Manufacturing Processes - Cutting Order Planning
Document Details
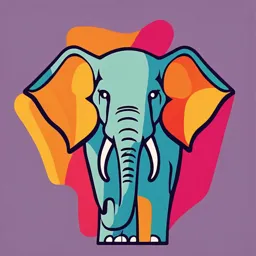
Uploaded by OptimisticSugilite7044
Tangshan Polytechnic University
Tags
Summary
These slides from Tangshan Polytechnic University covers the crucial steps in planning a cutting order, including surface processing methods, machining stage divisions, component arrangement, and equipment selection. It goes into detail on determining surface processing methods with economic considerations.
Full Transcript
新课内容 08:35 任务 9 :齿轮油泵齿轮轴 - 拟定工艺路线 任务: 完成项目报告单中拟定工艺路线部分内容以及前面所授课程中的内容 本节知识点: 选择各表面加工方法和加工方案 加工阶段的划分 工序集中与分散 加工工序的安排 机床及工艺装备的选择 ...
新课内容 08:35 任务 9 :齿轮油泵齿轮轴 - 拟定工艺路线 任务: 完成项目报告单中拟定工艺路线部分内容以及前面所授课程中的内容 本节知识点: 选择各表面加工方法和加工方案 加工阶段的划分 工序集中与分散 加工工序的安排 机床及工艺装备的选择 工艺路线的拟订 08:35 拟订工艺路线是设计工艺规程最为关键的一步,主要任务需顺序完成 以下几个方面的工作。 1 、选择各表面加工方法和加工方案 2 、划分加工阶段 3 、确定工序集中与分散 4 、确定加工顺序 5 、机床及工艺装备的选择 在拟定工艺路线时,需同时提出几种可能的加工方案,然后通过对比 分析 , 最后确定一种最为合理的工艺方案。 一. 加工方法和加工方案的选 08:35 择 一. 加工方法和加工方案的选择 各加工方法所能达到的经济精度及表面粗糙度 概念:经济精度 是指在正常的工作条件下(包括符合要求的标准设备、工艺装备、标 准技术等级的工人、不延长加工时间)所能保证的加工精度。 所能到达的粗糙度称为经济表面粗糙度。 一. 加工方法和加工方案的选 08:35 择 1. 表面加工方法的选择 在选择表面加工方法时,一般先根据表面精度和粗糙度要求选 择最终加工方法,然后再确定精加工前前期工序的加工方法。 选择加工方法,既要保证零件表面的质量,又要争取高生产效 率。 经济精度 序 一. 加工方法和加工方案的选 加工方法 ( 公差等级 经济粗糙度值 适用范围 08:36 号 Ra / um 择 表示 ) 1 粗车 IT11~13 12.5~50 2 粗车 - 半精车 IT8~10 3.2~6.3 适用于淬火钢以外 3 粗车 - 半精车 - 精车 IT7~8 0.8~1.6 的各种金属 外圆 4 粗车 - 半精车 - 精车 - 滚压 IT7~8 0.025~0.2 (或抛光) 表面 5 粗车 - 半精车 - 磨削 IT7~8 0.4~0.8 加工 主要用于淬火钢, 6 粗车 - 半精车 - 粗磨 - 精磨 IT6~7 0.1~0.4 方案 也可用于未淬火钢, 粗车 - 半精车 - 粗磨 - 精磨 - 0.012~0.1 但不宜加工有色金 7 IT5 超精加工 ( 或 R z 0.1 ) 属 8 粗车 - 半精车 - 精车 - 精细车 IT6~7 0.025~0.4 主要用于要求较高 (金刚车) 的有色金属加工 0.006~0.025 9 粗车 - 半精车 - 粗磨 - 精磨 - IT5 以 ( 或 Rz 超精磨(或镜面磨) 上 0.05 ) 极高精度的外圆加 0.006~0.1 工 10 粗车 - 半精车 - 粗磨 - 精磨 - IT5 以 ( 或 Rz 研磨 上 一. 加工方法和加工方案的选 08:36 择 金刚石车 研 磨 IT5~IT6 IT5 Ra0.01~1.25μm Ra0.008~0.32μm 精 车 超精加工 IT7~IT9 滚 压 IT5 Ra1.25~5μm IT6~IT7 Ra0.01~0.32μm 粗 车 半精车 Ra0.16~1.25μm IT10~IT13 IT8~IT11 砂带磨 Ra10~80μm Ra2.5~12.5μm IT5~IT6 Ra0.01~0.16μm 粗 磨 精 磨 IT8~IT9 IT6~IT7 Ra1.25~10μm Ra0.16~1.25μm 精密磨削 IT5 Ra0.008~0.08μm 抛 光 IT6~IT7 Ra0.008~1.25μm 序 加工方案 一. 加工方法和加工方案的选 经济精度 表面粗糙度 适用范围 08:36 号 择 级 Ra 值 /um 1 粗车—半精车 IT 10~8 3.2 ~ 6.3 2 粗车—半精车—精车 IT 8 ~ 7 0.8 ~ 1.6 回转体零件的端面 3 粗车—半精车—磨削 IT 8 ~ 6 0.2 ~ 0.8 平 面 4 粗刨 ( 或粗铣 )— 精刨 ( 或 精度要求不太高的不淬硬平 IT 10 ~ 8 6.3 ~ 1.6 精铣 ) 面 加 粗刨 ( 或粗铣 )— 精刨 ( 或 工 5 精铣 )— 刮研 IT 7 ~ 6 0.8 ~ 0.1 精度要求较高的不淬硬平面 方 粗刨 ( 或粗铣 )— 精刨 ( 或 案 6 精铣 )— 磨削 IT 7 0.8 ~ 0.2 精度要求高的淬硬平面或不 粗刨 ( 或粗铣 )— 精刨 ( 或 淬硬平面 7 IT 7 ~ 6 0.4 ~ 0.02 精铣 )— 粗磨—精磨 8 大量生产,较小的平面 ( 精 粗铣—拉 IT 9 ~ 7 0.8 ~ 0.2 度视拉刀精度而定 ) 9 粗铣—精铣—磨削—研磨 IT 5 以上 0.1 ~ 0.006 高精度平面 一. 加工方法和加工方案的选 08:36 择 粗 铣 半精铣 精 铣 高速精铣 抛 光 IT11~IT13 IT8~IT11 IT6~IT8 IT6~IT7 Ra0.008~1.25μm Ra5~20μm Ra2.5~10μm Ra0.63~5μm Ra0.16~1.25μm 研 磨 IT5~IT6 粗 磨 精磨 Ra0.008~0.63μm IT8~IT10 IT6~IT8 Ra1.25~10μm Ra0.16~1.25μm 导轨磨 IT6 粗 刨 半精刨 精 刨 Ra0.16~1.25μm 宽刃精刨 IT12~IT13 IT8~IT11 IT6~IT8 IT6 Ra5~20μm Ra2.5~10μm Ra0.63~5μm 砂带磨 Ra0.16~1.25μm IT5~IT7 Ra0.01~0.32μm 粗 车 半精车 精 车 刮 研 IT12~IT13 IT8~IT11 IT6~IT8 Ra0.04~1.25μm 精密磨 Ra10~80μm Ra1.25~5μm Ra1.25~5μm IT5~IT6 Ra0.01~0.32μm 粗 拉 精 拉 IT10~IT11 IT6~IT9 金刚石车 Ra5~20μm Ra0.32~2.5μm IT6 Ra0.02~1.25μm 粗糙度 Ra 值( 序号 加工方法 公差等级 适用范围 m) 08:36 1 钻 IT11 ~ 13 12.5 加工未淬火钢及铸铁。也可用 2 钻—铰 IT8 ~ 10 1.6 ~ 6.3 于加工有色金属。 孔径< 20 3 钻—粗铰—精铰 IT7 ~ 8 0.8 ~ 1.6 4 钻—扩 IT10 ~ 11 6.3 ~ 12.5 5 加工未淬火钢及铸铁。也可用 钻—扩—铰 IT8 ~ 9 1.6 ~ 3.2 内 6 钻—扩—粗铰—精铰 IT7 0.8 ~ 1.6 于加工有色金属。 孔径> 15 但一般< 80 孔 7 钻—扩—机铰—手铰 IT6 ~ 7 0.2 ~ 0.4 加 8 钻—扩—拉 IT7 ~ 9 0.1 ~ 1.6 大批量生产通孔, 孔径> 30 ,但一般< 80 工 9 粗镗(扩) IT11 ~ 13 6.3 ~ 12.5 方 10 粗镗(粗扩)—半精镗(精扩) IT9 ~ 10 1.6 ~ 3.2 案 除淬火钢以外的各种材料,毛 粗镗(粗扩)—半精镗(精扩)— 坯有铸出或锻出孔, 11 IT7 ~ 8 0.8 ~ 1.6 精镗(铰) 孔径> 30 12 粗镗(粗扩)—半精镗(精扩)— IT6 ~ 7 0.4 ~ 0.8 精镗—浮动镗刀镗孔 13 粗镗(扩)—半精镗—磨 IT7 ~ 8 0.2 ~ 0.8 主要用于淬火钢,也可用于未 14 粗镗(扩)—半精镗—粗磨—精磨 IT6 ~ 7 0.1 ~ 0.2 淬火钢,不宜用于有色金属 15 粗镗—半精镗—精镗—精细镗 IT6 ~ 7 0.05 ~ 0.4 主要用于高精度有色金属加工 16 粗镗—半精镗—精镗—珩磨 IT6 ~ 7 0.025 ~ 0.2 用于加工精度很高的孔 一. 加工方法和加工方案的选 08:36 择 扩 铰 手 铰 IT9~IT13 IT6~IT9 IT5 滚压 Ra1.25~40μm Ra0.32~10μm Ra0.08~1.25μm IT6~IT7 Ra0.01~1.25μm 钻 IT10~IT13 精 镗 Ra5~80μm IT7~IT9 金刚镗 Ra0.63~5μm IT5~IT7 半精镗 Ra0.16~1.25μm IT11~IT12 Ra2.5~10μm 粗 磨 精磨 IT9~IT11 IT7~IT8 珩 磨 粗 镗 Ra1.25~10μm Ra0.08~0.63μm IT5~IT8 IT12~IT13 Ra0.04~1.25μm Ra5~20μm 精 拉 IT7~IT9 研磨 粗 拉 Ra0.16~0.63μm IT5 IT9~IT10 Ra0.008~0.32μm Ra1.25~5μm 推 IT6~IT8 Ra0.08~1.25μm 一. 加工方法和加工方案的选 08:36 择 2. 选择表面加工方案应考虑的因素 选择加工方案时,一般是根据经验或是查表来确定,具体选择时应考 虑以下几个方面: 1 )、根据加工表面的技术要求,选择能获得经济精度的加工方法。 如:加工 IT7 ,表面粗糙度为 Ra 0.8um 的外圆柱面,通过精细车、滚压、磨削 可以达到要求,选择一种合理的加工方法。 2 )、要考虑被加工材料的性质; 例如,淬火钢的精加工用磨削的方法加工; 有色金属的表面粗糙度要求较高时,不能磨削 , 一般采用高速精细车削的方法进行 精加工。 一. 加工方法和加工方案的选 08:36 择 3 )、工件的结构、形状和尺寸大小 例如:对于加工精度为 IT7 的孔,采用镗削、铰削、拉削和磨削均可以达到要求,但箱体 上的孔不应选用拉孔和磨孔,应采用镗孔和铰孔的加工方法。而大孔应选用镗孔、小孔应 选用铰孔。 4 )、根据生产类型选择合理的加工方法。 如:大批大量生产应选用高效率的加工方法,采用专用设备。 例如,平面和孔可用拉削加工;轴类零件可采用半自动液压仿型车床加工; 复杂表面 可采用数控机床和加工中心等。 5 )、应充分利用本厂现有设备和工艺装备。发挥工人的创造性。 在选择加工方法时,应根据零件主要表面的技术要求和工厂具体条件,先选定它的最 终加工方法,然后再确定前导工序的加工方法。 二、加工阶段的划分 08:36 二、加工阶段的划分 当零件的加工质量要求较高时,不能在一道工序中完成全部加工内容,而应根据零件的技术 要求划分加工阶段。 1. 加工阶段划分: 1 )、粗加工阶段:尽量切除大部分余量,使工件形状、尺寸接近成品。 2 )、半精加工阶段:去除粗加工后留下的误差和缺陷,使被加工工件达 到一定的精度。为主要表面的精加工做准备,并完成次要表面的终加工(钻孔、 攻丝、铣键槽等)。 3 )、精加工阶段:保证各主要表面达到图纸要求,保证加工质量。这是 关键加工阶段,大多数零件经过这一加工阶段就已经完成。 4 )、光整加工阶段:为了获得高质量的尺寸精度和表面粗糙度。(标准 精度等级为 IT5 上, Ra≤0.2um )。不能纠正位置精度。位置精度用前道 工序保证。(抛光、研磨等) 二、加工阶段的划分 08:36 2. 划分加工阶段的目的 1). 保证零件加工质量; 粗加工时,切除的加工余量大,产生大量的切削力和切削热,使零件的变形产 生加工误差,必须通过后续的半精加工和精加工消除和修复,因而有利于保证 零件最终的加工质量。 2). 有利于及早发现毛坯缺陷并及时处理 毛坯粗加工后,可及时发现零件各种缺陷,采取补救措施 二、加工阶段的划分 08:36 2. 划分加工阶段的目的 3). 有利于合理利用机床设备 划分加工阶段后,就可以充分发挥机床的优势,粗加工可采用功率大、刚度好 和精度较低的机床加工,精加工则采用高精度机床,以确保工件的精度要求, 充分发挥机床的特点,合理使用设备。 4). 便于安排热处理工序 粗加工阶段前后,一般安排去应力处理等预先热处理工序,精加工前后要安排 淬火等最终热处理。 5). 避免损伤已加工表面 将精加工安排在最后,可以保护精加工表面在加工过程中少受损伤或不受损伤。 三、工序集中与分散 08:36 三、工序集中与分散 1. 工序集中与分散的概念 在制定工艺过程中,为便于组织生产,常将工艺过程划分为若干个工序。组合 工序时有两个不同的原则:即工序的集中和工序的分散。 1) 工序集中 就是将零件的加工集中在少数几道工序中完成,每道工序加 工内容多。可采用机械集中或组织集中。 2) 工序分散 就是将零件的加工分散到很多道工序中完成,每道工序加工 的内容少,工艺路线很长。有时每道工序只有一个工步。 三、工序集中与分散 08:36 2. 工序集中与分散的特点 工序集中 每道工序加工面多 特点: 1 )可以采用高效率的专用设备和工艺装备 , 生产效率高,对工人的技术水平要求 高; 2 )减少了装夹次数,容易保证各加工表面间的相互位置精度,并缩短辅助时间。 3 )工序集中,机床数量、操作工人和生产占地面积都减少,节省了人力、物力; 4 )工序集中所需要的设备相对结构复杂,调整、维修困难、投资大。(设备通用 性强、功能多) 三、工序集中与分散 08:36 2. 工序集中与分散的特点 工序分散:每道工序加工面少。 特点: 1 )劳动强度低、对操作工人的技术水平要求低。 2 )可以采用最合理的切削用量,减少基本时间。 3 )设备和工艺装备数量多,操作工人多,占地面积大。 4 )设备简单,调整方便,工人便于掌握,容易适应产品的变换。 三、工序集中与分散 08:36 3. 工序集中与分散的选择原则 工序分散:每道工序加工面少。 确定工序集中或分散的原则,主要根据设备、生产规模、零件的结构特点综合考虑 后确定。 1 )、对重型零件的加工,为减少装夹和往返搬运的次数,多采用工序集中的原 则。 2 )、对于刚性差,精度高的精密工件,应当用工序分散的原则。 随着数控机床的发展,现代生产倾向于采用工序集中的加工方法。工序集中的 优点多于工序分散。 三、工序集中与分散 08:36 3. 工序集中与分散的选择原则 工 大批大量生产时,如果使用采用数控机床、 序 加工中心则按工序集中原则组织工艺过程, 集 每个工序包括的加工内容 虽然设备的一次性投资较高,但有足够的 中 尽量多,甚至是在一个工 柔性 , 转产相对容易. 原 序内完成工件所有表面的 单件小批生产时,在通用机床上按工序集 加工。 则 中组织生产。 重型零件,为了减少工件的装卸和运输的 劳动量,工序应该集中。 工 序 每个工序所包括的加工内 大批大量生产时,如果使用专用流水线、 分 容尽量少。 甚至每个工序 自动线生产,则按工序分散原则组织生产, 只包括一个工步。 这种组织方式可以提高生产率,但对产品 散 转产比较困难。 原 则 对于刚性较差且精密的零件应该分散工序 四、加工顺序的安排 08:36 四、 加工顺序的安排 复杂零件的机械加工要经过一系列切削加工、热处理和辅助工序,因此在 拟订路线时,工艺人员要全面的把切削加工、热处理和辅助工序综合考虑。 1 .工序顺序的安排 2 .热处理工序的安排 3 .检验工序的安排 4. 其它工序的安排 四、加工顺序的安排 08:36 1 .工序顺序的安排 1 )基面先行 先基准面后其它表面,先把基准面加工出来,再以基准面定位来加工其它表面。 即上道工序的加工能为后面的工序提供精基准和合适的夹紧表面。前工序为后 工序提供基准的原则。 对于箱体零件,一般是以主要孔为粗基准加工平面,再以平面为精基准加工孔 系;对于轴类零件,一般是以外圆为粗基准加工中心孔,再以中心孔为精基准 加工外圆、端面等其他表面。 四、加工顺序的安排 08:36 1 .工序顺序的安排 2 ) 先主后次 零件的主要表面一般都是精度和表面质量要求比较高的表面,它们的加工对 整个零件的质量影响很大,因此先安排主要表面的加工,再将其他表面的加 工适当安排在它们中间穿插进行; 如主要表面是指装配表面、工作表面,次要表面是指键糟、联接用的光孔等。 10 四、加工顺序的安排 08:36 1 .工序顺序的安排 3 ) 先粗后精 零件的加工先粗加工,根据需要依次安排半精加工,最后安排精加工,粗精分开。 粗加工的热应力和热变形充分恢复后,然后精加工。 4 ) 先面后孔 对于箱体、支架和连杆等工件,应先加工平面后加工孔,因为平面轮廓面积较大, 能保证有可靠的定位基准,又能保证孔与面之间的位置精度要求。 比如加工零件的中心孔前必须先加工端面,然后再钻中心孔,否则有可能端面的 不平,使孔钻偏或中心孔折断。在零件表面钻孔也一样。 四、加工顺序的安排 08:36 2 .热处理工序的安排 根据热处理的目的和工件的材料,安排热处理在加工过程中的位置。 预备热处理 热 处 最终热处理 理 工 时效处理 序 表面装饰性镀层和 发兰处理 四、加工顺序的安排 08:36 2 .热处理工序的安排 1 )、预备热处理 预备热处理的目的是消除毛坯制造过程中产生的内应力,改善金属材料的切 削加工性能。常使用退火、正火、调质 一般安排在粗加工之前、后。在粗加工之前可改善材料的切削加工性能,安 排在粗加工之后,有利于消除残余应力 退火: 将钢加热到一定的温度,保温一段时间,随后由炉中缓慢冷却的一种热处 理工序。 作用:消除内应力,降低硬度,提高韧性,改善切削加工性。 应用:高碳钢采用退火,以降低硬度;放在粗加工前,毛坯制造出来以后。 四、加工顺序的安排 08:36 2 .热处理工序的安排 1 )、预备热处理 正火: 将钢加热到一定温度,保温一段时间后从炉中取出,在空气中冷却的一种 热处理工序。 作用:提高钢的强度和硬度,使工件具有合适的硬度,改善切削加工性。 应用: 低碳钢采用正火,以提高硬度。放在粗加工前,毛坯制造出来以后。 调质处理:淬火后再高温回火 作用:是获得细致均匀的组织,提高零件的综合机械性能。 应用:安排在粗加工后,半精加工前。常用于中碳钢和合金钢。 四、加工顺序的安排 08:36 2 .热处理工序的安排 2 ) 最终热处理 目的:提高工件表面硬度和耐磨性,一般安排在精加工的前后。 最终热处理常采用淬火、渗碳、渗氮淬火等工艺达到硬度要求 。 淬火: 将钢加热到一定的温度,保温一段时间,然后在冷却介质中迅速冷却, 以获得高硬度组织的一种热处理工艺。 作用:提高零件的硬度。 应用:一般安排在磨削前。 四、加工顺序的安排 08:36 2 .热处理工序的安排 3 ) 时效处理 目的:是消除毛坯制造中产生内应力,减小工件变形。 自然时效 / 人工时效 应用:一般安排在粗加工后,精加工之前。常用于大而复杂的铸件。 4 ) 表面热处理 为增加工件的耐蚀性和装饰性安排的热处理工序,例如镀铬、镀锌、发兰等,一 般都安排在工艺过程最后阶段进行。 四、加工顺序的安排 08:36 四、加工顺序的安排 08:36 热处理工艺特点 预备热处理 一般安排在粗加工前 与工序安排 最终热处理 热处 一般安排在精加工前后 理工 时效处理 一般安排在粗加工之后,精 序 加工前。 表面装饰性镀层 一般都安排在机械加工完毕 和发兰处理 后 毛坯 预备 粗加 预备 半精 最终 精加 表面 加工 热处理 工 热处理 热处理 成品 加工 热处理 工 时效 调制 镀锌 正火 时效 淬火 镀铬 退火 渗碳 发兰 四、加工顺序的安排 08:36 热处理工艺特点 与工序安排 · 为改善切削性能的热处理工序 ( 退火、正火、调质 ) 应安排在 切削加工之前 · 为清除内应力的热处理工序 ( 时效、退火、正火 ) 应安排在粗 加工之后 · 半精加工之后,精加工之前安排淬火 - 回火、渗碳、淬火等淬硬 处理工序,淬硬之后一般只磨 · 表面处理工序一般放在最后 : 镀铬、镀锌、阳极氧化、发黑、发 蓝 四、加工顺序的安排 08:36 3 .检验工序的安排 为保证零件质量,防止产生废品,需在下列场合安排检验工序 ( 除了安排尺寸检验之外,有的零件还要安排探伤、密封、平衡 等检验工序 ) : 1) 粗加工全部结束之后 ; 2) 送往外车间加工的前后; 3) 工时较长和重要工序前后; 4) 零件全部加工之后。 四、加工顺序的安排 08:36 4. 其它工序的安排 其他工序包括工件的清洗、去磁和涂防锈漆等 零件表层或内腔的毛刺对机器装配质量影响甚大时切削加工后,应安 排去毛刺工序。 零件在进入装配之前,一般都应安排清洗工序,去除切屑。研磨、珩 磨等光整加工工序之后,微小磨粒易附着在工件表面上,要注意清洗。 在用磁力夹紧工件的工序之后,要安排去磁工序,消除磁性后再进行 装配工序。 五、机床及工艺装备的选择 08:36 五、机床及工艺装备的选择 工艺装备(工装)是指产品在制造过程中所采用的各种工具的总称,包括夹具、 刀具、辅具、量具、模具等。 1 )机床与工装的尺寸规格 与工件的外廓尺寸相适应。 2 )机床与工装的精度范围 与工件所要求的精度相适应。 3 )机床与工装的生产效率 与工件加工的生产类型相适 应。 4 )结合企业生产现场情况 5 )切削用量 讨 08:36 论 1. 零件的切削加工顺序安排的原则是什么? 1 )基面先行; 2 ) 先主后次; 3 )先面后孔; 4 ) 先粗后精 2. 常用的热处理(时效、退火、调制、淬火、时效)工序如何安排? 目的是什么? 毛坯 预备 粗加 预备 半精 最终 精加 表面 加工 热处理 工 热处理 热处理 成品 加工 热处理 工 时效 调制 镀锌 正火 时效 淬火 镀铬 退火 渗碳 发兰 讨 08:36 论 退火: 加热→保温→随炉冷却。 作用:消除内应力,降低硬度,提高韧性,改善切削加工性。 应用:高碳钢采用退火,以降低硬度;放在粗加工前,毛坯制造出来以后。 正火:加热→保温→空冷 作用:提高钢的强度和硬度,使工件具有合适的硬度,改善切削加工性。 应用: 低碳钢采用正火,以提高硬度。放在粗加工前,毛坯制造出来以后。 调质处理:淬火后再高温回火 作用:是获得细致均匀的组织,提高零件的综合机械性能。 应用:安排在粗加工后,半精加工前。常用于中碳钢和合金钢。 时效处理 作用:是消除毛坯制造中产生内应力,减小工件变形。 自然时效 / 人工时效 应用:一般安排在粗加工后,精加工之前。常用于大而复杂的铸件。 序 序 加工方案 加工方法 总 经济精度 表面粗糙度 经济精度 经济粗糙度值 ( 公差等级 适用范围 适用范围 08:36 号 号 级 Ra 值Ra /um / um 结 表示 ) 1 1 粗车 粗车—半精车 1 、选择各表面加工方法和加工方案 IT11~13 3.2 IT8~IT10 ~ 12.5~50 6.3 2 2 粗车 - 半精车 IT8~10 3.2~6.3 内 粗车— 半精车—精车 IT7 ~ 8 0.8 ~ 1.6 回转体零件的端面 适用于淬火钢以 3 粗车 - 半精车 - 精车 IT7~8 0.8~1.6 孔 3 IT6 ~ 0.2 ~ 0.8 外的各种金属 平 外圆 粗车—半精车—磨削 粗车 - 半精车 - 精车 - 滚压 IT8IT7~8 加 4 0.025~0.2 面 表面 (或抛光) ( )— 精刨 ( 或精 工 45 粗车或粗铣 粗刨 ITl0 ~ 8 6.3 ~ 0.4~0.8 1.6 精度要求不太高的不 加 加工 - 半精车 铣 ) - 磨削 IT7~8 淬硬平面 方 主要用于淬火钢, 工 方案 6 粗刨 粗车 - 半精车 ( 或粗铣 - 粗磨( 或精 )— 精刨 - 精磨 IT6~7 0.1~0.4 精度要求较高的不淬 也可用于未淬火 案 5 IT7 ~ 6 0.8 ~ 0.1 方 铣 )— 刮研 0.012~0.1 硬平面 钢,但不宜加工 7 粗车 - 半精车 - 粗磨 - 精磨 - IT5 案 超精加工 粗刨 ( 或粗铣 )— 精刨 ( 或精 ( 或 R Z 0.1 ) 有色金属 6 IT7 0.8 ~ 0.2 铣 )— 磨削 精度要求高的淬硬平 主要用于要求较 粗车 - 半精车 - 精车 - 精细车 8 粗刨 IT6~7 0.025~0.4 面或不淬硬平面 7 ( 或粗铣 )— 精刨 ( 或精 高的有色金属加 (金刚车) IT7 ~ 6 0.4 ~ 0.02 铣 )— 粗磨—精磨 工 0.006~0.025 大量生产,较小的平 粗车 - 半精车 - 粗磨 - 精磨 IT5 以 89 粗铣—拉 - 超精磨(或镜面磨) ( 或 IT9 ~ 7 上 0.8 ~ 0.2 R Z面 ( 精度视拉刀精度 0.05 ) 极高精度的外圆 而定 ) 0.006~0.1 加工 粗车 - 半精车 - 粗磨 - 精磨 - IT5 以 910 粗铣—精铣—磨削—研磨 IT5 以上 0.1 ~( 或 RZ 0.006 高精度平面 总 08:36 结 2 、划分加工阶段 1 )、粗加工阶段:切除大部分余量,工件形状、尺寸接近成品。 2 )、半精加工阶段:为主要表面的精加工做准备,并完成次要表面的终加工 (钻孔、攻丝、铣键槽等)。 3 )、精加工阶段:保证各主要表面达到图纸要求,保证加工质量。这是关键 加工阶段,大多数零件经过这一加工阶段就已经完成。 4 )、光整加工阶段:为了获得高质量的尺寸精度和表面粗糙度。(标准精度 等级为 IT5 上, Ra≤0.2um )。不能纠正位置精度。位置精度用前道工序 保证。(抛光、研磨等) 总 08:36 结 3 、确定工序集中与分散 工序集中特点 每道工序加工面多 1 )采用专用设备和工艺装备 , 生产效率高,对工人的技术水平要求高; 2 )减少装夹次数,保证各加工表面间的相互位置精度,并缩短辅助时间。 3 )工序集中,机床数量、操作工人和生产占地面积都减少,节省了人力、物力; 4 )工序集中所需要的设备相对结构复杂,调整、维修困难、投资大。(设备通用 性强、功能多) 工序分散:每道工序加工面少。 1 )劳动强度低、对工人的技术水平要求低。 2 )可以采用最合理的切削用量,减少基本时间。 3 )设备和工艺装备数量多,操作工人多,占地面积大。 4 )设备简单,调整方便,工人便于掌握,容易适应产品的变换。 总 08:36 结 4 、确定加工顺序 1. 工序顺序的安排 1 )基面先行; 2 ) 先主后次; 3 )先面后孔; 4 ) 先粗后精 2. 热处理工序的安排 3 .检验工序的安排 1) 粗加工全部结束之后; 2) 送往外车间加工的前后; 3) 重要工序后; 4) 零件全部加工之后。 4. 其它工序的安排 其他工序包括工件的清洗、去磁和涂防锈漆等 总 08:36 结 5 、机床及工艺装备的选择 1 )机床与工装的尺寸规格 与工件的外廓尺寸相适应。 2 )机床与工装的精度范围 与工件所要求的精度相适应。 3 )机床与工装的生产效率 与工件加工的生产类型相适 应。 4 )结合企业生产现场情况 5 )切削用量 08:36 The End