Quality and Safety Precis (Airmen Leadership & Supervisory Course) - December 2023 - Pakistan Air Force PDF
Document Details
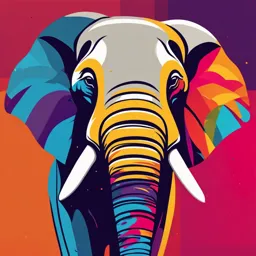
Uploaded by DecentCentaur
Airman Leadership Academy
2023
Pakistan Air Force
Gp Capt M Imran Chaudhry
Tags
Related
- Suggestion Scheme/Quality Circles - Chapter 14
- Lean Six Sigma (IE Elective 2) - LSS 1-Overview PDF
- QSM SG 4 FINALS PDF
- Quality Management for Organizational Excellence PDF
- Narratives of Total Quality Management, Green Management, Risk-Taking on Organizational Performance: 2024 PDF
- Narratives of Total Quality Management PDF
Summary
This document is a precis of Quality and Safety for Airmen Leadership and Supervisory Course, December 2023 from the Pakistan Air Force. It covers foundational principles and advanced methodologies for organizational excellence, such as Six Sigma, Lean, and Kaizen, for supervisors in aviation.
Full Transcript
RESTRICTED QUALITY DYNAMICS AIRMEN Strategies for Organizational Excellence LEADERSHIP From foundational principles to a...
RESTRICTED QUALITY DYNAMICS AIRMEN Strategies for Organizational Excellence LEADERSHIP From foundational principles to advanced methodologies, this precis ACADEMY equips you with the knowledge and tools to drive organizational excellence. Explore Six Sigma, Lean Philosophy, Kaizen, and more, as you learn to implement, sustain, and innovate quality strategies. RESTRICTED RESTRICTED PRECIS OF QUALITY AND SAFETY AIRMEN LEADERSHIP & SUPERVISORY COURSE The information given in this document is not to be communicated either directly or indirectly to the press or to any person not authorized to receive it. AIRMEN LEADERSHIP ACADEMY PAKISTAN AIR FORCE RESTRICTED RESTRICTED REPRODUCTION OF THE INFORMATION CONTAINED IN THIS PUBLICATION IS NOT PERMITTED WITHOUT PRIOR APPROVAL OF AIR HEADQUARTERS. PREPARED BY : QUALITY – Snr Tech Zaheer, Snr Tech Sher SAFETY – Chf Tech Tariq, Snr Tech Azmat REVIEWED BY : Wg Cdr Mubashar Ahmad VETTED BY : Gp Capt M Imran Chaudhry (i) RESTRICTED RESTRICTED FOREWORD 1. Air Staff has envisioned the establishment of Airmen Leadership Academy (ALA), as center of excellence for producing supervisors with true leadership spirit to make PAF compatible with contemporary Air Forces. This vision would be materialized by the merger of JCOs‟ Academy and Professional Training Department into Airmen Leadership Academy (ALA), to develop a proficient workforce by reinforcing leadership & management skills with focus on refined work ethics. To achieve this milestone in training, the faculty of Airmen Leadership Academy has been equipped with a multifaceted and comprehensive training as per futuristic requirements of PAF. 2. The SNCOs reporting at Airmen Leadership Academy for AL&SC would have already put on substantial years of service in their respective trades. The course at the ALA is aimed to enhance their innate skills and qualities so as to groom them as effective Junior Commanders. 3. The commitment to the highest standards of Quality and Safety is not just a requirement but a shared responsibility in PAF. This comprehensive guide, tailored for PAF supervisors, is not merely a manual but a strategic compass, charting the course towards a culture of continuous improvement and unwavering safety. Rooted in both theoretical frameworks and practical applications, this precis is a vital tool for supervisors seeking to enhance the efficacy of their operations. It is more than a guide; it is an invitation to elevate our commitment to excellence in the dynamic and demanding domain of aviation. May the insights within these pages foster a culture where safety is not just a priority, but an ingrained value, ensuring that every mission of PAF is executed with the utmost precision and care. Safe skies, successful missions, and enduring excellence await those who embrace the wisdom contained herein. (M IMRAN CHAUDHRY) Group Captain Officer Commanding Dated: December, 2023 Airmen Leadership Academy, PAF (ii) RESTRICTED RESTRICTED APPROVAL OF PRECIS TRADE: AL&SC DURATION OF COURSE: 08 WEEKS SCHOOL: AIRMEN LEADERSHIP ACADEMY, PAF _____________________________________________________________________________________________________________________________ ___________________________________________________________________________ 1. The Précis of Quality and Safety for AL&S Course of Airmen Leadership Academy, PAF has been devised in accordance and contents have been vetted for authority of facts. (M IMRAN CHAUDHRY) Group Captain Officer Commanding Dated: Airmen Leadership Academy, PAF _____________________________________________________________________________________________________________________________ ___________________________________________________________________________ 2. The Précis of Quality and Safety has been vetted for relevance and applicability of the topics and it meets the requirements of AL&S Course at Airmen Leadership Academy, PAF. Director Date:- Specialist Directorate / Agency 3. The Précis of Quality and Safety for AL&S Course at Airmen Leadership Academy, PAF has been checked for compliance with the existing standards / format and is hereby approved. Date:- Director Basic Training (iii) RESTRICTED RESTRICTED CHAPTER 1: INTRODUCTION TO QUALITY Desired Learning Objectives 1. After studying this chapter, students will be able to: (a) Explain the concept of Quality and its associated terminologies (b) Differentiate between Quality assurance and Quality control with examples (c) Assess the significance of Quality in ensuring productivity and efficiency for organizations. "The quality of a person's life is in direct proportion to their commitment to excellence, regardless of their chosen field of endeavor." Vince Lombardi Quality 2. Quality is a key aspect of any organization and it is defined as the level of excellence of a product or service. It can be referred to as how good something is. A high-quality product means that the product is very good and fulfills the purpose for which it is created. Let‟s see various definitions of Quality from different sources or individuals showcasing the diverse perspectives on what constitutes „Quality‟: (a) ISO 9001. “Degree to which a set of inherent characteristics fulfils requirements.” (b) Oxford Dictionary. “The standard of something as measured against other things of a similar kind; the degree of excellence of something.” (c) Deming. “The capacity to satisfy wants.” (d) Juran. “Fitness for use (fitness is defined by the customer).” (e) Crosby. “Conformance to requirements.” 3. Each of these definitions provides a unique lens through which to understand and evaluate quality, reflecting the multifaceted [many-sided] nature of quality in product and service. They highlight various aspects of quality including compliance with standards, customer satisfaction, comparative excellence, and fitness for intended use. 4. We must know the distinction between two terms; Output and Outcome, within the context of a process or an organization, emphasizing that Quality is more about the Outcome rather than just the Output. 4 RESTRICTED RESTRICTED (a) Output. It refers to the direct and tangible products or services produced as a result of a process or activity within an organization. It‟s the immediate result that comes from a set of inputs and activities. For example, in a manufacturing process, the output would be the number of goods produced. (b) Outcome. It refers to the broader impact or the long-term effects that the output has on a larger scale, often on the organization as whole or its customers. It‟s the ultimate goal or the reason why a process is carried out. For example, in the same manufacturing scenario, the Outcome could be the level of customer satisfaction and the market reputation the products earn for the company. Need for Quality 5. Quality is an essential aspect of any product or service. It ensures that the product or service meets the customer's requirements. Quality helps in building trust and loyalty among customers, which is critical for any organization's success. Implementing a Quality Management System (QMS) has proven to be cost-effective for many companies. For instance, Chinese factories, initially doubtful about QMS, have realized that the total costs of quality can amount to 25-35% of sales. By adopting preventive activities, improving processes, and detecting quality issues earlier, companies have saved substantial amounts. Notably, these Industries reduced costs as a percentage of sales and saved millions of dollars. Fig 1.1: Yearly savings of companies by implementing QMS 6. A question comes to our mind as to who can be a customer for a military organization such as PAF. PAF personnel can consider its stakeholders as its “customers”. Stakeholders can include AHQs, Concerned Directorates, Aircrew, Flt lines, Backup shops, Airmen, and Civilians to whom you are providing services. 5 RESTRICTED RESTRICTED Brief History 7. The concept of quality has been around for centuries. The ancient Egyptians used to inspect the quality of their food and drinks. While in the late 13 th century, European craftsmen began organizing into unions called guilds. These guilds [unions] were responsible for developing strict rules for product and service quality. Inspection committees enforced the rules by marking perfect goods with a special mark or symbol. At first this mark was used to track the origin of faulty items. But over time, the mark came to represent a craftsmen‟s good reputation. In the 20th century, as quality became a significant concern for businesses worldwide, the evolution of quality management can be summarized as follows: (a) 1920s.1 Some of the first seeds of quality management were planted as the principles of scientific management and these were widely adopted by the U.S. industry. Mainly, the „Hawthorne experiments‟ which were series of studies conducted in the 1920s that highlighted the effect of psychological and social factors on workplace productivity. It led to Hawthorne effect, which suggests that individuals improve their performance when they are noticed and paid attention to. (b) 1930s. Walter Shewhart developed the methods for statistical [related to numbers] analysis and control of quality. Statistical sampling techniques were used to evaluate quality, and quality control charts were employed to monitor production processes that allowed for more systematic assessment and control of quality. (c) 1950s. W. Edwards Deming taught quality methods to Japanese engineers and executives. He introduced the concept of the Deming Cycle, commonly known as PDCA (Plan-Do-Check-Act), which provided a structured framework for continuous improvement. PDCA shall be covered in detail subsequently. (d) Other Contributors. Joseph Juran, another leader in quality management, proposed the Juran Trilogy2, comprising three vital processes for quality improvement (Quality Planning, Quality Control and Quality Improvement). Philip Crosby was also a key figure in quality management who advocated the principle of “Doing it right for the first time” and the concept of “Zero defects”, that means it is more beneficial and cost effective to prevent problem from occurring in the first place than to discover it later and fix it. (e) It is important to remember that the origin of scientific quality concepts can be traced back to USA, one of the world‟s leading industrial powers. However, these concepts became more widely adopted in Japan after World 1 Students shall not be required to remember the dates in examinations 2 Set of three related things 6 RESTRICTED RESTRICTED War II, when Japan needed to rebuild its industry. Japan realized the value of quality for its industrial revival and became a global leader in quality standards. USA, on the other hand, did not pay much attention to the quality management ideas proposed by these experts. Japan was more receptive to these ideas and quickly became a world leader in quality. (f) 1960s. Kaoru Ishikawa, a renowned Japanese quality control expert, identified seven fundamental tools essential for quality improvement efforts. These tools empower organizations to identify, analyze, and rectify quality related issues efficiently. These, often referred to as the "7 Basic Tools of Quality" are: (i) Cause-and-Effect Diagram (Fishbone Diagram). (ii) Check Sheets. (iii) Control Charts. (iv) Histograms. (v) Pareto Charts. (vi) Scatter Diagrams. (vii) Flowcharts. 8. The Japanese adopted “companywide quality control,” contributing to Japan‟s quality leadership. Ultimately, the term “quality management systems” emerged. Presently standards such as ISO 9001:2015 are being extensively used to establish QMS. Fig 1.2: Evolution of Quality Quality Journey in Pakistan 9. Let‟s have insights into how Quality Management practices have matured overtime in Pakistan, reflecting a growing emphasis on continuous improvement and excellence across different sectors. (a) 1980s - Inspection/Testing in Big Industries. During the 1980s, the focus was primarily on inspection and testing within big industries such as 7 RESTRICTED RESTRICTED Automobile, Defence, Engineering and Textile. This phase represents the early stages of quality awareness where the emphasis was on detecting and correcting defects. (b) 1990s – ISO standard Adoption. In the 1990s, there was a shift towards adopting International Standard Organization (ISO) standards across various sectors including Automobile, Telecom, Banks, Software, Engineering and Universities. This period marked a move towards a more standardized approach to quality management. (c) 2000s – TQM Growth. The 2000s saw the growth of Total Quality Management (TQM) and Total Productive Maintenance (TPM) practices. These methodologies focus on continuous improvement and involve everyone in the organization in a collective effort to improve performance and quality. (d) 2010s – Advanced Quality Methodologies. In the 2010s, more advanced quality methodologies like Six Sigma3 were introduced, along with the establishment of Quality Control Circles (QCCs) in few of the schools. Additionally, the Higher Education Commission (HEC) initiated self- assessment practices to further promote quality in education. Quality Management 10. There are three main areas associated with quality management: (a) Quality Control (QC) (b) Quality Assurance (QA) (c) Quality Management System (QMS) 11. These are covered in detail in the following paragraphs: (a) Quality Control (QC). QC involves a series of activities aimed at verifying whether a product or service meets a predefined standard of quality. It emphasizes on identifying defects or deviations from the expected quality level after the product or service is produced or delivered. The primary goal of QC is to detect any discrepancies or issues and ensure that the final output aligns with the desired quality level. (b) In the context of QC understanding the term „product‟ is very important. It refers to the physical item or system that is being maintained. This could be a piece of machinery, a building, a software system, or any other item. The product is the tangible output that needs to be kept in good working condition. For example, in an aircraft maintenance scenario, the aircraft itself is the product. 3 Six Sigma will be explained in the next chapter. 8 RESTRICTED RESTRICTED (c) Quality Assurance (QA). QA encompasses a range of activities designed to ensure that a product or service adheres to the specified requirements throughout its development or production process. It places emphasis on preventing defects or deviations from the defined quality standards from occurring in the first place. The main objective of QA is to establish robust (unlikely to fail) processes, guidelines, and standards that, when followed, lead to the creation of high-quality products or services. These „high-quality products or services‟ fall under the scope of QC. So, it can be said that QC is narrow in scope and is a subset of QA. (d) We have already covered that focus of QC is the end product, whereas QA focusses on the entire process of producing products. Lets‟ have a deeper insight [knowledge] into the term „process‟. It refers to the set of activities or procedures carried out to maintain the product. This could involve routine checks, repairs, replacements, and other tasks necessary to keep the aircraft in optimal condition. The process is often planned and scheduled to ensure effective and efficient maintenance. An example may help us better understand the terms. (e) Snr Tech Qasim, an airframe technician is deployed in airframe accessory shop. His job is to check leakage in hydraulic components. He uses a tester for this job. He is experienced and confident so like many of his friends does not like to consult the Technical Orders (TOs). Chf Tech Ali, the QC inspector verifies on a particular day that all the hydraulic components checked by Qasim are free from any leaks. So as per Ali there are no issues and QC has no problems since all products are defect free. What do you think how a QA evaluator would react if he comes to know that Qasim did not use relevant TOs, while undertaking this activity. Moreover, what do you think, might happen if this practice is continued? You see, one day Qasim can make a mistake because of his bad habit of not consulting his TOs. QA will not let that happen because a part of the process is not going as per the plan. (f) Quality Management System (QMS). QMS is a set of policies, processes, and procedures required for planning and executing operational activities that ensure customer satisfaction through consistent product/service quality. QMS and CQI (Continuous quality improvement) are inter-related concepts in quality management. QMS provides the framework and structure for CQI that involves identifying opportunities for improvement, implementing changes, measuring outcomes, and making further adjustments as needed. It is evident that QMS is even broader in scope than QA. It provides a framework which leads to both QC and QA. For example, AHQ provides policies, guidelines, organizational framework, resources for conduct of QC and QA activities. It also expresses the organizational commitment to pursue Quality. All these things combine to form a QMS. So, we may conclude that QMS includes QC and QA as its subsets. 9 RESTRICTED RESTRICTED Fig 1.3: Relationship of QC, QA and QMS Differences between QC and QA 9. QA and QC are both necessary when it comes to managing quality. QA is about "doing things right," and QC is about "ensuring things were done right." Brief comparison between QA and QC is given in the following table: Aspect Quality Control (QC) Quality Assurance (QA) Performed after product Involved throughout Timing manufacturing/Service delivery development phase Planning and ensuring Focus Inspecting and correcting process setup Preventive, aiming to avoid Approach More reactive defects to occur Correction, Corrective action and Preventive action 10. In the field of quality management, three key concepts play a vital role in ensuring consistent and improved quality; Correction, Corrective Action, and Preventive Action. To understand these concepts, let‟s take an example of Mobile phone not coming „ON‟ when you install its battery. (a) Correction. It involves rectifying a detected problem or defect to meet the specified requirements. This is the immediate action taken to fix the problem or defect. For example, you can remove the battery from the mobile, check the polarity markings on the battery and the device, and reinstall the battery correctly. After these actions mobile comes on and the defect has been corrected. 10 RESTRICTED RESTRICTED (b) Corrective Action. It is a systematic approach to identify, analyze, and eliminate the root cause of a nonconformity or an undesirable situation and avoid it from happening again. For example, you can investigate why the battery was installed incorrectly in the first place, such as human error or unclear labeling. You can then take measures to address the root cause, such as providing training or labeling the battery. These steps resolve the root cause and constitute a corrective action. (c) Preventive Action. It involves practically identifying and eliminating potential causes of problem or defect to prevent them from occurring in the other devices also. For example, you can identify other devices or batteries that may have the same risk of reverse polarity, and check them for proper installation. You can also implement controls or safeguards to prevent reverse polarity, such as using keyed connectors, color-coded terminals, or polarity indicators. (d) It is pertinent [relevant] that we generally confuse correction with corrective action in PAF. For example, if there is an observation by the QA evaluator that there is a fuel spillage under the aircraft. We generally record the corrective action as „The fuel spill has been cleaned and supervisor has been briefed‟. This is just a correction; corrective action implies investigation why did the fuel spill happen and identification of the root causes such as shortage of drip trays, poor work ethics of personnel or some defects in the fuel system etc. Complete corrective action would require eliminating the root cause and not just the defect. 11. In short, correction is a reactive approach that fixes the problem after it happens, corrective action is an analytical approach that digs deeper to find the root cause of problem and prevents the problem from happening again, and preventive action is a defensive approach that prevents the same problem from happening in other similar systems or occurrences. Activities of QC and QA 12. QC / QA activities are interrelated, but they are defined differently. Typically, QA activities cover much of the quality system, while QC is a subset of QA activities. Here are some examples of QA and QC activities: 13. Quality Control (QC) Activities include: (a) Inspecting raw materials, components, and finished products to ensure they meet quality standards. (b) Conducting tests and measurements to verify product performance. (c) Documenting non-conformances and implementing corrections. (d) Conducting final inspections before products are shipped to customers. 11 RESTRICTED RESTRICTED Fig 1.4: QC inspector conducting final inspection 14. Quality Assurance (QA) Activities include: (a) Developing and implementing quality policies and procedures. (b) Conducting internal audits to ensure compliance with quality standards. (c) Providing training to employees on quality management principles. (d) Establishing and maintaining a document control system. (e) Performing risk assessments to identify potential issues (f) Conducting customer satisfaction surveys to gather feedback. (g) Developing and implementing corrective action plans to address quality issues. Roles of QA and QC with examples in different scenarios 15. Example 1. In case of wrong blood reports in the hospital, QA and QC play different roles in preventing, detecting, and correcting the errors. For example: (a) QA ensures that the laboratory has a clear policy and procedure for sample identification, labeling, handling, storage, and transportation. QA also ensures that the laboratory staff is trained and competent in following the protocol and documenting any incidents or deviations. (b) QC ensures that the laboratory instruments are calibrated before use. QC also ensures that the control materials are appropriate and stable for the test parameters. QC detects any diagnostic errors or shifts in the test results. 16. Example 2. In aircraft landing gear replacement activity Quality Assurance (QA) establishes procedures and standards for landing gear replacement. It includes 12 RESTRICTED RESTRICTED training maintenance personnel to follow these procedures consistently. Regular reviews and updates of procedures are part of QA. Fig 1.5: QA inspector conducting inspection 17. On the other hand, Quality Control (QC) inspects the replaced landing gear to ensure correct installation. Functionality tests verify that the new gear operates as expected. It documents the results of inspections and tests for future reference. If any issues are detected during QC, corrective actions are taken promptly. 18. Example 3. In the context of an aircraft inspection before flying, Quality Assurance (QA) would be involved in ensuring that the inspection process itself is robust and effective. This could involve: (a) Making sure that the inspection checklist or procedure is comprehensive and up-to-date. (b) Ensuring that the personnel performing the inspection has the necessary training and qualifications. (c) Checking that all necessary tools and equipment for the inspection are available and in good working condition. 19. On the other hand, Quality Control (QC) would be involved in checking the results of the inspection. This could involve: (a) Reviewing the completed inspection checklist to ensure all items have been checked and any issues have been noted. (b) If any issues were identified during the inspection, QC would check that these have been addressed correctly. (c) QC might also involve additional checks or tests on critical components of the aircraft, especially if any issues were identified during the inspection. 13 RESTRICTED RESTRICTED 20. With so much discussion we should now be able to handle a small case- study. We discuss this case because what you have learnt uptil now may seem to be in conflict with how PAF ensures quality. At flight lines of Alpha squadron pre-flight of 10 aircraft is done. The process of pre-flight requires many activities to be completed such as towing, refueling, visual inspections, arming the aircraft. The pre-flighted aircraft is a product of this process. Procedure requires that 2 / 10 pre-flighted aircraft are to be checked by QA personnel. So, our friend Snr Tech Saqlain who at QA squadron is asked to perform a Quality Verification Inspection (QVI). In your opinion who should carry out this inspection QA or the QC? Remember the pre- flighted aircraft is a finished product of a set of maintenance activities. 21. The answer is that Quality Verification Inspection falls in the domain of QC. But in PAF because of its organizational structure, QA squadron is tasked to do it. This is not a problem since QC is a subset of QA. QA squadrons were established much earlier than QC Flts and have a broader role. QA squadrons therefore do undertake QC activities but QC Flts are generally restricted to QC activities only. At times OC Engineering may also task QC Flts to undertake QA roles for special tasks but these are restricted within Engineering wing. 14 RESTRICTED RESTRICTED CHAPTER 2: QUALITY IMPROVEMENT METHODOLOGIES Desired Learning Objectives 1. After learning this chapter, students will be able to: (a) Explain the key principles of integrated methodologies of quality systems including Six Sigma and Lean Manufacturing. (b) Identify practical applications of Kaizen in different work environments. (c) Compare different type of tools used for quality improvement. "Quality is never an accident; it is always the result of intelligent effort." John Ruskin Introduction 2. Quality management systems make organizations, earn profit, grow and deliver safe products. Owners know this and often want the best strategies and practices for achieving quality. By combining strategies like Six Sigma and Lean, organizations can equip individuals to create a complete system that maximizes efficiency, minimizes waste, and consistently delivers products and services of superior quality. These are not just tools; they represent transformative [able to bring change] philosophies that have revolutionized the industries. Fig 2.1: Quality Methodologies 3. As shown in the figure 2.1, we shall basically cover two major methodologies of Quality management i.e. (a) Six Sigma (b) Lean Philosophy 15 RESTRICTED RESTRICTED 4. Six Sigma and Lean are both powerful methodologies for process improvement, but they focus on different aspects as given in the following table: Six Sigma Lean It is about improving quality through It is primarily about eliminating waste data-driven decision-making and reduction and improving efficiency. of defects. It is important when process It is most effective when there is a need to inefficiencies result in delays or reduce variability and improve quality. wasted effort It focuses on effectiveness through quality It focuses on efficiency through improvement waste reduction 5. We often use the words effectiveness and efficiency interchangeably, however both have different meaning. The effectiveness refers to the degree to which a product or service meets the stakeholders‟ requirements. It‟s about doing the right things and achieving the desired results. For example, in a PAF Hospital setting, effectiveness could be measured by the recovery rate of patients, patient‟s satisfaction, or the accuracy of diagnoses. A high recovery rate and high patient satisfaction would indicate that Hospital is effective, providing Quality Health care services. 6. The efficiency refers to the degree to which the process produces the required output at a minimum resource cost. It‟s about doing things right with less expenditure of resources. This is called resource optimization for achieving the output. For example, in a manufacturing plant, efficiency could be measured by the ratio of output produced to the input resources used. A higher ratio would indicate that the plant is efficient in converting resources into products with minimal waste. Six Sigma: A Paradigm [Model] of Precision and Excellence 7. In today's dynamic world, the pursuit [struggle] of quality has become a defining factor for organizational success. A key methodology for achieving this is Six Sigma. Originating in manufacturing and subsequently finding applications across various industries, Six Sigma stands as a powerful tool for process improvement and quality enhancement. 8. At its core, Six Sigma is a data-driven methodology aimed at reducing defects, minimizing variations, and enhancing process performance. The term "Sigma" represents a statistical [related to numbers] measure of variability, and the goal of Six Sigma is to achieve a level where only 3.4 defects occur per million opportunities for each product or service. Do you think it is achievable? This level of precision shows the commitment to excellence that Six Sigma represents. Six Sigma is an ideal and a goal, much is required to be done in terms of quality to achieve this ideal. A number of approaches can be used to achieve, or at least try to achieve Six Sigma. A five-step approach known as DMAIC is generally used to achieve Sig Sigma. 16 RESTRICTED RESTRICTED 9. DMAIC. It is an abbreviation for Define, Measure, Analyze, Improve, and Control. These actually signify the steps of the DMAIC process. This structured [planned / organized] approach provides a roadmap for process improvement. Recall from chapter 1, the definition of process i.e. a series of actions or steps taken to achieve a particular outcome. For example, the process of baking a cake involves several steps such as gathering ingredients, mixing them in a specific order, baking the mixture in an oven, and finally, decorating the cake. Each step is crucial and contributes to the final product, which is the baked cake. This concept is fundamental in process improvement methodologies like DMAIC (Define, Measure, Analyze, Improve, Control), where each step in a process is examined to identify and eliminate inefficiencies or defects. Here in order to improve the process we must undertake the following activities (We will use an example of and SNCOs‟ Mess that illustrates the application of DMAIC methodology in to the problem of delay in service): (a) Define. This initial phase involves identifying the problem, understanding customer requirements, and setting clear, measurable objectives. It establishes the foundation for the entire improvement process. In the case of Mess, the problem is the delay in service. This could be defined more specifically as “meals are not ready at the scheduled times” or “it takes too long for personnel to receive their meals after their arrival”. (b) Measure. In this phase, data is collected to quantify the current state of the process. Statistical tools and techniques are employed to assess process performance and identify areas for improvement. For the Mess, this could involve tracking the time it takes for meals to be prepared and served, and the time personnel spend waiting for their meals. It‟s important to collect reliable data on the process as it currently works. (c) Analyze. The data collected is then studied to identify root causes of defects or variations. This phase aims to gain a deep understanding of the underlying processes and their contributing factors. For Mess, this might involve looking at the workflow in the kitchen, the scheduling of meal times, the number of personnel served at each meal, etc. The goal is to identify where the delays are occurring and why. (d) Improve. Based on the understandings gained from the analysis, improvements are implemented to address the identified issues. The focus is on optimizing processes to meet or exceed customer expectations. In the case of Mess, this might involve changes to the kitchen workflow by providing more serving counters, providing trolleys for crockery shifting, detailing more waiters at peak times, adjusting the meal schedule, and additional training for kitchen staff, etc. The specific improvements will depend on the results of the analysis. (e) Control. The final phase involves putting in place measures to sustain the improvements achieved. Control mechanisms are established to monitor 17 RESTRICTED RESTRICTED process performance and ensure continued adherence to quality standards. This might involve ongoing monitoring of meal preparation and service times, regular feedback sessions with kitchen staff, etc. (f) For example, if the analysis step revealed that delays were occurring because of a bottleneck in the food preparation process, an improvement might be to rearrange the kitchen workflow to eliminate the bottleneck. The control step would then involve monitoring the new workflow to ensure it‟s working as intended and that the improvements are sustained. (g) Remember, the key to DMAIC is data, because each step involves collecting and analyzing data to understand the problem and identify effective solutions. It‟s also a cyclic process - once you‟ve gone through the DMAIC process for one problem, you can start it again for the further improvement. This continuous improvement is what makes DMAIC such a powerful tool for quality improvement. Fig 2.2: DMAIC framework 10. Data-driven decisions and Supervisors. Data-driven or evidence-based thinking is where military commanders sometimes fail. They are not accustomed to listening to „No‟, they develop a false belief of always being right and gradually they start ignoring data or facts. Being supervisors, you must always try and gather data behind a problem followed by an analysis before taking a decision and implementing it. Benefits of Six Sigma. 11. By targeting the root causes of defects, Six Sigma leads to a significant reduction in errors and defects, resulting in higher quality products or services as well as reducing substantial cost savings. This leads to increased customer satisfaction and loyalty. As Six Sigma relies on data analysis and statistical tools for process optimization, ensuring that decisions are based on evidence rather than intuition [instinct / sixth sense]. Implementing Six Sigma often necessitates a cultural shift towards a focus on quality and continuous improvement leading to a more empowered and engaged workforce 18 RESTRICTED RESTRICTED 12. The concept of Six sigma originated in 1980 and it is because of its success that it is still a powerful strategy for Quality management. We have seen that we can apply this concept in our day to day life in PAF. In fact, this approach can prove to be very effective at the organizational level. 13. In Six Sigma, variability or variation is considered the enemy as it can introduce waste and errors into a process. It is defined as a lack of consistency. It may be understood by the following example, if you‟re manufacturing an item, you want the parameters to be the same in every single item you produce. Material strength, length, and diameter must be uniform. Your customers also want a level of consistency. The differences between multiple instances of a single product are referred to as variation. 14. Variation can be measured in several ways, including the range (the difference between the highest and lowest values in a set of data) and standard deviation (the average distance between all the data points and the mean of your data set). 15. Variation can creep into any or all elements of a process due to factors such as wear and tear in a machine, changes in a process, measurement mistakes, variations in material quality or makeup, environmental changes, or unpredictable work quality. In most industries, focusing on decreasing fluctuations in processes increases performance by limiting factors that cause inconsistent results. Lean Philosophy: Streamlining Processes for Operational Excellence 16. Originating from the Toyota Production System (TPS), Lean offers a systematic approach to eliminating waste and optimizing processes across various industries. It emphasizes creating more value with fewer resources, which ultimately leads to increased efficiency and higher quality outputs. Keep in mind that Six sigma was focused on eliminating defects and efficiency was not a major concern. As opposed to that methodology, Lean targets waste reduction so that we achieve efficiency as well as effectiveness. Fig 2.3: Lean Philosophy 19 RESTRICTED RESTRICTED Key Principles of Lean 17. Following are the key principles of Lean philosophy: (a) Value. The first principle of Lean is identifying what is valuable to the customer. This involves understanding customer needs and preferences, and ensuring that resources are allocated to deliver that value. (b) Value Stream. Value stream mapping is a critical component of Lean. It involves analyzing the entire process from raw materials to delivery of the final product or service. By visualizing the flow of value, organizations can identify areas of improvement and waste reduction. (c) Flow. Lean emphasizes creating a seamless [smooth] flow of work through the value stream. This involves eliminating bottlenecks and interruptions in the process to ensure a steady and efficient workflow. (d) Pull. Rather than pushing products or services onto the market, Lean advocates for a pull system where production is driven by actual customer demand. This helps in preventing overproduction and excess inventory. (e) Perfection. The pursuit of perfection is a core principle of Lean. It acknowledges that true perfection is a continuous journey and encourages organizations to strive for it by eliminating waste and constantly improving processes. Tools and Techniques of Lean 18. Lean Manufacturing uses a variety of tools and techniques to achieve its objectives: (a) Kaizen. Kaizen, or continuous improvement, is a fundamental concept in Lean. It involves making small, incremental [step by step] changes to processes in order to achieve continuous improvement over time. (b) 5S Methodology. The 5S methodology (Sort, Set in Order, Shine, Standardize, Sustain) is a powerful tool for workplace organization and efficiency, which complements the principles of Lean. (c) Just-In-Time (JIT). JIT is a production strategy where materials are delivered just in time for production i.e. only when they are required, reducing the need for excess inventory and storage. Benefits of Implementing Lean 19. The adoption of Lean Manufacturing yields many benefits for organizations: (a) Waste Reduction. Lean focuses on eliminating waste, which can result in significant cost savings and increased efficiency. 20 RESTRICTED RESTRICTED (b) Increased Productivity. By optimizing processes and reducing unnecessary steps, Lean leads to higher levels of productivity. (c) Enhanced Quality. Lean principles and techniques lead to a reduction in defects and an improvement in overall product or service quality. (d) Improved Customer Satisfaction. By delivering value more efficiently, organizations are better able to meet customer needs and expectations. Types of Waste (Muda) in Lean 20. In Lean philosophy, there are typically eight types of waste, often remembered by using the acronym "DOWNTIME". These wastes represent activities that do not add value to the final product or service and should ideally be minimized or eliminated. Here they are: (a) Defects. Products or components that don't meet quality standards, requiring rework or disposal e.g. if a product is produced with a manufacturing defect, it will require additional time and resources to fix or scrap. (b) Overproduction. Producing more than what is immediately required by the next process or by customer demand. It's considered a waste because it ties up resources (materials, labor, equipment) in producing goods that might not be needed right away. Overproduction can lead to excessive inventory. (c) Waiting. Time spent by employees or processes waiting for the next step in a workflow e.g. if a machine operator has to wait for a specific tool or part before they can proceed, it leads to idle time. (d) Non-utilized Talent / Unused Talent. Not fully utilizing the skills, knowledge, and creativity of employees e.g. if employees are not given opportunities to contribute their ideas or expertise, it's a waste of their potential. (e) Transportation. Unnecessary movement of materials or products between processes or locations e.g. Coal fired electric plant at Sahiwal has to be supplied with coal shipped from Karachi. Locating this plant close to the port could have saved it from excessive transportation but there are of course other administrative reasons for this decision. (f) Inventory. This includes raw materials, work-in-progress, and finished goods that are in excess of what is needed for immediate use or demand. Inventory can be a result of overproduction, but it can also occur for other reasons, such as poor production scheduling or inaccurate demand forecasts. Considering overproduction and inventory separately, helps organizations pinpoint the specific causes and solutions for each. 21 RESTRICTED RESTRICTED Fig 2.4: Different types of Waste (g) Motion. Unnecessary movement of people within a workspace e.g. if a worker has to repeatedly reach for a tool or walk long distances between workstations, it's considered wasteful motion. (h) Excess Processing / Over Processing. Doing more work on a product than what's required by the customer e.g. adding extra features or processing steps that the customer doesn't value or need. For example, you are writing a loose minute for issuance of keys. You write a two-page document and use lots of difficult words. Of course, you work hard on it. However, such detail is not required. The effort you have put in was just not required so you have over processed a simple document. Kaizen: The Path to Continuous Improvement 21. In the continuous struggle for excellence; organizations seek methodologies that create a culture of continuous improvement. One such philosophy that has gained prominence in the world is Kaizen. Originating from Japan, Kaizen represents a commitment to incremental, continuous improvement in all aspects of an organization. It has become a powerful tool for driving positive change and achieving operational excellence. 22. Kaizen, which translates to "change for the better" is a philosophy that emphasizes making small, continuous improvements in processes, products, and services. It encourages employees at all levels of an organization to actively participate in identifying and implementing improvements, regardless of their magnitude. The essence of Kaizen lies in its belief that even the smallest changes can lead to significant advancements over time. 22 RESTRICTED RESTRICTED Key Principles of Kaizen 23. Following are the key principles of Kaizen: (a) Continuous Improvement. At the heart of Kaizen is the idea that improvement is an ongoing, never-ending process. It rejects complacency and encourages an untiring pursuit of excellence. (b) Empowerment of Employees. Kaizen empowers employees to take ownership of their work processes. It encourages them to identify areas for improvement and take initiative in implementing changes. (c) Waste Elimination. Kaizen focuses on eliminating waste in all forms, including time, resources, and effort. This leads to increased efficiency and productivity. (d) Standardization. While Kaizen emphasizes change, it also recognizes the importance of establishing and adhering to standardized processes. This ensures that improvements are sustained over time. (e) Teamwork and Collaboration. Kaizen promotes a culture of collaboration where teams work together to identify and implement improvements. It fosters a sense of unity and shared purpose among employees. For this it provides the concept of „Obeya Room‟. Obeya is a Japanese term that translates to "big room" or "war Fig 2.5: Obeya Room room." It refers to a physical space where cross-functional teams gather to collaborate, communicate, and make decisions about a specific project or process improvement initiative. The Obeya room is designed to facilitate real- time communication, visual management, and problem-solving. Tools and Techniques of Kaizen 24. Kaizen employs various tools and techniques to facilitate the process of continuous improvement: (a) PDCA Cycle. The Plan-Do-Check-Act cycle provides a systematic framework for problem-solving and implementing changes in a controlled and iterative manner. PDCA cycle is also part of other Quality Fig 2.6: The PDCA Cycle management strategies and systems such as ISO9001:2015 so if you see it somewhere else, don‟t be surprised. 23 RESTRICTED RESTRICTED (b) Gemba Walks. Gemba walk is a management practice originating from Japanese business philosophy, particularly within Lean and Kaizen methodologies. It involves leaders or managers going to the "Gemba," which means the actual workplace. The purpose of a Gemba walk is to observe, understand, and engage with the employees and activities on the ground, promoting identification of operational issues and improvement opportunities. More details of Gemba Walks will be given in the upcoming paragraphs. (c) 5 Whys. This technique involves repeatedly asking "why" to dig deep into the root causes of a problem, rather than addressing only the symptoms. (d) Poka Yoke. a Japanese term meaning "mistake-proofing" or "error prevention," refers to a concept that aims to design processes and systems in a way that minimizes the likelihood of human errors. It involves implementing fool proof mechanisms and safeguards to prevent mistakes at various stages of production or operation. By incorporating Poka Yoke principles, organizations enhance overall efficiency and reduce defects, fostering a culture of continuous improvement and ensuring higher product or service quality. For example, in manufacturing, using color-coded components or shapes that fit together uniquely ensures correct assembly. In software development, automated error-checking tools help prevent coding mistakes. Retail checkout systems incorporate Poka Yoke with barcode scanners to ensure accurate product identification. Even in daily life, smartphone charging cables designed to fit into charging ports in only one orientation are a consumer-friendly Poka Yoke example, preventing connection errors. (e) Quality Control Circles (QCC). These are small group of employees who voluntarily come together to solve specific quality related problems. These circles empower employees, promoting team work, and harnessing collective expertise to improve process. Benefits of Implementing Kaizen 25. The adoption of Kaizen yields a multitude of benefits for organizations: (a) Increased Productivity. Kaizen leads to improved processes, which result in higher levels of productivity and efficiency. (b) Cost Savings. By eliminating waste and optimizing processes, organizations can realize significant cost savings. (c) Employee Engagement and Satisfaction. Kaizen empowers employees to take ownership of their work and contribute to the improvement process. This leads to higher levels of job satisfaction and engagement. 24 RESTRICTED RESTRICTED (d) Enhanced Quality. The focus on continuous improvement leads to higher quality products and services, ultimately benefiting customers. The 5S Methodology: Transforming Workspaces for Efficiency 26. Originating from Japanese manufacturing practices, 5S offers a structured approach to creating and maintaining an organized, clean, and efficient workspace. The term "5S" represents a set of five Japanese words, each starting with the letter 'S': Seiri (Sort), Seiton (Set in Order), Seiso (Shine), Seiketsu (Standardize), and Shitsuke (Sustain). Together, these elements form a comprehensive strategy for workplace optimization. These are explained below. (a) Sort (Seiri). The first step involves separating essential items from non-essential ones. It involves a critical examination of tools, materials, and equipment to remove unnecessary clutter [disorder in pattern of things]. By eliminating unnecessary items, organizations free up valuable space and reduce the risk of errors or delays caused by misplaced items. (b) Set in Order (Seiton). This step focuses on arranging the remaining items in a logical and easily accessible manner. Tools and materials are organized based on frequency of use and workflow, ensuring that employees can locate and retrieve them efficiently. Proper labeling and clear visual cues play a crucial role in this stage. (c) Shine (Seiso). This step emphasizes cleanliness and regular maintenance. Workspaces are thoroughly cleaned and inspected to identify and address potential issues. A clean and well-maintained environment not only enhances safety but also promotes a culture of pride and ownership among employees. (d) Standardize (Seiketsu). Standardization involves establishing clear and consistent procedures for maintaining the first three S's. Standard operating procedures (SOPs) are documented, and regular audits are conducted to ensure adherence to the established standards. This step ensures that the improvements made are sustained over time. (e) Sustain (Shitsuke). Sustaining [maintaining / keepin] the improvements achieved through the first four steps requires ongoing commitment and discipline. Regular training, audits, and continuous improvement initiatives are implemented to reinforce the 5S principles and maintain the organized workspace. 25 RESTRICTED RESTRICTED Fig 2.7: 5S Methodology Benefits of Implementing 5S 27. The adoption of the 5S methodology yields a range of benefits for organizations: (a) Improved Quality and Efficiency. By organized workspace, reducing waste, eliminating unnecessary steps, and streamlining workflows, 5S leads to significant improvements in quality, productivity and efficiency. (b) Enhanced Safety. A clean and organized workspace reduces the risk of accidents and injuries, creating a safer work environment for employees. (c) Greater Morale and Engagement. A well-organized and clean workspace fosters a sense of pride and ownership among employees, leading to increased morale and higher levels of engagement. (d) Cost Savings. 5S reduces the need for excess inventory and minimizes downtime caused by disorganization or inefficiency, resulting in cost savings. Fig 2.8: Implementing 5S (Before and after) 26 RESTRICTED RESTRICTED Just-in-Time (JIT) Methodology: Rationalizing Operations for Efficiency 28. One methodology that has revolutionized production processes is Just-in-Time (JIT). Originating from the Toyota Production System (TPS), JIT has become a foundation of Lean principles, offering a systematic approach to optimizing operations. It focuses on delivering the right amount of materials, at the right time, and in the right sequence to meet customer demand. The core principle of JIT is to eliminate waste by synchronizing production with actual customer demand, thereby minimizing excess inventory and associated costs. It is the opposite of „Just-in-Case (JIC)‟ approach that focuses on keeping extra inventory on hand in case of fluctuations in demand or supply. The issue with JIC is that problems are often hidden in the inventory whereas JIT allows them to be seen clearly. 29. For example, in an Orderly Room of a Unit, Just-in-Time (JIT) would involve ordering stationery only when it‟s about to run out, ensuring minimal inventory at hand but also no work disturbances. On the other hand, Just-in-Case (JIC) would involve keeping a large stock of stationery items on hand to be ready for any unexpected increase in usage or supply chain variations. Key Principles of JIT 30. The key principles of Just-in-Time (JIT) are often referred to as the Five Zeros: (a) Zero Stock: At every step of the production process, products must arrive at just the right moment of utilization. (b) Zero Delay: To increase flexibility, each step in the process should take the least amount of time possible. (c) Zero Failure: All machines should ideally operate continuously with controlled performance. (d) Zero Defect: Part defects can require extra corrective processing or even result in scrapping the part altogether. (e) Zero Paper: Bureaucratic procedures and steps obviously weigh down manufacturing and production processes. 27 RESTRICTED RESTRICTED Tools and Techniques of JIT 31. JIT manufacturing employs various tools and techniques to facilitate its implementation: (a) Kanban System (b) Small Batch Production (c) Multi-Skilled Workforce 32. Now we‟ll see these tools and techniques in detail: (a) Kanban System. It is a project management methodology originating from Japan that utilizes a visual board with cards or sticky notes representing tasks, each moving through different stages of a workflow. The system provides real-time visibility into work progress, enabling teams to manage and optimize their processes more effectively. Kanban promotes a pull-based approach, allowing team members to pull new tasks only when they have the capacity, minimizing bottlenecks and enhancing overall workflow agility. (b) In any unit of PAF, Kanban can be effectively applied to manage different tasks and optimize workflow. Imagine a Kanban board divided into columns representing different stages of the task, such as "To-Do," "In Progress," and "Completed." Each task is represented by a card on the board. When a piece of work is to be done, a task card is placed in the "To-Do" column. As workers start working on tasks, cards move to the "In Progress" column. Upon completion, the cards are shifted to the "Completed" column. (c) This visual representation allows the team to quickly assess the status of ongoing work, identify bottlenecks, and allocate resources efficiently. The Kanban system ensures that the tasks are done in a timely manner while providing a transparent and adaptable framework for continuous improvement in the processes. (d) Small Batch Production. JIT encourages producing goods in smaller, more manageable batch sizes. This reduces setup times, enables quicker response to changes in demand, and helps maintain a steady workflow. (e) Multi-Skilled Workforce. Cross-training employees to perform multiple tasks or operations enhances flexibility in production. This allows for a more 28 RESTRICTED RESTRICTED adaptive [able to adjust] response to changes in demand or production schedules. Benefits of Implementing JIT 33. The adoption [acceptance] of JIT manufacturing results into a multitude of benefits for organizations: (a) Waste Reduction. JIT minimizes excess inventory, which in turn reduces storage costs and the risk of obsolescence. (b) Increased Productivity. By synchronizing production with customer demand, JIT leads to higher levels of productivity and resource utilization. (c) Cost Savings. Reduced inventory levels and streamlined processes result in significant cost savings for organizations. (d) Improved Quality. JIT encourages a focus on quality at every stage of production, leading to higher-quality outputs. The “5 Whys”: Unearthing [uncovering] the Root Causes of Challenges 34. The "5 Whys or Why-Why" is a problem-solving technique that originated from the Toyota Production System (TPS), a key component of Lean Philosophy. It is a simple yet powerful approach used to get to the root cause of a problem by asking "why" repeatedly. The goal is to identify the underlying issues rather than just addressing the symptoms. Steps of 5 Whys 35. Here's how the technique works: (a) Step 1: Identify the Problem. Begin by clearly defining the problem or the issue you want to address. This should be a specific and observable problem, such as a defect, a delay, or an inefficiency in a process. (b) Step 2: Ask "Why?". Ask why the problem occurred. This question prompts you to look beyond the immediate cause and consider what factors contributed to the issue. The answer you get is typically the immediate cause or symptom of the problem. (c) Step 3: Repeat the Question. For each answer you receive, ask "why" again. This process is repeated as many times as necessary to dig deeper into the causes. The idea is to keep asking "why" until you reach a point where further questioning is no longer productive. (d) Step 4: Identify the Root Cause. The final "why" question often leads to the identification of the root cause (the fundamental reason behind the 29 RESTRICTED RESTRICTED problem). This is the point at which you can act to address the underlying issue. (e) Step 5: Implement Solutions. Once you have identified the root cause, you can develop and implement solutions to address it. These solutions are designed to prevent the problem from recurring in the future. Example Application of the 5 Whys Technique 36. Let's illustrate the 5 Whys technique with an example: Problem: Products are consistently being produced with defects. (a) Why are there defects in the products? Because the machine is not operating correctly. (b) Why is the machine not operating correctly? Because it has not been maintained properly. (c) Why has the machine not been maintained properly? Because the maintenance schedule was not followed. (d) Why was the maintenance schedule not followed? Because the maintenance logs were not updated. (e) Why were the maintenance logs not updated? Because there was a lack of communication between shifts. 37. In this example, the root cause of the defect issue is the lack of communication between shifts. By addressing this communication breakdown, the organization can implement measures to ensure that maintenance tasks are consistently performed, ultimately reducing defects in the products. Gemba Walks: Insightful Journey to Operational Excellence Introduction 38. Gemba walk is a management practice that involves leaders or managers such as concerned Base Commanders, Officer commanding Units and Section Officer In-charges going to the "Gemba," (Actual Workplace). The purpose of a Gemba walk is to leave offices and engage with the workers and activities, promoting identification of operational issues and improvement opportunities. Gemba walks can take various forms depending on the specific objectives of the observation, for example Process Gemba Walk, Safety Gemba Walk and Employee Gemba Walk. 30 RESTRICTED RESTRICTED Benefits of Gemba Walk 39. By being physically present in the work environment, leaders can better grasp the challenges faced by teams and implement effective changes for continuous improvement. Gemba walks promote a collaborative approach to problem-solving, developing a more effective and responsive management style. For example, a manager might conduct a Gemba walk to ensure compliance with safety protocols, assess the efficiency of maintenance processes, and identify opportunities for streamlined workflows. This firsthand observation at the Gemba allows leaders to make informed decisions for continuous improvement in maintenance practices and overall operational efficiency. Structure of Gemba Walk 40. Here is the breakdown of structure typically associated with Gemba walks: (a) Preparation (i). Schedule. Gemba walks should be scheduled regularly, whether daily, weekly, or as deemed necessary by the organization. (ii). Route Planning. A specific route should be planned to cover key areas of a process. (iii). Checklist. A checklist of what to observe and questions to ask can be helpful to ensure a structured approach. (b) Execution (i). Observation. During the walk, the focus is on observing process, understanding the flow of work, and identifying any visible issue or waste. (ii). Engagement. Engage the employees, ask questions to understand their perspective and gather insights on potential improvements. (iii). Respect. Approach Gemba with a respectful attitude, appreciating the knowledge and experience of the front-line workers. Such walks should not be turned into occasions where personnel are admonished otherwise they shall never come up with their opinions. (c) Follow Up (i). Problem solving. Address the identified issues through problem solving sessions, utilizing cross functional teams if necessary and implement agreed upon improvement and monitor the results. 31 RESTRICTED RESTRICTED (ii). Feedback. Provide feedback to the teams, acknowledging their efforts and discussing the outcomes of the improvements. 32 RESTRICTED RESTRICTED CHAPTER 3: STATISTICAL PROCESS CONTROL (SPC) Desired Learning Objectives: 1. After learning this chapter, students will be able to: (a) Explain the concept of SPC and its significance in quality management. (b) Differentiate between various tools used in SPC. (c) Evaluate a given process data set and recommend appropriate SPC tools and techniques to monitor the process, justifying your choices. "Without data, you're just another person with an opinion." W. Edwards Deming Introduction 2. To implement quality management values, organizations must not only focus on process improvement but also on maintaining the gains achieved. Statistical Process Control (SPC) is a critical tool that enables organizations to monitor, analyze and control processes to ensure they remain within specified limits. By enforcing statistical techniques, it helps identify and address variations that could lead to defects or quality issues. 3. Statistical Process Control (SPC) involves collecting and analyzing data about key process variables, then utilizing visual tools like control charts to track the process's behavior over time and identify any significant deviations. Statistical analysis helps understand the causes of variation and identify opportunities for improvement, leading to the implementation of changes based on these insights. This data-driven approach finds widespread application across diverse industries, including manufacturing, healthcare, service, maintenance, and financial services. Variation in Processes 4. Processes inherently exhibit variation. Understanding the types of variation (common cause and special cause) forms the foundation of SPC. Common cause variation is inherent to the process and can be managed. It is like the background noise in a process. It's always present and results from factors like equipment wear, minor material differences, and slight changes in temperature. Think of it as the natural bumps and dips in a road. While annoying, they're expected and part of the ride. 5. Special cause variation is caused by specific, identifiable factors. It is like a sudden pothole in the road. It's unexpected and caused by specific events like equipment breakdowns, human errors, or defective materials. These sudden changes deserve attention and need to be addressed to prevent future problems. 33 RESTRICTED RESTRICTED 6. Understanding which type of variation is present is crucial for improvement of the quality. Common cause variation requires managing the contributing factors, while special cause variation demands investigation and corrective action. By identifying and eliminating these "potholes," we can smooth the road to better quality and efficiency. Fig 3.1: Variations Tools of Statistical Process Control 7. There are a lot of tools that are used to monitor, control and analyze processes. Here are some of the most important ones: (a) Control Charts. Control charts are the most fundamental tool of SPC. They provide a visual representation of process data over time, allowing organizations to distinguish between common cause and special cause variation (Figure 3.2). Control limits, derived from historical data, help identify when a process is out of control and requires intervention. Fig 3.2: Control Chart showing process behavior (b) Flow Chart. A flowchart is a picture of the separate steps of a process in sequential order. It can be used to describe various processes, such as a manufacturing process, an administrative or service process, or a project plan (Figure 3.3). 34 RESTRICTED RESTRICTED Fig 3.3: Flow Chart of TA/DA Claim Processing (c) For example, for processing of TA/DA claim, the claim is deposited to accts sqn where the pre-requisites are verified, if there is any deficiency in documents, the claim is returned to the user otherwise it is processed. A flow diagram can be used to visually represent the sequence of actions taken from the start to the end. (d) Cause and Effect Diagram (Fishbone Diagram). Cause and effect diagram, also known as an Ishikawa diagram or fishbone diagram, is a visual tool used to explore and understand the various potential causes of a specific problem or effect. It's particularly useful in identifying root causes in a structured and systematic way (Figure 3.4). (e) Cause and effect diagrams are used in a wide range of industries and fields including manufacturing, healthcare, quality control, project management, and problem-solving. They are particularly effective when dealing with complex problems that have multiple potential causes. (f) For example, in a manufacturing setting, if the main problem is defective products, the major categories might include factors like equipment, materials, processes, and human factors. Sub-causes under equipment could include issues like machine settings or maintenance, while under materials, it could involve issues related to raw materials or suppliers. By systematically analyzing these potential causes, teams can identify the most likely contributors to the problem and take targeted corrective actions. 35 RESTRICTED RESTRICTED Fig 3.4: Fishbone Diagram (g) We can understand this concept by another example of SNCO‟s Mess, that aims to improve airmen satisfaction by addressing common complaints. They use a fishbone diagram to identify potential root causes of personnel dissatisfaction, such as food quality, service speed, or cleanliness. This tool helps the Mess prioritize areas for improvement. (h) Check Sheets. Check sheets are simple data collection forms used to track the frequency of events or defects. They provide a structured way to collect and organize data for analysis (Figure 3.5). (i) For example, IT Center can use check sheets to record the number of computer related problems during inspections. The check sheet is divided into categories representing different types of defects (e.g., Network, Server, Email). Each time a defect is identified, the inspector marks a tally in the corresponding category. At the end of the inspection, the check sheet is analyzed to determine which types of defects are most common. This information helps the company identify areas for process improvement and allocate resources accordingly. Fig 3.5: IT Center Check Sheet 36 RESTRICTED RESTRICTED (j) Histograms. These display the distribution and frequency of a set of data. They provide a visual representation of variation within a process, helping to identify patterns and potential sources of variability (Figure 3.6). (k) For example, Mr. Ali owns a garden with 30 black cherry trees. Each tree is of a different height. The height of the trees (in inches): 61, 63, 64, 66, 68, 69, 71, 71.5, 72, 72.5, 73, 73.5, 74, 74.5, 76, 76.2, 76.5, 77, 77.5, 78, 78.5, 79, 79.2, 80, 81, 82, 83, 84, 85, 87. We can group the data as follows in a frequency distribution table by setting a range. (l) T 65 he n thi s da ta ca n Fig 3.6: Histogram be shown using a histogram that will help to visually understand the distribution of trees into particular groups and the frequency according to height of trees. (m) Pareto Charts. It is a specific type of bar chart that combines both bar and line graphs and helps identify the most significant factors contributing to a particular problem or situation (Figure 3.7). It is based on the Pareto Principle, also known as the 80-20 rule, which states that roughly 80% (Trivial4 Many) of effects come from 20% (Vital5 Few) of causes. (n) The bars in a Pareto chart represent individual categories or factors, arranged in descending order of frequency or impact. The line represents the cumulative percentage of the total. It starts at 0% and ends at 100%. 4 Of little importance 5 More important 37 RESTRICTED RESTRICTED TRIVIAL MANY Fig 3.7: Pareto Chart (o) Pareto charts are widely used in quality control, problem-solving, and process improvement. They help teams focus their efforts on the most critical issues, leading to more effective decision-making and resource allocation. For example, PAF‟s software development unit dealing with examination software wants to address the most significant issues causing examination department dissatisfaction. They use Pareto analysis to identify which types of bugs are responsible for the majority of complaints. This allows them to focus resources on fixing the most critical issues first. (p) Scatter Plots. These visualize the relationship between two variables (Figure 3.8). They help determine if there is a correlation between factors and identify potential cause-and-effect relationships. (q) For example, a shop tracks the sales of ice cream with rising temperature and by plotting the two (sale, temperature), it is very easily found out that there is a relationship between the two. The relationship between ice cream and temperature is quite obvious but in complex cases, this is not so easy and scatter plots are really helpful there. Fig 3.8: Scatter Plot Benefits of Statistical Process Control 8. Following are the benefits of implementing the SPC in an organization: 38 RESTRICTED RESTRICTED (a) SPC enables organizations to detect process changes early, allowing for timely intervention before defects occur or quality is compromised. (b) By focusing efforts on controlling processes, organizations can reduce the need for extensive end-product inspection, resulting in cost savings. (c) Maintaining processes within control limits leads to consistent, high- quality outputs, enhancing customer satisfaction and loyalty. Challenges and Considerations 9. SPC depends on accurate and reliable data. Ensuring the accuracy of the collected data is critical for the effectiveness of the technique. In complex processes, identifying relevant variables and establishing control limits can be challenging. Careful consideration and expertise are required. Case Studies: Real-World Applications of SPC 10. Here are some hypothetical case studies, how some of the organizations can implement the SPC: (a) PAF Aircraft Manufacturing: Reducing Defect Rates (i). Background. An aircraft manufacturing plant in PAF was experiencing high turbine failure rates on one of its transport aircraft. This was leading to costly rework impacting quality and confidence of the fleet managers. (ii). SPC Application. The plant implemented SPC techniques to monitor key process parameters during the manufacturing process. Control charts were used to track critical measurements, such as clearances between turbine blades. (iii). Outcome. With SPC in place, the team could quickly identify when the process was moving out of control. By taking timely corrective actions, they reduced the defect rate by 30%. This led to substantial cost savings and improved safety standards. (b) Healthcare: Improving Patient Wait Times (i). Background. A hospital's emergency department was facing challenges with long patient wait times, which was affecting patient experience and overall operational efficiency. (ii). SPC Application. The hospital applied SPC principles to analyze patient flow through the emergency department. They tracked metrices such as patient arrival times, triage durations (the amount of time it takes to assess and prioritize patients in a medical setting), and treatment times. 39 RESTRICTED RESTRICTED (iii). Outcome. Through SPC, the hospital identified bottlenecks and inefficiencies in the patient flow process. By making targeted process improvements, they reduced average wait times by 25%, leading to better patient outcomes and increased staff satisfaction. 11. These case studies illustrate how SPC can be applied across various departments / organizations to drive improvements in quality, efficiency, and customer satisfaction. By utilizing SPC tools and techniques, organizations can gain valuable insights into their processes, leading to better decision-making and ultimately, improved outcomes. 40 RESTRICTED RESTRICTED CHAPTER 4: KPI’S AND DASHBOARDS IN QUALITY MANAGEMENT Desired Learning Objectives 1. After studying this chapter, students will be able to: (a) Explain KPI‟s, Dashboard and their purpose using different examples. (b) Identify and select appropriate KPIs for different quality dimensions. (c) Develop a quality improvement plan based on the findings and recommendations from KPIs and dashboards “Selecting the right measure and measuring things right are both art and science. And KPIs influence management behavior as well as business culture.” Pearl Zhu, author of Digital Master Introduction 2. At its core, a KPI (Key Performance Indicator) is a measurable value that demonstrates how effectively an organization is achieving its key objectives. These objectives could range from customer satisfaction and operational efficiency to financial performance and employee productivity. Significance of KPIs 3. KPIs provide a clear picture of how well an organization is performing in critical areas. They are quantifiable parameters that provide insights into the efficiency, effectiveness, and overall performance of key processes. KPIs help align day-to-day operations with principal strategic goals. They serve as tools for identifying areas that need improvement, facilitating a culture of continuous enhancement. Selecting Relevant KPIs 4. The process of selecting KPIs is designed keeping in view the specific needs and objectives of an organization. So, the KPIs must be aligned with the strategic goals of that organization. For example, while assessing the performance of a PF&DI, it will be of no value to consider his cooking or singing skills. A KPI based on how many songs can be sung in how many ways or how many musical instruments can be played is not a valid KPI for PF&DI‟s but a perfectly valid KPI for a musician or singer. 41 RESTRICTED RESTRICTED 5. Aircraft serviceability and reliability are very important KPIs for flying squadrons. Your BMI, PER test scores and your performance in AL&SC can be very valid KPIs for your promotions. Similarly, overall course performance of AL&SC can be a KPI for ALA faculty. Implementation of KPIs 6. The steps of implementing Key Performance Indicators (e.g. PAF with the objective of enhancing physical fitness of personnel) are given below: (a) Objective. PAF wants to enhance the physical fitness of its employees. (b) Selecting relevant KPI. To improve the physical fitness of its employees, PAF will use KPIs (key performance indicators) to measure and motivate their personnel. For example, the KPI for this objective is the scores of the PER (Physical Efficiency Rating) test, which consists of running, reach ups and pushups. It will set quantity for each exercise, such as 2.5 km for running, 23 for reach ups, and 18 for pushups. PAF need to know the current number of personnel rated as pass and the desired number (target) to achieve as improvement. After setting target, it will inform the employees about the KPIs, the targets, and the reasons for implementing them such as improving their health, productivity, and morale. (c) Implementation and monitoring. PAF will assign roles and responsibilities for conduction of activities, data collection and reporting e.g. Sports flight. Then it will provide facilities like time, playgrounds, assign a wellness coordinator (PF&DI) to monitor and report on the KPIs, and offer rewards and recognition for employees who meet or exceed the targets. PAF will evaluate the effectiveness of the KPIs and the implementation process periodically. It needs to check if the KPIs are still relevant, achievable, and aligned with its objective. It also needs to identify any challenges, gaps, or opportunities for improvement. It can use various tools, such as surveys, interviews, or focus groups, to collect feedback from the employees and the management. Dashboards 7. A dashboard is a visual interface6 that displays important data in an easy-to- understand format. It allows users to get a quick overview of their performance and make data-driven decisions. They transform raw data into actionable insights. This is exactly what a KPI does. So, Dashboards are nothing but a graphical representation of various KPIs. Just by looking at a Dashboard senior commanders and supervisors can analyze the overall health of the organization. 6 Interface is where two entities [things] interact. A keyboard is an interface because humans and computer interact through it 42 RESTRICTED RESTRICTED What is Excel Dashboard? 8. A Microsoft Excel dashboard is a visual representation of KPIs, and other complex data in a way that‟s easy to understand. We can create both a static or dynamic dashboard in Excel. Static dashboards simply highlight data from a specific timeframe. It never changes. On the other hand, dynamic dashboards are updated daily to keep up with changes. KPI and Dashboards Success Stories7 9. As organizations navigate the era of big data, KPI‟s and Dashboards emerge as indispensable [unavoidable, necessary] tools for informed decision-making. Here are some real-world case studies illustrating how organizations have utilized KPIs and dashboards to overcome challenges, drive continuous improvement, and achieve exceptional quality standards. Case Study 1: Netflix's Viewer Insights Dashboard 10. Objective. Exploring how Netflix uses Dashboards and KPIs for content optimization. 11. KPI’s Utilized. Following KPI‟s were used: (a) Viewer Engagement (b) Content Popularity 7 Note. These success stories are just for understanding purpose, these will not be included in examination. 43 RESTRICTED RESTRICTED 12. Outcome. Netflix, a pioneer in data-driven decision-making, uses Dashboards and KPIs to interpret viewer preferences, watch patterns, and content performance. With the help of Dashboards and KPIs, they discovered their best content strategy, ensuring a personalized and engaging viewer experience. Case Study 2: Daraz.pk Web Store Analytics 13. Objective. Understanding the role of Dashboards and KPIs in Daraz.pk web store analytics. 14. KPI’s Utilized. Following KPI‟s were used: (a) Website Traffic (b) Conversion Rates of Traffic into customer 15. Outcome. Samsung used dashboards and KPIs to monitor the performance of its product listings on Daraz.pk. They tracked metrics like page load times, bounce rates8, and conversion rates (Number of site visits and bought the products) for their product pages. 16. They noticed that the page load time is high, they concluded that the website‟s performance is affecting the user experience. As a result, potential customers might leave the site before they have a chance to view the products, leading to a higher bounce rate. 17. To address this, Samsung worked with Daraz.pk and optimized the product images and reduced unnecessary site elements. This enhanced the user experience, potentially reducing the bounce rate and increasing the conversion rate. Similarly, if Samsung finds that the conversion rate is low despite a large number of site visits, they might decide to revamp their product descriptions, offer competitive pricing, or provide attractive discounts to entice customers to purchase. BEFORE KPI’s AFTER KPI’s 8 Number of site visits but left without purchasing 44 RESTRICTED RESTRICTED CHAPTER 5: QUALITY MANAGEMENT SYSTEMS (QMS) Desired Learning Objectives 1. After learning this chapter students will be able to: (a) Define QMS and its importance in an organization (b) Comprehend the significance of ISO 9001 in QMS (c) Demonstrate an ability to navigate through the ISO9001:2015 standard (d) Analyze a simple case and find appropriate sub-clause from the standard. "The bitterness of poor quality remains long after the sweetness of low price is forgotten." Benjamin Franklin Introduction 2. In modern world, quality has emerged as a defining factor for organizational success. Quality Management Systems (QMS) stand as the hub of the efforts, providing a structured framework [detailed plan to follow] to ensure that products and services consistently meet or exceed customer expectations. At its core, a Quality Management System (QMS) is a structured framework that establishes and documents an organization's policies, processes, and procedures to ensure consistent quality in its products or services. It includes a holistic [including everything] approach, from defining quality objectives to monitoring performance and promoting a culture of continuous improvement. ISO 9001 3. There are several quality frameworks available, ISO 9001 stands out for its global recognition and adaptability to various industries and organizational sizes. It is an internationally recognized standard developed by the International Organization for Standardization (ISO). It provides comprehensive guidelines for establishing, implementing, and maintaining an effective quality management system. It focusses on customer satisfaction, process optimization, risk management and continual improvement. In PAF, several setups are certified with ISO 9001 like PAC Kamra, PAF Hospital Islamabad and College of Aeronautical Engineering (CAE) etc. 4. In order to get the effective outcomes from ISO 9001, various approaches are followed, PDCA cycle is one of them. We have already studied PDCA in slight detail. 45 RESTRICTED RESTRICTED The Plan-Do-Check-Act (PDCA) cycle is a fundamental concept in ISO 9001, serving as a systematic approach to quality management. Let‟s consider a transportation company that wants to improve its delivery times. Here‟s how they could apply the PDCA cycle: (a) Plan (P). In the planning phase, organization defines its objectives and map out the processes needed to deliver results in accordance with ISO 9001 requirements. The company identifies that their delivery times are longer than the industry average. They set a goal to reduce delivery times by 15%. They plan to achieve this by optimizing their delivery routes using a new route planning software. (b) Do (D). The implementation phase involves executing the plans developed in the previous stage. The company implements the new route planning software on a small scale, initially only in one city. They train their drivers on how to use the software and start monitoring the delivery times. (c) Check (C). During the checking phase, company assesses the performance of its processes and monitor compliance with ISO 9001 standards. After a month of implementation, the company checks the delivery times. They find that the delivery times have reduced by 10%, which is progress, but not quite the 15% goal they set. (d) Act (A). The acting phase involves taking corrective and preventive actions based on the findings from the checking phase. The company decides to make adjustments to their plan. They provide additional training to their drivers and tweak [adjust] the settings in the route planning software to further optimize the routes. They continue to monitor the delivery times. (e) This cycle would then repeat, with the company continuously planning, doing, checking, and acting to improve their delivery times. Fig 5.1: The PDCA Cycle 5. ISO 9001 is structured around a set of clauses, each addressing crucial aspects of quality management. These clauses serve as building blocks, guiding organizations in establishing, implementing, and continually improving their quality management system. Understanding the significance and requirements of each clause is essential for achieving ISO 9001 certification and reaping the benefits it brings. 46 RESTRICTED RESTRICTED 6. Each clause of ISO 9001 comprises of few sub-clauses to address minute factors that can affect quality of product or service. For example, students are coming for a training session from different locations across Pakistan. It is the responsibility of the administration