Equipment Lockout Procedure PDF
Document Details
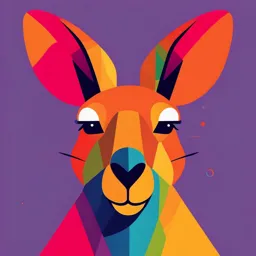
Uploaded by Reusl
Tags
Summary
This document outlines equipment lockout procedures for industrial settings, emphasizing the importance of safety precautions. It covers the use of lockout devices to isolate hazardous energy sources before maintenance work. The document provides a comprehensive overview of the subject.
Full Transcript
Safety Management Systems • Chapter 14 OBJECTIVE 5 ^ ll®l®i5^^^^S^^ --^~^l-.'~^^,-i].;.;-t'.-ir(~,'-.; ••-•;*,'--^.-a--q--l:,-^'-T-y--.1-'-^^- ;'..;-,.,- •• i,.~^ ;'-?'',-*).'',-i^-^.'r-i'-'-;;-ty:-.'.>i'',T,,-.,,^v'I ^i^islafn^l^^pos<^^i^ij^^ ^i^pi<^l^ui^^lg6Kc^i^^ ^^^^S^'.S&^S'f^^^ EQUIPMENT...
Safety Management Systems • Chapter 14 OBJECTIVE 5 ^ ll®l®i5^^^^S^^ --^~^l-.'~^^,-i].;.;-t'.-ir(~,'-.; ••-•;*,'--^.-a--q--l:,-^'-T-y--.1-'-^^- ;'..;-,.,- •• i,.~^ ;'-?'',-*).'',-i^-^.'r-i'-'-;;-ty:-.'.>i'',T,,-.,,^v'I ^i^islafn^l^^pos<^^i^ij^^ ^i^pi<^l^ui^^lg6Kc^i^^ ^^^^S^'.S&^S'f^^^ EQUIPMENT LOCKOUT Note: The following is taken, in large part, from the B.C. OH&S Regulations. It is presented as an example only and should not be construed as being exact or applicable to all jurisdictions. Nor should the wording be accepted as the exact wording in the BC OH&S Regulations. Lockout is a system of locks, which secures devices that control hazardous energy from release. Control devices, which are secured by locks, include main disconnect switches, circuit breakers, valves and clutches. General Requirement If the unexpected energizing or startup of machinery or equipment or the unexpected release of an energy source could cause injmy, the energy source must be isolated and effectively controlled. Hazardous Energy is any energy source (electric, compressed gas, steam, hydraulic energy or moving part) or any elevated object, which could release or move and injure a worker. Lookout is required when machinery or equipment is shut down for maintenance; no work may be done until the following conditions have been met: • AH parts and attachments have been secured against madvertent movement. • Where the work will expose workers to energy sources, the hazard has been effectively controlled. • The energy isolating devices have been locked out. Machinery or equipment is in use for normal production work, and a work activity creates a risk of injury to workers from the movement of the machinery or equipment, or exposure to an energy source, and the machinery or equipment is not effectively safeguarded to protect the workers from the risk. Lookout Procedures When lookout of energy isolating devices is required, the devices must be secured in the safe position using locks in accordance with procedures that are made available to aU workers who are required to work on the machinery or equipment. The employer must ensure that each worker required to lock out has ready access to sufficient personal locks to implement the required lockout procedure. Personal locks are locks assigned to a person. Only that person has the keys for that lock. Combination locks must not be used for lookout. Each personal lock must be marked or tagged to identify the person applying it. Provision must be implemented for shift or personnel changes, including the orderly transfer of conb-ol of locked out energy isolating devices between outgoing and incomtng workers. If the use of a personal lock is not practical for lookout, another effective means, if approved by the board, may be used in place of a personal lock to secure an energy-isolatmg device in the safe position. 3rd Class Edition 2.5 - Part A2 ?5> Chapter 14 • Safety Management Systems Access to Energy Isolating Devices When an energy-isolating device is locked out, the lock must not prevent access to other energy isolating devices supplying machinery or equipment that could cause injury to workers. For example, if one valve is locked closed with a chain or cable arrangement it cannot interfere with the movement of adjacent valves. Checking Locked Out Equipment Effective means of verifying lookout must be provided and used. Before commencing work, a worker must verify that aU energy sources have been effectively locked out. For example, a motor start button may be pushed to verify the power has been shut off. Bleed valves may be opened to verify lack of pressure in piping. Worker Responsibilities Each worker who works on machinery or equipment requiring lockout is responsible for: • Locking out the energy isolating devices before starting work, except as provided in Group Lookout Procedures • Removing personal locks on the completion of his or her work • Matntaming immediate control of the key(s) to personal locks throughout the duration of the work Removal of Locks A personal lock must only be removed by the worker who installed it. If this is not possible, the matter must be referred to the supervisor or manager in charge, who will be responsible for its removal. The supervisor or manager in charge must: • Make every reasonable effort to contact the worker who installed the lock • Ensure that the machinery or equipment can be operated safely before, removing the lock; the worker must be notified at the start of his or her next shift if the worker's personal locks have been removed since the worker's previous shift Group Lookout Procedures If a large number of workers are working on machinery or equipment or a large number of energy isolating devices must be locked out, a group lockout procedure that meets the requirements may be used. Lock out procedures vary from one plant to another. The worker must know and understand the lookout procedure at the plant where he or she is employed, and must foUow that procedure to the letter. Violation of lock out procedures is serious and can result in disciplinary action. LOCKOUT DEVICES Lockout devices, are devices that will isolate the source of danger from the worker. Locks are attached to control devices, or to a lock box location, which wUl effectively keep any person from operating the equipment, or exposing the source of danger, until the locks have been removed. Valves must be dosed and locked in the closed position by using chains, or specially constructed lookout devices designed to keep that particular type of valve from being opened before the lock is removed. For example, special lock out devices are made for ball valves and gate valves. Lock out hasps or cleats are designed for electrical circuit breakers, switches and electrical (plug) type cords. 3rd Class Edition 2.5 • Part A2 Safety Management Systems • Chapter 14 TYPICAL LOCKOUT PROCEDURE Jl When repacking a centrifugal pump, driven by an electric motor, the following lockout procedure could be used: • Shut down the pump according to operating procedures • Close the suction and discharge valves • Lock both valves in the closed position • Open the dram valve between suction and discharge valves and the pump. This wiU drain off any fluid pressure at the pump. Confirm, there is no pressure in the pump. • Open the electrical breaker and lock m the open position (some sites require the electrician to perform this procedure. In this case, the electrician and the worker must both put a personal lock on the hasp or cleat) • Confirm the lock out by trying to start the pump, using the start/stop switch. The pump should not start, since there should be no electrical power to the pump motor • Confirm the pump is safe, then complete and issue the work permit. 3rd C/ass Edition 2.5 • Part A2