Pollutant-Specific Treatment Techniques PDF
Document Details
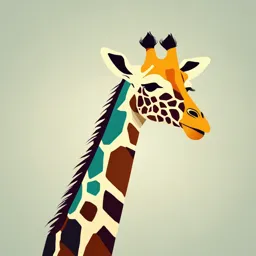
Uploaded by FavoredBanshee
ETH Zurich
Jing Wang
Tags
Summary
This document provides an overview of various techniques for treating pollutants, with a focus on specific pollutants like sulfur dioxide (SO2) and nitrogen oxides (NOx). It covers chemical and physical processes, such as absorption, neutralization, and catalytic methods. It also discusses the importance of factors like operational safety and efficiency in selecting appropriate treatment methods.
Full Transcript
Pollutant-specific Treatment Techniques Jing Wang Professor Empa ETH Zürich Swiss Federal Laboratories Institute of Environmental Engineering for Materials Science and...
Pollutant-specific Treatment Techniques Jing Wang Professor Empa ETH Zürich Swiss Federal Laboratories Institute of Environmental Engineering for Materials Science and Technology [email protected] Phone +41 44 633 36 21 Outline Desulphurisation Chemical sorption Neutralization and regenerative process Physical sorption Adsorption catalysis Denitrification Reduction process Oxidation process Reduction of other emissions mercury; VOC; dioxin and furan; odor 2 General Consideration Process-specific How efficient is the process and for which pollutants is it applicable? Pollutant-specific Which processes can be used to remove a specific pollutant from the exhaust gas? Criteria to select the most suitable scrubbing process: 1. Performance level 2. Economy 3. Operational safety 4. Suitability given operational limits 5. Recycling opportunities and cost of disposal 3 Desulphurisation Overview Desulphurisation: minimizing the SO2 and SO3 concentration in the exhaust gas. A) Neutralization Limestone processes method Chemical sorption -wet method Wellman-Lord -quasi-dry method method -dry method B) Regenerative processes Seawater method Physical sorption BF method Adsorption catalysis Sulfacid method 4 Chemical Sorption The wet method: a alkaline chemical wash pK=1.9 pK=7.2 SO2(g) + H2O(I) H2SO3 H+ + [HSO3]- H+ + [SO3]2- sulphurous hydrogen sulphite acid sulphite pK=-3 pK=2.0 SO3(g) + H2O(I) H2SO4 H+ + [HSO4]- H+ + [SO4]2- sulphuric hydrogen sulphate acid sulphate Hydrogen sulphite is subsequently oxidised to sulphate through the addition of air [HSO3]- + O2 + H2O [SO4]2- + [H3O]+ Addition of OH- ions shifts the equilibia toward the deprotonated form (to the right). Alkaline agents: CaO, Ca(OH)2, CaCO3 , NaOH, Na2CO3, MgO, Mg(OH)2 pK=6.4 H+ + [HCO3]- H2O + CO2 H+ + OH- H2O 5 The Limestone Method Limestone (CaCO3) is a cheap neutralizing agent for SO2. Large volume of scrubbing fluid and fine grinding of the limestone are needed. The limestone powder is mixed with water to form a thick suspension and sprayed into the scrubber. SO2 + CaCO3 + O2 CaSO4 + CO2 gypsum droplet separator scrubber tower cleaned gypsum washing gas drier scrubber solution circulation gas pre-heater concentrator cleaned gas gypsum to chimney gypsum raw flue gas oxidation air treatment from burner or filter freshwater and limestone inlet 6 Limestone Method Conditions Scrubber solution ratio (including circulation system) ≈ 10 l scrubber solution/ mn3 flue gas. The precipitated gypsum is separated from the water by a hydro- cyclone. After further treatment gypsum is used in the building industry. pH value of the absorber circulation system. Absorption of SO2: pH > 6 ( absorption efficiency 90 %) Dissolving the limestone: lower pH Oxidation of sulphites: optimal pH < 5 Compromise: operation at a pH of 5.5 - 6 (absorption liquid), reduced oxidation rate, increased residence time of the solution in tank. The separation coefficient is approximately 90 %. SO2 separation coefficient oxidation rate 10-3 pH value pH value 7 CaSO4·2H2O Crystal Formed in Ambient We found several types of sulfate aerosols, especially calcium sulfate crystal, in the ambient PM samples from Beijing (Figures c and d). In contrast, only amorphous sulfate was observed in the ambient PM samples in Zurich (Figures a and b). Yue, et al. Atmospheric Environment (2021), https://doi.org/10.1016/j.atmosenv.2021.118776 8 Effect of Relative Humidity We found that relative CaCO3 (ae) + H2O (g) → Ca(OH)(CO3H) (s) (1) humidity had strong influence Ca(OH)(CO3H) + SO2 (g) → CaSO3 (ae) + H2CO3 (a) (2) on the crystalline CaSO4·2H2O CaSO3 (ae) + ½ O2 (g) → CaSO4(ae) (3) CaSO4(ae) + 2H2O → CaSO4·2H2O(ae) (4) particles formation during the ae: aerosol phase; g: gas phase; s: solid phase; reaction of SO2 with calcium a: aqueous phase. carbonate. Yue, et al. Atmospheric Environment (2021), https://doi.org/10.1016/j.atmosenv.2021.118776 9 Semi-dry Method - The neutralising agent is sprayed into the flue gas as a solution or suspension. -The amount of water used for the solution or suspension is adjusted so that it completely evaporates on absorbing heat from the flue gas. - The salts form a solid precipitate which must be removed. - Gas temperature remains above the dew point, in contrast to the wet method. - Short lifetime of droplets -> need basic solutions to react with acid quickly. cleaned gas spray particle Neutralizing agent flue gas absorber separator CaO, Ca(OH)2 alkaline solution NaOH, Na2CO3 MgO, Mg(OH)2 (no CaCO3 because of its slow solid precipitate end product rate of reaction) product recycle 10 Dry Method - Pollutants directly contact alkali and alkaline-earth-metal hydroxides in solid form. - The neutralizing agent should have great specific surface area, by the convoluted surface created by the calcination reaction or when finely milled material of high porosity is used. - The process flow is very similar to that of the quasi-dry method. - Ca(OH) 2, Na2CO3, and NaHCO3. Stoichiometric factor The stoichiometric factor λ indicates how much neutralizing agent is required to fully react with the polluting substance. Wet method λ = ca. 1 Quasi-dry method λ = 1.5 – 2.5 Dry method λ= 2-6 In the dry process, in particular, λ depends strongly on the temperature in the adsorber. Reactivity of SO2 with alkali increases as the temperature decreases. 11 Wellman-Lord Method A sodium sulphite solution is used as the scrubbing medium. Phase equilibrium SO2(g) SO2(aq) SO2(aq) + Na2SO3 + H2O 2 NaHSO3 sodium sulphite sodium hydrogen sulphite 2 NaHSO3 Na2S2O5 + H2O sodium pyrosulphite - The solution laden with sodium hydrogen sulphite is regenerated by passing it through a vacuum evaporator and heating. -The released SO2 gas can be further treated to give sulphur, H2SO4 or liquid SO2. -After lowering the temperature the sodium hydrogen sulphite could also be converted to the sodium pyrosulfite which precipitates. -The decomposition of the sodium hydrogen sulphite leads to the production of fresh scrubber solution. - The method is based on reversible reactions and recycles the scrubber solution. 12 Process Flow Process flow diagram of the Wellman-Lord method (Bank, 1994) Scrubbed gas flue gas SO2 rich gas fresh water sodium hydroxide waste water solution by-product 1 blower 5 evaporator 9 charge container 2 heat exchanger 6 vapour compressor 10 container for SO2 rich gas 3 absorber 7 condenser 11 sulphate crystalliser 13 4 buffer tanks 8 centrifuge Physical Adsorption B-F method (by the Company Bergbau-Forschung) The SO2 is adsorbed by a moving bed of active coke at 120 - 150°C. Subsequent thermal desorption at 500 - 650 °C produces rich gas containing up to 30 % (V/V) SO2. The BF method is used to treat furnace and combustion chamber exhaust gases. In the extended BF-Uhde process, which uses a 2 or 3-stage adsorber construction, simultaneous treatment to convert NOx to elemental nitrogen by SCR (see slides below) is possible. 14 Adsorption Catalysis Sulfacid process The SO2 together with O2 and H2O is removed through the use of activated charcoal adsorbers at 60 - 75 °C. The three components react in the pores to create H2SO4. Saturated adsorber is regenerated either through a chemical reduction process or by washing. Adsorption SO2(g) SO2(ads) O2(g) O2(ads) H2O (g) H2O(ads) Chemical reaction SO2(ads) + O2(ads) + H2O(ads) H2SO4(ads) Regeneration ∆T Reduction: H2SO4(ads) + ½ C SO2 + ½ CO2 + H2O H2SO4(ads) + 3 H2S 4 S + H2O Washing: H2SO4(ads) H2SO4(aq) 15 De-SOx for Marine Ships Large marine diesel engines are usually operated on heavy fuel oil, with an average fuel sulfur content of 2.7% w/w1. Inside emission control areas (ECA), the sulfur content of the fuel shall not exceed 0.1% w/w on and after 1 January 20152. Total emission of sulfur oxides (including both auxiliary and main propulsion engines) should be reduced to 6.0 g SOx/(kW h) or less (calculated as SO2)3. The ECAs established are: Baltic Sea area – as defined in Annex I of MARPOL4 (SOx only); North Sea area – as defined in Annex V of MARPOL (SOx only); North American area (entered into effect 1 August 2012) – as defined in Appendix VII of Annex VI of MARPOL (SOx, NOx and PM); and United States Caribbean Sea area (entered into effect 1 January 2014) – as defined in Appendix VII of Annex VI of MARPOL (SOx, NOx and PM). 1. MAN Diesel, Operation on Low-Sulphur Fuels—Two-StrokeEngines; MAN Diesel, Copenhagen, 2005. 2. Sulphur oxides (SOx) and Particulate Matter (PM) – Regulation 14, International Maritime Organization. 3. Andreasen and Mayer, Use of Seawater Scrubbing for SO2 Removal from Marine Engine Exhaust Gas, Energy Fuels, 2007. 4. MARPOL (Marine Pollution) International Convention for the Prevention of Pollution from Ships. 16 17 Using seawater for flue gas desulfurization. Seawater typically contains about 1300 mg Magnesium per litter. Calcium hydroxide is used for scrubbing liquid regeneration. Used scrubber effluent is discharged to sea. Abrams et al. (1988) Use of Seawater in Flue Gas Desulfurization, JAPCA. 18 Desulphurisation Overview Desulphurisation: minimising the SO2 and SO3 concentration in the exhaust gas. A) Neutralisation Limestone processes method Chemical sorption -wet method Wellman-Lord -quasi-dry method method -dry method B) Regenerative processes Seawater method Physical sorption BF method Adsorption catalysis Sulfacid method 19 Denitrification Overview Denitrification processes are categorised as reductive or oxidative. Because of the poor solubility of NO in water, dry processes are practically always used for denitrification. Non-catalytic Catalytic reductive SNCR process (thermal reduction) SCR process oxidative Electron beam (EBDS process) Purasiv-N process SNCR (Selective Non-Catalytic Reduction) SCR (Selective Catalytic Reduction) EBDS (Electron Beam Dry Scrubbing) 20 Reductive Processes NOx, primarily NO, are reduced to N2 by the reaction with NH2 radicals. - aqueous NH3 solutions - gaseous NH3 (hardly used due to difficulties with safety) - aquatic solutions of urea (CH4N2O) Simplified schematic equations 6 NO + 4 NH3 5 N2 + 6 H2O (R1) 4 NO + 4 NH3 + O2 4 N2 + 6 H2O (R2) 6 NO2 + 8 NH3 7 N2 + 12 H2O (R3) 2 NO2 + 4 NH3 + O2 3 N2 + 6 H2O (R4) Unwanted reactions 4 NH3 + 3 O2 2 N2 + 6 H2O(excessive NH3 consumption) (R5) 4 NH3 + 4 O2 2 N2O + 6 H2O (R6) 4 NH3 + 5 O2 4 NO + 6 H2O (R7) 21 SNCR Process (Thermal Reduction) The reducing agent (urea solution or NH3) is blown directly into the combustion chamber. Conditions : - the exhaust gas and NH3 must be well mixed - the NH3 must be injected into the system at optimal temperature, within a limited temperature range (900 - 1000 ◦C). - minimum residence times must be maintained NOx reduction efficiency of the process: 60 - 80 %. Either the NOx reduction efficiency is lower than in catalytic processes or the plant must be operated with a high NH3/NOx ratio. A sensitive point in the latter case is the emission of unused ammonia (ammonia slip). Applications: cement factories, waste incinerators 22 Temperature Dependence If the temperature is too low no reaction occurs, and it is too high the ammonia is converted into NO (see R7 above). NH2 formation Efficiency NO reduction 23 SCR Process (Catalytic Reduction) Reduction of NOx occurs via the same set of reactions as during thermal processes, but at lower temperatures. Possible catalysts: - Special metal oxides (e.g. vanadium pentoxide V2O5), loaded on a porous substrate (titanium dioxide, aluminium oxide or silicon oxides) operating temperature range: 200 - 300 °C space velocity = 5,000 – 10,000 h-1 (cf. automobile three-way catalysts where space velocity ≈ 10,000 to 100,000 h-1) space velocity SV = V / Vkat residence time in catalyst tv = 1/SV= Vkat / V V = Volume flow rate (operation condition, humidity); Vkat = catalyst volume. - Molecule sieves (zeolites) operating temperature range: 300 - 480 °C - Activated coke: in the BF-Uhde process both SO2 and NOx are simultaneously removed. operating temperature range: 120 - 150 °C 24 SCR Characteristics Unwanted parasitic reactions at the catalyst are for example: - 4 NH3 + 3 O2 2 N2 + 6 H2O - 4 NH3 + 4 O2 2 N2O + 6 H2O - 2 SO2 + O2 2 SO3 Excess NH3 reacts with SO3 to give (NH4)HSO4 and (NH4) 2SO4. These ammonium salts can precipitate out and cause blockages. This problem disappears when desulphurisation is carried out before the denitrification step. NOx reduction efficiency of the SCR process: 80 - 90 %. Applications of the SCR method: waste incinerator plants, stationary diesel engines 25 Catalyst Arrangement (Warm) Warm SCR layout Heat- Process E-Filter Denox Scrubber exchanger E-filter: electrostatic filter catalyst materials: V2O5, WO3 advantages: - no ammonia in exhaust gas (scrubber downstream) - less contamination of scrubber water with dioxin (the SCR process reduces dioxin concentrations) disadvantages: - because the catalyst is located upstream of the scrubber the exhaust gas has a high SO2 concentration. This can lead to the generation of sulphuric acid which reduces the operational life of the catalyst. 26 Catalyst Arrangement (Cold) Cold SCR layout Heat Process E-Filter Scrubber exchang Heater Denox er catalyst materials: V2O5, WO3, zeolites, activated coke advantages: - inlet gas temperature at Denox is constant and independent of load - no ammonia in wastewater - placing the scrubber upstream of the catalyst ensures that unwanted parasitic reactions are minimised. disadvantages: - gas must be reheated from 50 - 70 °C to the catalyst operating temperature - possibly problems with ammonia in the scrubbed gas 27 Oxidative Processes The electron beam dry scrubber (EBDS) method - An intensive beam of electrons is passed through the exhaust gas flow, generating radicals (OH, O, HO2, N etc.). - These radicals oxidise NO and SO2 , + H2O → HNO3 and H2SO4. - Acids react with gaseous NH3 added to the flow to form crystalline ammonium nitrate and ammonium sulphate which are then filtered out. The Purasiv-N method - Nitrogen oxides are adsorbed onto zeolite molecule sieve material and catalytically oxidised. - The NO2 so created remains adsorbed onto the zeolite. - During subsequent thermal desorption NO2 rich gas is produced. 28 Denitrification Overview Denitrification processes are categorised as reductive or oxidative. Because of the poor solubility of NO in water, dry processes are practically always used for denitrification. Non-catalytic Catalytic reductive SNCR process (thermal reduction) SCR process oxidative Electron beam (EBDS process) Purasiv-N process SNCR (Selective Non-Catalytic Reduction) SCR (Selective Catalytic Reduction) EBDS (Electron Beam Dry Scrubbing) 29 Reducing Mercury Emissions Mercury is toxic and its recovery is valuable. Adsorption onto impregnated active charcoal Untreated active charcoal take up of mercury (0.2 – 0.3 %). Impregnated AC can adsorb up to 40%. Impregnated with sulphur, iodine, sulphuric acid etc. Regeneration using hot gas, supercritical steam or other extraction method Adsorption onto molecular sieves (physisorption) In the Purasiv-Hg process mercury in exhaust gas is removed by multistage condensation and physisorption on molecular sieve adsorber. Regeneration is accomplished through thermal methods. Adsorption onto a selenium filter (chemisorption) The filter consists of a porous substrate coated with a layer of selenium. Metallic mercury reacts with selenium to form mercury selenide, a compound with low solubility in water and very low vapour pressure, which is bound to the filter and so immobilised. 30 Reducing VOC emissions Separation of the VOCs: - absorption - adsorption - gas permeation Oxidation of the VOCs: - thermal post-combustion (TPC) - regenerative post-combustion (RPC) - catalytic post-combustion (CPC) - bio scrubbers and biofilters In the Adsox process Step 1: VOC adsorption. Step 2: VOC desorption and burning of the VOC-rich gas. Advantages: Concentrated VOC, higher calorific value of the gas, massive improvement in the economics of the combustion process. 31 Persistent Organic Pollutants The Stockholm Convention on POPs is a global treaty to protect human health and the environment from persistent chemicals Stockholm Convention, adopted in 2001 and entered into force in 2004. Polychlorinated dibenzo-p-dioxins and polychlorinated dibenzofurans (PCDD/PCDF) are two of the initial POPs under the Stockholm Convention. PCDD PCDF 75 congeners, 7 very toxic 135 congeners, ten with dioxin-like properties The 1976 Seveso disaster resulted in the highest known exposure to 2,3,7,8- tetrachlorodibenzo-p-dioxin (TCDD) in residential populations , which led to EU industrial safety regulations known as the Seveso II Directive. TCDD 32 Dioxins and Furans Polyhalogenated dioxins and furans (e.g. polychlorinated dibenzo-p-dioxins and polychlorinated dibenzofurans PCDD/PCDF) are generated: - the presence of organic precursor compounds - the presence of chlorides - suitable temperatures (200 - 600 °C) - metals in the exhaust gas: metal chlorides (including copper (II) chloride) have catalytic effects and also take part in the reactions as chlorine donors. - high O2 concentrations (above 12 vol-%) favour the creation of dioxins. In the waste gas treatment system, where temperatures in the range of 200 - 400°C are encountered and precursors (e.g. aromatics) exist, dioxins and furans can be created. Metal chlorides, play a central role in this process too. Critical in this respect are two regions: the cooling zone downstream of the combustion chamber and the dust removal zone in an electrostatic filter. 33 Primary Measures for Reduction 1. Optimising the combustion process - reducing excess air → high combustion temperatures → more complete combustion → fewer precursors and lower O2 concentration. - long residence time of the exhaust gas in the higher temperature zone - high level of turbulence in the combustion chamber 2. Exhaust gas recirculation → reduced O2 concentration 3. SNCR process, i.e. selective non-catalytic denitrification. Ammonia or urea solution are blown directly into the combustion chamber at about 900° C, acting as reducing agents. Ammonia, which is added in excess, is a good ligand for copper and inhibits its catalytic effects in the dioxin creation process. 4. Optimal temperature conditions in the exhaust gas - cooling the exhaust gases quickly in the range 400 - 250 °C - maintaining the operating temperature of electrostatic filter as low as possible i.e. < 250 °C 34 Secondary Measures for Reduction 1. Dust removal A fraction of the dioxins and furans are bound to dust particles. effective dust removal makes a significant contribution to the reduction of dioxin emissions. However, partial transfer into the gas phase takes place so that dust removal alone does not lead to an adequate reduction. 2. Adsorption onto activated charcoal or activated coke Filsorption with the entrained-flow process Active charcoal is dispersed into the exhaust gas and subsequently removed by a bag filter. The filter cake provides both the filtering and adsorption functions (Filsorption). Moving bed and solid bed absorbers If active charcoal is used as the active medium then the (sulfacid) desulphurisation process can be combined with dioxin removal. 3. Catalytic oxidation by the SCR process (for denitrification) The catalytic oxidation of the dioxins and furans to CO2, H2O and HCl occurs here. 35 Comparison of SNCR and SCR Denitrification: in both processes basically the same reactions occur. Dioxin and furan reduction: totally different mechanisms take place in the two processes. SNCR process: - reduces dioxin and furan creation by inhibiting the catalytic effects of metal chlorides through the addition of NH3; - internal to the combustion process; - reduction efficiency of dioxins and furans 80% - cleaned gas concentrations about 1 – 2 ng TE/m3 (TE: toxic equivalent). SCR process: - catalyses the oxidative decomposition of dioxins and furans; NH3 plays no role in this process; - external to the combustion process; - reduction of dioxins and furans is about 95% (in TE/m3); - cleaned gas concentrations below 0.1 ng TE/m3 are achievable. 36 POPs from Plastics: HBCD Example Polystyrene (PS) Hexabromocyclododecane (HBCD) - Flame retardant - Usually 0.7% in Expanded PS (EPS) and 2.5% in Extruded PS (XPS) The PS foam is used as a insulating material in construction. Impact of HBCDs ⚫ Persistence and Long-range transport ⚫ endocrine disruptor 4.严重的毒性效应 ⚫ enzyme inducer ⚫ developmental 具有相同的毒性终点( toxic end point ) neurotoxicant ⚫ reproductive disorder 环境激素效应: ⚫ carcinogen 性别变异和行为失常 ⚫ Bioaccumulation Biomagnification Bioaccumulation 致癌、致畸、 Bioconcentration 致突变 HBCDs have been detected in human serum and breast milk 38 Release of HBCD during Thermal Cutting ◼ Thermal cutting of PS foam induced evident emission of HBCDs and massive generation of ultrafine particles, and most of released HBCDs was loaded on the ultrafine particles. ◼ The lung deposition of HBCDs from 1 hour of polystyrene cutting is equivalent of normal intake of HBCDs in 32 - 400 days. ◼ Halogen-free flame-retardants are widely developed now. 39 Zhang, et al. 2012, Environmental Science & Technology. 46(20), 10990–10996. Reducing Olfactory Emissions - Olfactory emissions (i.e. disturbing smells) pose problems. - The detection threshold is the concentration of an odor when 50% of a population can distinguish between the odorous sample and an odor free blank. - Odor intensity is quantified using the European Odor Unit OUE. The number of odor units indicates the factor by which an exhaust gas must be diluted with clean air in order to reach the required odor threshold. VA + VVL VA = Volume of exhaust gas sample OU E = VA VVL = Volume of required diluting air By definition, the concentration of odor generating compounds at the odor threshold is 1 OUE. Odor active substances are frequently VOC. A reduction in emitted odor units generally indicates a reduction in the VOC concentration. Processes for odor reduction: - Bioscrubbers and biofilters - Chemical scrubbers (acid, basic or oxidative). - Adsorption onto active charcoal - Thermal and catalytic post-combustion 40 Olfactometer for Odor Testing 41