TQM Overview PDF
Document Details
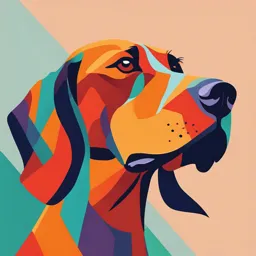
Uploaded by OptimisticLynx
Jadavpur University
Tags
Summary
This document provides an overview of total quality management (TQM), including specific case studies and Tata Steel's initiatives. It details the importance of TQM and its implementation across industries.
Full Transcript
SAKSHAM: IL6 WEBINAR for Logistics “Overview of TQM” Ignoring Quality – a recipe for catastrophe (Case 1) 2 Ignoring Quality – a recipe for catastrophe (Case 2) 3 Let’s Discu...
SAKSHAM: IL6 WEBINAR for Logistics “Overview of TQM” Ignoring Quality – a recipe for catastrophe (Case 1) 2 Ignoring Quality – a recipe for catastrophe (Case 2) 3 Let’s Discuss 4 Which country comes to your mind when we talk about Quality 5 Which country comes to your mind when we talk about “QUALITY” 9 Which companies or products have a reputation for good build quality? 10 What is Quality ? 11 Quality is the result of a carefully constructed cultural environment! - Philip Crosby Total Quality Management helps create such a cultural environment 12 TQM Definition Total Quality Management is: A set of systematic activities carried out by the entire organization to effectively and efficiently achieve company objectives so as to provide products and services with a level of quality that satisfies customers at the appropriate time and price TQM is neither a program nor a model that can be bought off-the-shelf It is an entire management system that includes a philosophy, principles, methods, and tools If a company tries to use the methods without understanding and embracing the philosophy, or the tools without the principles, it will fail The system cannot be "cherry-picked"; it is either entered into completely, or not at all 13 Steel Making at Tata Steel India: Long and Complex Value Chain Raw Materials Iron Making Steel Making Rolling and further processing 1 Hot metal > 2.3 million Heterogeneity Homogenization Customization end customers Crude Steel Production doubled, from 9.97 MnT in 2015 19.9 MnT in 2023 Two-fold increase in Dealers, from 10,991 in 2015 20,478 in 2023 Changing Three times increase in Steel Processing Centres, from 12 SPCs in 2015 40 SPCs in 2023 landscape Launch of new grades from new locations for catering to emerging requirements. Sustainability focus – Steel Recycling Business, Green Steel, Green Warehousing 1. Multi-sourcing and variation in the quality of input Raw Materials 2. Logistics and Transportation 3. Establishing plug and play Models for onboarding newly acquired units, new businesses and contract manufacturing Key Challenges 4. Ensuring Quality as Zero-day Requirement 5. Capability building of suppliers and partners in line with Tata Steel’s growth plans. 14 Integrated TQM Framework : the binding glue from mining to finished products Focused Methodologies TQM Vehicles Review & Assessment Problem Solving & Task Achieving Policy Management Shikhar 25 Daily Management Theory of Constraints (TOC, CCPM) Tracking & review mechanism and Knowledge Management Cross Functional Management Periodic assessments Retail Value Management Small Group Activities & Supplier Relationship Management Suggestion Management Standardization (Systems& Processes) Education & Training Guiding Principle - Standardise, Improve, Innovate (SII) A common lexicon for all to understand & speak the same language across the diverse & long value chain 15 S I I – Key dimensions of improvement Innovation (Breakthrough Improvement) Improvement Sustenance/ (Gradual Standardization Improvement) An adaptation of a Buddhist motif: eyes of the past (right), present (left), and future (top middle) (Courtesy : Shoji Shiba) 16 What is Daily Management Daily Management is the management of regular/routine jobs at all levels such that processes are stabilized to give consistent and predictable outcomes, aligned with customer requirements. It enables – Systematic way of monitoring performance parameters Understanding of ‘What’ is required to keep parameters stable How to handle deviations and regain control … to deliver stable and consistent outputs 17 Policy Management (PM) and Daily Management (DM) Target Set by Management Policy Management Daily Management Year 0: Year 1: Current Time Future Trend line indicates performance levels required if additional ‘stretched’ targets set by management are to be achieved. Trend line indicates performance levels if existing processes are to continue 18 Why Daily Management is important Importance of DM Big Improvement by Policy Management, Problem Solving/Task Achieving etc. Keep stable, Improve progressively Month All the members must commit continuously, long term 19 Why Daily Management is important Lack of DM leads to….. Big Improvement by Policy Management, Problem Solving/Task Achieving etc. Month Lack of stability will adversely impact the improvement cycle 20 PDCA and SDCA Improvement Wheel (PDCA) Sustenance Wheel (SDCA) Source: Dr N. Kano 21 Continual Improvement through PDCA 22 Governance Mechanism Joint Committees of Union Management Committees Central TQM & Management Apex Review (Quality, Safety, Env. etc.) Promotion & communication Joints Works Quality (Chaired by CEO&MD) Committee (JWQC) Support divisions (facilitation, reviews, workshops) Divisional Reviews (TQM Councils) (Chaired by Vice Presidents) Suggestion Box Education & training Committee Departmental Reviews(CAT/MR) Monitor and report progress of Departmental JDC (Chaired by Chiefs) TQM plan & activities meetings Key Deliverables Formulation of policies, guidelines and framework for various TQM methodologies and vehicles. Review of TQM practices & improvement projects Prioritization of focus areas and resource allocation Cross functional approach for problems 23 Triggers for change addressed through unwavering focus on Quality TQM Response Resilient, Resolute Agility: AWOW led Apex projects “Synergized” 2022 6 and Future-Ready StepUP – internal talent marketplace Excellence 2019 & beyond Open Innovation – Solvia & TSL InnoVerse Benchmark leader TBEM 2021 Enhancing customer Industry leader Digital Value Acceleration experience Seeking Innovent: Promoting market led innovation 2015, 2018 5 world class Value discovery thru’ Shikhar25: Accelerating EBITDA improvement Deming Grand 2009 - 2018 Corporate Quality Assurance digital, innovation Prize (DGP) 2012 “KVHS”: a focused problem-solving approach Codifying the Tata Steel way Deming Global outlook, TQM Diagnosis, Integrated TQM framework Application Prize Growth Customer: awareness to delight: 4 RVM, CVM, SVM, TOC (DAP) 2008 2005-2008 Development Leadership in Cost Launch of ASPIRE- 6푆푖푔푚푎 Excellence, 2004 3 competitiveness Total Operational Performance (TOP) Value chain focus 1997 - 2004 Measuring effectiveness through TBEM JRD QV Award Operational efficiency 2000 Modernization Quality Projects, TPM, Value Engineering Employee involvement 2 of mind Introduction of Tata Business Excellence Model PM’s Trophy 1992 - 1996 (13 times best Standardization ISO systems, Quality Circles, Improvement Projects Awareness integrated steel plant 1 1988 - 1991 & 11 times trophy) TQM as a vehicle to drive Business Excellence…a baton passed seamlessly across generations of leaders…. TPM: Total Productive Maintenance, TBEM: Tata Business Excellence Model, ASPIRE: Aspirational Initiative to Retain Excellence, TOC: Theory of Constraints, RVM: Retail Value 24 Management, CVM: Customer Value Management, KVHS: Kar Vijay Har Shikhar, AWOW: Agile Way of Working , DATOM: Data & Analytics Target Operating Model Tata Steel India: TQM Organizational Structure Peeyush Gupta VP TQM, GSP and Supply Chain Tripti Srivastava Chief TQM & CQA Suresh Divyanshu Avinash Ankur Ajinkya Valasani Chandra Nidhi Basu Srivastava Kumar Gandotra Vikas Deo Ravi Kumar Mishra Head TQM – DM, QMS Head TQM- Analytics Head CQA Head TQM – Org. Head TQM - TEEP, Head TQM & CQA - Head TQM, TSM & Empl. Engagement Learning & Innovation BE & Strategy TSK Driving Daily Driving improvements Implementation of QA Innovation Driving Tata Education Deployment of TQM Deployment of TQM Management, QMS, projects through requirements across Management and Excellence and CQA at TSK and CQA at TSM Employee Involvement different focused value chain, QA driving Group Level Programme (TEEP), initiatives like TPM, methodologies like – Governance (Quality Innovation Programs. Facilitating Business Quality Circles, MASS DMAIC/ DMADIC/ ToC/ Board meeting Apex Managing Organisation Assessments for TSL and Suggestion CCPM/ SIPs etc. Quality review), IATF Knowledge. Management certification and Driving TQM capability System improvement building Extended Eco system across the organization to facilitate the TQM deployment: 55 Improvement Managers in Divisions/ Profit Centers (full time engagement) 128 TQM coordinators in departments (Part time engagement) 25 Framework for People Involvement People Involvement KPI – Overall % Employee Involvement SGA MASS+ Suggestion Team based activity Team based activity Subject – Function Subject - Themes given by Management Based Local problems Management, Ideas Individual Activity Focus – Employee implemented through Innovative Suggestions Engagement SGA Circles of employees are Permanent teams such Focus - Employee implemented by as ‘Quality Circles’ and Development management ‘TPM Circles’ Temporary teams which Members are from the come together as task KPIs – same workplace force No. of Suggestions Cross Functional generated/ employee KPIs – members No. of Suggestion % Active Circles KPIs – Implemented/ No. of Kaizens/ Circle % ideas implemented Employee No. of ideas generated SGA - Small Group Activity, MASS+ - Manthan Ab Shopfloor Se+ 26 For us TQM means understanding 01 The objective of our job. 02 Our customer and their requirements (MoU) 03 The input, process and product characteristics of our processes 04 Process characteristics we monitor and control to achieve product characteristics (Control chart/trend chart etc.) 05 The SOPs we observe to achieve the product characteristics 06 The corrections/corrective actions we take in case of deviation in a systematic way 07 Awareness of customer complaints and actions thereon 27 Look at the sky with feet firmly on the ground ! 28 Thank You 29