Control Valves PDF
Document Details
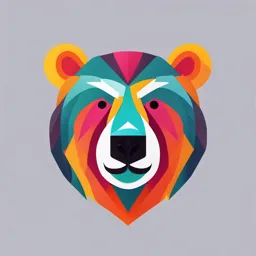
Uploaded by GoodDwarf
Northwestern University in Qatar
Tags
Summary
This document describes control valves, their types, parts, and functions. It covers different types of actuators, such as diaphragm actuators, and various valve actions like air-to-open (AO) and air-to-close (AC).
Full Transcript
Control Valves What are VALVES? Mechanical devices designed to direct, stop, mix or regulate the flow, pressure or temperature of a process fluid. Kinds of VALVES: On-off valves, Throttling valves, One way valves & Safety valves Control Valves There are many different ways to manipulate the fl...
Control Valves What are VALVES? Mechanical devices designed to direct, stop, mix or regulate the flow, pressure or temperature of a process fluid. Kinds of VALVES: On-off valves, Throttling valves, One way valves & Safety valves Control Valves There are many different ways to manipulate the flows of material and energy into and out of a process; for example, the speed of a pump drive, screw conveyer, or blower can be adjusted. However, a simple and widely used method of accomplishing this result with fluids is to use a control valve, also called an automatic control valve. Control Valves Control Valves are used commonly for: Level control Pressure control Temperature control Flow control Control Valves require an output signal from the controller to move https://www.youtube.com/watch?v=KtsiM1st0KA https://www.youtube.com/watch?v=qLSl9ZGIl0A https://www.youtube.com/watch?v=XDyTPlkwKak https://www.youtube.com/watch?v=hXfYiQ0zy84 Control Valve Parts The control valve Actuator Diaphragm Actuator components include the valve body, trim, seat, and actuator. Instrument Air Supply Signal from Controller Positioner Valve Body Valve Parts Valve Body In Guide Bushings In Grey Green The valve components include the valve body, seat, disk, and stem. Valve Stem in Silver/Chrome Valve trim which are the internals of the valve consists of the: disk, seat ring, valve stem and guide Valve Disk in Orange bushings Valve Seat in Blue Valve Position Indicator An indicator is the part of the valve that will show what position the valve physically is in. It is a local indication only and lets the field operator know where it is operating. Especially helpful when stroking a valve Valve Body Action Applied Force Directly Applied Force will have a reverse Action and cause the valve to Open Closes the valve Direct Acting refers to the force that is applied to the valve in a Applied Force downwards direction that will cause the valve to close. Valve Closes Valve Opens Reverse Acting refers to the force that is applied to the valve in a downwards direction will cause the valve to open. Control Valve Actuator A control valve will receive a signal (typically pneumatic) from the controller to position it. (3Psi to 15Psi, or 20 kPa to 100 kPa) When the air signal is applied to one side or the other side of the diaphragm a force is generated that will cause the valve to move downwards or upwards Diaphragm Actuator Positions the valve according the output signal from the controller. Must be able to overcome any forces acting on the valve to allow the actuator to position the valve. Control Valve Actuator The actuator will move the valve when an air signal is applied to the diaphragm. When the spring is used to keep the valve closed and the applied air signal is used to open the valve. This type of valve is called an Air to Open (AO) When the spring is used to keep the valve open and the applied air signal is used to close the valve. This type of valve is called an Air to Close (AC) Control Valve Actuator Air-to-Open Control Valves Air-to-Close Control Valves Normally, the choice of A-O or A-C valve is based on safety considerations. 2 Control Valve Actuators In any control system there is a risk that the supply for the signal maybe lost. In the event that the signal is lost valves that will ‘Fail Open’ (FO) or ‘Fail Close’ (FC) at the loss of the supply signal. Meaning when the air is removed the spring will force the valve to one position or the other. The idea is that if this situation were to occur the valve would fail in its safest position. Control Valve Actuators In a gas plant lets assume the loss of the instrument air supply. This would create an unsafe uncontrolled situation because there is no control signal available. The safest strategy is to make sure the plant is isolated and will depressure. Therefore FO or FC valves will be strategically selected at specific points in the system such as: A FC valve would be used in the inlet to the gas plant that will close to prevent more gasses from entering the plant. A FO valve would be selected that would open to depressure the plant to the flare. Fail-Open, Fail-Closed Action Due to its design using a spring the No Air valve will have a natural position. It is a built in is safety feature When the air is removed the spring No Air will force the valve into its natural position. In the valves pictured here when the air is removed the valves will Fail to the closed position This is an important consideration in the design of process safety Fail-Open, Fail-Closed Action In this picture are two valves No Air that use instrument air to close. If there was a loss on instrument No Air air the spring would push the valves open. We will call this Fail Open valves. Meaning is we have a failure they will stay open Example: Pneumatic control valves are to be specified for the applications listed below. State whether an A-O or A-C valve should be used for the following manipulated variables and give reason(s). A-O, which means FC A-O, which means FC A-O, which means FC A-C, which means FO Air to Open Valve Spring Force Pushes Downwards Air Pressure Pushes Upwards When the Air Pressure is greater the valve moves upwards Result Valve Opens Signal from Controller A pneumatic control valve (air-to-open) Pneumatically operated control valve https://www.youtube.com/watch?v=hXfYiQ0zy84 A control valve in a Process Unit Electric actuator on a control valve positioner Hydraulic actuator on a control valve positioner Control Valve with positioners SELECTING A VALVE TYPE Valve types are used to describe the mechanical characteristics and geometry (Ex/ gate, ball, globe valves). The valve characteristics is the relationship of the change in valve opening to the change in f low through the valve. Control Valve Characteristics Selecting a control valve, some rules of thumb: Equal Percentage: Equal increments of valve travel produce an equal percentage in f low change Used in processes where large changes in pressure drop are expected Used in processes where a small percentage of the total pressure drop is permitted by the valve Used in temperature and pressure control loops Control Valve Characteristics Selecting a control valve, some rules of thumb: Linear: Valve travel is directly proportional to the valve stroke Used in liquid level or f low loops Used in systems where the pressure drop across the valve is expected to remain fairly constant (ie. steady state systems) Control Valve Characteristics Selecting a control valve, some rules of thumb: Quick Opening: large increase in f low with a small change in valve stroke Used for frequent on-off service Used for processes where "instantly" large f low is needed (ie. safety systems or cooling water systems) Types of control valve Gate Valves Best Suited Control: Quick Opening Recommended Uses: 1. Fully open/closed, non-throttling 2. Infrequent operation 3. Minimal f luid trapping in line Applications: Oil, gas, air, slurries, heavy liquids, steam, noncondensing gases, and corrosive liquids Advantages: Disadvantages: 1. High capacity 1. Poor control 2. Tight shutoff 2. Cavitate at low pressure drops 3. Low cost 3. Cannot be used for throttling Types of control valve Globe Valves Best Suited Control: Linear and Equal percentage Recommended Uses: 1. Throttling service/f low regulation 2. Frequent operation Applications: Liquids, vapors, gases, corrosive substances, slurries Advantages: Disadvantages: 1. Efficient throttling 1. High pressure drop 2. Accurate f low control 2. More expensive than other valves 3. Available in multiple ports Types of control valve Ball Valves Best Suited Control: Quick opening, linear Recommended Uses: 1. Fully open/closed, limited-throttling 2. Higher temperature f luids Valve Ball Applications: Most liquids, high temperatures, slurries Advantages: Disadvantages: Valve Body 1. Low cost 1. Poor throttling characteristics 2. High capacity. 2. Prone to cavitation 3. Low leakage and maintenance. 4. Tight sealing with low torque Types of control valve Butterfly Valves Best Suited Control: Linear, Equal percentage Butterfly Recommended Uses: 1. Fully open/closed or throttling services 2. Frequent operation Valve Body 3. Minimal f luid trapping in line Applications: Liquids, gases, slurries, liquids with suspended solids Advantages: Disadvantages: 1. Low cost and maintenance. 1. High torque required for control 2. High capacity 2. Prone to cavitation at lower f lows 3. Good f low control 4. Low pressure drop Butterfly Valve for Control Actuator Valve Body Butterfly Check Valves Check valves allows flow in only one direction Two most common designs are the swing check and the lift check Swing check; the disk swings around a pivot point when the flow goes in one direction. When the flow reverses the valve closes In a lift check the flow will lift the disk upwards and when the flow reverses will push the disk closed Check valve Swing Check Lift Check Disk Pivot Direction of Flow There are many types of valves available, each having their advantages and limitations. The basic requirements and selection depend on their ability to perform specific functions such as: 1. Ability to throttle or control the rate of flow; 2. Lack of turbulence or resistance to flow when fully open - turbulence reduces head pressure; 3. Quick opening and closing mechanism - rapid response is many times needed in an emergency or for safety; 4. Tight shut off - prevents leaks against high pressure; 5. Ability to allow flow in one direction only - prevents return; 6. Opening at a pre-set pressure - procedure control to prevent equipment damage; and 7. Ability to handle abrasive fluids - hardened material prevents rapid wear. Term Part of the Process Identify the Mode that the Controller must be in Master Controller Slave Controller Process Variable Manipulated Variable The Load Where will the operator input the Setpoint?