Catalyst Synthesis PDF
Document Details
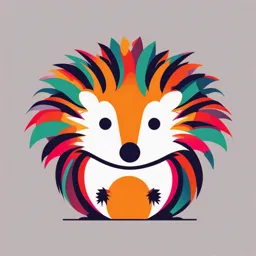
Uploaded by CongratulatoryOtter6853
Universiti Teknologi MARA
Mohd Lokman Ibrahim
Tags
Summary
This document provides a comprehensive overview of catalyst synthesis, covering various techniques and applications. It details different methods such as impregnation, precipitation, and gel formation, along with the factors affecting catalyst production and characterization. The document also touches upon the criteria for a good catalyst, such as high activity, selectivity, and mechanical strength.
Full Transcript
SYNTHESIS OF CATALYST Assoc Prof Dr Mohd Lokman Ibrahim Faculty of Applied Sciences Universiti Teknologi MARA Shah Alam, Selangor 0165002195 [email protected] ...
SYNTHESIS OF CATALYST Assoc Prof Dr Mohd Lokman Ibrahim Faculty of Applied Sciences Universiti Teknologi MARA Shah Alam, Selangor 0165002195 [email protected] area Al2O3 (inert) byk pores - high sample atalyst ① supported · - surface area↑ - functional group ↑ (active sites) 1. Create a group of 5 members How to produce catalyst 2. Find a Journal (From Elsevier or Wiley only) reporting selectivity : about any catalysis reaction (current research paper, 2016-2019) - proper functional group -> - design (chemical 3. Extract all the listed information as below: properties ( i. Types, name of catalyst and their application size - pore ii. The preparation steps (make sure every group use difference small size molecule procedure) > - (physical selectivity) iii. The characterization technique, and iv. The catalytic evaluation 4. Prepare slide presentation reporting all those collected data. V 5. Duration: 2 weeks Flow Process of Catalyst Production Synthesis of Catalyst Lab/reactor Commercialize Catalysis characterization catalytic activity !!! Criteria for a GOOD catalyst are; 1. High activity 2. High selectivity 3. High thermal & mechanical strength 4. Low-cost Heterogeneous catalyst Unsupported Catalyst: Typically very active catalyst that do not require high surface area, for examples: i. Iron catalyst for ammonia production - usually used for high temperature applications ii. Refractory aluminates for catalytic combustion – normally has large surface area iii. Gamma alumina catalyst for isomerization clay catalyst for hydrogenation process Supported Catalyst: Requires a high surface area support to disperse the primary catalyst, the support may also act as a co-catalyst or secondary catalyst for the reaction. How to synthesis a catalyst? I ② processing ⑤ activation ① preparation Processing the primary solid Associating all the Functionalization or useful components activation of the (e.g., impregnation Treatment of primary solid or co-precipitation intermediate solid E.g., or crystallization). or precursor. E.g.: 1. Formation of drying, thermal sulfides decomposition of Preparation of the the salts, 2. De-ammoniation primary solid (or calcination etc. 3. Sulfonation ↓ ex : first precursory solid) air milo ada ppt. Activation of the precursor Three Fundamental Stages (A) Preparation of the Primary Solid The common parameters: i. Quantity of materials (solutions, carrier). ii. Concentrations of substances. iii. Stirring conditions (the shape and volume of vessel/reactor). iv. Temperature and temperature changes. v. Sequence and duration of all operations. There are 5 methods to prepare the primary solid: i. Deposition / Impregnation Q ii. Precipitation & Co-precipitation ② iii. Gel formation ③ iv. Selective Removal ⑪ v. Pillared Layer Compounds ⑪ (1) Deposition a. Impregnation of deposition Impregnation is by contacting solid with liquid or solid with gas * containing the components to be deposited on the surface. - > mestiada surface ! Factors determining the rate of impregnation processes; ü Selective adsorption of species (charged or not) by coulomb force, van der Waals forces or H-bonds; ü Ion exchange between the charged surface and the electrolyte; ü Polymerisation/depolymerisation of the species (molecules, ions) attached to the surface; ü Partial dissolution of the surface of the solid. The types of products depend on: i. The nature of both reactants - the liquids and the solid surface ii. The reaction conditions - temperature, pressure etc The main properties of the catalyst need to be highlighted; * i. The texture and surface characteristics. ii. * The presence of functional groups (e.g., the number and strength of the acidic and basic sites and the isoelectric point) iii. * The presence of exchangeable ions iv. * the reactivity (surface dissolution in acidic or basic solution, etc.). Click the link: https://youtu.be/ZIme3liGVeo Types of Impregnations * Impregnation by soaking or with an excess of solution Dry or pore volume impregnation Incipient wetness impregnation Impregnation by percolation Deposition by selective reaction with the surface of the support Co-impregnation Successive impregnation q Impregnation by soaking, or with an excess of solution oc o Excess liquid is eliminated by evaporation or by draining. o The quantity of active element deposited on the surface is depends on the solid/liquid ratio. - o Deposition is slow - several hours or days. - - - o Loss of surface area - Extensive restructuring of the - surface may occur o The method allows the distribution - of the species to be very well controlled and high dispersions may be obtained. - - o The method - works best if ion/solid interactions are involved. q Dry or pore volume impregnation o The required amounts of components are introduced in the - volume corresponding to the pore volume of the support. - o The method is best suited to deposition of species which - interact very weakly with the surface, and for deposition of - - - quantities exceeding the number of adsorption sites on the - - surface. o If the number of species which can adsorb on the surface is - - smaller, a chromatographic effect- - may occur, i.e. attachment to the mouth of the pores. - - o Redistribution inside the pores is very slow. - & q Incipient wetness impregnation o A-procedure similar to dry impregnation, - but the volume of the solution is more empirically - - determined - to correspond to that beyond which the catalyst begins to look wet. o https://youtu.be/iLgxEow-W34 q Deposition by selective reaction with the surface of the support o The carrier is left in contact with an excess of solution for a definite time, and then the excess liquid is removed, e.g. using a dipping technique. o The objective is to make a strong bond with the surface. o The process is little used but it has potential for grafting or anchoring active elements to a support. q Impregnation by percolation The precursor is sorbed/ion exchanged by percolation of the impregnating solution through a bed of carrier. There is much similarity between this method and impregnation with an excess of solution (method 1). The advantage is a faster approach to equilibrium. But, there may be differences in the degree of deposition along the carrier bed. https://youtu.be/N_pARn50GHo q Co-impregnation Two or several active components are introduced in a single step. Difficult to get uniform distribution. Other type of Deposition: B. Gas phase deposition Deposition occurs by adsorption or reaction from a gas phase. This method may ensure excellent dispersion and very well controlled distribution of the active species. Chemical vapour deposition is an example of gas phase deposition. https://youtu.be/j80jsWFm8Lc C. Solid/solid reaction In certain cases it is possible to use a solid salt of the active element, e.g. a nitrate, to impregnate the support. This is done by dry mixing. The method is well adapted to industrial production but is difficult to use reproducibly in a laboratory. D. Wash coat* Monolith (or honey comb) catalysts are prepared by covering the surface of the channels with a suspension of small particles in water (the suspension is called "slurry" or "slip"). Water is evaporated and the final calcination promotes adhesion of the particles to the monolith. deposition / impregnation ? suspension dan solution, beza dgn impregnation deposited on surface - need precipitating agent (NHz) (2) Precipitation - - need solid surface 1. One or more metals are precipitated together with the support or precursor. 2. The factors need to control during the process: the order and rate of addition of one solution into the other; the mixing procedure; the pH and variation of pH during the process the maturation process. 3. Precipitation involves 2 distinct processes: Nucleation - requires that the system is far from equilibrium (high supersaturation or in the case of ionic species, a solubility product far exceeding the solubility constant of the solid to be precipitated). Growth - of the new phase takes place in conditions which gradually approach the equilibrium state. Precipitates are solids consisting of particles in a solution. Sometimes solid is a result of a chemical reaction in a solution. These solid particles will eventually settle down due to their density. In centrifugation, the resulting C precipitated is also known as the pellet. The solution above the precipitate is known as the E supernatant. The particle size in the precipitate changes from occasion to occasion. Colloidal suspensions contain tiny particles, which do not settle down, and cannot be easily filtered. Crystals can be easily filtered, and they are larger in size. Co-Precipitation “Co-precipitation is a process in which normally soluble compounds are carried out of solution by a precipitate.” There are four types of co-precipitation as i. surface adsorption, ii. mixed- crystal formation, iii. occlusion and iv. mechanical entrapment. Surface adsorption takes place for precipitates with larger surface areas. Specially coagulated colloids contaminate by this method. In mixed- crystal formation, one of the ions in the crystal lattice is replaced by another ion. Surface adsorption and mixed- crystal formation are equilibrium processes, whereas the other two are kinetic phenomena. https://youtu.be/73dw6w0zNXA Cont.. Co-precipitation When a crystal is growing rapidly, contaminant can trap inside the growing crystal and this is known as occlusion. Mechanical entrapment is the mechanism where some amount of solution is trapped inside the crystals. This happens when two growing crystals are close together, so that they grow together. Quick Task!! What is the difference between Precipitation and Co-precipitation? - s need two more ion S involve one ion Example: Precipitation & co-precipitation methods ü Synthesis of zeolites Zeolites are normally prepared by Crystallization (precipitation) in hydrothermal conditions (T=350-525 K) of (Si,Al)-containing hydrogels. Above 373 K, crystallization is normally performed under autogenous pressure. Both batch and continuous synthesis methods can be envisaged. (3) Gel Formation and Related Processes It starting from solutions, give gels or solid-like substances, which retain all the active elements contained in the starting solutions, and from which the solvent and reaction by-products are eliminated by evaporation or sublimation. These gels are later decomposed or further transformed, usually to oxides. The gel can be obtained by: i. Chemical reaction – e.g., polymerisation ii. Complexation iii. Freeze drying iv. Addition of gum or gelling agent, e.g., hydroxymethyl cellulose https://youtu.be/AjWkd0VIsa8 https://youtu.be/hFSbgANbKuw (4) Selective Removal Selective removal is a method used for very few, but important catalysts. Example: Raney Ni catalyst Starting from a relatively coarse powder of an alloy (e.g. NiAlx) one component (Al) is removed by a leaching agent (NaOH) leaving the active agent (Ni) in a relatively highly dispersed form. https://youtu.be/7GHkKk-3uss https://en.wikipedia.org/wiki/Raney_nickel (5) Pillared layer method One can take advantage of existing layered structures for making solids with approximately slit-shaped pores. Such solids are most often prepared from clays (pillared-clays). In a fist step, the sign and number of the charges compensating those of the layers must be adjusted. This is generally done by Na ionic exchange. Acidic activated carbon SO3H (B) Processing/Treatment of the Primary Solid - C - C I - S03H ! - -S03H These treatments include drying, thermal decomposition of the SO 3 H salts, calcination, etc. The product obtained is a reasonably inert solid (usually an oxide) which can be stored easily. CaNO3 ↓ > - calcination Cag The main recommendation is all the process subjected to exactly the same conditions and to supply sufficient quantity of gas or liquid to the reactor to ensure complete reaction. For example: (i) nitrogen for complete evaporation and (ii) oxygen for quantitative formation of oxides. gas out (N2) ·( - E T (C) Activation of the Precursor The catalyst always contain species with different reactivity, which come from: (i) Different locations in the depth of the pellets / support (effect of diffusion on reactivity) (ii) Different crystallite sizes (incase for nucleation and growth mechanism) (iii) Various degrees of interaction with the support (iv) Differences in the degree of contamination. For those reasons, the activation rate becomes affected as the degree of reaction proceeds; there are even cases where reaction is never complete. Example of activation precursor: (i) Reduction to metal (e.g., hydrogenation catalysts), (ii) Formation of sulfides (e.g., hydrodesulfurisation), (iii) Deammoniation (e.g., acidic zeolites). (iv) Sulfonation (e.g., sulfonated carbon catalyst) (D) Catalyst Forming methods In principle the support, precursory solids, precursors or catalysts, can be used in various forms Generally the catalysts are used as entities of larger size and/or better defined shapes (beads, pellets, extrudates, rings, monoliths, etc.). The forming operations are to ensure the catalysts has; ü mechanical properties; ü resistance to thermal shock; ü gas or liquid flow through the reactor. The shape and size of catalyst must be suitable towards the application 1. Powder: Preparation, crushing and grinding In a powder, which is a collection of particles of relatively small size (typically 0.5 pm – l mm), the particles may have different shapes and this influences strongly the shaping operations. The crushing and/or grinding operation is aimed at producing particles of a size such that after the forming operation, pores of the desired size are formed. Crushing and/or grinding is used with material of natural origin or with products of operations. Grinding may take place in the absence (dry) or presence (wet) of a liquid, usually water. 2. Spray drying In spray drying, a slurry of a powder in suspension in water is fed to a nozzle which sprays small droplets into hot air. Spray drying gives particles of almost identical shapes (spheres with a slightly depressed surface at one spot) and sizes, used as such in fluid bed operations. https://youtu.be/0o4ZCjHnaRw 3. Oil drop A sol or gel is introduced as drops through a nozzle into a hot liquid. Heat removes the solvent and brings about the hardening of the gel. According to relative densities the drops may move downwards (oil drop per se) or upwards. Beads are obtained. 4. Granulation Granulation (or pilling) is the agglomeration-forming operation made by progressive humidification of a powder in a rotating granulator, resulting in the formation of spheroidal particles, granules or beads. The pan may be concave (hemispheric granulator or "bowl granulator") or cylindric (flat granulator or "dish granulator"). https://youtu.be/BAxFTDcKoDk 5. Tableting The powder is firmly compressed to be shaped into small cylinders, rings and even beads. https://youtu.be/4xggZRckfTE 6. Extrusion A paste, which may be "soft" or "stiff" (or: "wet" or "dry") is pushed through a die, forming a cylinder which is cut into small sections. Example: monolith ü Monoliths are formed by extrusion through special dies creating multiple channels. (A variant in monolith manufacture uses corrugated foils of the support which are joined together to create channels). STABILITY DURING HANDLING AND STORAGE 4 common contaminants that are potentially harmful: 1. Water; water brings about hydrolysis and formation of liquid films which dissolve active elements, and may bring about the corrosion of containers; 2. C02; C02 brings about carbonate formation. The reaction of carbonates, during activation, may give an activated catalyst with altered texture; 3. Hydrocarbons; if hydrocarbons are present, there is a danger of uncontrolled reactions during calcination (overheating) or activation (over- reduction); 4 Poisons or inhibitors HOW TO PROTECT THE ACTIVATED CATALYST? There are 3 methods are widely used for protecting these catalysts from alteration during storage and handling: 1. Passivation 2. Protection by inert gas 3. Protection by a condensed phase 1. Passivation Passivation often involves the controlled exposure of the catalyst to air at ambient temperature. Rapid exothermic reactions are prevented while forming stable surface layers which inhibit further rapid reaction upon air exposure. https://en.wikipedia.org/wiki/Passivation_(chemistry) Example: Ni catalysts which would oxidize catastrophically upon exposure to air, and of highly dispersed supported Pt catalysts. Passivation technique: 1. controlled oxidation, 2. adsorption of protecting (usually inhibiting) molecules, 3. reactions with a weakly oxidising agent dissolved in water. 2. Protection by an inert gas Activated metal catalysts and hydrodesulphurization catalysts can be stored and handled in an inert atmosphere (N2). 3. Protection by a condensed phase Activated metal catalysts (essentially Ni) can be effectively protected by a wax (stearic acid, etc.). Even catalysts in a powder form, for use as suspensions, can be protected this way. The waxy mixture is shaped into pellets. Part of the catalysts used in the fat and oil industry undergoes this treatment. Extras Catalyst loading in the reactor i. https://youtu.be/Hd3FDqMWuFQ ii. https://youtu.be/V4R6u28Gehg