What is an abrasive wheel? What materials are commonly used in abrasive wheels? What is the function of a bonded abrasive wheel? Define the term "grit size" in abrasive wheels. Exp... What is an abrasive wheel? What materials are commonly used in abrasive wheels? What is the function of a bonded abrasive wheel? Define the term "grit size" in abrasive wheels. Explain the difference between a grinding wheel and a cutting wheel. How does the hardness of an abrasive wheel affect its performance? Describe the structure of an abrasive wheel. What is the role of the bonding material in an abrasive wheel? Compare vitrified, resinoid, and rubber-bonded abrasive wheels. What are the common defects in abrasive wheels, and how can they be prevented? How do you select an appropriate abrasive wheel for a given machining operation? What is a grinding machine? Name any three types of grinding machines. What is the purpose of coolant in grinding operations? Explain the working principle of a cylindrical grinding machine. Explain the working principle of a surface grinding machine. How does centerless grinding differ from cylindrical grinding? What factors affect the selection of a grinding wheel? Discuss the advantages and disadvantages of grinding over other machining processes. How does the dressing and truing of a grinding wheel improve performance? Explain the role of grit size, bond type, and wheel grade in grinding efficiency.
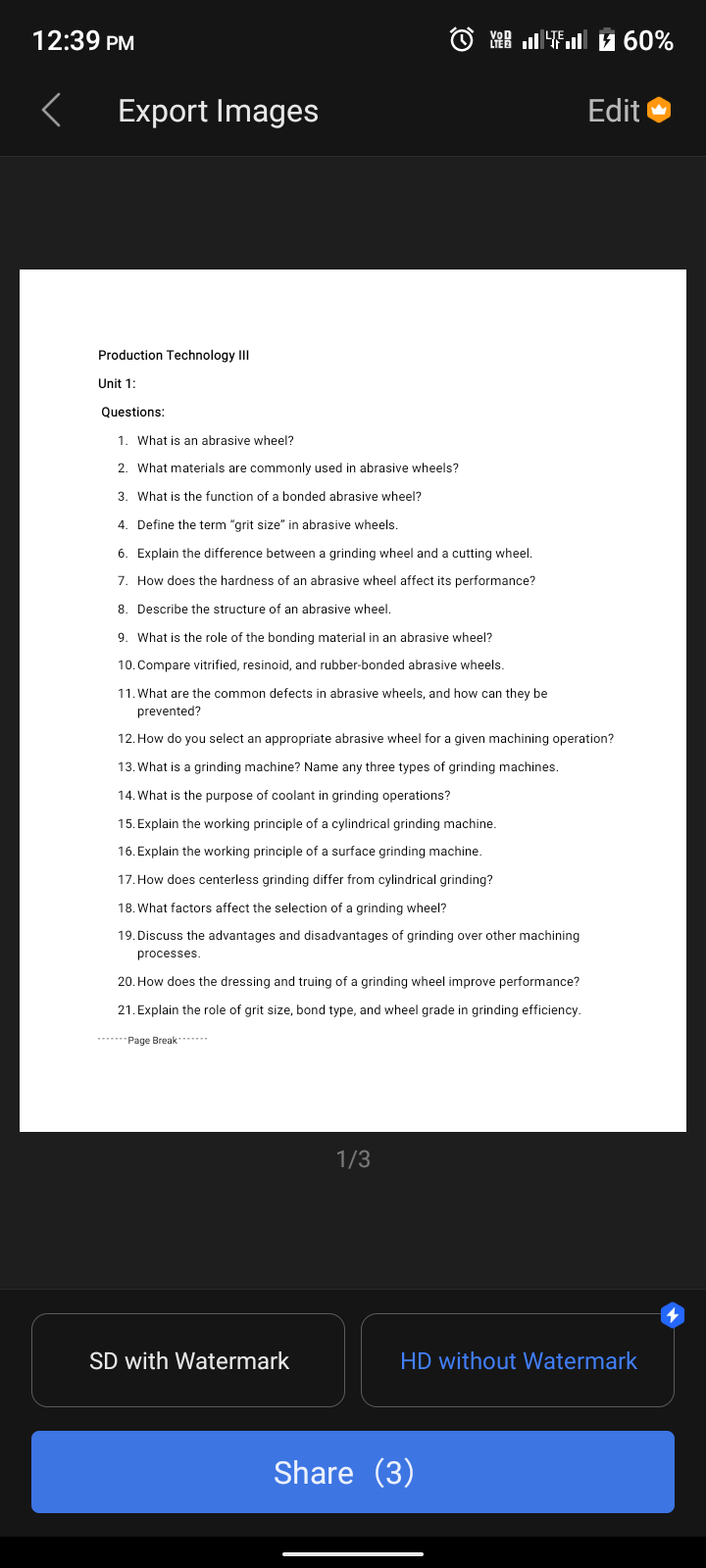
Understand the Problem
The image contains a list of questions related to abrasive wheels, grinding wheels, and grinding machines, likely part of a Production Technology III unit. The questions cover definitions, functions, materials, comparisons, selection criteria, and working principles within the context of grinding processes.
Answer
Answers to the questions have been provided about abrasive wheels and grinding.
Here are the answers to the questions:
- An abrasive wheel is a tool used for grinding, cutting, polishing, or material removal. It consists of abrasive grains held together by a bonding material.
- Common materials used in abrasive wheels include aluminum oxide, silicon carbide, diamond, and cubic boron nitride.
- The function of the bonding material in a bonded abrasive wheel is to hold the abrasive particles together, allow for controlled wear, and release dulled grains to expose new sharp grains.
- Grit size refers to the size of the abrasive particles in the wheel, which affects the material removal rate and surface finish. Larger grit sizes remove material faster but produce a rougher finish, while smaller grit sizes create smoother finishes.
- (Question 5 is missing)
- A grinding wheel is typically thicker and used for stock removal and rough shaping, while a cutting wheel is thinner and designed for precise cutting operations.
- The harder the abrasive wheel, the more resistant it is to wear. Harder wheels are suitable for grinding soft materials, while softer wheels are better for hard materials.
- An abrasive wheel consists of abrasive grains, a bonding material, and sometimes a filler. The structure refers to the spacing between the abrasive grains.
- The bonding material holds the abrasive grains together, and affects the wheel's ability to resist wear and fracture. It also influences the rate at which the abrasive grains are released during grinding.
- Vitrified wheels are hard, rigid, and porous, suitable for precision grinding. Resinoid wheels are tougher and more flexible, used for high-speed operations. Rubber-bonded wheels offer a smooth finish and are used for polishing.
- Common defects include cracking, chipping, and imbalance. Preventative measures are proper storage, handling, and regular inspection.
- Select an abrasive wheel based on the material being machined, the desired finish, the amount of material to be removed, and the type of grinding machine being used. Also important are grit size, grade, bond type and structure.
- A grinding machine is a power tool used for grinding. Three types are: cylindrical grinding machine, surface grinding machine, and centerless grinding machine.
- Coolant in grinding operations reduces heat, lubricates the cutting action, removes swarf (chips), and improves surface finish.
- A cylindrical grinding machine grinds the external or internal cylindrical surfaces of a workpiece by rotating the work piece and the grinding wheel.
- A surface grinding machine grinds flat surfaces by moving the workpiece linearly under a rotating grinding wheel.
- Centerless grinding supports the workpiece without centers, offering higher production rates and automation compared to cylindrical grinding.
- Factors affecting grinding wheel selection include material to be ground, desired surface finish, stock removal rate, machine capabilities, wheel speed, and coolant type. Also consider are grit size, bond type, and wheel grade.
- Grinding provides high precision and smooth finishes but has a lower material removal rate compared to other machining processes like milling or turning.
- Dressing reshapes the wheel, while truing makes the wheel concentric. These processes restore the wheel's cutting ability and improve grinding accuracy.
- Grit size affects the surface finish and material removal rate. The bond type influences wheel strength and wear resistance. Wheel grade relates to the wheel's hardness and ability to retain abrasive particles.
Answer for screen readers
Here are the answers to the questions:
- An abrasive wheel is a tool used for grinding, cutting, polishing, or material removal. It consists of abrasive grains held together by a bonding material.
- Common materials used in abrasive wheels include aluminum oxide, silicon carbide, diamond, and cubic boron nitride.
- The function of the bonding material in a bonded abrasive wheel is to hold the abrasive particles together, allow for controlled wear, and release dulled grains to expose new sharp grains.
- Grit size refers to the size of the abrasive particles in the wheel, which affects the material removal rate and surface finish. Larger grit sizes remove material faster but produce a rougher finish, while smaller grit sizes create smoother finishes.
- (Question 5 is missing)
- A grinding wheel is typically thicker and used for stock removal and rough shaping, while a cutting wheel is thinner and designed for precise cutting operations.
- The harder the abrasive wheel, the more resistant it is to wear. Harder wheels are suitable for grinding soft materials, while softer wheels are better for hard materials.
- An abrasive wheel consists of abrasive grains, a bonding material, and sometimes a filler. The structure refers to the spacing between the abrasive grains.
- The bonding material holds the abrasive grains together, and affects the wheel's ability to resist wear and fracture. It also influences the rate at which the abrasive grains are released during grinding.
- Vitrified wheels are hard, rigid, and porous, suitable for precision grinding. Resinoid wheels are tougher and more flexible, used for high-speed operations. Rubber-bonded wheels offer a smooth finish and are used for polishing.
- Common defects include cracking, chipping, and imbalance. Preventative measures are proper storage, handling, and regular inspection.
- Select an abrasive wheel based on the material being machined, the desired finish, the amount of material to be removed, and the type of grinding machine being used. Also important are grit size, grade, bond type and structure.
- A grinding machine is a power tool used for grinding. Three types are: cylindrical grinding machine, surface grinding machine, and centerless grinding machine.
- Coolant in grinding operations reduces heat, lubricates the cutting action, removes swarf (chips), and improves surface finish.
- A cylindrical grinding machine grinds the external or internal cylindrical surfaces of a workpiece by rotating the work piece and the grinding wheel.
- A surface grinding machine grinds flat surfaces by moving the workpiece linearly under a rotating grinding wheel.
- Centerless grinding supports the workpiece without centers, offering higher production rates and automation compared to cylindrical grinding.
- Factors affecting grinding wheel selection include material to be ground, desired surface finish, stock removal rate, machine capabilities, wheel speed, and coolant type. Also consider are grit size, bond type, and wheel grade.
- Grinding provides high precision and smooth finishes but has a lower material removal rate compared to other machining processes like milling or turning.
- Dressing reshapes the wheel, while truing makes the wheel concentric. These processes restore the wheel's cutting ability and improve grinding accuracy.
- Grit size affects the surface finish and material removal rate. The bond type influences wheel strength and wear resistance. Wheel grade relates to the wheel's hardness and ability to retain abrasive particles.
More Information
Abrasive wheels are essential tools in manufacturing for achieving precise dimensions and smooth surface finishes. The selection of the right abrasive wheel depends on several factors, including the material being worked on, the desired finish, and the type of grinding machine used.
Tips
When selecting an abrasive wheel, always consider the material of the workpiece, the desired surface finish, and the capabilities of the grinding machine. Regular maintenance, such as dressing and truing, is crucial for optimal performance and safety.
Sources
- Mastering the Use of Abrasive Wheels: The Comprehensive Guide - kingsunmachining.com
- Guide about Grinding Wheels Types, Material & Specifications - hindustanabrasives.com
- The 7 Factors Used to Determine a Grinding Wheel Specification - nortonabrasives.com
AI-generated content may contain errors. Please verify critical information