03 Carbon Fibers WS24-25 PDF
Document Details
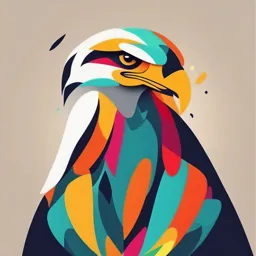
Uploaded by ComelyAsh3415
Technical University of Munich
2024
Prof. Dr.-Ing. K. Drechsler
Tags
Summary
This document is a lecture on carbon fibers, discussing their properties, history, and applications. It covers topics like the structure of carbon fibers, their manufacturing processes, and market analysis. The content is aimed at students or professionals involved in material science, engineering, or related fields at the Technical University of Munich.
Full Transcript
Composite Materials and Structure-Property-Relationship 3 Carbon Fibers Prof. Dr.-Ing. K. Drechsler L. Heidemann, M. Sc. Nils Siemen, M. Sc. Dr. Michael Heine & Dr. Kristina Klatt (SGL Group) Chair of Carbon Composites TUM School of Engineering and Design Technical University of Munich 3.1 Cont...
Composite Materials and Structure-Property-Relationship 3 Carbon Fibers Prof. Dr.-Ing. K. Drechsler L. Heidemann, M. Sc. Nils Siemen, M. Sc. Dr. Michael Heine & Dr. Kristina Klatt (SGL Group) Chair of Carbon Composites TUM School of Engineering and Design Technical University of Munich 3.1 Content 3 Carbon Fibers 3.1 Content 3.2 Introduction to Carbon Fibers 3.3 Manufacturing of Carbon Fibers 3.4 Carbon Fiber Properties WS 2024/25 | Composite Materials and Structure-Property-Relationship 2 Chair of Carbon Composites TUM School of Engineering and Design Technical University of Munich 3.2 Introduction of Carbon Fibers 3.2.1 History of Carbon Fibers 3.2.2 Structure of Carbon Fibers 3.2.3 General Carbon Fiber Applications 3.2.4 Carbon Fiber Market 3.2.5 Characteristics of Carbon Fibers WS 2024/25 | Composite Materials and Structure-Property-Relationship 3 Chair of Carbon Composites TUM School of Engineering and Design Technical University of Munich 3.2.1 History of Carbon Fibers (1/3) Early Carbon Fibers Initially not used as reinforcement material First incandescent electric lamps invented by Thomas Edison were made from cellulosic materials (bamboo, natural cellulose, cotton etc.) Fig. 1: Bamboo Fig. 2: Cotton field Fig. 3: One of Edison’s early light bulbs WS 2024/25 | Composite Materials and Structure-Property-Relationship 4 Chair of Carbon Composites TUM School of Engineering and Design Technical University of Munich 3.2.1 History of Carbon Fibers (2/3) Development of Carbon Fibers 1968: patent by Royal 1950: First oxidized Aircraft Establishment of PAN fiber “Orlon” by 1959: First Farnborough (RAE) carbon fibers Fig. 2: PAN based Carbon DuPont fiber by SGL from PAN (JP) 1880 1920 1940 1960 1980 2000 2020 1964: “Thornel 25” by Union 1971: US production acc. 2009: JV SGL Group and Carbide (US) made from To RAE patent by BMW Group (SGL ACF) viscose rayon Hercules and Morganite Fig. 1: Edison’s light bulb WS 2024/25 | Composite Materials and Structure-Property-Relationship 5 Chair of Carbon Composites TUM School of Engineering and Design Technical University of Munich 3.2.1 History of Carbon Fibers (3/3) Fields of Research – Carbon Traditional Carbon Modern Carbon Novel Carbon > Year 1800 > Year 1960 > Year 1985 1985 Fullerenes Electrodes Kroto, Curl & Fe, Al & Si Smalley Production Copyright by AIRBUS 1991 Nanotubes S. Iijima Graphite Parts Solar & Semi- Copyright by BMW AG 2004 Graphene conductor Geim, Novoselov Industry Light weight through CFRP WS 2024/25 | Composite Materials and Structure-Property-Relationship 6 Chair of Carbon Composites TUM School of Engineering and Design Technical University of Munich 3.2.2 Structure of Carbon Fibers Definition: Carbon fibers are fibers made from carbon-based precursors on large scale that are converted by pyrolysis into specific carbon structure with high tensile strength. Fig. 1: Carbon fiber based on polyacrylonitrile (PAN) by SGL Group [SGL] Since 1970ies carbon fibers are used as reinforcing materials WS 2024/25 | Composite Materials and Structure-Property-Relationship 7 Chair of Carbon Composites TUM School of Engineering and Design Technical University of Munich 3.2.2 Structure of Carbon Fibers High Strength of Carbon Fibers strong covalent bonds with binding energy of 350 kJ/mol highly oriented graphite structure of carbon fibers Weak van-der- Waals-Bond c Human hair b A a c = 0.67 nm B Strong covalent bonds A a = 0.14 nm Fig. 1: Unit cell of carbon single crystal Fig. 2: Scanning electron micrograph of carbon fiber and human hair WS 2024/25 | Composite Materials and Structure-Property-Relationship 8 Chair of Carbon Composites TUM School of Engineering and Design Technical University of Munich 3.2.3 General Carbon Fiber Applications Market Segments of Carbon Composites Aerospace Automotive Sports & Leisure etc. Fig. 3: Callaway carbon golf driver [carbonfibergear.com] Fig. 1: Boeing 787 Dreamliner [cnde.iastate.edu] Fig. 2: BMW i3 passenger compartment [bmw.de] WS 2024/25 | Composite Materials and Structure-Property-Relationship 9 Chair of Carbon Composites TUM School of Engineering and Design Technical University of Munich 3.2.4 Carbon Fiber Market (1/3) Global annual production and yearly capacity 1E+10 1.62 billion t 3% 3% 1E+09 6% 100000000 57.7 mio t 4% 10000000 4% USA & Mexico Global annual production [t] 35% Japan 1000000 5% China Taiwan 100000 58 kt South Korea 7% Hungary 10000 Germany France 1000 7% Great Britain RoW 100 10% 10 19% 1 Crude Steel Aluminum CFRP Fig. 1: Global annual production of crude steel, aluminum and CFRP Fig. 2: Yearly carbon fiber capacity by region/countries (2016); total:130,900t in 2015 [worldsteel.org, world-aluminium.org, CCeV/AVK] [CCeV/AVK] WS 2024/25 | Composite Materials and Structure-Property-Relationship 10 Chair of Carbon Composites TUM School of Engineering and Design Technical University of Munich 3.2.4 Carbon Fiber Market (2/3) Carbon Fiber Capacities by Manufacturer, Global Demand Fig. 1: Carbon fiber capacities in 09/2019 by manufacturer [CCeV19] Fig. 2: Global carbon fiber demand 2010–2026 (*estimate) [CU] WS 2024/25 | Composite Materials and Structure-Property-Relationship 11 Chair of Carbon Composites TUM School of Engineering and Design Technical University of Munich 3.2.4 Carbon Fiber Market (3/3) Market Segments – Global Demand and Revenue in 2013 2% 1% 7% Aerospace & Defense 6% 4% 5% Wind Turbines 4% 5% 30% Sport/Leisure 7% Molding & Compound 11% 50% Automotive 8% Pressure Vessels 12% Civil Engineering 11% 14% Marine 14% 9% Other Fig. 1: Global carbon fiber demand in 2013; total: 46500 t [CCeV/AVK] Fig. 2: Global carbon fiber revenue in 2013; total: US$ 1.7 billion [CCeV/AVK] WS 2024/25 | Composite Materials and Structure-Property-Relationship 12 Chair of Carbon Composites TUM School of Engineering and Design Technical University of Munich 3.2.5 Characteristics of Carbon Fibers Low density: 1.74 – 1.90 [g/cm3] Negative thermal expansion coefficient -0.5 to -1.1 [10-6/°C] No significant problems at inhalation of filaments < 5 µm Anisotropic in axial and transverse directions + High modulus (especially pitch based) + Good thermal stability (in absence of O2) + High thermal conductivity + High strength (especially PAN based) + Excellent creep resistance - High cost - Low strain to failure - Oxidation at temperatures > 450°C WS 2024/25 | Composite Materials and Structure-Property-Relationship 13 Chair of Carbon Composites TUM School of Engineering and Design Technical University of Munich 3.3 Manufacturing of Carbon Fibers 3.3.1 Process Chain 3.3.2 Raw Materials 3.3.3 Manufacturing Routes 3.3.4 Surface Treatment and Sizing WS 2024/25 | Composite Materials and Structure-Property-Relationship 14 Chair of Carbon Composites TUM School of Engineering and Design Technical University of Munich 3.3.1 Process Chain Strong bonds Carbon Atoms in hexagonal layers ➔ stiff and tight Carbon layers within the fiber arranged along the fiber direction Human Hair Single, dense thin fibers 6-7 µm diameter Carbon - fiber Carbon Fiber tow: 1.000-50.000 single fibres are clustered to allow cost efficient handling We know how the material should look like. ☺ Now we have to make it! WS 2024/25 | Composite Materials and Structure-Property-Relationship 15 Chair of Carbon Composites TUM School of Engineering and Design Technical University of Munich 3.3.1 Process Chain – How to make a Carbon Fiber? Classical Methods for Fiber Making Suitable for Carbon? Melt Spinning Carbon does not melt at all! (Polyester, Glass, Basalt) Solution spinning Carbon is not soluble at all! (Aramide, viscose rayon) Ceramic like fiber making Desired internal fiber structure not (binder + nanoparticles extruded & sintered) achievable! Others, e.g. electrospinning See above Therefore…. Works! Organic Organic polymeric Carbon BUT complex polymeric raw material fiber fiber and costly WS 2024/25 | Composite Materials and Structure-Property-Relationship 16 Chair of Carbon Composites TUM School of Engineering and Design Technical University of Munich 3.3.1 Process Chain PAN C Fiber Carbon Composites Crude Oil Acrylonitrile Precursor Fiber Materials Surface Spin Dope Polymerisation Spinning Stabilisation Carbonisation Treatment Preparation & Sizing WS 2024/25 | Composite Materials and Structure-Property-Relationship 17 Chair of Carbon Composites TUM School of Engineering and Design Technical University of Munich 3.3.1 Process Chain PAN C Fiber Precursor Spin Dope Polymerisation Spinning Preparation WS 2024/25 | Composite Materials and Structure-Property-Relationship 18 Chair of Carbon Composites TUM School of Engineering and Design Technical University of Munich 3.3.1 Process Chain – Polymerisation Acrylo Nitrile H H Different Possibilities z.B.: C C H CN Solution polymerisation Catalyst, Dispersion polymerisation Comonomer Precipitation polymerisation CN CN CN CN CN Poly Acrylo Nitrile Highly polar Solvens: Organic: DMAc, DMF, DMSO Solvent Inorganic: ZnCl2, NaSCN Spinn Dope Quality demands extreme purity (10% - >20% PAN + Solvent) WS 2024/25 | Composite Materials and Structure-Property-Relationship 19 Chair of Carbon Composites TUM School of Engineering and Design Technical University of Munich 3.3.1 Process Chain – Spinning Spinn bath Fiber formation in spinning bath Stretching Stretching for orientiation of molecules Washing Drying Fiber structure develops during spinning Source IVC, Frankfurt All defects reduce tenacity of carbon fiber Winding WS 2024/25 | Composite Materials and Structure-Property-Relationship 20 Chair of Carbon Composites TUM School of Engineering and Design Technical University of Munich 3.3.1 Process Chain Carbon Fiber Surface Stabilisation Carbonisation Treatment & Sizing WS 2024/25 | Composite Materials and Structure-Property-Relationship 21 Chair of Carbon Composites TUM School of Engineering and Design Technical University of Munich 3.3.1 Process Chain – Stabilisation (Oxidation) PAN Fiber white, flammable CN CN CN CN CN Gases Temperature 220-280°C (HCN,...) Air Oxidised PAN Fiber black, non flammable WS 2024/25 | Composite Materials and Structure-Property-Relationship 22 Chair of Carbon Composites TUM School of Engineering and Design Technical University of Munich 3.3.1 Process Chain – Carbonisation (Graphitisation) Gases Temperature » 1000°C (HCN, CO,...) C% N% H% O% Optimum Tenacity: PAN 68 26 6 - 1300 - 1500°C → HT, IM Fibers 1000 °C >92 50 wt.-%) a c = 0.67 nm Carbonized structure must show regions B with graphitic layers Emerging structure must be oriented along A covalent bonds to utilize high C-C binding energy a = 0.14 nm Fig. 1: Unit cell of carbon single crystal WS 2024/25 | Composite Materials and Structure-Property-Relationship 25 Chair of Carbon Composites TUM School of Engineering and Design Technical University of Munich 3.3.2 Raw materials Suitable Raw Materials T > 500 °C Nitrogen atmosphere Carbon yield Preservation of form Fig. 1: Pretzel before pyrolysis Fig. 2: Pretzel after pyrolysis Every carbonaceous matter exhibits a theoretical carbon yield WS 2024/25 | Composite Materials and Structure-Property-Relationship 26 Chair of Carbon Composites TUM School of Engineering and Design Technical University of Munich 3.3.2 Raw materials Precursor Materials Man-made fibers Synthetic Natural Vegetable Animal Polycondensation Polymerisation Polyaddition origin origin Polyamide 6, Cellulosic Vegetable Alginate Polyester, Elastane Paper fiber Polyacrylonitrile, fibers protein fibers Polyamide Polypropylene, 6.6 Polyethylene, Polyvinyl chloride Viscose, Cupro, Acetate, Modal, Lyocell [Fonds der Chemischen Industrie im Verband der Chemischen Industrie e. V. / Textilchemie / http://fonds.vci.de/] WS 2024/25 | Composite Materials and Structure-Property-Relationship 27 Chair of Carbon Composites TUM School of Engineering and Design Technical University of Munich 3.3.2 Raw materials Precursor Materials - Overview Precursor Carbon yield Characteristic Market share High orientation of molecular chains Polyacrylonitrile Low amount of defects 50 % 95 % (PAN) Medium / high modulus High / ultimate strength Can be graphitized Pitch 80 % Ultimate modulus < 5% Low / medium strength Non-regular structure Minimal, Lignin > 40 % High amount of defects lab only Low modulus / strength Cannot be graphitized Minimal, Cellulose 25% High amount of defects felts Low modulus / strength WS 2024/25 | Composite Materials and Structure-Property-Relationship 28 Chair of Carbon Composites TUM School of Engineering and Design Technical University of Munich 3.3.2 Raw materials Precursor Materials PAN Molecular formula (C3H3N)n Fig. 1: Precursor based on PAN [sae.org] Molecular weight M = n x 53 Share of carbon atomic 36 mass Theoretic carbon yield 68 wt.-% Practical carbon yield 50 wt.-% Practice/Theory 0.74 Fig. 1: PAN based carbon fiber [SGL] WS 2024/25 | Composite Materials and Structure-Property-Relationship 29 Chair of Carbon Composites TUM School of Engineering and Design Technical University of Munich 3.3.2 Raw materials Contact of Precursor Materials spheres without coalescence Coalescence Pitch Progressed Practical carbon yield 80 wt.-% coalescence Finished Carbon fibers can be produced from coalescence − Isotropic pitch Fig. 1: Formation of mesophase pitch from isotropic pitch – − Mesophase pitch (MPP): coalescence of spheres [Fitzer 1998] − Polymerized and condensed from isotropic pitch − Formation of spheres of aromatic hydrocarbons − Collision and coalescence of spheres − Development of solid, infusible and anisotropic coke Fig. 2: Example for chemical structure of mesophase pitch (MPP) WS 2024/25 | Composite Materials and Structure-Property-Relationship 30 Chair of Carbon Composites TUM School of Engineering and Design Technical University of Munich 3.3.2 Raw materials Precursor Materials Lignin Molecular formula (C11H14O4)n Molecular weight M = n x 210 Share of carbon atomic 132 mass Thermo-chemical Theoretic carbon yield 63 wt.-% enzymatic hydrolysis Melt spinning Practical carbon yield > 40 wt.-% Thermal Practice/Theory > 0,64 transformation WS 2024/25 | Composite Materials and Structure-Property-Relationship 31 Chair of Carbon Composites TUM School of Engineering and Design Technical University of Munich 3.3.2 Raw materials Precursor Materials Cellulose Wet spinning Molecular formula (C6H10O5)n Molecular weight M = n x 162 Share of carbon atomic 72 mass Theoretic carbon yield 44 wt.-% Practical carbon yield 25 wt.-% Thermal Practice/Theory 0,57 transformation WS 2024/25 | Composite Materials and Structure-Property-Relationship 32 Chair of Carbon Composites TUM School of Engineering and Design Technical University of Munich 3.3.3 Manufacturing Routes Carbon Fiber Production Using a PAN Based Precursor PAN PAN Stabilisation Carbonisation Graphitisation Solution Precursor Fiber ▪ Spinning ▪ 200-300°C ▪ 1200-1400°C ▪ 2000-3000°C ▪ air ▪ nitrogen ▪ argon atmosphere atmosphere High strength High modulus WS 2024/25 | Composite Materials and Structure-Property-Relationship 33 Chair of Carbon Composites TUM School of Engineering and Design Technical University of Munich 3.3.3 Manufacturing Routes Spinning Processes for PAN Based Precursors Solution spinning - Wet spinning Spin Bath - Water Todays standard process for carbon fiber precursor Spinneret Hole Solvent Water Solidification Spinning Solution PAN + Solvent (Close to solubility limit) Fig. 1: Schematic principle of wet spinning process [Morgan 2005] WS 2024/25 | Composite Materials and Structure-Property-Relationship 34 Chair of Carbon Composites TUM School of Engineering and Design Technical University of Munich 3.3.3 Manufacturing Routes Spinning Processes for PAN Based Precursors Solution spinning - Dry spinning Used for PAN fibers, but not for PAN as carbon fiber precursor Alternatives to solution spinning Melt spinning - R&D state Pseudo melt spinning - pilot in 80th Fig. 1: Schematic principle of dry spinning process [Morgan 2005] WS 2024/25 | Composite Materials and Structure-Property-Relationship 35 Chair of Carbon Composites TUM School of Engineering and Design Technical University of Munich 3.3.3 Manufacturing Routes PAN Precursor Production Spinning Washing Stretching Drying ▪ PAN powder is ▪ Removal of ▪ Longitudinal ▪ Removal of water dissolved in solvent by alignment of on fiber surface solvent washing with molecular chains and in fiber ▪ PAN solution is water ▪ Formation of transferred into micro and macro fibrous form structure WS 2024/25 | Composite Materials and Structure-Property-Relationship 36 Chair of Carbon Composites TUM School of Engineering and Design Technical University of Munich 3.3.3 Manufacturing Routes Stretching of PAN Based Filament During Precursor Production Formation of micro and macro structure at the end of spinneret Spinning direction Microfibrils of lamellae (folded Amorphous polymer with Non-regular regions molecular chains) randomly aligned lamellae between lamellae Fig. 1: Structural model for formation of micro and macro structure [Elias] Spinning is crucial for alignment of covalent bonds in longitudinal direction of future carbon fiber WS 2024/25 | Composite Materials and Structure-Property-Relationship 37 Chair of Carbon Composites TUM School of Engineering and Design Technical University of Munich 3.3.3 Manufacturing Routes Stabilization = Chemical reaction under oxygen (=oxidation) Irreversible thermal stabilization Highly exothermal reaction (2-3x stronger than oxyhydrogen reaction) Fibers are under tension to prevent shrinkage and tearing apart 200 - 300°C PAN + O2 PANOX Air (21 wt.-% O2) Precursor Stabilization Finish PANOX PANOX cannot burn under air or melt = prerequisite for carbonization WS 2024/25 | Composite Materials and Structure-Property-Relationship 38 Chair of Carbon Composites TUM School of Engineering and Design Technical University of Munich 3.3.3 Manufacturing Routes Stabilization Disentanglement of the polymer chains by externally Non-stretched fiber applied stretching Additionally inner stretching occurs due to shortening of the chemical bonds The process of stretching is Stretched fiber dependent on reaction temperature and reaction Molecular structure for highly oriented progress. PAN “Tie” molecules with back-folded regions WS 2024/25 | Composite Materials and Structure-Property-Relationship 39 Chair of Carbon Composites TUM School of Engineering and Design Technical University of Munich 3.3.3 Manufacturing Routes Stabilization Application fields for PANOX fibers Reinforcing carbon/carbon aircraft brakes Reinforcing brake pads in automotive applications (replacement of asbestos) Heat and flammability resistant insulation WS 2024/25 | Composite Materials and Structure-Property-Relationship 40 Chair of Carbon Composites TUM School of Engineering and Design Technical University of Munich 3.3.3 Manufacturing Routes Carbonization Influencing factors before carbonization (1) Target density from 1.36-1.42 g/cm3 to obtain fire-proof and infusible stabilized PAN fiber (2) Oxygen content between 10 – 12 wt.-% for maximum carbon yield (3) Good alignment of C-C bonds along longitudinal fiber direction (4) Minimization of defects WS 2024/25 | Composite Materials and Structure-Property-Relationship 41 Chair of Carbon Composites TUM School of Engineering and Design Technical University of Munich 3.3.3 Manufacturing Routes Carbonization With increasing density of oxidized fiber, density of carbon fiber decreases Preferred density of oxidized fiber: 1.375 g/cm3 Fig. 1: Relation between density of carbon fibers and that of stabilized fibers [Morgan 2005] WS 2024/25 | Composite Materials and Structure-Property-Relationship 42 Chair of Carbon Composites TUM School of Engineering and Design Technical University of Munich 3.3.3 Manufacturing Routes Carbonization Conducted in nitrogen atmosphere Thermal degradation of non-carbon atoms Formation of carbon rings Mass loss of about 50 wt.-% Fig. 1: Carbonization of stabilized fibers [Morgan] WS 2024/25 | Composite Materials and Structure-Property-Relationship 43 Chair of Carbon Composites TUM School of Engineering and Design Technical University of Munich 3.3.3 Manufacturing Routes Carbonization Pitch PAN MPP- Pitch Ideal graphite lattice Fig. 1: Decrease of graphite layer distance with increasing temperature Fig. 2: Formation of graphite lattice [SGL Group, Marsh 1991] Formation of graphitic layers and reduction of layer distance WS 2024/25 | Composite Materials and Structure-Property-Relationship 44 Chair of Carbon Composites TUM School of Engineering and Design Technical University of Munich 3.3.3 Manufacturing Routes Graphitization Maximum in Maximum in strength stiffness Higher heat treatment under argon Improvement of preferred Tensile strength orientation and Young‘s Young‘s modulus Modulus Below 1400°C: increase in temperature leads to increase in strength At 1800°C: minimum in strength (nitrogen loss) Above 1800°C: second 1200 1600 2000 2400 2800 1200 1600 2000 2400 2800 maximum in strength Temperature Temperature (lattice rearrangement) WS 2024/25 | Composite Materials and Structure-Property-Relationship 45 Chair of Carbon Composites TUM School of Engineering and Design Technical University of Munich 3.3.3 Manufacturing Routes [Barnet et al 1974] Cavities Types of defects Voids Stacking faults Disclinations Defects within Morphologic the layer Microcracks defects Defects prohibit formation of ideal graphitic structure WS 2024/25 | Composite Materials and Structure-Property-Relationship 46 Chair of Carbon Composites TUM School of Engineering and Design Technical University of Munich 3.3.3 Manufacturing Routes Carbon Fiber Production Using a Pitch Based Precursor Mesophase Thermoset Pitch fiber Carbon fiber Graphite fiber pitch (MPP) MPP fiber ▪ Two-phase ▪ Thermoplastic ▪ Oxidation ▪ Carbonisation ▪ Graphitisation emulsion or fiber with high ▪ Cross-linking under inert gas low degree of between molecular orientation molecules weight single along fiber axis ▪ Retention phase meso- and freeze of pitch orientation WS 2024/25 | Composite Materials and Structure-Property-Relationship 47 Chair of Carbon Composites TUM School of Engineering and Design Technical University of Munich 3.3.3 Manufacturing Routes Theoretic Young‘s modulus: 1060 GPa Pitch vs. PAN Based Fibers Theoretic dependency Pitch based fibers establish three- acc. to Ruland Young‘s modulus dimensional graphite order during graphitization →High Young’s modulus of pitch based fibers Isotropic pitch basis Degree of orientation Fig. 1: Influence of the degree of orientation on Young’s modulus [Fitzer 1998] Young’s modulus of carbon fiber increases with degree of orientation of graphitic layers WS 2024/25 | Composite Materials and Structure-Property-Relationship 48 Chair of Carbon Composites TUM School of Engineering and Design Technical University of Munich 3.3.3 Manufacturing Routes Pitch vs. PAN Based Fibers Properties of carbon fibers in longitudinal fiber direction, based on graphite single crystal Theory Practice Tensile strength 6370 100 000 [MPa] [Toray T1000G] Young’s modulus 1060 450-890 [GPa] Fig. 1: Layer plane distance of graphite lattice Pitch based fibers reach ultra high modulus PAN based fibers reach very high strength WS 2024/25 | Composite Materials and Structure-Property-Relationship 49 Chair of Carbon Composites TUM School of Engineering and Design Technical University of Munich 3.3.3 Manufacturing Routes Vapor Grown Carbon Fibers Produced by catalytic chemical vapor deposition (CCVD) Cross-section of vapor grown carbon Nucleation of a filament by using a submicron filament activated catalyst After nucleation fiber grows away from hot substrate Final product: discontinuous fibers − with diameters 1-100 µm − With lengths few millimeter to few hundred millimeters No stabilization needed → one-step process Alternative to fiberglass for use in short- fiber reinforced composites Fig. 1: Manufacture of vapor grown fiber [espci.org] WS 2024/25 | Composite Materials and Structure-Property-Relationship 50 Chair of Carbon Composites TUM School of Engineering and Design Technical University of Munich 3.3.4 Surface Treatment and Sizing Fiber-matrix adhesion Sizing/Surface finish For effective load transfer by the matrix between filaments (1) Surface treatment: − increase number of active/reactive surface groups Carbon fiber (mainly oxides) − roughen fiber surface to increase surface area Polymer Polymer matrix matrix (2) Sizing or surface finish − = Application of a coating − Improvement of adhesion between filaments Oxidic surface − Facilitation in wetting out the fiber with matrix material groups − Function as a lubricant to prevent fiber damage during subsequent handling processes To fully exploit the excellent mechanical properties of carbon fibers a strong interaction to the future polymer matrix has to be established WS 2024/25 | Composite Materials and Structure-Property-Relationship 51 Chair of Carbon Composites TUM School of Engineering and Design Technical University of Munich 3.3.4 Surface Treatment and Sizing Surface Treatment Oxidative Methods − Anionic oxidation (electrolysis, most common) − Wet oxidation (chemical) − Dry oxidation (chemical) Requirements − Interaction with sizing and matrix material Carbon fiber − Supply of polar links (oxidic surface groups) Possible effects − Removal of outer, weak surface layer − Changes in surface area of fiber − Chemical modification of surface − Changes in polar surface free energy Polar and reactive surface groups on carbon fiber surface determine the adhesion WS 2024/25 | Composite Materials and Structure-Property-Relationship 52 Chair of Carbon Composites TUM School of Engineering and Design Technical University of Munich 3.3.4 Surface Treatment and Sizing Sizing/Surface Finish Methods − Deposition from dispersion of a polymer (most common) − Electrodeposition of polymer on fiber surface − Electropolymerization of polymer on fiber surface − Plasma polymerization Requirements − Good physical and chemical bonding of matrix to fiber surface − Choice of sizing depends on future matrix material Concept of an interphase Fig.1: Concept of interphases [Morgan 2005] − Three-dimensional phase between fibers and matrix − Due to diffusion of matrix polymer into sizing and sizing into matrix development of an interphase with changing properties WS 2024/25 | Composite Materials and Structure-Property-Relationship 53 Chair of Carbon Composites TUM School of Engineering and Design Technical University of Munich 3.3.4 Surface Treatment and Sizing Sizing/Surface Finish Effects − Compared by using Scanning Electron Microscopy (SEM) − Application of different sizes using identical matrix system Fig.1: Adhesive failure without suitable sizing Fig.2: Cohesive failure with adapted sizing WS 2024/25 | Composite Materials and Structure-Property-Relationship 54 Chair of Carbon Composites TUM School of Engineering and Design Technical University of Munich 3.3 Carbon Fiber Properties 3.4.1 Fiber Types and Designation 3.4.2 Comparison to Other Materials 3.4.3 Specific Carbon Fiber Applications WS 2024/25 | Composite Materials and Structure-Property-Relationship 55 Chair of Carbon Composites TUM School of Engineering and Design Technical University of Munich 3.4.1 Fiber type and Designation Monofilament: individual filament d ≈ 0.005 - 0.1 mm, typical 6-8 µm Multi-filaments: several monofilaments − 1k = 1000 filaments Human hair − 6k = 6000 filaments − 50k = 50,000 filaments Low tow: − 1-12k: aerospace − 12-24k: sports and leisure Heavy tow: − 50-320k − for mechanical engineering, industrial Fig. 1: Scanning electron micrograph of carbon fiber and human hair WS 2024/25 | Composite Materials and Structure-Property-Relationship 56 Chair of Carbon Composites TUM School of Engineering and Design Technical University of Munich 3.4.1 Fiber Type and Application Fiber types 7000 Aviation 6000 IM HT: High Tensile IM: Intermediate Modulus Strength [MPa] 5000 HM: High Modulus HT HM UHM: Ultra High Modulus Space 4000 Industrial UHM 3000 100 300 500 700 900 Young's modulus [GPa] WS 2024/25 | Composite Materials and Structure-Property-Relationship 57 Chair of Carbon Composites TUM School of Engineering and Design Technical University of Munich 3.4.1 Fiber Type and Application Fiber types 7000 Based on PAN HT, IM: produced by carbonization at 6000 IM temperatures between Based on pitch 1200-1400°C Strength [MPa] 5000 HM, UHM: HT additional heat treatment HM (graphitization) at temperatures between 4000 2000-3000°C UHM 3000 100 300 500 700 900 Young's modulus [GPa] WS 2024/25 | Composite Materials and Structure-Property-Relationship 58 Chair of Carbon Composites TUM School of Engineering and Design Technical University of Munich 3.4.1 Fiber Type and Application Properties of Various Carbon Fiber Types HT IM HM UHM Tensile strength [MPa] 4000 6000 2500 2150 Young’s modulus E1 [GPa] 240 295 400 450-950 (in fiber direction) Young’s modulus E2 [GPa] 28 n.a. 15 n.a. (transverse to fiber direction) Density [g/cm3] 1.74 1.74 1.81 1.90 WS 2024/25 | Composite Materials and Structure-Property-Relationship 59 Chair of Carbon Composites TUM School of Engineering and Design Technical University of Munich 3.4.2 Comparison to Other Materials Comparison of Carbon Fiber to Wood, Steel and Aluminum [MPa] [g/cm³] [MPa] [g/cm³] 8 6000 3000 7 5000 6 2500 5 4000 2000 4 3000 1500 3 2000 1000 2 1000 500 1 0 0 0 Density Tensile Strength Specific Tensile Strength WS 2024/25 | Composite Materials and Structure-Property-Relationship 60 Chair of Carbon Composites TUM School of Engineering and Design Technical University of Munich 3.4.3 Specific Carbon Fiber Applications Aerospace Applications Fig. 1: Boeing 787 Dreamliner nose section [Boeing] Fig. 2: Airbus A350 XWB lower wing cover [Airbus] WS 2024/25 | Composite Materials and Structure-Property-Relationship 61 Chair of Carbon Composites TUM School of Engineering and Design Technical University of Munich 3.4.3 Specific Carbon Fiber Applications Automotive Applications Fig. 1: BMW i8 passenger compartment [bmw.de] Fig. 3: New BMW 7 series with carbon fiber reinforced parts [bmw.de] Fig. 4: Design component – Side blade Fig. 2: Structural component - Rocker and Audi R8 [Benteler SGL] A-piller Lamborghini [Benteler SGL] WS 2024/25 | Composite Materials and Structure-Property-Relationship 62 Chair of Carbon Composites TUM School of Engineering and Design Technical University of Munich 3.4.3 Specific Carbon Fiber Applications Sports and Leisure Applications Fig. 1: Hockey racket [Reebok] Fig. 3: Bike [braid-bikes.de] Fig. 2: Ski with wood core [Völkl] WS 2024/25 | Composite Materials and Structure-Property-Relationship 63 Chair of Carbon Composites TUM School of Engineering and Design Technical University of Munich A1 References (1/2) Schürmann, H., 2007, Konstruieren mit Faser-Kunststoff-Verbunden, Springer, Berlin Heidelberg, ISBN 3540721908 Morgan, P., 2005, Carbon fibers and their composites, Taylor and Francis Group, Boca Raton, ISBN 0-8247-0983-7 Fitzer, E., Manocha, L.M., 1998, Carbon Reinforcements and Carbon/Carbon Composites, Springer, Berlin Heidelberg New York, ISBN 3-540-62933-5 Kühnel, M., Witten, E., 2014, Composites Market Report 2014 - Market developments, trends, challenges and opportunities, Carbon Composites e.V., AVK – Industrievereinigung Verstärkte Kunststoffe Sauer, M., Schüppel, D., 2024, Market Report 2023 – The global market for carbon fibers and carbon composites, Composites United e.V. Sauer, M., Schüppel, D., 2019, Composites Market Report 2019 – The global CF- and CC-Market 2019, Composites United e.V. Gosh, P., 2004, Fiber science and technology, Tata McGraw-Hill, New Delhi, ISBN: 978-0-07-133141-8 Holman, J., Stone, P., 2001, Chemistry, Nelson Thomas Ltd, Cheltenham, ISBN: 0748762396 WS 2024/25 | Composite Materials and Structure-Property-Relationship 64 Chair of Carbon Composites TUM School of Engineering and Design Technical University of Munich A1 References (2/2) Matsumoto, T., 1985, Mesophase pitch and its carbon fibers, Pure & Appl. Chem. 57 (11), pp.1553-1562, IUPAC, Great Britain Beste, A., 2014, ReaxFF Study of the Oxidation of Lignin Model Compounds for the Most Common Linkages in Softwood in View of Carbon Fiber Production, J. Phys. Chem. A 118, pp. 803−814, doi: 10.1021/jp410454q Dumanli, A.G., Windle, A.H., 2012, Carbon fibres from cellulosic precursors: a review, J Mater Sci 47, pp. 4236-4250, doi: 10.1007/s10853-011-0681-8 Pilato, L., Michno, M., 1994, Advanced Composite Materials, Springer, Berlin, ISBN 978-3-642-08187-3 WS 2024/25 | Composite Materials and Structure-Property-Relationship 65