Customers, and Clients Article 2 – Perform services only in their areas of competence. Article 3 – Continue their professional development throughout their careers and provide opportunities for the professional and ethical development of others. Article 4 – Act in a professional manner in dealings with ASQ staff and each employer, customer or client. Article 5 – Act as faithful agents or trustees and avoid conflict of interest and the appearance of conflicts of interest. Relations With Peers Article 6 – Build their professional reputation on the merit of their services and not compete unfairly with others. Article 7 – Assure that credit for the work of others is given to those to whom it is due. Copyright Institute of Quality and Reliability July-2024 CRE Reference Material 23 23 Ethical Issues Ethics include relations with management, subordinates, other professionals, society, suppliers, government officials, A reliability engineer can face situations that could pose challenges to him/her For example, – management may pressurize him/her for concealing information that could put them in trouble – Government officials may ask for bribe for providing compliance reports – Suppliers may ask for favors in approving substandard parts It is essential that the reliability engineer follows ethical practices as per ASQ code of ethics and complying to the law of the land Copyright Institute of Quality and Reliability July-2024 CRE Reference Material 24 24 ©Institute of Quality and Reliability July-2024 12 CRE Reference Book Section 1 : Reliability Fundamentals Sub Section A : Leadership Foundations Topic 1A7 : Supplier reliability assessments Explain how supplier reliability impacts the overall reliability program and describe key reliability concepts that should be included in supplier reliability assessments. Understand Remember Evaluate Analyze Create Apply Maximum Cognitive Level : Copyright Institute of Quality and Reliability July-2024 CRE Reference Material 25 25 Supplier Reliability We are as good as the weakest link! Taking efforts to assure reliability of purchased products is equally important Most companies buy significant proportion of parts from suppliers due to strategic reasons and capabilities Thus it is essential to select good suppliers and work with them by clearly specify requirements and demanding reliable products Specifying reliability in terms of MTBF is not often adequate. Reliability distributions such as Weibull, normal, lognormal may be considered to measure risks or costs It is also necessary to integrate testing and validation of parts and subsystems from suppliers The testing should include validation of integrated system to evaluate reliability of total system – This is necessary as there is often interaction of various subsystems with each other. Thus testing of a subsystem in isolation is no guarantee that it will work as a system Copyright Institute of Quality and Reliability July-2024 CRE Reference Material 26 26 ©Institute of Quality and Reliability July-2024 13 CRE Reference Book Supplier Reliability When suppliers are responsible for design, sound practices of design and development must be implemented by the supplier Warranty agreements with design-responsible suppliers should be carefully evaluated to address aspects of responsibility for failure investigation, replacement, transportation, legal claims etc. For suppliers not responsible for design, warranty responsibility is with the parent company. Manufacturing process controls need to be adequate for the type of part/product supplied. Use of sound practices such SPC, FMEA, are useful. It is also necessary to assess stability of suppliers’ processes Reliability requirements need to be included in the supplier purchase orders and/or agreements Input for testing and validation should include any standards and/or regulatory requirements Sampling plans should be agreed with clear acceptance criteria. MIL-HDBK-781 provides fixed length and sequential sampling plans for reliability verification. Regular feedbacks of any problems/failures are necessary for continuous improvement Copyright Institute of Quality and Reliability July-2024 CRE Reference Material 27 27 Section 1 : Reliability Management Sub Section A : Strategic Management Topic 1A8 : Performance Monitoring Describe the importance of performance monitoring to ensure that product reliability or safety requirements continue to be met, and identify life-cycle points in which process and product reliability data are collected and evaluated. Understand Remember Evaluate Analyze Create Apply Maximum Cognitive Level : Copyright Institute of Quality and Reliability July-2024 CRE Reference Material 28 28 ©Institute of Quality and Reliability July-2024 14 CRE Reference Book Performance Monitoring Performance monitoring means measuring progress towards reliability, maintainability and safety (RMS) goals with reference to target Performance monitoring can be in terms of MTBF/MTTF, MTTR, Availability, cumulative failure rates, early warning, assessment of corrective actions taken and/or design changes made Performance monitoring also encompasses safety issues reported Monitoring could be done using stratification of data by product, by region, by user segments etc. – For example failure rates of cars in taxi and private owners Based on performance monitoring, feedback should be given to those responsible to take decisions to improve the situation Copyright Institute of Quality and Reliability July-2024 CRE Reference Material 29 29 Performance Monitoring (continued) Examples of RMS measures used in monitoring: – Repairs per thousand (RPT) till warranty – Mean time to repair (MTTR) for maintainability – Number of safety issues reported per thousand units Performance indicators must be based on objectives of particular projects based on customer requirements – Quality Function Deployment (QFD) can be used for this Benchmarking can be used to set objectives in order to gain or improve market share Customer satisfaction surveys and customer complaints database are important methods to monitor performance Copyright Institute of Quality and Reliability July-2024 CRE Reference Material 30 30 ©Institute of Quality and Reliability July-2024 15 CRE Reference Book Trend Analysis As discussed before, comparing trend analysis can be useful to evaluate effectiveness of action. In most consumer durable products, one has to wait until sufficient number of products cross warranty and also careful in interpretation of ‘live’ data where the products have not crossed particular time period. A quicker assessment can be done with Weibull analysis of incomplete data. Months after build JEP Automotive Failcodes: CHGS, CHSV, CHSE (valve spring guide, exh & intake valve guide seal) 1.5 3 Months after build RPH: Repairs per Hundred Units 6 Months after build 1.2 9 Months after build Cumulative RPH 12 Months after build 0.9 15 Months after build 0.6 0.3 0 6 96 96 6 6 6 7 97 97 7 7 7 8 98 98 8 8 8 N9 AR AY L9 P9 V9 N9 AR AY L9 P9 V9 N9 AR AY L9 P9 V9 JA M M JU SE NO JA M M JU SE NO JA M M JU SE NO Build Date Copyright Institute of Quality and Reliability July-2024 CRE Reference Material 31 31 Monitoring in Product Life Cycle Design and Test and Manufacturing Develop Evaluate and Service DFMEA Test data Warranty data Prediction analysis analysis Allocation Qualification Corrective/ Design reviews tests Preventive Parts selection ALT Action Derating HALT Durability Redundancy Fatigue tests improvement Block diagrams MEOST MTTR Tolerance analysis Growth models Availability Monte Carlo FRACAS Simulation PRST Copyright Institute of Quality and Reliability July-2024 CRE Reference Material 32 32 ©Institute of Quality and Reliability July-2024 16 CRE Reference Book Section 1 : Reliability Fundamentals Sub Section A : Reliability Foundations Topic 1B1 : Basic Reliability Terminology Explain basic terms related to reliability and the associated metrics (e.g., MTTF, MTBF, MTTR, service interval, maintainability, availability, failure rate, reliability, and bathtub curve). (Apply) Understand Remember Evaluate Analyze Create Apply Maximum Cognitive Level : Copyright Institute of Quality and Reliability July-2024 CRE Reference Material 33 33 What is Reliability? As per ASQ Glossary, Reliability is defined as: “The probability that a product, system, or service will perform its intended function adequately for a specified period of time or will operate in a defined environment without failure.” Note: Durability is a measure of useful Life (a special case of reliability). Copyright Institute of Quality and Reliability July-2024 CRE Reference Material 34 34 ©Institute of Quality and Reliability July-2024 17 CRE Reference Book Reliability: Empirical calculation Consider an example! A company has manufactured 5000 water pumps. Till the end of 6 months, 20 pumps have failed! What is the estimated reliability at six months? Since 20 pumps failed, 4980 pumps survived! Thus estimated reliability for six months is 4980/5000 or 0.996! Copyright Institute of Quality and Reliability July-2024 CRE Reference Material 35 35 Failure Failure: The inability of an item, product or service to perform required functions on demand due to one or more defects. (Source ASQ Glossary) Copyright Institute of Quality and Reliability July-2024 CRE Reference Material 36 36 ©Institute of Quality and Reliability July-2024 18 CRE Reference Book Failure MIL-STD-721 defines: Failure: The event, or ,inoperable state, in which any, item or part of an item does not perform as specified A critical failure or combination of failures, that prevents an item from performing a specified mission A dependent failure is caused by the failure of an associated item(s) Chargeable Failure is within the responsibility of a given organizational entity (applied to terms such as FAILURES, MAINTENACE TIME etc.) A relevant failure occurs during operational life of a product For the information of participants, MIL-Std-721 is cancelled without replacement but we are still retaining some definitions from it. Copyright Institute of Quality and Reliability July-2024 CRE Reference Material 37 37 Types of Systems There are 2 basic types of systems Repairable Non-repairable Copyright Institute of Quality and Reliability July-2024 CRE Reference Material 38 38 ©Institute of Quality and Reliability July-2024 19 CRE Reference Book Mean Time Between Failures (MTBF) MTBF is applicable for repairable systems Total Working Time MTBF 𝜽 = Total Number of failures 𝟏 Average Failure Rate 𝝀 = , 𝝀𝜽 = 𝟏 𝜽 Working Failed Working Failed Working Copyright Institute of Quality and Reliability July-2024 CRE Reference Material 39 39 MTBF Example 300 cars have accumulated 45000 hours. Total Working Time MTBF 𝜃 = Total Number of failures 10 failures are observed. What is the 1 Average Failure Rate 𝜆 = , 𝜆𝜃 = 1 MTBF? What is the failure rate? 𝜃 Car is a repairable system: Use MTBF MTBF = 45000/10 =4500 hours Average Failure rate =10/45000 = 0.00022 per hour Copyright Institute of Quality and Reliability July-2024 CRE Reference Material 40 40 ©Institute of Quality and Reliability July-2024 20 CRE Reference Book Mean Time To Failure (MTTF) For non-repairable systems, Mean Time to Failure is calculated as failed units are not repaired Total Test Time MTTF 𝜃 = Total Number of failures 1 Average Failure Rate 𝜆 = , 𝜆𝜃 = 1 𝜃 Copyright Institute of Quality and Reliability July-2024 CRE Reference Material 41 41 Reliability Measures Non-Repairable Systems 5 oil pumps were tested with failure hours of 45, 33, 62, 94 and 105. What is the MTTF and failure rate? pumps are non repairable in this case: use MTTF (45 + 33 + 62 + 94 + 105) MTTF 𝜽 = = 67.8 𝟓 𝟓 Failure rate 𝝀 = = 0.0147 (45 + 33 + 62 + 94 + 105) Note that MTTF is reciprocal of failure rate Question to participants: What will be the MTTF is two more pumps are tested till 120 hours each and test is stopped without failure of these two pumps? Copyright Institute of Quality and Reliability July-2024 CRE Reference Material 42 42 ©Institute of Quality and Reliability July-2024 21 CRE Reference Book Instantaneous Hazard Rate Instantaneous failure rate or hazard rate (t) at time t is the probability of failure per unit time given that item has survived till time t Consider an example of wiper motors: From a batch of 200 wiper motors, 196 are working satisfactorily till 20000 kilometers. In the next 1000 kilometers, 3 motors fail. What is the hazard rate at 20000 kilometers? 20000 Copyright Institute of Quality and Reliability July-2024 CRE Reference Material 43 43 Hazard Rate Example At 20000 kilometers, 196 motors are working. In the next 1000 kilometers, 3 motors fail. Thus, hazard rate per kilometer per unit will be: 3 1 𝜆 20000 = × = 0.000015 per kilometer 196 1000 Note: Often, h(t) is used in notation for hazard rate instead of 𝝀 𝐭. Also, most reliability literature refers hazard rate as failure rate. Copyright Institute of Quality and Reliability July-2024 CRE Reference Material 44 44 ©Institute of Quality and Reliability July-2024 22 CRE Reference Book Maintainability Maintainability is probability that a failed system will be repaired within a given time, once it has failed, when maintenance is performed by qualified personnel using specified procedure and resources. If we say there is a 98% probability that a vehicle is repaired within 8 hours, we can say that M(8)=0.98. Maintainability can be measured with Mean Time To Repair (MTTR). MTTR is average repair time and is given by Total Maintenance Down Time MTTR = Total Number of Maintenance Actions Copyright Institute of Quality and Reliability July-2024 CRE Reference Material 45 45 Maintainability Maintenance actions typically include: 1. Diagnosis time 2. Part procurement time 3. Teardown time 4. Reassemble or rebuild time 5. Verification time Copyright Institute of Quality and Reliability July-2024 CRE Reference Material 46 46 ©Institute of Quality and Reliability July-2024 23 CRE Reference Book Preventive Actions and MTBMA Preventive maintenance actions are often taken to minimize failures. It is customary to take preventive actions when the system is not in use, such as on holidays. However, this is not possible for systems with continuous processes such as Cement plants. A measure Mean Time Between Maintenance Actions (MTBMA) includes preventive as well as correction maintenance actions. Copyright Institute of Quality and Reliability July-2024 CRE Reference Material 47 47 Availability Availability can be considered as fraction of time that a system is usable. As per MIL-Std-721: Availability is a measure of the degree to which an item is in an operable and committable state at the start of a mission when the mission is called for at an unknown (random) time. (Item state at start of a mission includes the combined effects of the readiness-related system R & M parameters, but excludes mission time) Inherent or Steady State Availability AI A more general formula, MTBF 𝐀𝐈 = MTBF + MTTR 𝑨𝒗𝒆𝒓𝒂𝒈𝒆 𝑼𝒑𝒕𝒊𝒎𝒆 A= 𝑨𝒗𝒆𝒓𝒂𝒈𝒆 𝑼𝒑𝒕𝒊𝒎𝒆+𝑨𝒗𝒆𝒓𝒂𝒈𝒆 𝑫𝒐𝒘𝒏𝒕𝒊𝒎𝒆 Copyright Institute of Quality and Reliability July-2024 CRE Reference Material 48 48 ©Institute of Quality and Reliability July-2024 24 CRE Reference Book Service Interval Service Interval is the recommended time between routine checks and replacements such as lubrication, change of filter, interchanging tire positions on automobile, clutch adjustments, tappet settings etc. Do you know any examples of service intervals? Copyright Institute of Quality and Reliability July-2024 CRE Reference Material 49 49 The Bathtub Curve Instantaneous Hazard Rate Random Failures Time Copyright Institute of Quality and Reliability July-2024 CRE Reference Material 50 50 ©Institute of Quality and Reliability July-2024 25 CRE Reference Book The Bathtub Curve The decreasing hazard rate period is also called Burn-in Period, ‘Infant Mortality Period’, Debugging period and Break-in period – Failures in this period are predominantly due to manufacturing and assembly defects, design errors, welding flaws, cracks, material defects, contamination, poor quality control etc. In the constant hazard rate period, failures occur randomly due to environmental factors, human errors, random loads etc. In the wear-out period, failures occur due to fatigue, excessive wear, corrosion, aging, friction etc. Copyright Institute of Quality and Reliability July-2024 CRE Reference Material 51 51 Bathtub Curve: Summary Table Phase Failure rate Possible Causes Possible improvement actions Burn-in Decreasing Manufacturing Defects: Better QC, (DFR) Welding, soldering, assembly Acceptance testing, Burn-in errors, part defects, poor QC, testing, screening, Highly poor workmanship Accelerated Stress Screening Useful Life Constant (CFR) Environment, random loads, Excess strength, Human errors, ‘Acts of God’, redundancy, robust design chance events Wear Out Increasing (IFR) Fatigue, Corrosion, Aging, Derating, preventive Friction maintenance, parts replacement, better material, improved designs, technology, Copyright Institute of Quality and Reliability July-2024 CRE Reference Material 52 52 ©Institute of Quality and Reliability July-2024 26 CRE Reference Book Failure Rate over product life cycle “Instantaneous” Hazard Rate Early Life Failures End-of-Life Failures “Wear-out” Failures” Decreasing Increasing failure rate Constant failure rate failure rate “Useful Life” Time Copyright Institute of Quality and Reliability July-2024 CRE Reference Material 53 53 Section 1 : Reliability Fundamentals Sub Section A : Reliability Foundations Topic 1B2 : Drivers of reliability requirements and targets Describe how customer expectations and industry standards, safety, liability, and regulatory concerns drive reliability requirements. Understand Remember Evaluate Analyze Create Apply Maximum Cognitive Level : Copyright Institute of Quality and Reliability July-2024 CRE Reference Material 54 54 ©Institute of Quality and Reliability July-2024 27