1 industria 40.docx
Document Details
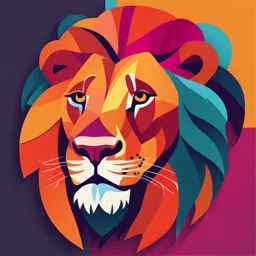
Uploaded by CatchyAllegory
Universidad Carlos III de Madrid
Full Transcript
Industria 4.0 ¿Cuál de las siguientes tecnologías no es aplicable a la Industria 4?0? Merchandising La primera cinta transportadora, históricamente podríamos englobarla dentro de… b) La 2ª Revolución Industrial ¿Qué sistema de mantenimiento aboga por “cero averías, cero defectos, cero accidentes”? T...
Industria 4.0 ¿Cuál de las siguientes tecnologías no es aplicable a la Industria 4?0? Merchandising La primera cinta transportadora, históricamente podríamos englobarla dentro de… b) La 2ª Revolución Industrial ¿Qué sistema de mantenimiento aboga por “cero averías, cero defectos, cero accidentes”? TPM (Total Productive Maintenance) ¿Cuál de los siguientes casos posibles de fallo no se considera en el método de mantenimiento RCM (Reliability Centred Maintenance)? Fallo humano De los siguientes parámetros. ¿Cuál NO es un indicador de mantenimiento? c) Desviación típica ¿Cuál de los siguientes aspectos se considera un inconveniente para la implantación de un sistema de mantenimiento predictivo? b) Formación de los operarios La Orden de Trabajo… d) Debe ser generada cada vez que se realiza una operación de mantenimiento En el organigrama ideal del servicio de mantenimiento ¿Quién o quiénes tiene la función de administrar al personal de mantenimiento, ejecutar el mantenimiento programado, definir repuestos críticos y stock mínimo de repuestos y elaborar informes técnicos? b) jefe de mantenimiento Evolución de las tecnologías: En la evolución de las tecnologías ha habido 4 revoluciones industriales que son Industria 1.0, Industria 2.0, Industria 3.0, Industria 4.0. Industria 1.0: Mecanización, potencia de vapor, primer telar de tejer mecánico. Industria 2.0: Producción en masa, montaje de energías eléctricas, primera cinta transportadora Industria 3.0: Automatización, computadoras y electrónica, microelectrónica. Primer controlador lógico programable (Plc). Industria 4.0: Sistemas ciber físicos, internet de las cosas, redes. Características de la industria 4.0: Las características de la industria son la Conectividad y comunicación, big data, inteligencia artificial, interacción humano- maquina, Fabricación avanzada. En la industria 4.0 tenemos avanzada sensores, datos masivos, inteligencia artificial ¿Cuál es el objetivo de la tecnología? El objetivo de esta tecnología es hacer más cómoda nuestra vida, así como proporcionar una mayor seguridad en diversos ámbitos. -Se empezó con inteligencia artificial, luego machine learnig y estamos en Deep learnign MANTENIMIENTO Y TIPOS DE MANTENIMIENTO La falta de disponibilidad de una maquina o un dispositivo afecta a la producción, mantenimiento, compras, logística. ¿Qué es el mantenimiento? El mantenimiento son un conjunto de acciones que permiten mantener o restablecer el estado operaciones de un bien especifico para asegurar un servicio determinado. El mantenimiento se realiza para evitar fallos, retrasar fallos y recuperar el estado operativo. Etapas del Mantenimiento: Primera generación (0-1950): La primera generación de las etapas del mantenimiento fue solo mantenimiento correctivo. Segunda generación (1950-1980): La segunda generación de las etapas del mantenimiento tuvieron características como el Manteniendo correctivo, preventivo, sistemas de planificación y control, informatización, grandes OVERHANDS que son los costos de operación. Tercera generación (1980-2000): La tercera generación de las etapas del mantenimiento tuvieron características como Mantenimiento preventivo y monitorización, modelo análisis modo falla efecto (AMFE), análisis de costos de operación, contratación externa. Cuarta generación (2000-2015): La tercera generación de las etapas del mantenimiento tuvieron características como gestión integrada del mantenimiento basado en nuevos conceptos como RCM, TPM, Orientación en resultados y satisfacción de clientes, certificados de integridad ISO 9001 Y ISO 14001, Análisis de riesgos. Problemas derivados de un mal mantenimiento: Elevado nivel de averías, Baja disponibilidad de las máquinas y equipos, Velocidades de trabajo inferiores a la óptima, Duración excesiva de alguna avería, Escasa información para solucionar las averías., Desánimo, desidia, baja confianza en los equipos. Tipos de mantenimiento: Correctivo ligado reparación, Preventivo ligado a verificar, predictivo ligado a estudio Mantenimiento correctivo: Mantenimiento accidental, mantenimiento de emergencia, mantenimiento por norma. El mantenimiento correctivo No es programado puede suceder el cualquier momento. Mantenimiento Preventivo Se realiza para evitar fallos, es planificado y programado se realiza en base en las especificaciones del fabricante. Mantenimiento Predictivo se basa en la medición y seguimiento constante como análisis térmico, análisis de aceite, vibraciones, análisis acústicos, análisis de corrientes, humos de combustión Mantenimiento proactivo de la confiabilidad (PRM) es un proceso de probada eficacia para: Eliminar fallas recurrentes, Reducir los costes de mantenimiento, Reducir el tiempo de paradas, Mejorar la calidad de los productos., Aumentar la vida útil de las máquinas, Optimizar la eficiencia de la Planta, Mejorar la planificación, Capacitar al personal. El Mantenimiento Productivo Total (TPM) es una filosofía y una serie de prácticas orientadas a mejorar la eficiencia y efectividad de los equipos de producción. Su objetivo principal es maximizar la disponibilidad y el rendimiento de las máquinas y equipos, al tiempo que se minimizan los fallos, los tiempos de parada no planificados y los defectos de calidad. TPM es una metodología integral que involucra a todos los empleados de la organización, desde los operarios hasta la alta dirección, promoviendo una cultura de mejora continua. Principios Fundamentales del TPM: autónomo, planificado, mejoras focalizadas, educación y entrenamiento, gestión temprana de equipos, control de calidad, seguridad higiene y medio ambiente. Mantenimiento Autónomo: Los operarios de producción son capacitados para realizar tareas de mantenimiento básico, tales como la limpieza, la lubricación y las inspecciones rutinarias. Esto ayuda a identificar problemas potenciales antes de que se conviertan en fallos graves. Mantenimiento Planificado: Se desarrollan planes de mantenimiento preventivo y predictivo para asegurar que los equipos se mantengan en óptimas condiciones y para prevenir fallos inesperados. Mejoras Focalizadas: Se llevan a cabo actividades de mejora continúa enfocadas en eliminar pérdidas y desperdicios, optimizando los procesos y aumentando la eficiencia. Educación y Entrenamiento: Todos los empleados reciben capacitación adecuada para que comprendan la importancia del TPM y adquieran las habilidades necesarias para contribuir al programa. Gestión Temprana de Equipos: Se integra el mantenimiento en la fase de diseño y adquisición de nuevos equipos para asegurar que sean fáciles de mantener y operar. Control de Calidad: Se implementan métodos y herramientas de control de calidad para asegurar que los equipos produzcan productos sin defectos. Seguridad, Higiene y Medio Ambiente: Se enfatiza la creación de un ambiente de trabajo seguro y saludable, minimizando riesgos y cumpliendo con las normativas ambientales. El Mantenimiento Centrado en la Confiabilidad (RCM) es una metodología utilizada en la gestión del mantenimiento que se centra en asegurar la confiabilidad de los activos físicos de una organización, como maquinaria, equipos y sistemas. el RCM busca identificar las estrategias de mantenimiento más efectivas y eficientes para mitigar los riesgos asociados con el fallo de los activos, maximizando así la confiabilidad y disponibilidad de los mismos. Principios Fundamentales del RCM: Enfoque Basado en el Riesgo, Análisis de Funciones y Modos de Fallo, Selección de Estrategias de Mantenimiento, Optimización de Recursos, Monitoreo y Mejora Continua. Enfoque Basado en el Riesgo: El RCM se centra en identificar y mitigar los riesgos asociados con el fallo de los activos, priorizando aquellos equipos cuyo fallo pueda tener un impacto significativo en la seguridad, la producción, el medio ambiente o los costos operativos. Análisis de Funciones y Modos de Fallo: Se analizan las funciones críticas de los activos y se identifican los modos de fallo potenciales que podrían afectar esas funciones. Esto implica comprender cómo y por qué podrían fallar los activos y cuáles serían las consecuencias de esos fallos. Selección de Estrategias de Mantenimiento: Una vez identificados los modos de fallo, se seleccionan las estrategias de mantenimiento más adecuadas para mitigar los riesgos asociados. Estas estrategias pueden incluir mantenimiento preventivo, predictivo, detectivo o incluso acciones de diseño o modificación. Optimización de Recursos: El RCM busca optimizar el uso de recursos al aplicar estrategias de mantenimiento efectivas y eficientes, evitando el sobre mantenimiento o el su mantenimiento. Monitoreo y Mejora Continua: Se establecen sistemas de monitoreo y seguimiento para evaluar la efectividad de las estrategias de mantenimiento implementadas y se fomenta una cultura de mejora continua para ajustar y mejorar el programa de RCM con el tiempo. Fases para el mantenimiento centrado en la confiabilidad son listado y codificación de equipos, Listado y funciones específicas, Determinación de fallos funcionales y técnicos, determinación modos de fallo, determinación de efectos de los modos de fallo, determinación de las medidas preventivas. Leyes de supervivencia de un equipo: 1 ley Normal o de “Gauss”: La distribución de fallos aparece centrada alrededor de un valor medio de su vida. 2. Ley exponencial: Corresponde a una Tasa de fallos constante, con causas aleatorias e independientes del tiempo. 3. Ley de Weibull: Curva con tres parámetros “de forma” que permite ajustar los estudios a Tasas de fallos crecientes, constantes y decrecientes. El MTBF es el tiempo medio entre averías El TTF es tiempo hasta el fallo El MTTR tiempo medio hasta la reparación INDICADORES DE MANTENIMIENTO: Disponibilidad es igual al tiempo medio entre averías sobre tiempo medio entre averías mas tiempo medio hasta la reparación. Tasa de mantenimiento preventivo son las horas planificadas sobre el total de horas planificadas. Numero de llamadas son el número de llamas del personal asistencial durante un periodo determinado. Tasa de actividades de mantenimiento preventivo son el número de actividades realizadas sobre el número de actividades previstas. El MTBF es el tiempo medio entre averías El TTF es tiempo hasta el fallo El MTTR tiempo medio hasta la reparación Organigrama del servicio de mantenimiento son jefe, supervisores (mecánicos, eléctricos, fontaneros, eléctricos), mantenedores. GMAO es la gestión de mantenimiento asistido por ordenador. OT significa Orden de Trabajo