Welding Inspection Technology PDF
Document Details
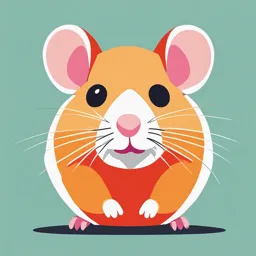
Uploaded by BestPerformingPlateau
Tags
Summary
This document discusses welding inspection technology, focusing on metal joining and cutting processes. It details shielded metal arc welding (SMAW) and gas metal arc welding (GMAW), including electrode classifications and characteristics, and describes the various types of welding processes in general.
Full Transcript
WELDING INSPECTION TECHNOLOGY CHAPTER 3—METAL JOINING AND CUTTING PROCESSES Since the electrode is such an important feature of the shielded metal arc welding process, it is necessary to understand how the various types are classified and identified. The American Welding Society has developed a sy...
WELDING INSPECTION TECHNOLOGY CHAPTER 3—METAL JOINING AND CUTTING PROCESSES Since the electrode is such an important feature of the shielded metal arc welding process, it is necessary to understand how the various types are classified and identified. The American Welding Society has developed a system for the identification of shielded metal arc welding electrodes. Figure 3.3 illustrates the various parts of this system. This illustration shows that the arc is created between the electrode and the workpiece due to the flow of electricity. This arc provides heat, or energy, to melt the base metal, filler metal and electrode coating. As the welding arc progresses to the right, it leaves behind solidified weld metal covered by a layer of converted flux, referred to as slag. This slag tends to float to the outside of the metal since it solidifies after the molten metal has solidified. In doing so, there is less likelihood that it will be trapped inside the weld resulting in a slag inclusion. American Welding Society Specifications A5.1 and A5.5 describe the requirements for carbon and low alloy steel electrodes, respectively. They describe the various classifications and characteristics of these electrodes. Another feature noted in Figure 3.2 is the presence of shielding gas which is produced when the electrode coating is heated and decomposed. These gases assist the flux in the shielding of the molten metal in the arc region. The identification consists of an “E,” which stands for electrode, followed by four or five digits. The first two, or three, numbers refer to the minimum tensile strength of the deposited weld metal. These numbers state the minimum tensile strength in thousands of pounds per square inch. For example, an E7018 means that the tensile strength of the deposited weld metal is at least 70 000 psi. while an E12018 means the tensile strength of the deposited weld metal is at least 120 000 psi. The primary element of the shielded metal arc welding process is the electrode itself. It is made up of a metal core wire covered with a layer of granular flux held in place by some type of bonding agent. All carbon and low alloy steel electrodes use essentially the same type of steel core wire, a low carbon, rimmed steel. Any alloying is provided from the coating, since it is more economical to achieve alloying in this way. The next number refers to the positions in which the electrode can be used. A “1” indicates the electrode is suitable for use in any position. A “2” means that the molten metal is so fluid that the electrode can only be used in the flat position for all welding types and in the horizontal position for fillet welds only. A “4” means the electrode is suitable for welding in a downhill progression. The number “3” is no longer used as a designation. The electrode coating when dry is a nonconductor of electricity. When an arc is struck the following happens; 1. Shielding—some of the coating decomposes to form a gaseous shield for the molten metal. The last number in the designation describes other characteristics which are determined by the composition of the coating present on the electrode. This coating will determine its operating characteristics and recommended electrical current: AC (alternating current), DCEP (direct current, electrode positive) or DCEN (direct current, electrode negative). Table 3.1 lists the significance of the last digit of the SMAW electrode identification system. 2. Deoxidation—the coating provides a fluxing action to remove impurities and oxygen and other atmospheric gases. 3. Alloying—the coating provides additional alloying elements for the weld deposit. 4. Ionizing—when the flux coating becomes molten it improves electrical characteristics to increase arc stability. 5. Insulating—the solidified slag provides an insulating blanket to slow down the weld metal cooling rate. The thickness of the slag will have an effect on the weld bead appearance. Heavier slag will produce beads that are smooth and have a good appearance. Thin slag will produce deposits that have rougher surfaces. Position The metal droplets are transferred across the arc by a magnetic pinch effect. As current is passed through a conductor a circular magnetic field is induced in the conductor. As it gets near the end of the electrode the magnetic field becomes concentrated and pinches off the droplets on the end of the electrode aiding in metal transfer. Strength Coating/Operating Characteristics Figure 3.3—SMAW Electrode Identification System 3-5 CHAPTER 3—METAL JOINING AND CUTTING PROCESSES WELDING INSPECTION TECHNOLOGY Table 3.1 Significance of Last Digit of SMAW Identification F-No. Classification F-3 F-3 F-2 F-2 F-2 F-4 F-4 F-4 F-1 F-1 F-1 F-1 EXX10 EXXX1 EXXX2 EXXX3 EXXX4 EXXX5 EXXX6 EXXX8 EXX20 EXX24 EXX27 EXX28 Current DCEP AC & DCEP AC & DCEN AC & DC AC & DC DCEP AC or DCEP AC or DCEP AC or DC AC or DC AC or DC AC or DCEP Arc Digging Digging Medium Light Light Medium Medium Medium Medium Light Medium Medium Penetration Deep Deep Medium Light Light Medium Medium Medium Medium Light Medium Medium Covering & Slag Iron Powder Cellulose-sodium Cellulose-potassium Rutile-sodium Rutile-potassium Rutile-iron powder Low hydrogen- sodium Low hydrogen-potassium Low hydrogen-iron powder Iron oxide-sodium Rutile-iron powder Iron oxide-iron powder Low hydrogen-iron powder 0%–10% 0% 0%–10% 0%–10% 25%–40% 0% 0% 25%–45% 0% 50% 50% 50% Note: Iron powder percentage is based on weight of the covering. It is important to note that those electrodes ending in “5,” “6,” or “8” are classified as “low hydrogen” types. To maintain this low hydrogen (moisture) content, they must be stored in their original factory-sealed metal container or an acceptable storage oven. This oven should be heated electrically and have a temperature control capability in the range of 150°F to 350°F. Since this device will assist in the maintenance of a low moisture content (less than 0.2%), it must be suitably vented. Any low hydrogen electrodes which are not to be used immediately should be placed into the holding oven as soon as their airtight container is opened. Most codes require that low hydrogen electrodes be held at a minimum oven temperature of 250°F [120°C] after removal from their sealed container. Table 3.2 Steel Alloy Suffixes for SMAW Electrodes Suffix A1 B1 B2 B3 B4 C1 C2 C3 D1 D2 G* W However, it is important to note that electrodes other than those mentioned above may be harmed if placed in the oven. Some electrode types are designed to have a certain moisture level. If this moisture is eliminated, the operating characteristics of the electrode will deteriorate significantly. Major Alloy Element(s) 0.5% Molybdenum 0.5% Molybdenum—0.5% Chromium 0.5% Molybdenum—1.25% Chromium 1.0% Molybdenum—2.25% Chromium 0.5% Molybdenum—2.0% Chromium 2.5% Nickel 3.5% Nickel 1.0% Nickel 0.3% Molybdenum—1.5% Manganese 0.3% Molybdenum—1.75% Manganese 0.2% Molybdenum; 0.3% Chromium; 0.5% Nickel; 1.0% Manganese; 0.1% Vanadium Weathering Steel *Need to have minimum content of one element only. metal are melted by the heat produced from the welding arc created between the end of the electrode and the workpiece when they are brought close together. Those SMAW electrodes used for joining low alloy steels may also have an alpha-numeric suffix which is added to the standard designation after a hyphen. Table 3.2 shows the significance of these designations. The power source for shielded metal arc welding is referred to as a constant current power source, having a “drooping” characteristic. This terminology can be more easily understood by looking at the characteristic voltampere (V-A) curve for this type of power source. The equipment for shielded metal arc welding is relatively simple. A transformer-rectifier is shown in Figure 3.4, and an inverter power supply is shown in Figure 3.5. One lead from the welding power source is connected to the piece to be welded and the opposite lead goes to the electrode holder into which the welder places the welding electrode to be consumed. The electrode and base As a welder increases arc length, the resistance in the welding circuit increases due to the larger gap the current must cross. As can be seen in the typical volt-amp curve in Figure 3.6, this increase in resistance causes a slight 3-6 WELDING INSPECTION TECHNOLOGY CHAPTER 3—METAL JOINING AND CUTTING PROCESSES Figure 3.4—Shielded Metal Arc Transformer-Rectifier Figure 3.5—Shielded Metal Arc Inverter Power Supply decrease (10%) in the current flow across the arc gap. This decrease in current results in a significant increase in voltage (32%) supplied by the power source, which limits the drop in current. Since heat is a function of voltage, amperage, and time, it can be readily seen that a long arc length (32 volts × 135 amps × 60)/10 ipm = 25 920 J/in) will result in more heat produced than a short arc length (22 volts × 150 amps × 60)/10 ipm = 19 800 J/in). This is significant from a process control standpoint, because the welder can increase or decrease the fluidity of the weld pool simply by changing the arc length. However, an extremely long arc length will cause a loss of heat in the weld pool due to loss of arc concentration. An excessively long arc length will also result in a loss of arc stability and weld pool shielding gases. Voltage Change 32% Shielded metal arc welding is used in most industries for numerous applications. It is used for most materials except for some of the more exotic alloys. Even though it is a relatively old method and newer processes have replaced it in some applications, shielded metal arc welding remains as a popular process which will continue to be in great use by the welding industry. There are several reasons why the process continues to be so popular. First, the equipment is relatively simple and inexpensive. This helps to make the process quite Figure 3.6—Volt-Ampere Curve for Constant Current Power Source 3-7 CHAPTER 3—METAL JOINING AND CUTTING PROCESSES WELDING INSPECTION TECHNOLOGY a series of concentric circles surrounding the conductor, as shown in Figure 3.7. portable. In fact, there are numerous gasoline or diesel engine-driven types which don’t rely on electrical input; thus, shielded metal arc welding can be accomplished in remote locations. Also, some of the newer solid state power sources are so small and lightweight that the welder can easily carry them to the work. And, due to the availability of numerous types of electrodes, the process is considered quite versatile. Finally, with the improved equipment and electrodes available today, the resulting weld quality can be consistently high. This magnetic field is strongest when contained entirely within a magnetically permeable material and resists having to travel through the air outside this magnetically permeable material. Consequently, when welding a magnetically permeable material, such as steel, the field can become distorted when the arc approaches the edge of a plate, the end of a weld, or some abrupt change in contour of the part being welded. This is shown in Figure 3.8. One of the limitations of shielded metal arc welding is its speed. The speed is primarily hampered by the fact that the welder must periodically stop welding and replace the consumed electrode with a new one, since they are typically only 9 in to 18 in in length. SMAW has been replaced by other semiautomatic, mechanized and automatic processes in many applications simply because they offer increased productivity when compared to manual shielded metal arc welding. To reduce the effects of arc blow, several alternatives can be tried. They include: 1. Change from DC to AC. 2. Hold as short an arc as possible. 3. Reduce welding current. 4. Angle the electrode in the direction opposite the arc blow. Another disadvantage, which also affects productivity, is the fact that following welding, there is a layer of solidified slag which must be removed. A further limitation, when low hydrogen type electrodes are used, is that they require storage in an appropriate electrode holding oven which will maintain their low moisture levels. 5. Use heavy tack welds at either end of a joint, with intermittent tack welds along the length of the joint. 6. Weld toward a heavy tack or toward a completed weld. Now that some of the basic principles have been presented, it is appropriate to discuss some of the discontinuities which may result during the shielded metal arc process. While these are not the only discontinuities we can expect, they may result because of the misapplication of this particular process. 7. Use a backstep technique. 8. Weld away from the work connection to reduce back blow; weld toward the work connection to reduce forward blow. One potential problem is the presence of porosity in the finished weld. When porosity is encountered, it is normally the result of the presence of moisture or contamination in the weld region. It could be present in the electrode coating, on the surface of the material, or come from the atmosphere surrounding the welding operation. Porosity can also occur when the welder is using an arc length which is too long. This problem of “long arcing” is especially likely when using low hydrogen electrodes. So, the preferred shorter arc length will aid in the elimination of porosity in the weld metal. Direction of flux Porosity can also result from the presence of a phenomenon referred to as arc blow. While this can occur with any arc welding process, it will be discussed here since it is a common problem which plagues the manual welder. Direction of current To understand arc blow, one must first understand that there is a magnetic field developed whenever an electric current is passed through a conductor. This magnetic field is developed in a direction perpendicular to the direction of the electric current, so it can be visualized as Figure 3.7—Magnetic Field Around Electric Conductor 3-8 WELDING INSPECTION TECHNOLOGY CHAPTER 3—METAL JOINING AND CUTTING PROCESSES Electrode Travel Forward blow Back blow Figure 3.8—Distorted Magnetic Fields at Ends of Welds applications. Gas metal arc welding is characterized by a solid wire electrode which is fed continuously through a welding gun. An arc is created between this wire and the workpiece to heat and melt the base and filler materials. Once molten, the wire becomes deposited in the weld joint. Figure 3.9 depicts the essential elements of the process. 9. Attach the work cable to both ends of the joint to be welded. 10. Wrap work cable around the workpiece and pass work current through it in such a direction that the magnetic field set up will tend to neutralize the magnetic field causing the arc blow. 11. Extend the end of the joint by attaching runoff plates. An important feature for GMAW is that all of the shielding for welding is provided by a protective gas atmosphere which is also emitted from the welding gun from some external source. Gases used include both inert and reactive types. Inert gases such as argon and helium are used for some applications. They can be applied singly, or in combination with each other, or mixed with reactive gases such as oxygen or carbon dioxide. Many gas metal arc welding applications use carbon dioxide shielding alone, because of its relatively low cost compared to inert gases. In addition to porosity, arc blow can also cause spatter, undercut, improper weld contour, and decreased penetration. Slag inclusions can also occur with SMAW simply because it relies on a flux system for weld protection. With any process incorporating a flux, the possibility of trapping slag within the weld deposit is a definite concern. The welder can reduce this tendency by using techniques which allow the molten slag to flow freely to the surface of the metal. Thorough cleaning of the slag from each weld pass prior to deposition of additional passes will also reduce the occurrence of slag inclusions in multipass welds. The electrodes used for this process are solid wires which are supplied on spools or reels of various sizes. As is the case for shielded metal arc welding electrodes, there is an approved American Welding Society identification system for gas metal arc welding electrodes. They are denoted by the letters “ER,” followed by two or three numbers, the letter “S,” a hyphen, and finally, another number, as shown in Figure 3.10. Since shielded metal arc welding is primarily accomplished manually, numerous discontinuities can result from improper manipulation of the electrode. Some of these are incomplete fusion, incomplete joint penetration, cracking, undercut, overlap, incorrect weld size, and improper weld profile. “ER” designates the wire as being an electrode and a rod, meaning that it may conduct electricity (electrode), or simply be applied as a filler metal (rod) when used with other welding processes. The next two or three numbers state the minimum tensile strength of the deposited weld metal in thousands of pounds per square inch. So, like the SMAW types, an ER70S-6 denotes a filler metal whose tensile strength is at least 70 000 psi. An ER120S6 denotes a filler metal whose tensile strength is at least 120 000 psi The letter “S” stands for a solid wire. Gas Metal Arc Welding (GMAW) The next process to be discussed is gas metal arc welding, GMAW. While gas metal arc welding is the AWS designation for the process, we also hear it commonly referred to as “MIG” welding. It is most commonly employed as a semiautomatic process; however, it is also used in mechanized and automatic applications as well. Therefore, it is very well-suited for robotic welding 3-9 CHAPTER 3—METAL JOINING AND CUTTING PROCESSES WELDING INSPECTION TECHNOLOGY SHIELDING GAS IN DIRECTION OF TRAVEL SOLID ELECTRODE WIRE CURRENT CONDUCTOR WIRE GUIDE AND CONTACT TUBE GAS NOZZLE CONSUMABLE ELECTRODE ARC GASEOUS SHIELD BASE METAL WELD METAL Figure 3.9—Gas Metal Arc Welding, Including Schematic of Details Electrode Rod Even when a spool of wire is in place on the wire feeder, it should be covered with a protective covering when not used for prolonged periods of time. Chemical Composition Strength The power supply used for gas metal arc welding is quite different from the type employed for shielded metal arc welding. Instead of a constant current type, gas metal arc welding uses what is referred to as a constant voltage, or constant potential, power source. That is, welding is accomplished using a preset value of voltage over the range of welding currents. Solid Wire Figure 3.10—GMAW Electrode Identification System Gas metal arc welding is normally accomplished using direct current, electrode positive (DCEP). When this type of power source is combined with a wire feeder, the result is a welding process which can be semiautomatic, mechanized or fully automatic. Figure 3.11 shows a typical gas metal arc welding setup. Finally, the number after the hyphen refers to the particular chemical composition of the electrode. This will dictate both its operating characteristics as well as what properties are to be expected from the deposited weld. Gas metal arc electrodes typically have increased amounts of deoxidizers such as manganese, silicon, and aluminum to help avoid the formation of porosity. As can be seen, the equipment is a bit more complex than that used for shielded metal arc welding. A complete setup includes a power source, wire feeder, gas source, and welding gun attached to the wire feeder by a flexible cable through which the electrode and gas travel. To set up for welding, the welder will adjust the voltage at the power source and the wire feed speed at the wire feeder. As the wire feed speed is increased, the welding current increases as well. The melt-off rate of the electrode is proportional to the arc current, so the wire feed speed actually controls this feature as well. Even though the wire doesn’t have a flux coating, it is still important to store the material properly when not in use. The most critical factor here is that the wire must be kept clean. If allowed to remain out in the open, it may become contaminated with rust, oil, moisture, grinding dust or other materials present in a weld shop environment. So, when not being used, the wire should be kept in its original plastic wrapping and/or shipping container. It was mentioned that this power source is a constant potential type; however, a look at a typical V-A curve, 3-10 WELDING INSPECTION TECHNOLOGY CHAPTER 3—METAL JOINING AND CUTTING PROCESSES When the machine adjustments are changed, the result is the operating characteristics will be drastically altered. Of primary concern is the manner in which the molten metal is transferred from the end of the electrode, across the arc region, to the base metal. With gas metal arc welding, there are four basic modes of metal transfer. They are spray, globular, pulsed arc (see Figure 3.13), and short circuiting. Figure 3.14 shows three of the four modes. Their characteristics are so different that it’s almost as if there are four separate welding processes. Each specific type has definite advantages and limitations which make it better for some applications than others. The type of metal transfer depends upon several factors, including shielding gas, current and voltage levels, and power source characteristics. One of the basic ways in which these four types differ is that they provide varying amounts of heat to the workpiece. Spray transfer is considered to be the hottest, followed by pulsed arc, globular, and finally short circuiting. Therefore, spray transfer is the best for heavier sections and full penetration weld joints, as long as they can be positioned in the flat position. Globular transfer provides almost as much heating and weld metal deposition, but its operating characteristics tend to be less stable, resulting in increased spatter. Figure 3.11—Gas Metal Arc Welding Equipment Pulsed arc gas metal arc welding requires a welding power source capable of producing a pulsing direct current output which allows the welder to program the exact combination of high and low currents for improved heat control and process flexibility. The welder can set both the amount and duration of the high current pulse. So during operation, the current alternates between a high pulse current and a lower pulse current, both of which can be set with machine controls. Figure 3.12, will show that the line is not flat but actually has a slight slope. This feature allows the process to function as a semiautomatic type, meaning that the welder does not have to control the feeding of the filler metal as was the case for manual shielded metal arc welding. Another way to describe this system is to call it a “Self-Regulating Constant Potential” system. Short circuiting transfer results in the least amount of heating to the base metal, making it an excellent choice for welding of sheet metal and joints having excessive gaps due to poor fit up. The short circuiting transfer method is characteristically colder due to the electrode actually coming in contact with the base metal, creating a short circuit for a portion of the welding cycle. So, the arc is intermittently operating and extinguishing. The brief periods of arc extinction allow for some cooling to occur to aid in reducing the tendency of burning through thin materials. Care must be taken when short circuiting transfer is used for heavier section welding, since incomplete fusion can result from insufficient heating of the base metal. This is accomplished because a minor change in the guns’ position with respect to the workpiece will result in a substantial increase or decrease in the arc current. Looking at Figure 3.12, it can be seen that moving the gun closer to the workpiece will reduce the electrical resistance and produce an instantaneous increase in current. This, in turn, instantaneously burns off the additional electrode to bring the arc length and current back to their original values. This reduces the effect of the operator’s manipulation on the welding characteristics, making the process less operator-sensitive and therefore easier to learn the manipulative aspects. As mentioned, the shielding gases have a significant effect on the type of metal transfer. Spray transfer can be 3-11 VOLTAGE, V CHAPTER 3—METAL JOINING AND CUTTING PROCESSES 40 35 30 25 20 15 10 5 0 WELDING INSPECTION TECHNOLOGY A (25 V @ 100 A) B (20 V @ 200 A) C (15 V @ 300 A) 0 50 100 150 200 250 300 350 CURRENT, A Decrease in V = Increase in A Figure 3.12—Typical Constant Potential V-A Curve that consists of a metal sheath and a core of various powered materials, primarily iron. The core of metal cored wire contributes almost entirely to the deposited weld metal. The current in metal cored wires is concentrated on the outside sheet, the metal powders inside are less conductive because of the granular nature. Focusing current on the wires’ outer diameter creates a broader, bowl shaped arc cone. It also can create finer molten droplets and a less turbulent weld pool Some of the advantages of metal cored wires are: high deposition rates, no slag and almost no spatter, ability to bridge gaps without burn through, and excellent side wall fusion and root penetration An E70C-6M is a typical metal cored wire designation. E stand for electrode. The next two digits indicate that the tensile strength of the weld deposit is at least 70 000 psi. C stands for Composite Metal Cored Electrode. The 6 is the category for the wire and the M means mixed gas The versatility offered by this process has resulted in its use in many industrial applications. GMAW can be effectively used to join or overlay many types of ferrous and nonferrous metals. The use of gas shielding, instead of a flux which can become contaminated, can reduce the possibility of introducing hydrogen into the weld zone, so GMAW can be used successfully in situations where the presence of hydrogen could cause problems. Figure 3.13—Pulse Arc Transfer achieved only when there is at least 80% argon present in the gas mixture. Ar-CO2 is probably the most popular gas for GMAW of carbon steel. Due to the lack of a slag coating which must be removed after welding, GMAW is well suited for automatic and robotic welding or other high production situations. This is one of the major advantages of the process. Since there is little or no cleaning required following welding, the Joining the GMAW family of filler metals are metal cored electrodes. Metal cored wire is a tubular electrode 3-12